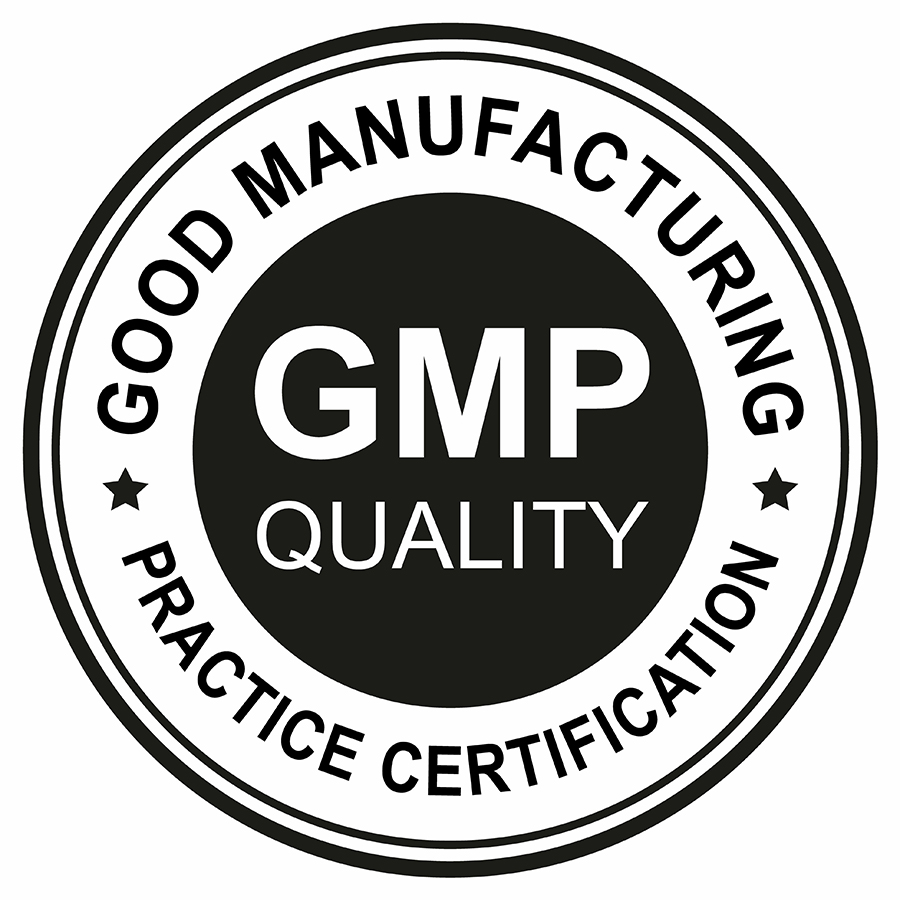
Good Manufacturing Practice
GMP stands for ‘Good Manufacturing Practice’. These are binding guidelines for quality assurance in the manufacture of medicinal products, active substances, foodstuffs and medical devices. The aim is to manufacture products that are safe, effective and of consistent quality.
The origins of GMP date back to the 1960s. Today, GMP requirements are harmonised worldwide, for example by the WHO, the EU GMP guidelines or the ICH regulations. They are considered an international standard. ICH stands for ‘International Council for Harmonisation of Technical Requirements for Pharmaceuticals for Human Use’.
ICH guideline Title Relevance for machine builders
- Q7: GMP for active pharmaceutical ingredients (APIs): Requirements for equipment, cleaning, cross-contamination, maintenance and documentation
- Q8: Pharmaceutical Development - Focus on process understanding – machines must support reproducible processes
- Q9: Quality risk management: Machines should enable risk-based maintenance, cleaning and process control.
- Q10: Pharmaceutical quality system: Mechanical engineering must be integrated into an overarching quality system, including a life cycle approach.
GMP therefore does not only affect manufacturers of pharmaceutical or food products. Machine and plant manufacturers are also indirectly affected. This is because GMP-compliant production is only possible if the machines used work hygienically and precisely. Surfaces must be cleanable. Dead spaces must be avoided. The machines must not cause product contamination or cross-contamination. Q12: Lifecycle management: Changes to machines and systems must also be documented, evaluated and approved.
Another important contribution made by machine manufacturers is qualification documentation. Certain evidence must be provided for every GMP-relevant machine. This includes:
- DQ (Design Qualification): Proof that the design meets the requirements.
- IQ (Installation Qualification): Documentation of correct installation in accordance with specifications.
- OQ (Operational Qualification): Checking that the machine functions as intended.
- MQ or PQ (Performance Qualification): Validation of performance in practical operation.
Machine manufacturers support their customers in preparing these documents. To this end, they supply drawings, material lists, calibration protocols, FAT documents (Factory Acceptance Test) and cleaning certificates. This makes them an integral part of a GMP-compliant overall system.
GMP is also relevant during ongoing operations. The machines must deliver reliably reproducible results. They must be regularly maintained, cleaned and qualified. Documentation and traceability play a central role in this.
GMP is not a one-off project, but a permanent quality system. Machine manufacturers help to ensure that it is technically sound right from the start.