Blending bulk materials, maintaining particle structures and avoiding dust
Bulk homogenisation and dust binding
The ability to mix and wet powders is as old as human civilisation. Druggists and dyers used mortars and crushed powder particles in crucibles to increase the surface area of the mixed material particles. In this way, crushing and bulk mixing were carried out simultaneously. From a strictly scientific point of view, further changes were made to the powder particles. Electron microscopic observations show how diverse and individual powder particles can change. Clumpy powder deagglomerates, dry particles wet and coat themselves with finer fractions, dispersed particles agglomerate, absorbers can dehumidify powder, dispersions can crystallise under pressure and friction.
Law of nature: The smaller the dust particles are, the greater their specific attraction. As the particle diameter decreases, the specific surface area increases logarithmically. The same applies to chemical reactivity.
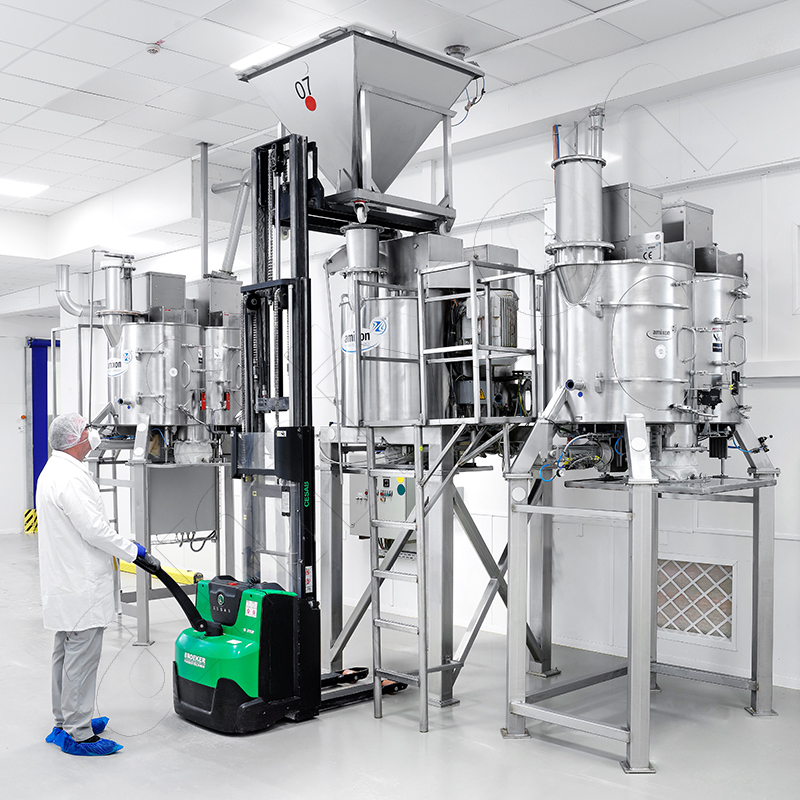
Testing and process development
The mixing systems described above can be tested in the amixon GmbH technical center. Here, we gain interesting insights together with our customers. amixon® permanently keeps more than 30 test apparatuses available for you. In this way, we can make almost "the entire world of powder mixing" available to our customers at one location. A day in the amixon® technical center will be rewarding for a profitable investment decision. A powder mixer usually has a long service life. Often more than 20 years, sometimes even 40 years. Many times a day, important questions repeat themselves in the daily routine:
- Preservation of particle structures: How efficiently is mixing carried out?
- Flexibility: How much may filling levels vary?
- Efficiency: How well does self-cleaning and residual emptying work?
- Production reliability: Is it enough to take a look inside the mixer?
- Acceptance and ergonomics: How quickly can inspection openings be opened and closed?
- Are inspection doors permanently tight?
- Exclusion of contamination: How long does dry cleaning take?
- Control of microbiology: How long does wet cleaning and drying take?
- many more questions .....
We predict with high probability very good results and a high gain of knowledge.
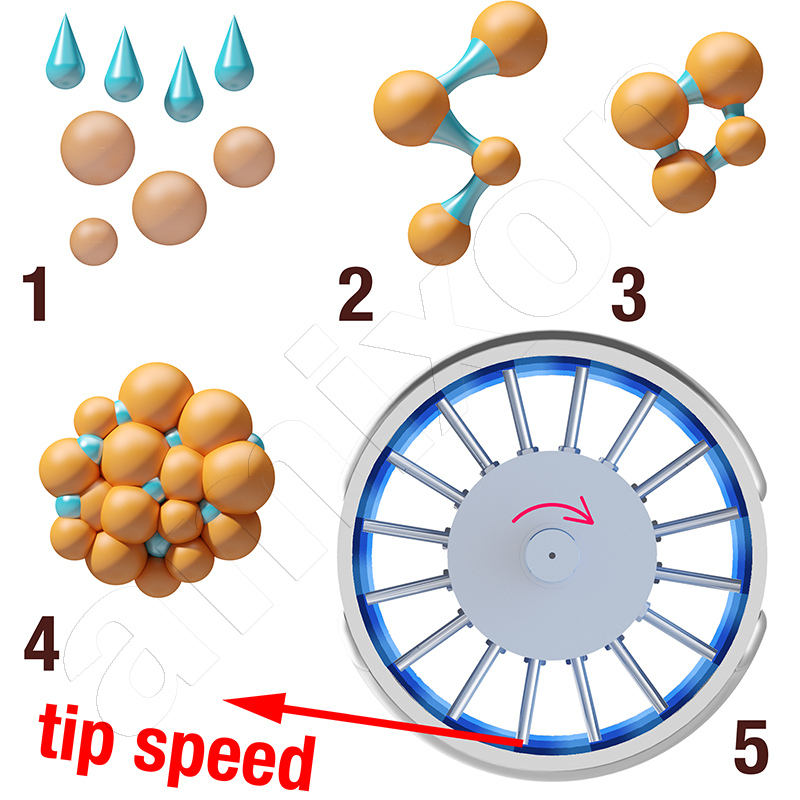
Wetting, compacting, enlarging, rounding and discharging powder particles.
Agglomeration through dynamic compaction
The mixer shaft rotates at high speed. The blades agitate the mix. The faster the tiller rotates, the faster the mix rotates. The faster the mix rotates, the stronger the centrifugal forces. The mix is thrown into the mixing chamber. There it is slowed down. The peripheral speed at the mix wall is 0 m/s. At the front of the mandrels, however, the peripheral speed is 10 to 20 m/s. The gap between the mixing chamber and the mandrel is approx. 1.5 mm. In this shear gap, mixing, wetting, shearing, compacting, deagglomeration and agglomeration take place with high intensity. The amixon annular gap mixing granulator can agglomerate very effectively. The result is uniformly round pellets. Ideally, 100% of the dust particles are bound.
- Moisten
- Distribute liquid
- Liquid bridges bind particles
- Agglomerates roll up - like a snowball
- turbulent movement of the ring layer with shearing and compaction
Important parameters for good agglomeration include
- Particle size of the powder / dust
- Rotational speed
- Number of pins
- Length of the process chamber
- Type of liquid
- Location of the liquid addition
- Pre-treatment and type of liquid addition
- Temperature of the goods
- Mass flow of powder
- Mass flow of liquid
- Filling level of the ring layer mixer
- Dwell time
Build-up granulation or build-up agglomeration
Both terms are used in the literature and usually mean the same thing. In any case, the term ‘agglomeration’ is correct. It describes the increase in particle size due to the adhesion of many small particles. A granulation process also occurs when a solid mass (flakes, extrudates) is reduced to a friable structure. In this blog, a more aggressive form of agglomeration is also mentioned. o-called ring-layer mixing granulators can carry out agglomeration processes particularly effectively and inexpensively. his ring-layer mixing machine is operated continuously. he mixing shaft is equipped with many pins. The peripheral speed is 10 to 25 m/s at a high rotation frequency. Accordingly, the powder is accelerated into a rotational movement and pressed against the wall of the mixing chamber. The shear and pressure forces acting on the powder are 200 times greater than the gravitational force. he particles come so close together that interparticle forces become effective. The particles build up and grow. They are discharged downwards on the opposite side of the mixing chamber. he binding mechanisms can be improved by adding small amounts of a liquid binder.
amixon® ring layer mixer from our production: The basic development was developed around 25 years ago for the agglomeration of carbon black. The amixon® production programme is mainly focused on mixers with vertically arranged mixing tools.
Dust
Wherever powdery goods are processed, dusts occur. Their unpleasant property is that they can escape through the smallest of leaks. For example, from big bags, mixers, silos, pipelines or from filling plants. Dust can remain suspended in the air for a long time and settle everywhere. This happens preferentially on horizontal surfaces. In the event of a airblow, they swirl up again and float in the air. Some dusts are hygroscopic, absorbing moisture from the surrounding air and wetting all the surfaces on which they are deposited. This makes cleaning more difficult. Salt dusts, in particular, can be corrosive. Dusts can be combustible and even explosive. This is always the case if they are of organic origin; if they are very fine and dry. In the working environment, dusts are always a nuisance, they affect our well-being and irritate the respiratory tract. Escaping dusts are expensive, they represent material loss and imply disposal costs.
Powders that are end-used by consumers are usually conditioned, so that their dust content is negligible.
When particles are smaller than 0.1 µm, they are referred to as nanoparticles. Many materials exhibit completely new properties when they are nanodisperse. In medicine, powder metallurgy, electrical engineering and high-performance ceramics, nanodisperse structures pave the way for new materials and functions.
As the particle diameter decreases, the specific surface area increases logarithmically. The same applies to chemical reactivity. If particles are smaller than 0.1 µm, they are referred to as nanoparticles. Many materials exhibit completely new properties when they are nanodispersed. In medicine, powder metallurgy, electrical engineering and high-performance ceramics, nanodisperse structures pave the way for new materials and functions.
Binding dusts. Gently moisten bulk materials. Distribute extremely small liquid material quantities into large powder quantities
Dust binding by wetting can take place gently and accurately in amixon® mixers. Dust emissions can be avoided by agglomerating dust-fine particles together or by adhering them to larger particles. Even the smallest amounts of a suitable liquid can be helpful. The precondition, however, is that the liquid is distributed evenly over the entire surface of the bulk material.
Two-substance nozzles are also known as atomising nozzles. They can atomise low-viscosity liquids micro-fine. At the same time, they create a fluidisation zone in the mix. This favours the mixing process.
KoneSlid® powder blender
Dust formation can be avoided within the bulk material by avoiding abrasion on the particles. This is where a conflict of objectives becomes apparent: on the one hand, the mixing process should achieve ideal homogeneity, but on the other hand, the particles should not break, crush or round during mixing. This problem can only be solved if an ideal mixing quality can be achieved with minimum energy consumption. This KoneSlid® mixer from amixon® realizes the gentlest way of powder mixing. It is preferably used:
- Where many spray-dried agglomerates are involved in the mixing process. These are, for example, milk powder derivatives for dietary nutrients such as baby food, cappuccino, .....
- medical active ingredients
- biological substrates
- enzymes
- cultures of bacteria
- instant beverages, iced tea, spices, tea, muesli, fat powder, lecithin powder, .....
KoneSlid® mixers achieve ideal mixing qualities in a very short mixing time. The discharge process is completed in just a few seconds.
Gyraton® mixer for large bulk material quantities
It is a great privilege when a production manager can have homogeneously mixed raw materials at his disposal. This simplifies the subsequent process steps and guarantees consistent quality of the end product. Gyraton® mixers from amixon® make a valuable contribution here. For example, when the contents of a 40-foot deep-sea container (approx. 70 m³ bulk material) are to be homogenized. The mixer spiral rotates slowly and mixes all powder particles from bottom to top. In the process, the mixer spiral glides slowly along the mixing chamber wall - similar to a gyroscope. A Gyraton mixer can also discharge the mixed materials completely. It is then equipped with ComDisc® tools.
The mixing principle of the Gyraton® mixer works universally. The components can be dry, moist or wet. Particle sizes, bulk densities, flow properties, particle shapes, .... can vary greatly. Gyraton® achieves the highest mixing qualities. The mixing time is adjustable:
- long at very low drive power and low speed
- short with increased drive power
Gyraton® mixer for continuous bulk mixing
A large volume Gyraton® mixer can also operate as a continuous mixer. The mixing process is based on continuous boiler flow. Normally, gravimetric feeding systems would have to be used. However, in contrast to batch feeders, these are relatively expensive. But even if the mixer is filled by batch, the mixed material is discharged continuously. This is largely independent of the number of components, as long as they are of similar size. The mixed material is all the more homogeneous
- the smaller the batches are
- the more constant their weight
- the more constant the time cycles are
- the higher the filling level is adjusted
- the faster the mixing tool rotates
Processes, industries and the many industry-specific designations
The cube symbolises how powders can be changed in the mixer. The three dimensions represent 1) the processes, 2) the industries and 3) the industry-specific designations.
The different processes are of varying importance for the individual industries:
- In the pharmaceutical industry, active ingredient synthesis and vacuum drying are of great importance.
- In solid galenics, the trituration of active ingredients is important with the aim of achieving large surface areas and good ‘bioavailability’.
- In the food industry, the focus is on gentle mixing. The particles should be retained. In addition, the powders produced should be dust-free.
- In the fine chemicals industry, space-dominating total flow is important. Only then can efficient heat transfer take place - an essential prerequisite for complete reaction processes.
- Polymers are conditioned with additives to create high-performance plastics. These include, for example, prepared fillers, reinforcements, colour pigments, stabilisers, metal soaps, self-extinguishing additives, antistatic agents, ....
- Nanoparticles are used as coating substances in the solid-state synthesis of engineering ceramic materials (powdered metals and nanoceramics). They coat finely dispersed metal salts and metal oxides. Nanofine particles are either reactants or act as catalysts in the calcination process at high temperatures.
The terms ‘solid blending’, ‘powder blending’ or ‘bulk blending’ are basically just headings for various types of powder formulation/solids refinement. A refining process can only be successful if almost every single particle in the batch has undergone the desired material transformation. In this respect, the capture and flow of all particles must be space-controlled and free of dead space.
The phenomena of particle technology are taught in mechanical process engineering. This scientific discipline belongs to the engineering sciences. It was largely founded by Professor Dr Hans Rumpf (University of Karlsruhe) in the 1970s. He analysed individual empirical results from material preparation and examined them for physical laws. Using methods of dimensional analysis, he and his scientists developed reliable calculation methods to describe complex comminution and mixing processes.
© Copyright by amixon GmbH