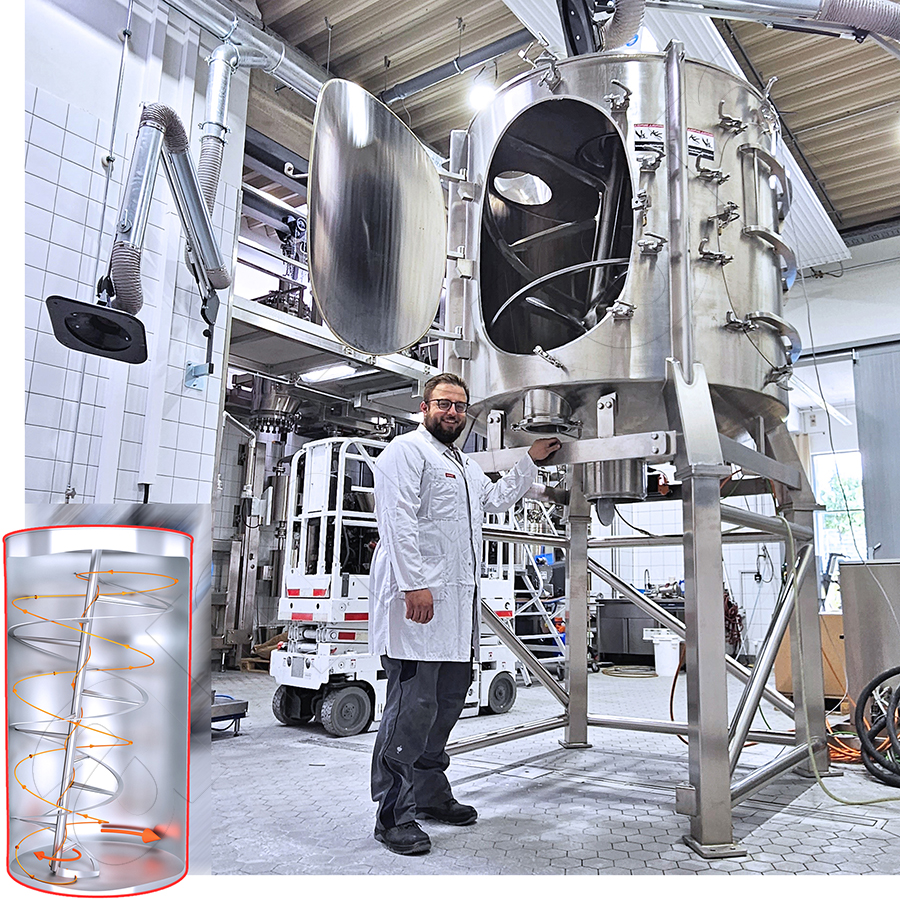
Large-capacity mixer
Large-capacity mixers, also known as large-capacity mixing silos, large-capacity silo mixers, large-capacity homogenisers or silo mixers, are process engineering devices for homogenising large quantities of bulk materials. Unlike conventional mixers, they are used less for intensive mixing and more for equalising the stored material during the storage period. The aim is to standardise a product manufactured in batches over the storage period.
A silo mixer typically performs a dual function. It serves both as a storage container for powdered bulk materials and as a simple mixing system. Homogenisation is usually achieved by small, mechanically moved mixing tools that only mix a small area of the silo. The better the powder flows, the better the homogenisation. In practice, however, such mixers only achieve rough homogenisation. Ideal distribution cannot be achieved with them. The mixing result is usually random: sometimes it is slightly better, sometimes slightly worse, but never really good.
As a general rule, the larger the volume of a large-capacity mixer, the lower the achievable homogeneity quality. Large-capacity mixers are therefore not suitable for applications where high mixing quality is required, especially if the powders flow poorly or there are differences in moisture content.
Precision mixers are the opposite of this. These have dynamically operated mixing tools that penetrate the entire mixing chamber, such as helix or ploughshare mixing tools. During the mixing process, all particles are in relative motion to each other. This results in a technically ideal mixing quality. This even applies to component compositions of up to 1:100,000. amixon GmbH will be happy to carry out tests for you.
Certain performance indicators apply to such processes. The specific drive power is at least 7 W per litre of mixed material and can be twice as high in some cases. A batch of 10 m³ therefore requires a drive power of at least 70 kW. The larger the batch, the greater the drive power required. This can be very high, especially with high bulk densities or poor flowability of the powders.
There are applications where large batches must be homogeneous. One example of this is the manufacture of engineering ceramics. Such materials are produced in long process chains with many successive processing steps. If the raw materials are uniform, the product quality remains constant at the end. In such cases, consistently high homogeneity is essential without having to intervene in individual process steps.
How have such requirements been handled in the past?
Many small batches were mixed individually with high precision and filled into exactly identical containers. Equal quantities were taken from each container. These partial quantities were then processed together in the same batch mixer. This ensured a high degree of initial homogeneity.
There is now a new solution for efficiently and economically homogenising large quantities of bulk solids up to 100 m³:
Gyraton®.
The company amixon® has developed this innovative mixing system. It enables ideal mixing quality at very low rotational speeds of the helix mixing tool, even with batch sizes of 20 to 100 m³. The technology combines high mixing quality with greatly reduced specific drive power. Compared to classic precision mixers, the drive power can be reduced by 80 to 90 percent. In return, the mixing time is extended by a factor of five to ten. That is, for example, 2 or 3 hours.