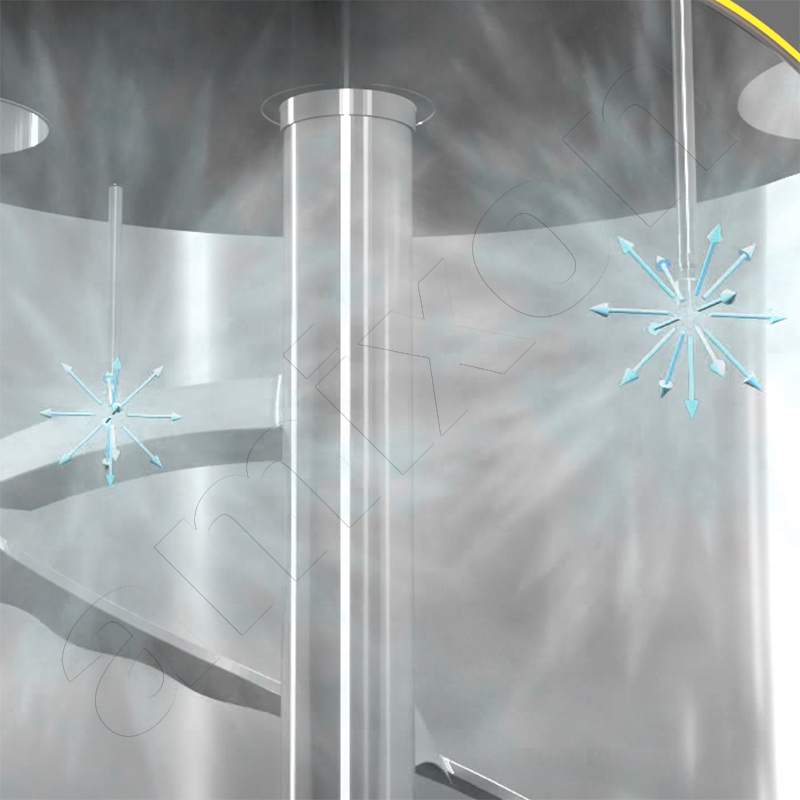
CIP cleaning-in-place
This glossary article primarily refers to powder mixers, vacuum mixer-dryers, synthesis reactors, agglomerators and fermenters.
CIP (Cleaning In Place) is a process for cleaning process equipment. The definition and objective of CIP can be described as follows: Producing clean internal surfaces of a production plant without any significant change to the fixtures required for production. Depending on the water pressure during cleaning, a distinction is made between low-pressure cleaning (up to 3 bar), medium-pressure cleaning (up to 10 bar) and high-pressure cleaning (25-65 bar). Many equipment manufacturers prefer to speak of "washing in place" (WIP).
In most cases, cleaning is done with washing water. Larger production plants cannot simply be dismantled. In this respect, cleaning takes place at the installation site. Such wet cleaning is referred to as "washing-in-place" (WIP). Cleaning can be manual, semi-automatic or fully automatic. In the latter case, one speaks of a washing-in-place system.
Cleaning-in-place (CIP) places higher demands on the cleaning process. CIP suggests that after the CIP process the system is ready for the next production start. Ultimately, however, both terms, WIP and CIP, are not clearly defined. Service delimitations and preparatory handling as well as post-processing activities must always be described precisely. this results from two constellations: 1) Hygiene requirements are defined differently in every company. 2) Almost every production plant is individually designed.
Rotary washing nozzles are widespread. They draw their rotational energy from the water flowing through the nozzle. Powder mixers are cleaned either by the low-pressure (water pressure is approx. 2 to 3.5 bar) or medium-pressure method (water pressure is up to 10 bar). The washing water nozzles must be suitably designed according to pressure and volume flow. If, for example, a low-pressure nozzle were operated with high water pressure, it would only mist the wash water. The cleaning effect would be minimal. Medium-pressure washing nozzles have a separate rotary drive (electric or pneumatic).
Often the use of detergents can be avoided if the wash water temperature is increased. Increased wash water pressure can also improve washing efficiency.
The success factors for efficient wet cleaning are:
Avoid contamination,
- choosing a particularly well-suited mixing system
- optimised operation of the mixer
- optimised method of adding liquid
- skilful multi-step operations
- minimal agitation and energy input during mixing
- minimal heat build-up from the mixing process
- short mixing time
Sophisticated hygienic design
Temperature of the wash water
Pressure of the wash water
The presence of detergent substances. Depending on the type of soiling, acidic or basic detergents can be added to the wash water. Sometimes the soiling is particularly stubborn. Then it makes sense to add foam and soak dirt adhesions.
Requirements for the design of the mixer/vacuum dryer/synthesis reactor:
- good visibility
- hygienically manufactured inspection doors - without dead space
- complete wetting of all internal surfaces by the cleaning agents
- minimal spray shadows
- no air bubbles in valves, pumps, pipelines, nozzles, seals and
- no widening of cross-sections
- no dead spaces
- Avoidance of surfaces that are difficult to wet, e.g. narrow gaps on seals, flanges, tank nozzles
- complete drainability of the system