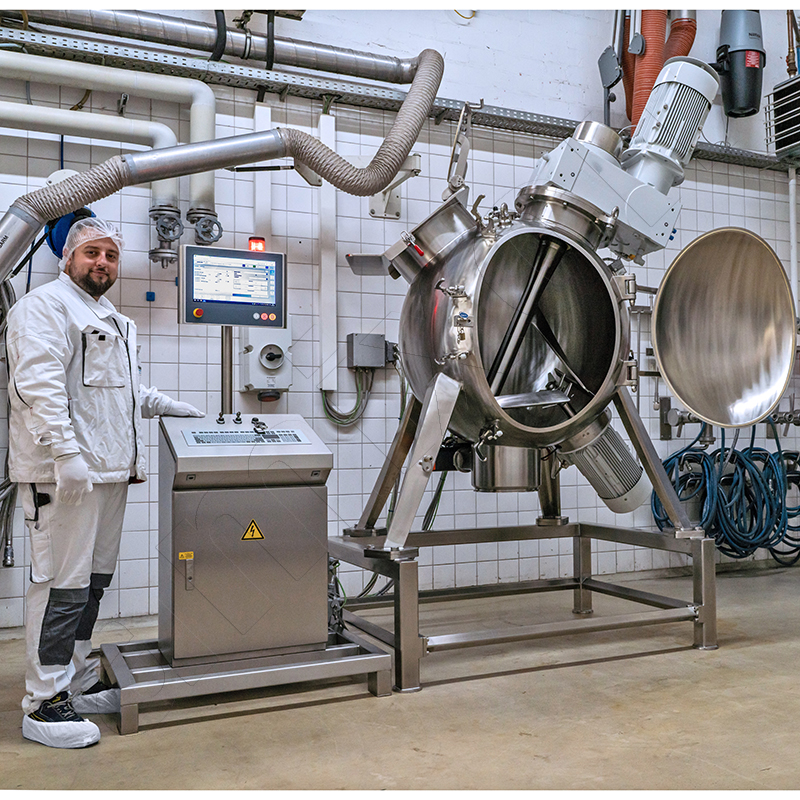
Hollow-ball mixer for 400-litre batches in the amixon® technical centre. It mixes all types of dry, moist and wet bulk materials/powders.
Hollow sphere mixer for bulk materials: SpherHelics®
amixon® process equipment is well known for its vertical spiral mixing tools. The amixon GmbH manufacturing programme is very diversified. amixon® can offer a specific solution for almost every mixing task. The name amixon® is, to a certain extent, a synonym for vertical precision mixers.
It is less well known that amixon® cylindrical mixers also carry out the mixing process in inclined positions. This is rare, but there are isolated process engineering reasons that speak in favour of an inclined position of the rotational axis of the mixing tool shaft by 20°, 25° or 30°. This may be the case, for example, if the mixing tool helix is to turn particularly slowly, if a cutting rotor is to work with low filling levels or if a static mixing tool is to be dispensed with.
The mixing chamber does not have to be cylindrical or conical. Other rotationally symmetrical shapes are also possible. For example, a spiral mixing tool can rotate around a vertical or inclined axis in the hollow sphere.
The sphere requires the smallest specific surface area for its volume. Taking into account that the gross volume of a hollow sphere mixer has to be dimensioned larger than the gross volume of a cylindrical mixer, the surface reduction compared to a cylindrical mixing chamber is approx. 13 %. In practice, this plays no role in terms of ease of cleaning. It is assumed that all surfaces are ground smooth and joint-free.
Quality criteria that pay off in everyday use
In view of the long service life of a powder mixer, the choice of mixer should be made carefully. amixon® offers ideal conditions. In addition to the amixon hollow ball mixers, all other amixon test mixers can also be compared 1:1. All test mixers have a useful volume of 400 litres.
The mixing tests provide information about the essential quality criteria:
- complete emptying
- flexibility at different filling levels
- cleanability
- ergonomic aspects
- short set-up times
- resource-saving operation
- favourable acquisition costs
Mixing quality and mixing efficiency
If the mixing tool is designed like a helix and its rotation creates an envelope volume that is slightly smaller than the inner diameter of the hollow sphere, then the volume flow displaced by the spiral mixer in the spherical mixing chamber can be calculated fairly accurately.
IV = π / 4 · (D² - d²) · Φ · S · n · ζ
IV: Displacement volume flow
D/d: Helix diameter outside/inside
Φ: Filling degree
S: Helix pitch
n: Rotational frequency
ζ : Speed coefficient
As a rule, the entire contents of the mixing chamber are thoroughly mixed once after approximately five revolutions for all amixon® mixers.
It is interesting to note that this formula also applies when the mixing tool rotates very slowly.
As a rule, amixon® mixers achieve ideal mixing qualities after 25 to 40 revolutions. This also applies, for example, to component compositions of 1 to 100,000.
Ideal mixing quality means that the mixing quality achieved cannot be improved in practice. This applies regardless of the precision mixer used for mixing. The analytically determined mixing quality variance of a 20-gram sample is then less than 5%.
This means that all amixon® mixers can mix even particularly fragile goods ideally, gently and accurately.
amixon® provides comprehensive and objective advice
amixon® is a global leader in the field of vertical mixers. This is based on more than 40 years of experience with thousands of amixon® mixers worldwide. amixon® provides comprehensive and objective advice on all aspects of vertical precision mixers. This also includes mixers with spherical mixing chambers.
Our customers are cordially invited to conduct trials. In addition to hollow sphere mixers, many other mixers are available in the same size.
Typical quality criteria are
- complete emptying
- flexibility at different filling levels
- cleanability
- ergonomic aspects
- short set-up times
- resource-saving operation
- favourable acquisition costs
- ......
amixon® machines are free of ‘teething troubles’! This also applies to our SpherHelics® mixer. The name stands for the spherical mixing chamber and the amixon®-typical mixing helix.
The amixon® product range includes the following mixers:
- KS: KoneSlid® mixers have an internal counter-rotating cone that serves as a discharge device.
- VM: vertical single-shaft mixers have cylindrical mixing chambers.
- SH: hollow-ball mixers have vertical or inclined mixing shafts.
- HM: twin-shaft mixers have two cylinders that engage with each other.
- AM: conical mixers have cylindrical-conical mixing chambers.
The proof of the pudding is in the eating
Tests should be carried out before making a purchase decision. Trials in the amixon® technical centre are always informative. You can test several test mixers in parallel. This allows you to assess mixing efficiency, variety of applications, residual emptying and cleanability. In view of the long service life of powder mixers (20-30 years), this effort makes sense.
Typical questions could be:
How often does the mixer need to be completely discharged (cleaning or product change)?
Will this be necessary more frequently in the future?
Can the mixer blender discharge itself completely?
Can the remaining product be sold?
or do the residues have to be disposed of?
How long does the discharging process take?
How large are the residues?
How long does dry cleaning take?
How long does wet cleaning take?
How well can it be automated?
........
Can customers test all mixers?
Answer from Mr Böning: Yes, of course. All mixer types, including our new SpherHelics®, are available. The batch size is a uniform 400 litres. This allows our customers to gain all the important insights. At the same time, these insights serve amixon® as valuable impetus for future developments.
Incidentally, it was not a great deal of work for amixon® to develop the new hollow-sphere mixer for all 12 sizes. As a contract manufacturer, we design each mixing plant individually anyway. We use our proven variant configurator for this. In addition, we have extensive expertise in the mixing mechanics of vertical mixers with mixing spirals – regardless of whether these are mounted vertically or at an angle.
In the manufacture of our hollow-ball mixers, amixon® relies exclusively on proven and reliable components. These include, in particular,
- the bearings of the mixing mechanism
- the mixing tool
- the drive
- the design and function of the dead-space-free shut-off valve,
- the Clever-Cut® inspection door with OmgaSeal® seal,
- the cutting rotors,
- the liquid supply and the sanitary flanges.
What is the product portfolio?
All common sizes of the SpherHelics® series are available. The useful volumes of the mixers are available in the following increments (in litres): 400, 600, 800, 1000, 1250, 1500, 2000, 2500, 3000, 4000 and 5000. Larger hollow-ball mixers are feasible in principle, but be delivered disassembled for transport reasons. For this reason, our table of dimensions currently ends at a usable volume of 5 m³.
Please refer to our data sheet ‘SpherHelics® Hollow-Ball Mixer Type SH’ for dimensions and technical information.
Each individual hollow-ball mixer is customised to the specific customer requirements. This also applies to the respective strength requirements and drive concepts. The flow properties of the materials to be mixed and their bulk density play an important role here. They can be very light (fumed silica has 0.01 kg/dm³). They can be very heavy; up to 6 kg/dm³ (powder metals).
Data sheet for SpherHelics®
SpherHelics® Hollow spherical mixer Type SH The type designation corresponds to the maximum batch size in litres. Highest mixing qualities can be achieved even at low filling levels. | Approximate gross volume of the mixer | Approximate diameter of the hollow sphere | Approximate dimensions of various amixon® hollow sphere mixers. For exact planning, please request detailed dimension sheets! We will be happy to provide you with CAD data on request. | The required drive power can vary greatly depending on bulk density, flow characteristics, rotation frequency, processing task such as deagglomeration. | |||||
A | B | C | D | E | from | up to | |||
Net capacity [litres] | Litres | mm | mm | kW | |||||
400 | 571 | 1030 | 910 | 1130 | 1750 | 410 | 180 | 3 | 6 |
600 | 857 | 1180 | 950 | 1230 | 1830 | 410 | 180 | 5 | 11 |
800 | 1143 | 1300 | 1090 | 1330 | 2030 | 410 | 180 | 7 | 15 |
1000 | 1429 | 1400 | 1130 | 1430 | 2140 | 520 | 180 | 9 | 21 |
1250 | 1786 | 1500 | 1150 | 1530 | 2210 | 520 | 180 | 12 | 25 |
1500 | 2143 | 1600 | 1170 | 1630 | 2290 | 520 | 270 | 14 | 30 |
2000 | 2857 | 1760 | 1180 | 1780 | 2400 | 605 | 270 | 19 | 39 |
2500 | 3571 | 1900 | 1210 | 1930 | 2610 | 605 | 270 | 23 | 50 |
3000 | 4286 | 2020 | 1200 | 2030 | 2680 | 680 | 270 | 28 | 60 |
4000 | 5714 | 2220 | 1200 | 2230 | 2820 | 680 | 270 | 37 | 80 |
5000 | 7143 | 2400 | 1265 | 2430 | 3026 | 680 | 270 | 45 | 100 |
- Larger mixers available on request.
- The circumferential speed can vary greatly from about 0.8 m/s to about 3.5 m/s. As a rule, hollow-sphere mixers of the SpherHelics® type are operated as slowly rotating mixers.
- As a specialist welding company, amixon® has European, Japanese, Korean and American approvals for processing a wide range of materials. The materials of the amixon® mixers that come into contact with the product are optional: normal steel S355J2Ge, Hardox, austenitic stainless steels 1.4301, 1.4541, 1.4571, 1.4404, 1.4539, 1.4529, duplex stainless steels 1.44 62, 1.4162, 1.4363 as well as nickel-based materials Alloy 59-2.4605, Hastelloy-C22 and nickel.
- The agitators meet the highest hygiene requirements and comply with the EHEDG guidelines for dry and wet cleaning. In addition,
- they meet the FDA hygiene guidelines and the design requirements of the 3-A Sanitary Standards.
What will be relevant in the future when customers want to buy the optimum powder mixer for their mixing plant?
Answer from M. Böning: Proximity to the market and the ability to quickly implement change processes are decisive factors for economic success:
- The role in the value-added process: It is important to understand what role the mixer plays in the company's overall production process. If the mixer is a central component of the value chain, it must be given special attention. amixon® advises you worldwide with specific industry knowledge.
- The market of customers and their business models: Customers want products with clear unique selling points such as dust-free, improved flow behaviour, specific colouring, instant capability, exact granulometry and defined bulk density. A properly designed amixon® mixer is able to meet the most demanding requirements. It delivers the desired product quality.
- Flexibility and adaptability: Flexibility is an important criterion. Market requirements are becoming more and more individual. An amixon® mixer can be used universally. It is possible to react effectively to product changes without the need for additional personnel or large investments.
- In-house innovation: A modern amixon® mixer is not only efficient, but also promotes innovation. With a well-equipped amixon® mixer, creative product developments can be driven forward. This increases employee motivation. This is how new market segments can be opened up.
- Automation and digitalisation: There is no way around digitalisation. amixon® experts will be happy to advise you. Intelligent sensors, data-based process optimisation and connection to higher-level process control systems (Industry 4.0) lead to greater efficiency.
- Sustainability and energy efficiency: environmentally friendly production is a high priority. Modern amixon® mixers conserve resources and have a small ecological footprint.
- Service and support: After-sales support is important. This includes not only spare parts service, regular maintenance and practical training. amixon® also offers a wide range of process engineering support over the entire service life of the mixer.
For us as a mixer manufacturer, there is hardly anything better than hearing our customers' success stories. They encourage us in our claim to continue to be a trendsetter in the future.
Are there any other new developments besides the hollow sphere mixer?
Answer from M. Böning: Yes, there are indeed. We have developed and successfully launched the Gyraton® mixing system. This mixer offers ideal solutions when the following requirements have to be met:
- Batch size: suitable for batches from 10 m³ up to sizes between 70 and 100 m³.
- Mixing material: suitable for free-flowing, dry materials as well as for moist, lumpy and poorly flowing goods. But also for goods that solidify when they are not moved.
- Particle sizes: the Gyraton® mixes fine, dusty or nano-disperse particles as well as coarse-grained materials up to 20 mm.
- Variable filling level: The Gyraton® mixer enables flexible batch sizes from just 10% to 100% filling level.
- Hygienic design: Gyraton® was specially developed for the highest hygiene standards: active pharmaceutical ingredients and nutrients.
- Mixing time: offers flexibility from short mixing times to several hours at low drive power.
The Gyraton® mixer delivers excellent mixing quality even at extreme mixing ratios of up to 1:100,000. This makes it the ideal choice for demanding applications where high precision, flexibility and efficiency are required.
The power required to homogenise 1.5 t (3 m³) of bulk material is only 3.3 kW
1,500 kg (approx. 3 m³) of corn flour and 15 g of nanodispersed blue powder (patent blue) are mixed in the Gyraton GM 3000 mixer at an extremely low speed:
- Mixing spiral: 3 revolutions per minute
- Peripheral speed: 0.27 m/s
- Drive power: 3.3 kW
The abscissa shows the time course.
With this sophisticated product range, amixon GmbH underlines its process and quality leadership in vertical precision mixers / blenders
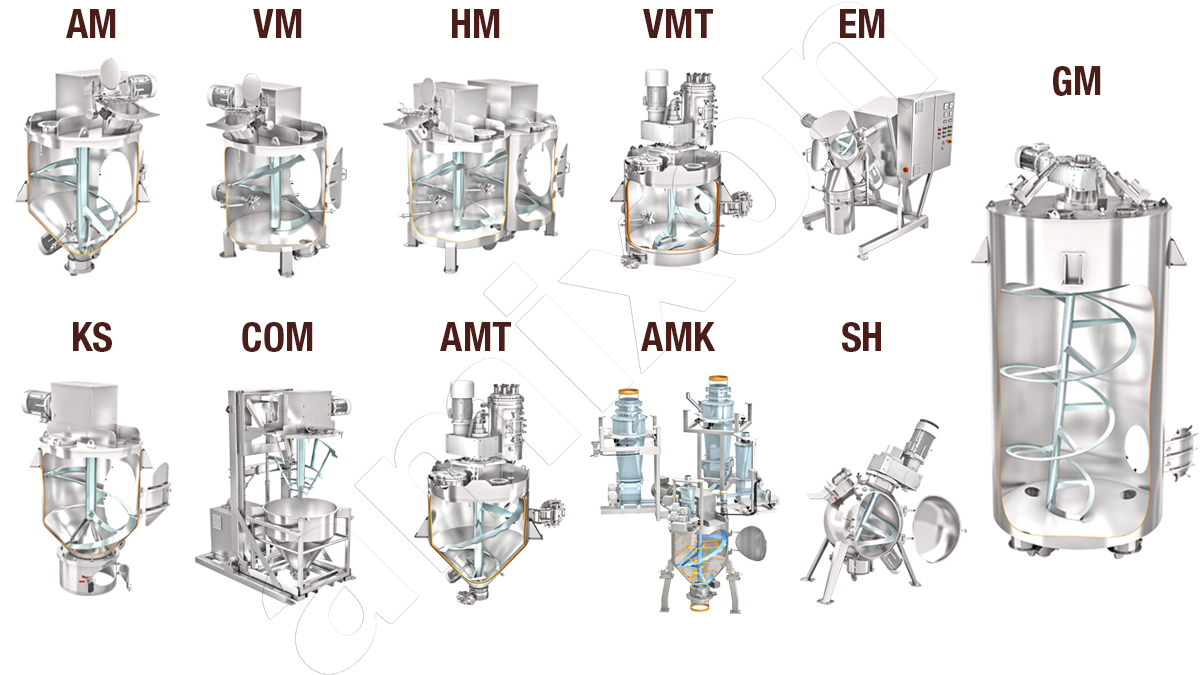
Hollow sphere mixers have interesting properties
amixon® already offers the most comprehensive range of vertical precision mixers, underscoring its 40-year market presence. With over 40 patent applications worldwide, we are positioning ourselves as an innovation leader and quality benchmark for powder mixers with vertically mounted mixing tools.
We started developing our hollow-ball mixer as early as 2021/22. It was extensively tested and then presented to the public in time for the company's 40th anniversary in 2024.
amixon® aspires to always be at the cutting edge and to be able to provide a competent answer to every question. We can only achieve this if our experiments are based on sound practical experience. Our goal is to impress our customers with our expertise and innovative solutions at all times.
© Copyright by amixon GmbH