
KoneSlid®: Mix powder in seconds and discharge it completely.
KoneSlid® mixer with complete discharge
Some producers want to use particularly small, powerful batch mixers in their powder blending operations. This should increase their competitiveness. In this way, more mixing jobs should be completed in a short time.
This means that not only the feeding and mixing process must be accelerated, but also that the discharge must happen quickly and without residues.
Powder mixing companies want to produce ideal mixing qualities. This should take place by fulfilling important secondary requirements:
- They want to preserve the granulometry of the raw materials.
- No dust should occur.
- This is especially relevant for instant products produced with the spray agglomerator.
- They want short mixing times and the best possible discharge of residual material.
- They want contamination-free batch consistency, no matter which raw materials are used.
They want a validated cleaning routine, adapted to the degree of contamination and adjusted to the raw material composition of the subsequent production orders. - The cleaning should be carried out either dry, moist or wet.
- Automatic or manual.
Unique performance
The spiral mixing tool gently conveys the mixing goods upwards. This takes place on the periphery of the mixing chamber. In the center of the mixing chamber, the downward flow prevails. The conical closing element directs the flow back outwards. Different rotation speeds overlay the entire volume of the mixing chamber. Each particle is randomly in the upward movement or in the downward movement.
Conical closing element in the mixing chamber.
Conical valves have been used in the bulk solids industry for many decades. They are only installed vertically and have the advantage of optionally discharging mixing goods either rapidly or in a dosing mode. Their use within a precision powder mixer is a novelty. The cone in this case has particularly steep and smooth slopes. Gravity causes the mixing goods to slide downwards. This is how they are guided to the periphery. The mixing good flows into the operating range of the mixing tool and is conveyed upwards again and again. Theoretically, the mixing spiral has completely conveyed the entire mixing chamber volume upward after approximately 5 revolutions. This is the explanation for the extremely short mixing time.
amixon® offers unique benefits for the user with this new development.
This powder mixing machine is called KoneSlid® mixer and combines excellent features:
- The mixing process is three-dimensional with minimal energy input.
- The peripheral speed of the mixing tool is very low (optionally below 1 m/s to approx. 3 m/s).
- The mixing process takes only 20 to 120 seconds, depending on the mixing task.
- Discharge takes place segregation-free - with low agitation of the mixing tool.
- A "displacer cone" lowers and discharges the mixed goods within a few seconds.
- The degrees of filling can vary - from about 10% to 100%.
- The mixer meets the highest hygiene requirements; far beyond the EHEDG requirements.
An "Atex" EG type examination certificate is available for the mixer. - The mixing chamber meets the requirements for catergory II 1D and thus a zone 20 is permitted.
- Three or four large inspection doors allow for convenient inspection of all components in contact with the product.
- These inspection doors are uniquely hygienically designed: "OmgaSeal®".
For example, with this small KoneSlid® mixer of size KS 500 (500 litres usable capacity), it is possible to supply a filling / packing machine with a sufficient amount of mixed material. The maximum filling volume flow here is, for example, 10 m³ of baby food per hour.
Optionally, the mix can be inerted inside the mixer. Vacuum application and evacuation of ambient air from the mixing chamber then extends the batch time.
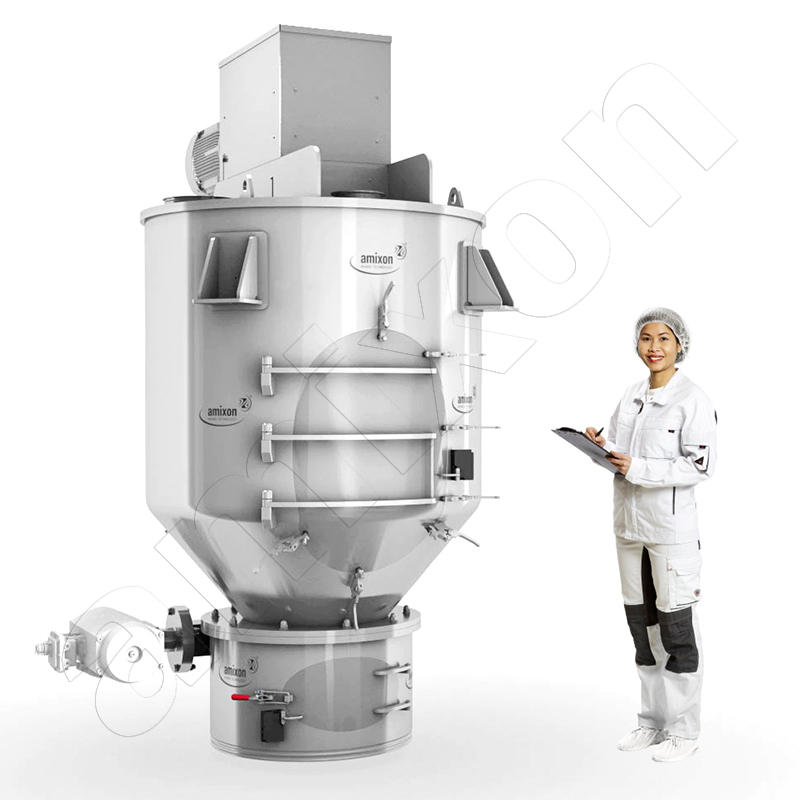
Model: KS 2400. All areas that are in contact with the mixing good can be conveniently inspected by the operator. In practice, good ergonomics means quality assurance and time savings. How many thousands of times is a powder mixer cleaned or inspected? Maybe 5 times per shift? With two-shift operation, that's two thousand times a year. Considering the complete discharge, 6 minutes may be saved each time. The time saving per shift is 30 minutes.
In this section, amixon® answers questions that are frequently asked:
What prompted amixon® to develop the conical powder mixer type KoneSlid®?
Answer by amixon®: This type of mixer was developed for the mixing of particularly sensitive components. These include frozen nutrients and frozen bacterial cultures. However, this also includes goods resulting from freeze-drying or produced in the spray tower and agglomerator. These are mainly instant nutrients or agglomerated medical actives with excellent instant properties. Ideally, these goods would be packed directly from the plant: in sachets, in bags, in foil bags, folding cartons or in cans.
Does this concern additives for spray-dried blended products with ingredients that must not be heated?
Answer by amixon®: Yes, exactly, the KoneSlid® mixer was also developed for that kind of instant products. There are often components that must not be exposed to the thermal treatment of a spray tower or an agglomerator, such as vitamin B2, probiotics, prebiotics, omega-3 fatty acid or omega-6 fatty acid. In this case, a final mixing process after the spraying process is unavoidable. During mixing, these substances must be agitated extremely gently - hardly noticeably.
In these cases, however, the highest mixing quality is essential. Isn't that a conflict of objectives? .... on the one hand to mix homogeneously, on the other hand to preserve the particles in their existing granulometry? The process of discharging from the mixer can also stress the mixing goods. Especially when the mixing goods have to be discharged from the mixer quickly and residue-free?
Answer by amixon®: It may seem illogical, but it is actually possible to adequately homogenize such goods and discharge them without residue. This is done by three-dimensional rearrangement. An inwardly inclined mixer spiral rotates at a low rotational frequency and conveys the mixed materials upwards in the periphery of the mixing chamber. The goods flow from above to the center. They glide downwards along the mixing shaft. Once they reach the bottom, they are directed outward by the conical displacer body. There they are once again picked up by the mixing tool. Ideal mixing qualities are achieved after only a few revolutions. The homogeneity equals the best possible distribution and can no longer be improved in practice.
Is it true that a high mixing quality is only achieved if the mixing tool rotates at high speed?
Answer by amixon®: This may be true for other mixing systems. The opposite applies to the amixon® mixers presented here. The entire content of the mixing chamber is completely conveyed and rearranged after about 4-5 revolutions. This happens regardless of the rotational frequency. As a rule, the ideal mixing quality is achieved after 8 to 20 revolutions. Then the conical displacement body / the closure element lowers and the goods leave the mixer within a few seconds.
Doesn't it then matter whether the mixing tool carries out the mixing process with a low or higher rotational frequency?
Answer by amixon®: This consideration is indeed close at hand. However, it must be borne in mind that the phenomena of wear and abrasion do not occur linearly to the relative speed. Often the destruction of the particles even occurs quadratically to the circumferential speed. This situation would be present if the mixing tool would agitate the particles at high speed and if the particles would flow rapidly in relation to each other. Then they grind against each other with increased pressure. The particles break or become rounder. Fine dust is unintentionally produced. In this respect, the adapted slow rotary movement of the mixing unit helix is of great importance.
Are there any other reasons for using such a vertical KoneSlid® mixer?
Answer by amixon®: Yes, there is no doubt about it. It is the profane things that can dominate day-to-day operations, for example when it comes to residual discharge. The better a mixing plant discharges, the more effectively the mixing operation works. In the case of free-flowing products, this means for the mixer described here:
- Virtually no product carryover due to remaining residues
- discharge of the mixed goods within seconds (but optionally also in a dosing manner)
- almost no residues that have to be disposed of when a recipe change has to be carried out
- all raw materials that have been used are discharged as high quality retail goods.
Sustainable action is becoming increasingly important with a view to our raw materials, our drinking water and with a view to our natural resources. Environmentally conscious action is an added value for the end consumer!
Answer by amixon®: In this KoneSlid® mixer there are practically no sources of contamination if the mixing goods are free-flowing. The mixing tool is only driven and mounted at the top. There is only one shaft seal. This is arranged above the product and is subject to virtually no wear. It only seals against dust.
The KoneSlid® mixer is a product of the amixon® manufacturing excellence. The operator will enjoy it for many decades to come.
KoneSlid® mixers can be installed directly above filling lines. They work either continuously or batch-by-batch, accurately and extremely quickly. They can be installed as end-of-the-line mixers at the end of a process chain above the filling machine. - Sometimes it makes sense to carry out the mixing tests at the customer's site. Can amixon® provide rental test mixers?
Answer by amixon®: Mixing trials with your original products serve to gain know-how and eliminate uncertainty. Feel free to visit us at the test center in Paderborn and bring your mixing goods with you. KoneSlid® mixers in various sizes are available here. On request, you can also rent our test mixers. We recommend this procedure whenever a freshly produced spray product changes over the course of the storage period.
Hygienic inspection doors from amixon® with OmgaSeal® seal
At this point, amixon® would also like to emphasize that it is much more motivating for the plant operator to operate a plant that is particularly hygienically designed and has excellent ergonomic visibility. This is made possible by inspection doors manufactured using the Clever-Cut® process. The operator will usually enjoy using and maintaining a hygienically designed mixing plant. This is important in view of the long service life of amixon® mixers. They often work for more than 30 years. Used amixon® mixers are rarely sold on the second-hand market.
If required, you are welcome to use our technical centre in Paderborn. KoneSlid® mixers are available there in various sizes for tests with your mixing materials.
© Copyright by amixon GmbH