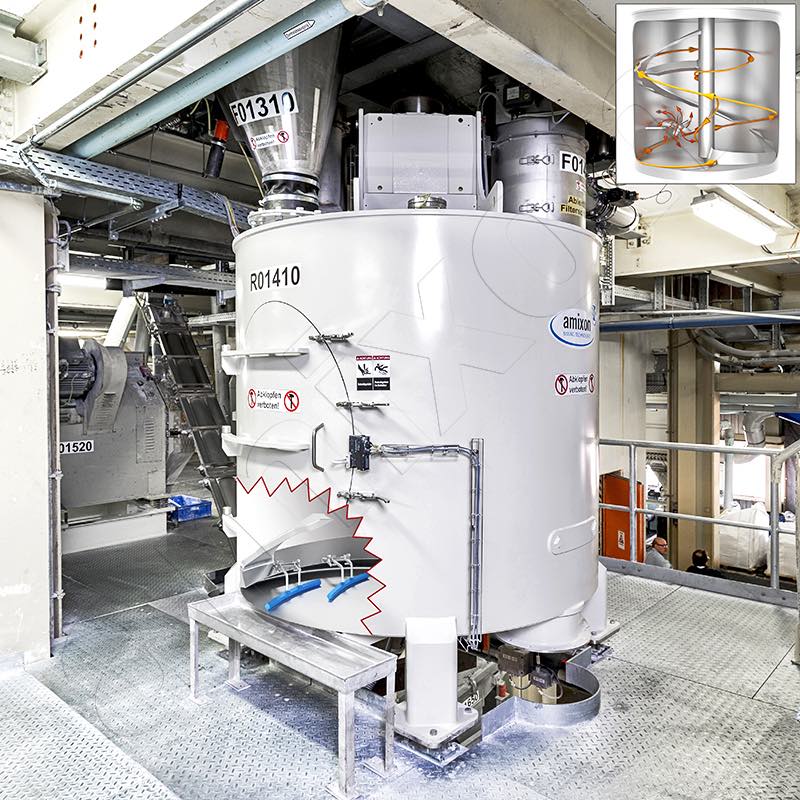
Optimum complete discharging with SinConcave® and ComDisc® technology.
FAQ: Innovation: Powder mixers discharge completely. Can abrasive powders wear out mixing tools?
In this blog article we address some common questions from amixon® interested parties about the advantages of our innovative complete emptying and the wear factor of mixing plants. If you do not find the answer to your potential questions in this article, please contact us personally. We look forward to you!
It is undisputed that amixon® vertical single-shaft mixers produce ideal mixing qualities. But can such a flat-bottomed powder mixer empty to such a high degree that more than 99.95% of the filled powders are discharged ideally mixed?
In practice, this means that, for example, in the case of an amixon® mixer with a useful capacity of 1000 liters, less than 0.5 liters of residue remain in the mixer after the mixing process; or less than 2 liters in the case of a 4000-liter batch. Furthermore, the larger the mixing batches, the smaller the percentage of residue. Volume increases with the third power of expansion. However, the surface area of a mixer increases only with the second power of expansion.
Back to your question: Yes, this is possible thanks to innovative amixon® technologies: These are the ComDisc®, SinConcave® and SinConvex® systems. Sometimes our customers want amixon® to guarantee a residual discharge percentage. amixon® can only agree such assurances on a product-specific basis. Each powder has specific flow properties. Flowability is influenced by moisture, particle size distribution, electrical charge, temperature, cohesion, adhesion, etc. amixon® always requires tests with your original products for this purpose.
In practice, significantly better residual discharge rates will always be achieved with the additional equipment ComDisc®, SinConvex® and SinConcave.
SinConcave® mixing tool
The mixing unit spirals are inclined concavely to the mixing unit axis. In this way, the slope of the mixing mechanism helix is supplemented by the slope of the tilt. The entire mixing tool consists only of strongly inclined surfaces. Gravity allows free-flowing mixing materials to flow downwards without segregation. Nevertheless, the helical shape is retained. It is essential for the high mixing efficiency.
Even 99.997 % residual discharging can be achieved.
ComDisc® Tools
are located on the back of the lower mixer arm. They float through the mixing material and have no significance during mixing. Only when the fill level drops do they tilt and clear the mix residues into the discharge nozzle. ComDisc® tools work in a similar way to windscreen wipers. They normally only touch the bottom of the mixer when the discharge is advanced.
How do ComDisc® tools behave when the mixing materials are abrasive?
Mixing materials with hard particles such as quartz sand, corundum or calcined materials exclude the use of ComDisc® discharge tools. Then a thin layer of mixing material remains in the mixer. However, this powder layer is ideally homogeneously mixed. After filling an identical mix formulation, these residues take part in the mixing process. At the end of the mixing campaign, this residue can be removed manually. The mixture residue is ideally homogeneously mixed.
The rubber lips of the ComDisc® tools are made of food-grade plastic. They are not expensive and can be replaced in a few simple steps.
How do the metallic mixing tools change when mixing materials are particularly abrasive?
First of all, you notice that the surfaces become smoother and smoother. They become as smooth as mirrors. You can also see that edges become rounded. These effects are more visible in the periphery than in the centre.
If the wear continues, there will be a visible loss of material on the mixing tool. Worn material should then be replaced by welding application. The filler metal should be harder than the mix particles. The procedure is called "weld armouring". Such repair measures are carried out by amixon® experts at the customer's site in the mixer. The mixer does not have to be dismantled. A few hours after the armouring, the customer can clean and continue production. It should be noted at this point that wear develops approximately with the square of the mixing tool speed. The mixing tools of the amixon® mixers rotate slowly, the circumferential speeds are normally only approx. 0.9 m/s to 2.2 m/s.
What happens when the mixing materials grind the mixer mirror-bright and material loss becomes visible at the mixing unit? Can it happen that a new vertical mixer mixes better than an older vertical mixer? Or vice versa?
We can report that the areas of a mixer exposed to wear become particularly smooth. They are even polished to a shine by the mixing material. The coefficient of friction resulting from the "powder and metal" pairing is thus reduced. For this reason, you can be sure of the durability of your ideal mixing material. Low material removal at the mixing tool has no influence at all on the mixing quality/mixing efficiency.
Can such coefficients of friction (sliding friction coefficient) change?
Of course, we were also concerned with this question when the mixing system was developed about 40 years ago. Since 1980, thousands of such flat-bottomed vertical mixers have been manufactured. They are used successfully in almost all industries. Many are still working flawlessly for almost 40 years. All empirical data regarding mixing quality is positive.
If the mixing tool is retrofitted with a welding armour, doesn't the mixing vessel also have to be repaired?
Not usually. amixon® employees can quickly measure the thickness of the mixing chamber wall. We generally register very little wear there. In this respect, we see extremely little need for action on the mixing chamber.
© Copyright by amixon GmbH