Sterile mixing equipment for infant formula and baby food manufacturing
Infant formula is a dietary nutrient. It requires hygienically designed processes. Powdered baby food must be aseptically pure, precisely dosed and biofunctionally compatible.
amixon® mixers meet these requirements at the highest level.
They have been specially developed to homogenise complex powder mixtures safely, efficiently and with the utmost care for the product.
Maximum hygiene:
amixon® mixers are designed according to HACCP principles. They comply with EHEDG recommendations and even exceed them. They mix without dead space. They are easy to clean and empty themselves automatically after each batch to 99.97%. In this respect, they operate technically contamination-free.
Instant properties are retained
After spray drying and agglomeration, the milk solids have a sensitive structure. Thermosensitive components such as vitamins, probiotics, prebiotic agents, secondary plant substances and trace elements are only added in the final mixing process.
An amixon® mixer ensures that these sensitive agglomerates are not destroyed and that the desired instant properties (rapid solubility, low dust formation) are fully retained.
Excellent mixing quality:
Even at a dosage of 1 : 100,000, the amixon® mixer achieves ideal mixing quality after just a few minutes.
This distribution quality is considered ideal – no further improvement can be achieved technically, regardless of how long the mixing process takes. 15-gram samples from a 10 m³ batch show mixing quality coefficients of less than 5%. These results have been confirmed analytically many times.
Flexibility in operation:
amixon® mixers are designed for both batch and continuous mixing operations.
amixon® has the solution!
The end user decides whether dry cleaning, wet cleaning or manual or automatic cleaning is required.
amixon® offers excellent opportunities worldwide.
- For product and process development,
- for testing,
- and for optimisation and validation.
Our technical centres are located in: China, Benelux, Germany, India, Korea, Japan, Thailand and the USA.
The challenges of infant formula manufacturing
High-quality baby food contains many tiny components, including trace elements and minerals, as well as vitamins and probiotics. amixon® mixers are also suitable for gently mixing such heterogeneous particle structures. Efficient powder mixing means minimal shear, low mixing tool rotation frequency and short mixing times. The end product is homogeneous, dust-free, easily wettable, quickly soluble and completely dispersible.
Left: amixon® twin-shaft mixer for 7 m³ batches. With ComDisc® for complete discharge.
Mixing equipment for infant formula and baby food production
amixon®produces customized mixing equipment that creates perfectly homogenous blends at filling levels ranging from 5 to 100 percent, ensuring uniformity from batch to batch. Our high-performance powder processing machines are especially gentle, capable of retaining particle structure, achieving excellent sinkability and solubility, and eliminating the creation of dust within the mixture.
Because the mixing machines are designed completely free of dead-space, a three-dimensional flow can gently yet completely homogenize the goods in as little as 70 to 200 rotations. Equipped with innovative mechanisms that achieve up to 99.997% discharge, cleaning your mixer between batches is easy. Furthermore, the ergonomic Clever-Cut® inspection doors grant full access to the mixing chamber.
All of our mixing equipment is hygienically designed according to EHEDG, GMP, and FDA standards, facilitating the health and safety certification process for your infant formula or baby food production facilities.
And with testing centers located in Europe, North America, and throughout Asia, our processing and validation experts are always on-hand to help you ensure the highest performance and quality standards with your baby food mixer. Together we can develop a customized mixing machine for infant formula or baby food that will perform to your exact processing and batch requirements and fit seamlessly into your production line.
amixon® mixers for powdered baby food and infant formula
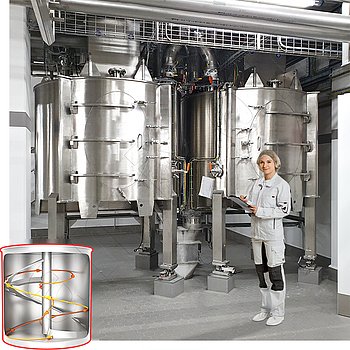
Vertical single-shaft mixer
The vertical single-shaft mixers from amixon® are ideal for the final homogenisation of spray-dried baby food and dry dietary foods. In this case, the mixtures consist of relatively robust agglomerates produced by fluidised bed agglomeration.
For mixtures containing more sensitive agglomerates, the amixon® twin-shaft mixer is recommended. Its advantage is that it requires only one third of the mixing time at the same mixing tool rotation speed. This reduces the shear and pressure loads on the agglomerates by two thirds.
Whether single-shaft or twin-shaft mixers: in both cases, ideal mixing qualities are achieved that cannot be improved in practice. Thanks to ComDisc®, both mixers can empty themselves completely. Mixers from amixon® guarantee high-quality and hygienic end products with excellent solution behaviour (instant properties).
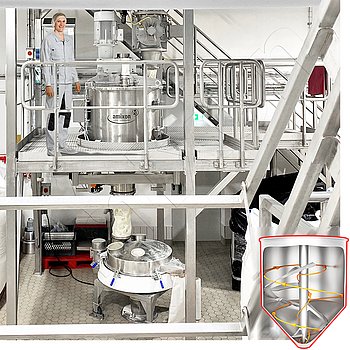
Continuous Powder Mixer AMK
When producing baby food or dietary supplements in large quantities and over long periods of time, the use of a continuous mixing system may be advisable. The amixon® continuous mixer shown here produces ideal mixing qualities. Its output capacity is up to 12 m³/h. The mixing principle corresponds to continuous kettle flow. All components involved in the recipe are dosed into the mixer gravimetrically. The mixed product is discharged continuously. A control valve keeps the filling level in the mixing chamber constant. This mixing process is also particularly gentle.
The advantage of the continuous mixer from amixon® is that there is no product loss at the beginning or end of the mixing cycle. From the first to the last gram, saleable goods are produced in excellent quality. The mixed materials are packaged directly after a control sieving (end-of-line). This mixer from amixon® can also mix in batches.
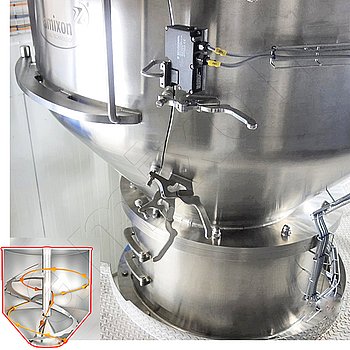
KoneSlid® Precision Mixer KS
The KoneSlid® mixer is an innovative further development of the proven cone mixer from amixon®. It combines high mixing performance with particularly fast discharge. The mixing quality is excellent – regardless of the nature of the raw materials used. At the same time, the mixing energy required is very low. The KoneSlid® mixer works just as quickly and efficiently as the amixon® twin-shaft mixer.
A special feature is the fast and complete discharge. Free-flowing mixed materials are completely discharged within a few seconds. The product is transferred to the downstream vessel in such a way that no pile-ups occur. This prevents the risk of segregation in subsequent process steps. These properties make the KoneSlid® mixer particularly interesting when batch mixing is required but continuous processing is necessary.
In such cases, two KoneSlid® mixers can be used in ‘twin mode’. While one is mixing, the other is being filled or emptied. The raw materials are weighed in batches with high accuracy. The traceability of each batch is fully maintained. Nevertheless, the production process can run virtually continuously.