Innovative technologies
The history of amixon® goes back more than 40 years. During this time, we have registered over 40 patents worldwide. Today, we are one of the innovation and quality leaders in the field of vertical precision mixers for bulk solids. Our equipment achieves ideal mixing qualities and meets the highest demands in process engineering.
In addition, we are dedicated to other key areas of process technology. These include
- improved automation,
- the introduction of predictive maintenance,
- the homogenisation of particularly large batches (Gyraton® silo mixers) and
- excellent operator ergonomics.
- We pay particular attention to the best possible discharge of residues,
- automated cleaning processes
- both dry and wet, and
- compliance with the highest hygiene standards.
amixon® mixers are used for dry, moist and wet solids. Our mixing plants, sterilizers, fermenters, vacuum mix dryers and synthesis reactors are among the best in their class.
KoneSlid® mixer
The KoneSlid® mixer is an innovative further development of the cone mixer from amixon®. Its cone-shaped closure element serves both as a mixing element and as a shut-off valve. The cone closes the mixing chamber with its tip pointing upwards, thus significantly supporting the mixing process. The material to be mixed is conveyed upwards and then slides down the cone. It reaches the periphery of the mixing chamber, where the spiral mixer picks up the material and conveys it upwards again. The emptying process takes place when the cone is lowered. The bulk material then flows downwards past it. In this case, too, it slides downwards over the closure cone. The brand name KoneSlid® is derived from this operating principle.
The KoneSlid® mixer achieves ideal mixing qualities within 30 to 120 seconds – regardless of the filling level. No matter what the properties of the bulk materials are. The mixing process is particularly gentle. Only minimal energy is required. The granulometry of the powders is not changed.
The KoneSlid® mixer not only empties completely, but also in just a few seconds. Free-flowing goods are discharged completely.
KoneSlid®mixers are ideal for mixing goods with sensitive particle structures.
- For example, for powders that have been dried in a spray tower and agglomerated in a fluidised bed process.
- All types of breadcrumbs where the particles must not be crushed,
- dry food with good instant properties,
- coated particles,
- moist bulk materials that must not agglomerate,
- nanostructured high-performance ceramics
- .....
KoneSlid®mixers are also used where mixing and emptying times are minimal.
- For example, when batch mixers mix virtually continuously.
- KoneSlid® mixers can also be used as continuous mixers. Their mixing principle is based on continuous tank flow.
New amixon® test center
In 2024, amixon® built three new synthesis reactors/vacuum mixing dryers for testing purposes. The batch size is 200 litres. We can modify, dry, refine or synthesise substances for our customers.
At the technical centre, amixon® is also happy to meet demanding process requirements for your process development/product development.
- Vacuum up to 25 bar overpressure
- Temperature up to 350 °C.
- Alloy 59 material for corrosive products.
- Explosion-proof environment (Gases and Dust Explosion requirements).
In addition, we can homogenise large batches in the Gyraton® silo mixer, with component compositions of up to 1:100,000. The solids or powders can be dry, moist or wet.
Feel free to visit us with your original product! We look forward to your challenges!
Gyraton® mixing silo – precision for silo mixers
The Gyraton® mixing silo is an innovative new development from amixon®. It mixes batches of up to 100 m³ hygienically, efficiently and reliably. It even mixes partial fillings from 5% reliably.
Highest mixing precision:
Component ratios of up to 1:100,000 are distributed evenly. The coefficient of variation is less than 5%. The analysed sample quantity is only 15 grams. The Gyraton® thus sets new standards in silo mixing technology.
Your advantages at a glance:
- Very low drive power, adaptable to the desired mixing time.
- Universally applicable for dry, moist or pasty bulk materials.
- Process reliability even with widely varying grain sizes and bulk densities.
- Flexible operation: batch or continuous.
- Gyraton® silo mixers meet the highest hygiene standards. They can be cleaned dry or wet. Cleaning can be carried out manually, semi-automatically or fully automatically.
- With the help of ComDisc® discharge systems, Gyraton® silo mixers can be emptied almost completely.
- A Gyraton® test mixer with a batch volume of up to 3 m³ is available for process engineering trials.
SpherHelics® hollow sphere mixer
The mixing chamber is a hollow sphere. A helical mixing tool rotates inside it. This conveys the mixing goods from bottom to top. The axis of the mixing tool can be arranged vertically or at an angle. The greater the angle, the better the mixing effect. The optimum angle is 20°. This mixing system therefore belongs to the group of vertical precision powder mixers.
SpherHelics® hollow sphere mixers have similar interesting properties to the amixon® vertical single-shaft mixer.
- Very good mixing results
- Mixes well even at low filling levels.
- Good hygienic properties
- Compact design
- Additional features can be added on request.
- Cutting rotor
- Liquid material addition indicator
- ComDisc®
- SinConvex®
- OmegaSeal®
- WaterDragon®
- ....
Clever-Cut® inspection doors with OmgaSeal® seal
The amixon® mixers are equipped with large, ergonomic inspection doors that allow access to the mixing container. What makes them special is that the inspection doors seal without dead space. The polymer seal seals very close to the mixed material.
An innovative manufacturing process ensures that the inspection doors remain permanently sealed. This is also the case when the doors are opened and closed frequently.
Another special feature is the groove into which the round polymer seal is inserted: the groove is curved towards the rear. The seal is clamped into its seat. No adhesive is required. Nevertheless, it cannot be lost.
When the inspection door is closed, the shape of the seal resembles the Greek letter Ω. As the brand name ‘Omega’ cannot be protected, amixon® decided to use the brand name OmgaSeal®.
KwickKlamp® is the ergonomic locking system from amixon®
When a powder mixer needs to be cleaned or inspected, every minute counts. Cleaning times are unproductive times.
The inspection door of a mixer is technically sophisticated. It follows the contour of the housing and must close tightly at all times. The seal must be free of dead space and permanently gas-tight. The closure system must be safe and quick to operate.
This is exactly why KwickKlamp® was developed. It fulfils two tasks:
- It presses the inspection door firmly into place and
- locks it securely in the end position.
Your advantages at a glance:
- One-hand operation: the door can be opened and closed easily, quickly and reliably with just one hand.
- Robust and durable: The sturdy construction is designed for high loads and many closing cycles.
- Secure closure: Thanks to the self-locking mechanism, accidental opening is impossible.
- Ergonomically designed: The high force transmission in the final phase of pressing ensures easy and precise handling.
- Hygienic design: There are no threads and no dirt corners. Cleaning is easy. The contact pressure can be individually adjusted.
For occupational safety reasons, KwickKlamp® is supplemented by electrical or mechanical locking systems.
ComDisc® – Complete discharge for maximum yield
Even the last remnants of product are perfectly mixed and should not be lost. amixon® technology ensures that almost everything is discharged from the mixer. This increases the batch yield to up to 99.97%. Waste is avoided and cleaning effort is significantly reduced. Self-cleaning is fully automatic.
During the mixing process, the ComDisc® tools remain raised. They swim through the mixture. As they are in the flow shadow, they do not influence the mixing process. They only lower during emptying. Then they push the residual product into the mixer outlet without segregation.
The ComDisc® tools are made of food-safe plastic. They are hygienic, sterilizable and durable. They can be quickly replaced if necessary.
Residual discharge behaviour of two different precision mixers
Two different precision mixers in industrial use each mix batches of 3.8 tonnes of food supplements. The mixing quality is excellent in both cases and cannot be improved further.
Case 1: Horizontal twin-shaft mixer with paddle mixing tools: The mixing time is only a few minutes. After emptying, 55 kg of perfectly mixed product remains in the mixer. This quantity can only be recovered by manual removal. However, this would have to be done under sterile conditions. In practice, this is unrealistic as it takes too long and ties up personnel. In most cases, the residue is sucked out and destroyed. In the case of wet cleaning, the residues are rinsed out with water and end up in the waste water.
Case 2: Vertical twin-shaft mixer from amixon®, equipped with SinConcave®mixing augers and ComDisc®discharge tools. Here, too, the mixing process takes only a few minutes. Depending on the product, only 1.2 kg remains after emptying. Emptying is automatic and self-acting.
Calculation example:
Avoidable product loss per batch (case 1): 45 kg − 1.2 kg = 43.8 kg. With six different recipes per day and 200 production days, this results in: 43.8 kg × 4 × 200 = 35,040 kg of avoidable loss per year. At a raw material price of €3 to €8 per kilogram:
Added value thanks to amixon® technology: 64,560 kg × €3 = €105,120 to 64,560 kg × €8 = €280,320 per year.
Even the last remnants of the product are perfectly mixed and should not be lost. amixon® technology ensures that almost everything is discharged from the mixer.
Working time, water consumption and wastewater charges were not taken into account. A precision mixer from amixon® pays for itself in a short time.
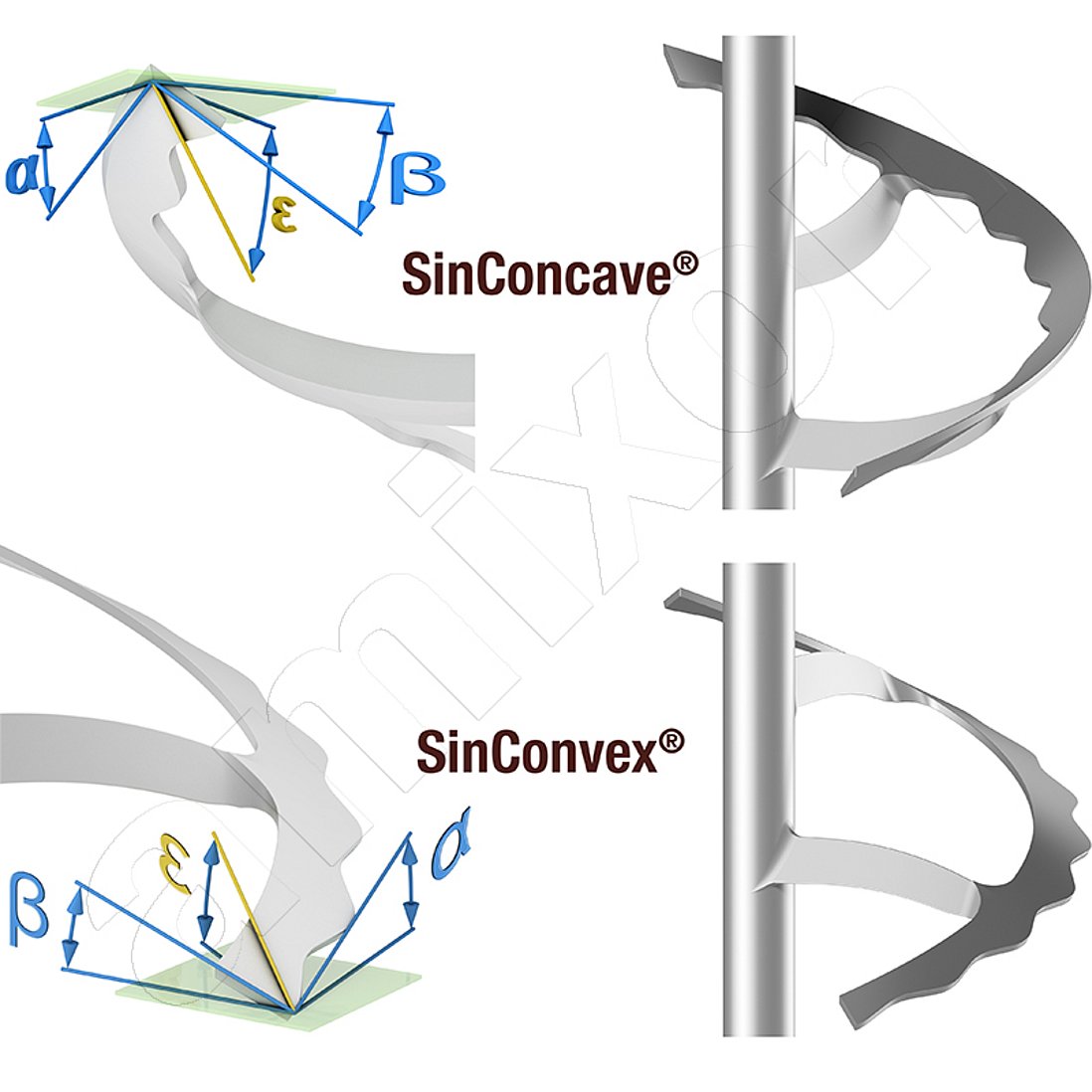
Standard spiral, SinConcave® and SinConvex®
Three geometries – one goal: the perfect mix. amixon® offers three versions of spiral mixing tools: Standard, SinConcave® and SinConvex®.
All of them generate an even, three-dimensional flow in the mix – efficiently, gently and reproducibly.
When rotating around a vertical or inclined axis, the product is gently conveyed upwards along the wall. In the centre, it flows back downwards. An intensive mixing effect is created between these main flows.
Each particle comes into contact with every other particle, resulting in a stochastic ideal distribution. Maximum mixing quality that cannot be surpassed in practice.
Customised geometry – tailored to your mixing task!
With over 40 years of experience, we can recommend the optimum spiral geometry, which we adapt individually to your product and process. We also precisely coordinate the angles.
- α: the pitch of the mixing spiral
- β: the tangential tilt
- Epsilon (ε) is the resulting slope angle, which allows the mixed material to flow downwards completely.
We take the following into account:
- Self-cleaning effects
- Complete, automatic emptying
- Flexible operation with changing filling levels
- Efficiency during automatic wet cleaning
WaterDragon® Wet Cleaning System
WaterDragon® is a system for automatic wet cleaning and drying of an amixon® mixer / vacuum mixer dryer / synthesis reactor. The pressure of the washing water is approx. 3.5 bar, the temperature can be up to 90 °C.
A large opening cross-section is available for the incoming hot air. After the mixer has dried, the spray lance moves out of the mixing chamber. The opening then closes without any dead space.
Depending on the size of the machine, several WaterDragon® systems can be installed in the mixer.
Manufacturing portfolio of amixon®
amixon® is a global trendsetter and quality leader in the field of vertical precision mixers. We look forward to your specific task. All machines are available for trials, even for large batches of up to 3 m³. Risks that can arise from scale-up calculations can thus be eliminated.
amixon GmbH
Halberstaedter Strasse 55
33106 Paderborn
Germany
Telephone: +49-5251-688888-0