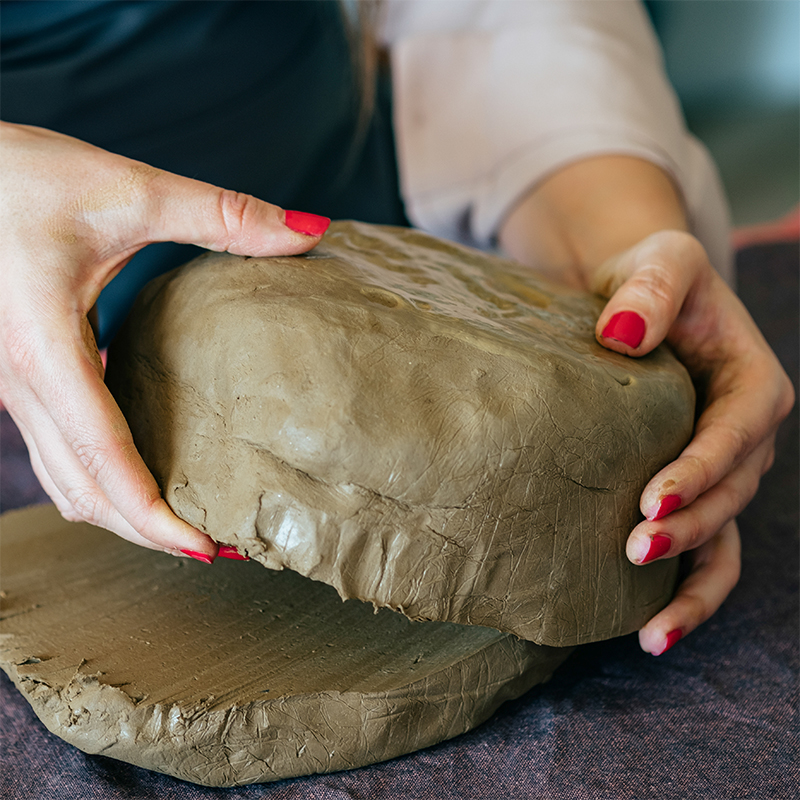
This clay mass is plastically moldable and well suited for pottery. Chemical products can also have similar consistencies. Then they are difficult to process.
Mixing, drying, tempering, discharging and dosing of high-viscosity materials
Disperse active ingredients and substances sometimes have an unfavorable consistency when they are wet. Then they are viscoplastic, pasty, highly viscous, lumpy, poor flowing and sometimes even toxic. Products that result from the synthesis of active ingredients sometimes have similar properties. After crystallization/flocculation, they are dehumidified in a chamber filter press or centrifuge. Some wet mixes have the tendency to solidify if they are not moved (time solidification).
The challenges are even more significant when dealing with large batches of many cubic meters. amixon® can offer interesting solutions for these applications!
The rheology of highly viscous substances can vary greatly. Dilatant material systems flow worse the more they are agitated/sheared; structurally viscous goods flow better the more they are sheared. Similar to thixotropic goods, they can re-solidify when the exposure to shear stress is stopped.
In technical chemistry, attempts are made to avoid the substance states described above because researchers know that it is difficult to handle them reliably. The mechanical processes such as conveying, mixing, discharging and dosing are more difficult.
In many cases, however, it is not possible to avoid the undesired material states. Then another solution is sought. Attempts are made to produce and process the masses continuously. In this process, comparatively small apparatuses with high filling levels are used, and the continuously flowing product stream is used for self-cleaning as long as the production campaign is running. The apparatuses are only flooded, rinsed or manually cleaned when the campaign stops.
However, the continuous production method cannot be used if process steps of synthesis and drying are carried out at overpressure or under vacuum.
amixon®can offer efficient solutions if the educts of the synthesis steps have the following characteristics:
- plastic,
- highly viscous,
- adhesive,
- lumpy
- time solidifying
- large masses up to 30 m³ in special cases up to 70 m³
- ……
Suspension/paste bunkers from amixon® have been in use for many years trouble-free. These devices serve as a buffer/connecting link when continuously operating machines and machines operating on a batch principle work in conjunction in a production chain. For example, a peeler centrifuge works continuously, but the downstream vacuum mixer dryer works batchwise. The air jet mill installed under the mixer dryer, in turn, works continuously.
Trials in the amixon® test centre
Materials of this type should be processed according to the methods of kneading. The change of shape and flow of such masses can only take place economically if primarily tensile forces and low shear forces are operating.
Regardless of the nature of your mixed materials, which you want to store, discharge, dose, mix, dry or chemically convert in large volumes (many cubic meters), you are welcome to reserve an appointment at our plant pilot plant. This allows experimenting with your original products.
amixon® machines are robust, particularly hygienic and meet the highest requirements in terms of process technology. Typically, we achieve excellent results. In many cases, we can even dehumidify your plastic masses cost-effectively by contact drying , optionally combined with inert gas flushing or vacuum application.
<h3>Question from a customer: What solution does amixon<sup>®</sup> propose when, for example, 20 m³ of a pasty mass needs to be stored, moved and discharged?</h3>.
<p><strong>Answer from amixon<sup>®</sup>:</strong> There are three alternatives. Two paste bins with flat bottoms or the paste bin in conical design. The latter can optionally be supplemented with a continuously operating dosing device.</p>.
<h3>1) Paste bunker with rotating spiral mixing tool. This mixing system bears the name Gyraton® and is a new development from amixon®.</h3>
<p>The mixing process takes place by conveying the material to be mixed upwards. The rotation of the mixing tool helix is superimposed by the pendulum-like movement of the mixing tool axis. As a result, the mixing tool reaches all zones of the mixing chamber and mixes the products without dead space. The mixing process is characterised by the interaction of two superimposed movements: a) the mixing tool helix rotates and b) it oscillates in a circular manner.</p>
<p>In the process, the centre of rotation shifts continuously. This phenomenon enables the operator to carry out the homogenising process at minimum speed.</p> <p>The Gyraton is a mixing unit with a rotating helix.
<p>The Gyraton® mixer can serve well wherever the following challenges exist:</p>
<ul> <li>excellent good homogeneity should be achieved,</li> <li>the mixing batches are large,</li> <li>the mixing materials have strong changing flow properties,</li> <li>the mixing process should be energy-saving with minimally small motors</li> </ul>.
2) Flat-bottom paste bunker
Here, a shovel-like "crawler arm" rotates over the floor of the amixon® paste bunker. If the discharge should take place more steadily, then a second, third or fourth arm is installed. The special feature of this flat-bottom paste bunker: it has a low overall height. The mixing tool is only mounted and driven at the top. The machine has no dead space and is particularly hygienic (EHEDG and FDA compliant). A flat bottom bunker can supply several production lines. Then there are at least two closure fittings on the floor, optionally more.
Especially sticky pastes would stick to the wall. The amixon® paste bunker can also discharge such goods safely, as the rotating helix slowly slides along the cylinder like a scraper. Such a system has almost no mixing function. The drive power and the energy input are correspondingly low.
3) The conical paste bunker can discharge continuously and even in a dosing manner
Here the mixing/discharge tool rotates either to the right or to the left. One direction of rotation ensures loosening and, optionally, mixing. The other direction of rotation is used to press the plastic goods downwards - similar to an extruder. Sometimes the plastic masses have to be transferred to a continuously working process. Then it is required that the amixon® bunker discharges the goods in a gravimetrically controlled manner. A constant mass flow should flow out over time.
This can be done reliably if the discharge bunker rests on load cells. The weighing signal controls the rotational frequency of the discharge tools. Depending on the nature of the pastes, this amixon® discharge bunker can even convey against differing ambient pressures.
Please schedule an appointment for a trial at the amixon® technical center. This allows experimenting with your original products. amixon® machines are robust, particularly hygienic and meet the highest requirements in terms of process technology. Typically, we achieve excellent results and we can even vacuum dry your plastic masses at a reasonable price.
More than 30 different testing machines are available to you in the amixon GmbH technical centre. It is highly likely that we can also provide an excellent solution to your task.
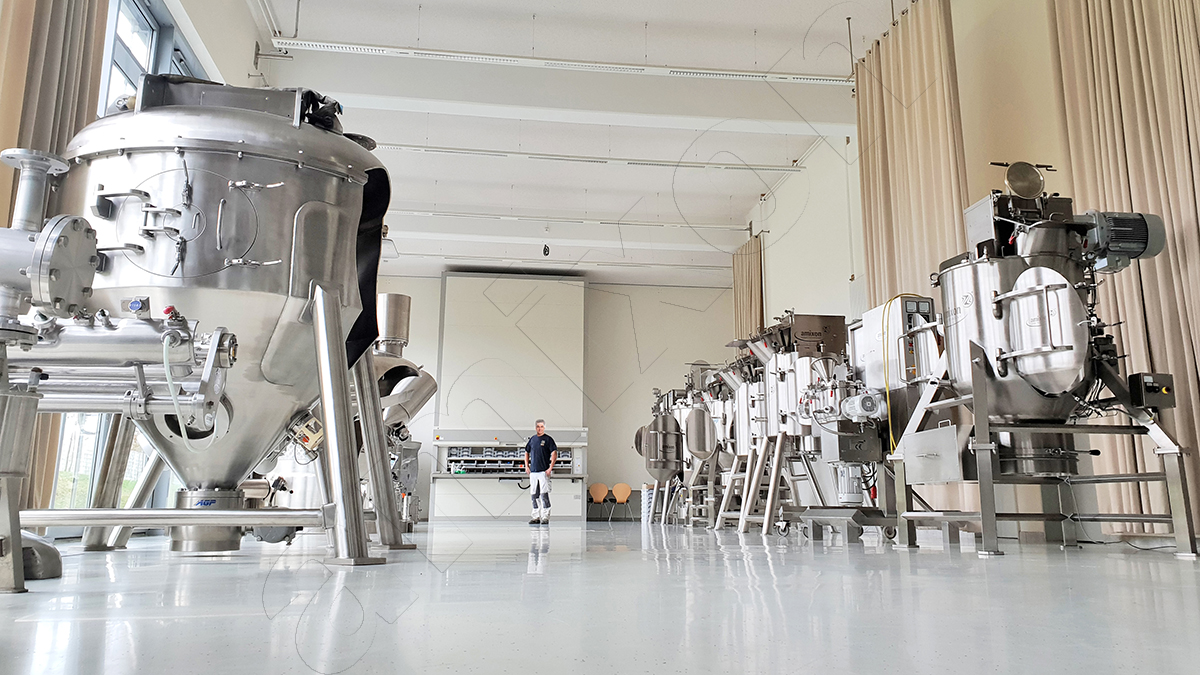
© Copyright by amixon GmbH