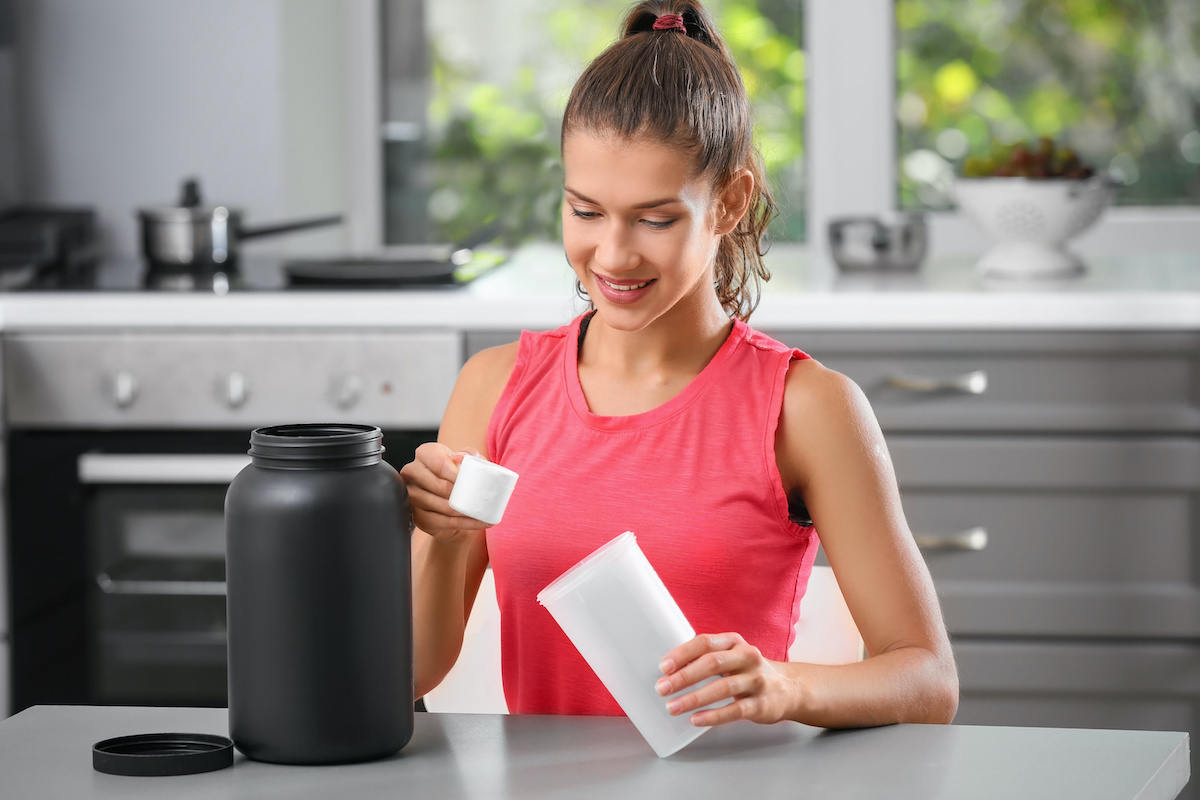
The right mix for health and more performance
The composition of natural active ingredients is important for the success of a good dietary supplement. Equally important are good tolerability and a pleasant taste. The mixing system used to blend the powders influences the appearance, solubility and bioavailability.
Here we describe how amixon® powder mixers with innovative technologies ensure uniform mixing, efficient dust control and compliance with high hygiene standards.
Improving the quality of powdered dietary supplements, sports nutrition products, diet products and generic drugs in powder form:
- optimal homogeneity
- gentle processing – no heat input
- exemplary hygiene standards
- up to 99.986% discharge of the mixer. You save a lot of money every day
Good residual emptying saves a lot of time and money
The illustrated amixon® HM 7000 precision mixer can mix batches of up to 7 m³ of material. The result is an ideal random mixture*. The mixing quality cannot be improved in practice. This is regardless of whether the maximum filling is 7,000 litres or only 800 litres.
*) An ideal random mixture cannot be improved in practice, regardless of the mixing system used.
It should be particularly emphasised that amixon® twin-shaft mixers mix very gently. The peripheral speed of the mixing tools can be adjusted between 0.8 and 1.4 m/s. Nevertheless, the mixing time is only 2 to 5 minutes.
This amixon® mixer was retrofitted with ComDisc®. This improves the emptying of residues. Depending on the mixture, the emptying of residues is 0.5 kg to 0.8 kg. This corresponds to 0.09 to 0.14 per thousand based on the batch mass of 5600 kg.
ComDisc® tools push the mix residue from the bottom into the discharge nozzle. This is done automatically and without segregation. The mixer remains closed until complete emptying.
amixon® conical mixers also empty themselves almost completely
Individuality is also expressed in nutrition. There are pescatarians, lacto-ovo vegetarians, lacto-ovo vegetarians and lacto-ovo vegetarians. There are fruitarians, raw foodists, paleo and carnivores. Still others follow a kosher, halal or Ayurvedic diet. Those who consciously choose a particular diet usually take equally conscious steps to ensure they are getting the vitamins and nutrients they need in the form of food supplements.
One form of personal optimisation is ‘body or biohacking’: body hackers deliberately introduce substances into their bodies that are supposed to enhance their own performance: think faster, think more freely, perform better in sports, look smarter...
The demands on food supplements are correspondingly high. They should be quick and easy to take anywhere and be safe to use. Combination products are in demand and the shelf life of the products is important. That is why it is sometimes necessary to coat certain active ingredients before they are mixed with other powders. In addition, the taste must be pleasant, regardless of whether it is a large pack, tablet or sachet. The distribution of the active ingredients must always be exact.
Precision and cost advantages for large batches
Mixers in the production of food supplements are therefore subject to particularly high demands on the achievable homogeneity of the mixture.
Only so-called “precision mixers” can be used to meet these mixing quality requirements. Precision mixers consist of a fixed mixing chamber and moving mixing tools. These must use the entire space to spread the components about the chamber and to create a random mixture. This is how a technically ideal mixing quality is achieved, one that cannot be improved in practice. In addition, the mixer should work quickly in the production of the food supplements, but not change the particle shape or size of the raw materials. These requirements very much limit the range of mixing systems that can be considered, with a vertical design proving to be particularly suitable.
The outstanding mixing efficiency of this design is demonstrated when the smallest quantities of anti-caking agents have to be mixed in for further processing in tablet presses. These substances are very light, clumping and very difficult to distribute. However, they lose their actual anti-caking effect very quickly as soon as they are exposed to pressure or shear stress. Ideally distributing very small quantities while maintaining their full effectiveness is a special skill that amixon mixers have mastered with confidence, even with large batches.
Bulk batches have many advantages for manufacturers of FS. The effort for providing and weighing the individual components is drastically reduced. At the end of the mixing time, one-off sampling and evaluation is sufficient. As a result, large batches can often save many thousands of euros.
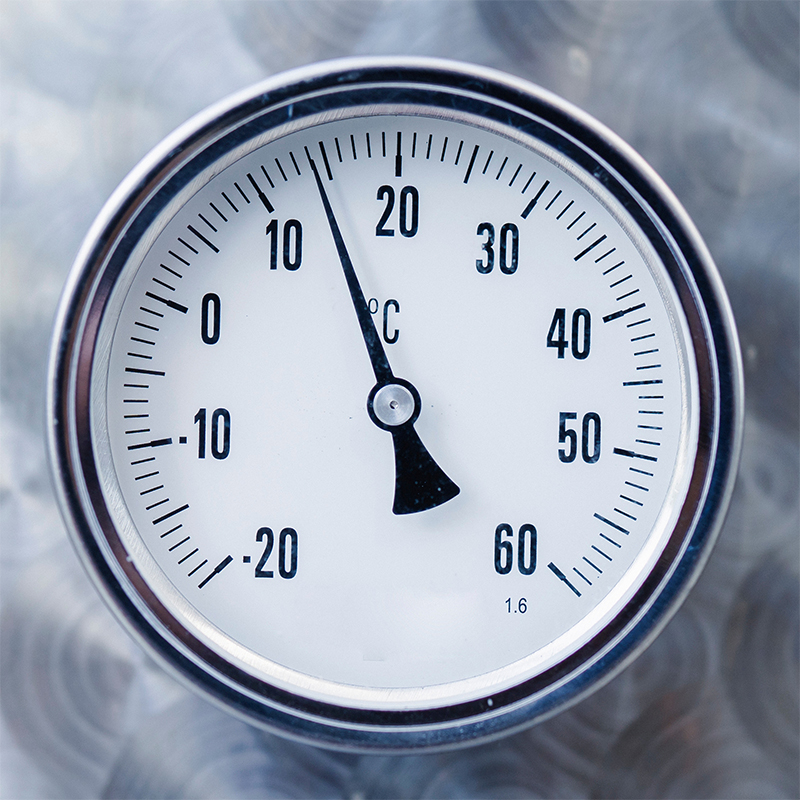
The amixon® mixing process leaves no measurable heat input in the mix.
Mixed materials must not heat up during the mixing process.
Mr Alexander Voitl adds another important aspect to the list of requirements for the mixers: ‘Some of the ingredients are very sensitive, which is why low temperature development during the mixing process is very important to us.’
In many applications - even with large batches - amixon has been able to prove that the energy input is minimised each time. No heat tinting can be registered in the product, nor is there any significant increase in dust.
The latter is particularly important for the consumer, who expects good solubility and dispersibility of the finished product. However, it also plays a role when high-performance packaging machines fill sachets and pouches.
The fact that the temperature of the mixture does not rise during the mixing process is essential for the shelf life of the food supplements in the global distribution process. If the mixed products are packaged when warm, they can clump together and micro-condensation can cause unwanted discolouration.
Maintaining the stability of the products is therefore extremely important for manufacturers for quality reasons alone. At Herbalife Nutrition, for example, a dedicated team takes care of product stability under different climatic conditions of use and transport of the food supplements. The suitability of new product formulations and packaging is tested in special stability chamber tests before they go into production.
Cleaning efficiency determines the degree of flexibility
Due to frequent recipe changes and because of the strict specifications for pharmaceutical production, the mixers used in the production of FS should be validatable in a short time and easy to clean.
Alexander Voitl gives an insight into mixer selection in practice. “Before we use a mixer, it must successfully and safely pass the qualification and validation procedures. The space-saving vertical twin-shaft mixers from amixon have all passed these tests.”
The installation and operation of the mixer is ensured during this qualification process. For validation, the mixing and cleaning processes must also be checked for conformity to the defined specifications. If a mixer does not pass this qualification, it cannot be used in production according to the specifications.
During wet cleaning of a precision mixer, for example, rotating washing heads are lowered/inserted into the mixing chamber from above and from the side. At the same time, the mixing tools rotate and ensure that all surfaces in contact with the product are flushed with water. The wash water is discharged at the lowest point in the bottom of the mixer.
Since the heat capacity of stainless steel is only 11 percent of the heat capacity of water, the mixer heats up very quickly when cleaned with warm water. That is why the machine dries more quickly afterwards. As a rule, no detergents are needed for cleaning.
Multi-stage wet cleaning is only needed if very intensive colours or aromas have been processed. It consists of pre-wetting, foaming and rinsing. The same applies when liquids have to be mixed in micro-droplets into a powder and consequently unwanted adhesions have to be washed off. Given good organisation, washing and drying takes an hour.
Many nutrient processing plants successfully carry out drying and cleaning by mixing one or two rinsing batches. These rinsing batches are properly packaged so that they can be used again later as a recyclable material if the recipe is suitable.
Here it becomes clear how valuable the individual mixtures can be in food supplements. That is why another feature of the mixer is crucial in the manufacturing process - the degree of residue emptying. With the vertical mixer from amixon, the 7,000 litres of mix can be discharged down to a residue of 0.5 litres, or 0.007 percent.
Why does 0.007 percent matter? Because every extra gram that the mixer produces can be sold and does not have to be disposed of. The less residue that remains in the mixer, the easier and faster the cleaning process, the lower the potential contamination and the higher the batch reproducibility.
For good process efficiency, it is the small constants that ultimately influence the cost of producing the FS. So if set-up and cleaning times can be clearly planned and are short, and the product quantities to be discarded are low, the bottom line is higher margins for the food supplement manufacturer.
Strictly regulated on the borderline to medicine
§ 1 of the Nem (Food Supplements Ordinance) defines food supplements as foodstuffs which:
- are intended to supplement the general diet (intended use);
- are a concentrate of nutrients or other substances with a nutritional or physiological effect, alone or in combination (composition), and
- are brought to the market in dose form, in particular in the form of capsules, pastilles, tablets, pills and other similar dosage forms, sachets of powder, ampoules of liquids, bottles with droppers and similar dosage forms of liquids and powders for ingestion in measured small quantities (dosage form).
Food supplements are therefore foods that serve to supplement the general diet with vitamins, minerals or other substances such as amino acids, dietary fibres or secondary plant substances. They contain the nutritionally effective nutrients in concentrated form and in dosed quantities.
Demarcation from drugs is not always easy. Food supplements must not have pharmacological properties, as required by the definition of medicinal products in § 2 of the German Medicines Act (AMG), or give the consumer such an impression.
Distinguishing them from foods for general consumption can sometimes be difficult as well. According to the definition of the term “food” in Art. 2 of the Basic Regulation, this includes all substances or products which serve the purpose of nutrition, whereas food supplements are intended to supplement the normal diet.
Production according to pharmaceutical guidelines
The requirements for the production technology used to prepare FS for pleasant intake by the consumer, correspond to those for food and pharmaceutical production according to relevant technical specifications as specified by GMP/FDA.
Because ever newer packaging variants and ingredients for FS are entering the market, many manufacturers rely on the services of contract manufacturers. They know the high demands in production very well and are able to produce the required outstanding and consistent quality.
FS manufacturers take advantage of the production flexibility of contract manufacturers and their readiness to tackle new challenges. This is because the different dosage forms require different, sometimes specialised and investment-intensive, manufacturing and packaging processes.
However, when sales volumes reach a certain level, Herbalife Nutrition, for example, which produces about 65% of its food supplements itself, takes over the production in-house and expands the existing know-how and process knowledge internally.
High quality under strict observation
Since the products must be 100% traceable, as is also the case in the pharmaceutical industry, quality assurance usually begins at the incoming goods stage. Many manufacturers, including Herbalife Nutrition and Nutrichem, monitor quality at various points in the production process. The focus is on the feeding of the mixers, the mixing process including sampling and precisely reproducible mixing ratios, right through to routine packaging inspection and an accurate cleaning analysis carried out on all product contact surfaces throughout the process.
Nutrichem produces food supplements in the form of powdered products with trace elements, vitamins and minerals which can be mixed with water and consumed as a drink by the consumer. The company does 100% of the production itself.
“The quality of our products is examined in multi-stage control procedures consisting of chemical, physical and microbiological processes. Regular internal and external audits as well as continuous staff training help us to achieve and maintain an especially high product quality,” says Alexander Voitl, Opex Manager at Nutrichem Diät + Pharma GmbH, describing their special challenges.
The foundation stone for homogeneity and thus for the outstanding quality of powdered products in particular is therefore laid as a first step by a stable and reproducible mixing process, and not only at Nutrichem. A reproducible and homogeneous mixture also has a positive effect later in the process, because efficiency on the packaging line increases due to a uniform product flow.
amixon® vertical twin-shaft mixer
Two vertically mounted helix mixing tools rotate in the same direction, with the mixing chamber formed by their enveloping surfaces as they rotate. The components involved in the recipe are poured or sucked into the mixing chamber from above. After about 50 to 60 revolutions, an ideal mixing quality is achieved. Depending on the rotational frequency of the mixing tools, this corresponds to a mixing time of approximately 2 to 5 minutes.
Then a bottom valve that closes without dead space opens and the mixture is discharged without segregation. The shear flow that takes place here is described as ‘three-dimensional redistribution’. The mixing tools convey the goods upwards at the periphery and, following the force of gravity, allow them to flow downwards in the centres, along the mixing shafts. At the same time, the mixing tools expel the goods radially.
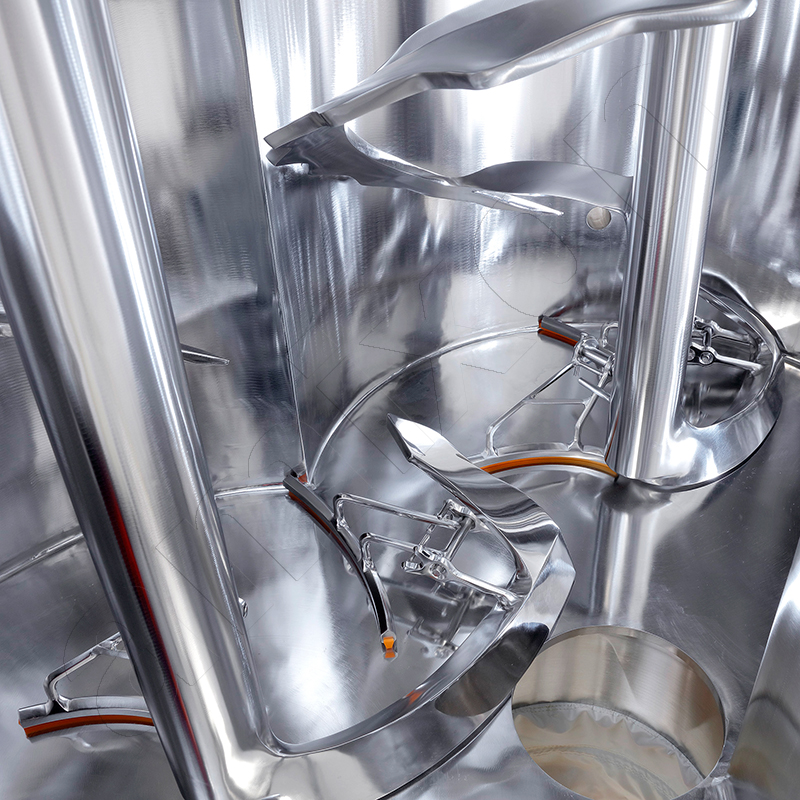
ComDisc® tools (optionally retrofittable) remove even the last powder residues - down to a few grams.
Food supplements are strong sales drivers
Consumers have high expectations of the product performance of food supplements. The dosage form should be convenient, and it should be quick and easy to take anywhere. Combination preparations (as a drink or in solid form) are in demand and the shelf life of the products is important.
In 2018[1], 1.439 billion euros were spent on food supplements (NEM for short) in Germany, according to the umbrella organisation of the German food industry. That's 225 million packs. In purely statistical terms, that's almost three packs per person per year. Vitamin C, multivitamin supplements and the minerals magnesium and calcium are purchased most frequently.
Statista arrives at slightly different figures for 2019, but still a significant increase: 75 million units (+3 million compared to 2018) of vitamins and minerals were purchased by consumers for a total of €1.1 billion (+€240 million). Magnesium is also in first place at Statista. Vitamin B products are becoming increasingly popular. In addition to magnesium, vitamin C supplements are also important sales drivers. More than two thirds of Germans have already taken dietary supplements or can imagine doing so in the future.
The reason for this trend lies in modern society: those who perform measurably are recognised. And those who overcome challenges with a smile and an ‘I can do it - yes, we can! This starts at school and doesn't stop when they retire. Because even the ‘best agers’ want one thing above all else: to stay fit and healthy.
This trend is not new. For a long time, nutrition-conscious consumers have been able to buy classic health food products.
But only those who prevent nutritional deficiencies and are resistant to pathogens can remain mentally and physically active in the long term. Health is the basis for happiness and contentment. The flu pandemic has shown this particularly clearly.
‘According to a survey of more than 1,000 people aged 18 and over conducted by the market research institute YouGov, 61% of respondents want to improve their general state of health, 36% want to prevent colds, 39% want to optimise their bodily functions and 33% want to increase their fitness.
But even a healthy body needs more fuel to perform at its best than in normal operation. A balanced diet is usually enough, but not always. More and more people are turning to dietary supplements. The dosage forms are: Effervescent tablets, effervescent powders, soluble powders, sticks, tablets or capsules.
Typical topics in solid dosage forms and solid generics
In fact, there are many similarities between the manufacture of active pharmaceutical ingredients and the manufacture of food supplements (protein shakes, dietary supplements, mineral drinks, enteral nutrition powders).
- Purity of raw materials
- Selection of excipients: fillers, (binders, lubricants and disintegrants for compressed tablets)
- Hygiene in production and in the production environment
- Regulatory requirements
- Bioavailability
- Prescription formulation and mixing quality
- Care and efficiency, especially in the composition of the components and the order of the addition of the components (mulistep mixing order)
- Displacement of atmospheric oxygen from the powder mixture by pure nitrogen or carbon dioxide. The mixing process and filling are carried out under inert gas conditions.
Pharmaceutical products in the form of tablets, capsules or powder
If active ingredients in powder form are effective as pharmaceutical products, further requirements apply:
- Approval procedures must fulfil legal test criteria. The specific effectiveness of the pharmaceutical product must be proven.
- Some powdered food supplements are used for parenteral nutrition (injection into the bloodstream). These food supplements must be liquefied and sterilised. Class A clean room conditions must be maintained.
- Highly concentrated pharmaceutical active ingredients (HPAPIs: Highly Potent Active Pharmaceutical Ingredients) can pose a hazard. They must be dosed very precisely. They are ‘diluted’ in stages with powdered fillers. In older textbooks on galenics, the term ‘trituration’ is used.
- Typical fillers (diluents) are: starch, calcium carbonate, sarbitol, microcrystalline cellulose, ethylcellulose, lactose, sucrose,....
- In these cases, the active ingredients are handled and the logistics are carried out with the help of isolators in a high-containment process.
© Copyright by amixon GmbH