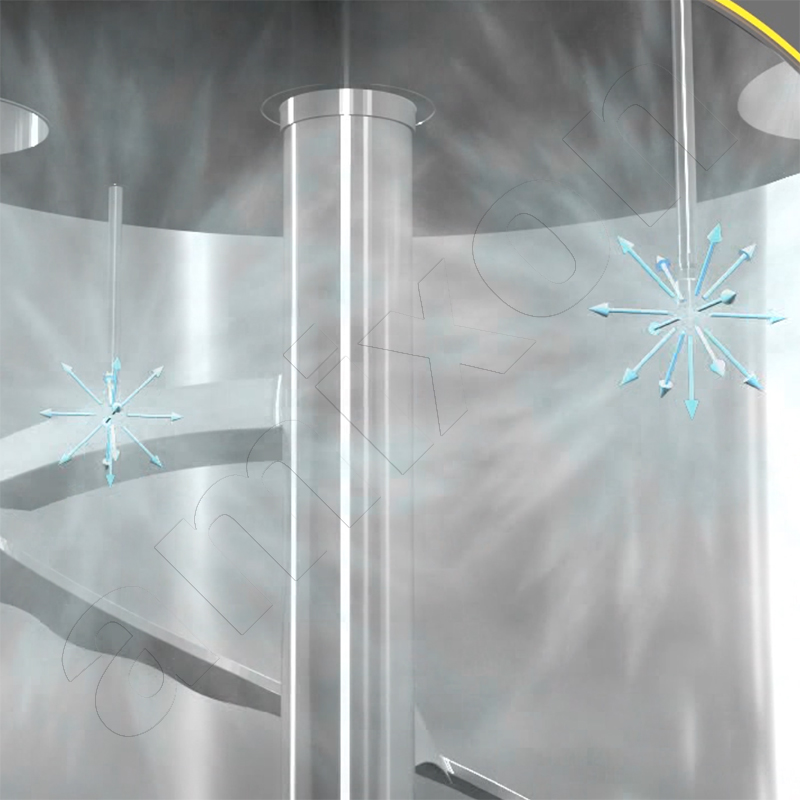
Rotary spray nozzles wet the mixing chamber and the mixing tools. Among other factors, the size and speed of the droplets also determine the efficiency of the washing.
Wet cleaning of powder mixers; automatic or manual; Washing in Place (WIP)
Factories that produce or process dry materials avoid the presence of water or moisture.
In mixing plants that process dry materials, water is reluctant to tolerate. Water or high humidity in the ambient air can negatively influence the powder quality; especially if bulk materials are hygroscopic. Quality assurance goes out of control when microbiological processes are unintentionally triggered in the mix that contaminate the powder and ambient air.
In this respect, the following applies almost in general: companies that process and mix powdery goods want to avoid the open appearance of water. In this respect, they will look for ways to clean the mixers as dry as possible. In some cases, cleaning can even be dispensed with altogether,
- if the mixer can be discharged to a high degree
- if the subsequent batch has similar recipe components
- if the mixer is hygienically designed.
Depending on the industry, product group, degree of contamination and sequence of production, there are graduated cleaning regimes.
Although dry cleaning is a fast and low-risk way of cleaning, many plants cannot do without wet cleaning of their mixing plants. Some of them are listed below as examples.
- pharmaceutical agents,
- vitamin mixtures,
- dietary food for premature babies, or sick people, ......
- Instant products such as spicy sauces, soups, beverages, flavored tea,
- stabilizers,
- color-intensive spices,
- aromas, flavors,
- strong-smelling substances,
- high concentrates,
- premixtures (premixes) and triturations
- active substances in which enzymes are involved or
- tobacco; chewing tobacco, snuff, snus
- plant protection products,
- inorganic colors, color pigments, ceramic color bodies, organic colors,
- nanopowders
- ....
this list is not exhaustive
Practical example: nutrient preparation for enteral nutrition:
The bulk mixer shown on the right is exemplary for particularly hygienic powder mixtures. Carbohydrates, fats, vitamins and minerals are combined in powder form. Such a composition is physiologically optimally utilizable. The final products are easily digestible, long-lasting and very tasty. The powder mixture is dissolved in water like an instant drink. The nutrient density is particularly high but balanced. It allows a whole food diet without solid ingredients. The liquid can be drunk or given by tube.
The same powder mixer is also used to produce tablet masses, vitamin preparations, and food supplements. A formulation change takes place after almost every batch. ComDisc® tools achieve excellent residual discharging down to a few grams. This saves a lot of raw material. Almost all input materials are converted into saleable goods. There is hardly any waste. In this respect, very little washing water is required. Wet cleaning and drying are automatic.
Powder mixing plants that are regularly wet cleaned should be designed to be hygienic. amixon® has 40 years of experience and has developed unique solutions:
By way of example, this also involves the following items:
SinConvex®/ Concave® and ComDisc® ensure good residual discharge. This means that (almost) all the mix is utilized right from the start and a lot of washing water is saved. Other aspects relate to the design of the inspection doors and their seals, OmgaSeal® seals particularly close to the product - technically free of dead space, the type and design of the shaft seals, lip seals glide on ceramic shaft coatings - they work optionally with or without gas flushing, the type and design of the dead space-free discharge valve, DosiFlap® can save vertical installation space and replace valves, the operating mode and design of the dust filtration during filling and emptying of the mixer, the type of drying and disposal of the moist vapors, ... and much more
In the amixon® pilot plant we have good conditions to optimize your mixing processes and cleaning regimes. Optionally, we will demonstrate various wet cleaning concepts to you.
Reliable drying of the mixer
After wet cleaning, the washing water must flow out completely. Drying of the mixer is particularly fast when the mixer is cleaned with hot water. Due to the high heat capacity of water (more than 8 times that of steel) and the good heat conduction of steel, the mixer heats up spontaneously. This heat energy is used to evaporate the residual water. It is crucial that the resulting water vapour is safely discharged. This can be accelerated by feeding in warm air. It is recommended to open the inspection doors in the final phase of drying.
© Copyright by amixon GmbH