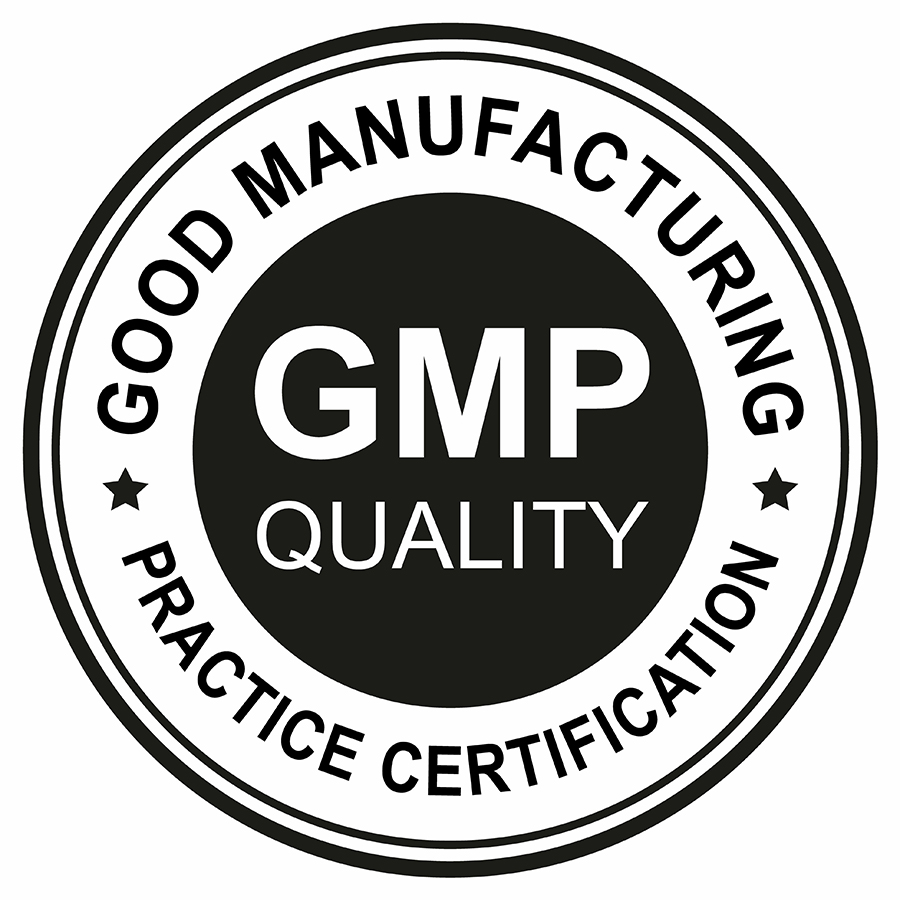
GMP(適正製造規範)
GMPとは "適正製造基準"の略。 医薬品、有効成分、食品、医療機器の製造における品質保証のための拘束力のあるガイドラインである。 その目的は、製品を安全かつ効率的に、安定した品質で製造することである。
GMPの起源は1960年代にさかのぼる。 今日、GMPの要件は、例えばWHO、EUのGMPガイドライン、ICH規則などによって、世界的に調和されている。 これらは国際標準とみなされている。 ICHとは "国際人間用医薬品技術基準調和評議会 "の略である。
ICHガイドライン名 機械エンジニアにとっての関連性
- Q7:原薬GMPについて教えてください: 設備、洗浄、交差汚染、メンテナンス、文書化に関する要求事項
- Q8: 医薬品開発 - プロセスの理解に注力 - 機械は再現可能なプロセスをサポートしなければならない
- Q9:品質リスク管理:機械は、リスクベースのメンテナンス、洗浄、プロセス管理を可能にすべきである。
- Q10:医薬品の品質システム:機械工学は、ライフサイクルアプローチを含む包括的な品質システムに統合されなければならない。
したがって、GMPが影響を及ぼすのは医薬品や食品技術製品の製造業者だけではない。 機械メーカーやプラントメーカーも間接的に影響を受ける。 GMPに準拠した生産は、使用される機械が衛生的かつ正確に作動して初めて可能になるからだ。 表面は清掃可能でなければならない。 デッドスペースは避けなければならない。 機械が製品汚染や二次汚染を引き起こしてはならない。 Q12:ライフサイクル管理:機械やシステムの変更を文書化し、評価し、承認することも可能でなければならない。
機械メーカーによるもう一つの重要な貢献は、適格性確認文書にある。 GMPに関連するすべての機械について、一定の証拠を提供しなければならない。 これには以下が含まれる。
- DQ(デザイン・クオリフィケーション): 設計が要求事項を満たしていることの証明。
- IQ(設置資格): 仕様書に従って正しく設置されたことを証明する文書。
- OQ(オペレーション・クオリフィケーション): 機械が意図したとおりに機能するかどうかをチェックすること。
- MQまたはPQ(パフォーマンス・クオリフィケーション): 実運用における性能の検証。
機械エンジニアは、これらの文書の作成において顧客をサポートする。 図面、材料リスト、校正プロトコル、FAT(工場受入試験)文書、洗浄証明書などを提供する。 そのため、GMPに準拠したシステム全体の不可欠な一部となっている。
GMPは運転中にも関係する。 機械は確実に再現性のある結果を出さなければならない。 機械は定期的にメンテナンスされ、洗浄され、適格でなければならない。 ここでは、文書化とトレーサビリティが中心的な役割を果たす。
GMPは単発のプロジェクトではなく、恒久的な品質システムである。 メカニカル・エンジニアは、当初から技術的に安全であることを保証する手助けをします。