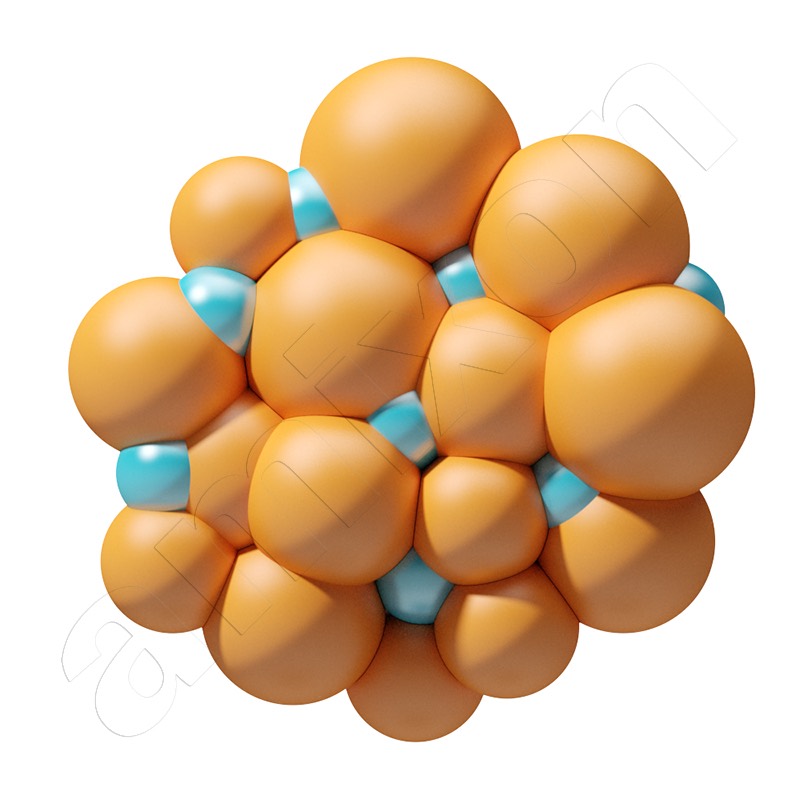
The water molecule has a dipole character. It has special wetting and dissolving properties. When a powder is wetted with water, the particles want to stick together. Water is a frequently used binding agent for agglomeration processes.
Factors for effective powder moistening in the mixing process
In almost all areas of the bulk goods processing industry, powders are wetted with liquids.
This process seems trivial. Sometimes the humidification results are unsatisfactory. Lumps may form, the liquid may not be homogeneously distributed or the bulk material may subsequently have poor flow properties.
How liquid-affine is the powder surface? What is the capillarity of the powder?
Typical manifestations of different liquids are first of all:
a. Low surface tension
b. High surface tension
c. Backflowing liquid
d. Advancing liquid
e. Liquid is injected into the turbulence area of the swirler (single-fluid nozzle)
f. Liquid is sprayed microfine and the powder is fluidised (two-substance nozzle)
Capillarity of the powder and surface tension of the liquid
If the surface tension of a liquid is low (a), then the liquid wants to wet the solid surface spontaneously. The capillaries (5) of a particle are then also penetrated. The higher (b) the surface tension of a liquid, the less the liquid wants to penetrate the capillaries of the particles. The same applies to the cavities of a powder mixture. If the surface tension is high, liquid distribution in the powder is only possible if the liquid and particles are intensively mixed and rubbed together.
The homogeneous wetting of a powder is not trivial.
In the dry state (1), the powder is present as a solid-air dispersion. The cavities between the particles are uneven and change constantly during mixing. If a liquid is poured into the moving mix, the air must be displaced from the cavities. The liquid is distributed as a thin liquid layer around each individual particle. It is called the adsorption layer (1). The adsorbed liquid adheres firmly and can only be removed thermally. If the liquid content increases during mixing , the liquid collects at the contact points of the particles in so-called bridges and (2) gussets. The "gusset fluid" can bind the particles together. This allows agglomeration(build-up granulation) to begin. As the liquid content increases, larger free spaces (3) between the solid particles are filled with liquid. Once all the capillaries formed by the particle system are filled with liquid, (4) saturation takes place. The bulk material becomes a suspension.
If the surface tension of the liquid is low and the affinity between the liquid and solid is particularly high, so-called flash absorption can take place. The available liquid is immediately absorbed by the solid. This often leads to unwanted agglomerates. But a prolonged mixing process can hardly improve the liquid distribution. In cases of high affinity between powder and liquid, the liquid should be added (as shown in figure f) at a constant slow rate, dosed and sprayed during mixing. Spraying below the bulk material level usually improves the self-cleaning of the mixer.
Nowadays, it is easy to analyse the properties of liquids and bulk solids. Is it still appropriate to carry out practical mixing tests in mixers?
In fact, we can now analyse the characteristics of liquids and powders quickly and accurately. Unfortunately, however, disperse systems consisting of different powders are too complex to simulate their mixing or even their moistening. For the foreseeable future, the computational effort will be much more expensive than the practical test.
In the amixon® technical centre a wide variety of wetting processes are used almost daily. We would be happy to demonstrate these processes to you using your original products and show you how your wetted powders look and flow afterwards.
Powder moistening can lead to unwanted soiling of the mixer
Depending on the viscosity and stickiness of the liquid, unwanted adhesion may occur. These can form on the wall or on the mixing tools.
As a rule, it is advantageous if the mixing chamber has a high filling level. The dry powder components should be filled in first. Mixing the powder components is the preliminary stage of wetting. The way in which the liquid material is added is of great importance. High concentration differences must be avoided. amixon® uses liquid addition lances that protrude into the lower part of the mixing chamber. The volume flow of the liquid addition should be based on two parameters:
- Adsorption capacity of the powder
- Speed of the mixing tools. The faster the powder flows, the more evenly the liquid is distributed in the powder.
Deposits and adhesions of liquid substances must be avoided at all costs. They should only be tolerated in exceptional cases, as they can cause major problems:
- The final product lacks precisely those liquid components that contaminate the mixer.
- Any build-up can increase with each batch. They can dissolve during mixing and contaminate the mix in an uncontrolled manner.
- Adhesions increase friction during mixing. The mix is heated unintentionally.
- Strongly adhering caking can block the mixing tools.
The best method of liquid addition during mixing can be determined by tests in the amixon® technical centre.
© Copyright by amixon GmbH