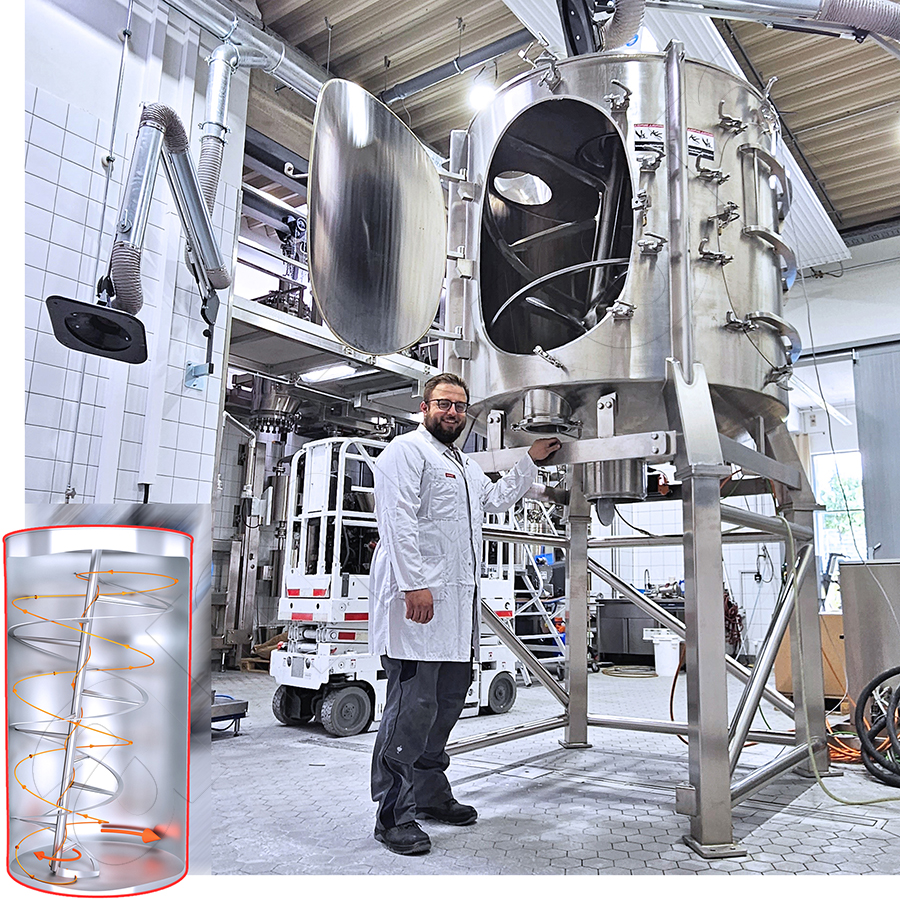
Mélangeur grande capacité
Les mélangeurs de grande capacité, également appelés silos mélangeurs de grande capacité, homogénéisateurs de grande capacité ou mélangeurs de silos, sont des appareils de procédé destinés à l'homogénéisation de grandes quantités de produits en vrac. Contrairement aux mélangeurs classiques, ils servent moins à mélanger intensivement qu'à uniformiser le matériau stocké pendant la durée de stockage. L'objectif est d'uniformiser un produit fabriqué par lots pendant la durée de stockage.
Un mélangeur de silo remplit généralement une double fonction. Il sert à la fois de récipient de stockage pour les produits en vrac pulvérulents et de système de mélange simple. L'homogénéisation est généralement assurée par de petits outils de mélange mécaniques qui ne mélangent qu'une petite partie du silo. Plus la poudre s'écoule facilement, plus l'uniformisation est efficace. Dans la pratique, cependant, ces mélangeurs n'obtiennent qu'une homogénéisation grossière. Une répartition idéale n'est donc pas possible. Le résultat du mélange est généralement aléatoire : parfois il est un peu meilleur, parfois un peu moins bon, mais jamais vraiment bon.
En principe, plus le volume d'un mélangeur de grande capacité est important, plus la qualité d'homogénéité obtenue est faible. Les mélangeurs de grande capacité ne conviennent donc pas aux applications qui exigent une grande qualité de mélange, en particulier lorsque les poudres s'écoulent mal ou présentent des différences d'humidité.
Les mélangeurs de précision sont tout le contraire. Ceux-ci sont équipés d'outils de mélange à fonctionnement dynamique qui pénètrent dans toute la chambre de mélange, tels que des outils de mélange hélicoïdaux ou à charrue. Pendant le processus de mélange, toutes les particules sont en mouvement relatif les unes par rapport aux autres. Il en résulte une qualité de mélange techniquement idéale. Cela vaut même pour des compositions de composants jusqu'à 1:100 000. amixon GmbH se fera un plaisir de réaliser des tests pour vous.
Ces processus sont soumis à des indices de performance spécifiques. La puissance d'entraînement spécifique est d'au moins 7 W par litre de produit mélangé et peut dans certains cas être deux fois plus élevée. Une charge de 10 m³ nécessite donc une puissance d'entraînement d'au moins 70 kW. Plus la charge est importante, plus la puissance d'entraînement requise est élevée. Elle peut être très élevée, en particulier lorsque la densité apparente est élevée ou que la fluidité des poudres est mauvaise.
Il existe des applications dans lesquelles les grandes charges doivent être homogènes. La fabrication de céramiques techniques en est un exemple. Ces matériaux sont issus de longues chaînes de processus comprenant de nombreuses étapes de traitement successives. Si les matières premières sont homogènes, la qualité du produit final reste constante. Dans de tels cas, une homogénéité élevée et constante est indispensable, sans qu'il soit nécessaire d'intervenir dans les différentes étapes du processus.
Comment ces exigences étaient-elles satisfaites jusqu'à présent ?
De nombreux petits lots étaient mélangés individuellement avec une grande précision, puis conditionnés dans des récipients identiques. Des quantités égales étaient prélevées de chaque récipient. Ces quantités partielles étaient ensuite traitées ensemble dans le même mélangeur de lots. Cela permettait de garantir une grande homogénéité initiale.
Il existe désormais une nouvelle solution pour homogénéiser de manière efficace et économique de grandes quantités de produits en vrac jusqu'à 100 m³ :
Gyraton®.
La société amixon® a développé ce nouveau système de mélange. Il permet d'obtenir une qualité de mélange idéale à des fréquences de rotation très faibles de l'outil de mélange hélicoïdal, même pour des tailles de lots de 20 à 100 m³. Cette technologie allie une qualité de mélange élevée à une puissance d'entraînement spécifique fortement réduite. Par rapport aux mélangeurs de précision classiques, la puissance d'entraînement peut être réduite de 80 à 90 %. En contrepartie, le temps de mélange est multiplié par cinq à dix. Cela représente par exemple 2 ou 3 heures.