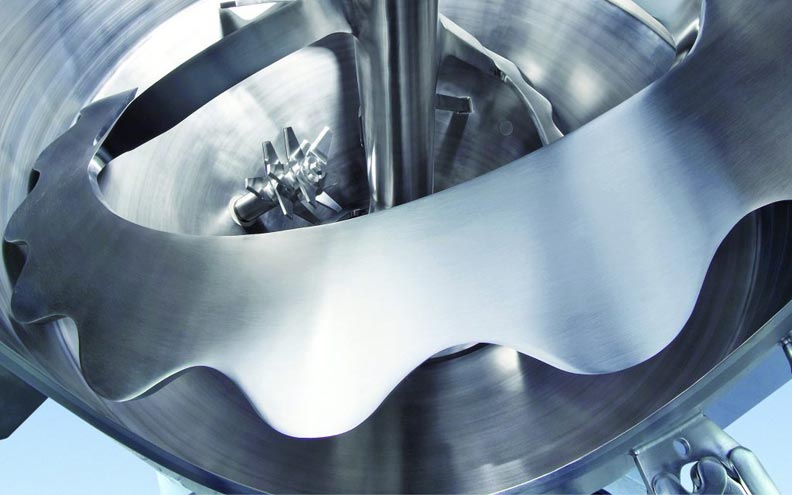
The SinConvex® mixing spiral is inclined outwards (convex). The mixture flows off completely.
New powder mixing generation with complete discharge
The thought seems fascinating and disconcerting to anyone who mixes bulk solids: "If a mixing plant were to discharge itself 100% automatically, any cleaning would be obsolete". Contamination risks would be eliminated.
If you get an overview of the technology of solids mixing, you quickly get the impression that actually all industrially usable mixing principles have long been invented. Differences are at most visible in nuances of different manufacturers.
In principle, this statement is true, but there are exceptions! Continuous further developments of amixon® are approaching the goal of being able to empty a powder mixer completely!
There are continuous further developments on the part of amixon® for powder mixers with vertical mixing tools. They pursue the goal of user benefits of the operators:
- Ideal mixing qualities independent of the degree of difficulty of the mixing task
- Residue-free discharge of the mixed materials
- Exemplary hygienic properties
- Easy operation, long service life, low noise emission
- Economical consumption of resources
amixon® powder mixers and dryers are tailor-made solutions manufactured according to the customer’s requirements.
Mixing takes place free of dead space by means of three-dimensional rearrangement.
The performance of vertical helical mixers is certainly undisputed. A helical mixing unit rotates around a vertically mounted axis. The mixing goods are conveyed upwards in the periphery of the mixing chamber. From the top, the goods flow downward, obeying the force of gravity. The downward flow takes place in the center of the mixing chamber.
The mixing tools of the amixon® mixers generally rotate slowly. Their peripheral speed is usually only 0.8 m/s to 2.5 m/s. This is the reason why amixon® precision mixers homogenize particularly gentle. They normally do not change the granulometry and texture of the bulk solids. Another major advantage is that the mixing tools are only supported and driven from above. In this respect, they meet the highest hygiene requirements and are virtually maintenance-free.
A standard mixer helix approaches the vessel wall at a 90° angle.
In some cases, however, users of standard vertical mixers have had to accept a disadvantage: If the mixing goods flow poorly (include particularly fine particles or are moist or greasy), then residues can stick to the spiral tool after discharging. In this case, complete discharge is not possible. Not even by particularly accelerating the rotation of the mixing tool.
The SinConvex® and SinConcave® versions are highly efficient further developments of the conventional mixer spiral.
This is exactly, where an innovative solution from amixon GmbH comes in. In the new generation of amixon® mixing units, the spiral tool is tilted either inwards or outwards. Tests have shown, that mixing efficiency is actually improved in this way.
In addition, this design detail increases the discharge efficiency quite considerably. Take, for example, a 2 m³ cylindrical amixon® mixer that has been mixing a milk-based baby formula. After discharging, the residual quantity is only 240 grams. This corresponds to a residual discharge rate of 99.983%.
ComDisc® tools are discharging devices for particularly good residual emptying.
The product residue on the floor can be effectively discharged by ComDisc® tools. The remaining mixing good is only a few grams of powder. Operators of this new generation of amixon® mixers enjoy three advantages:
- The mixer can be operated with differing filling levels from 10 to 100 %.
- One and the same amixon® mixer can homogenize extremely gently, but it can also deagglomerate intensively. It can distribute liquid additives micro-fine in the powder. A single amixon® precision mixer is sufficient to perform different mixing tasks.
- In practice, thorough residual discharging means raw material savings, less cleaning effort and time savings. The production process is virtually contamination-free. Almost all raw materials used become saleable goods. Waste is avoided. Disposal costs are saved. This is an important contribution to environmental protection and the saving of our resources.
The ComDisc® tools have no function during the mixing process. They float in the mix. Only in the final emptying phase do they settle on the floor and remove the ideally mixed powder residues. ComDisc® tools are particularly wear-resistant. They are made of food-safe material.
The amixon® team would like to invite you to presentations, mixing trials and a factory tour. You will be surprised
- by the variety of solutions amixon® experts have developed over more than 40 years and
- by the excellent mixing results.
© Copyright by amixon GmbH