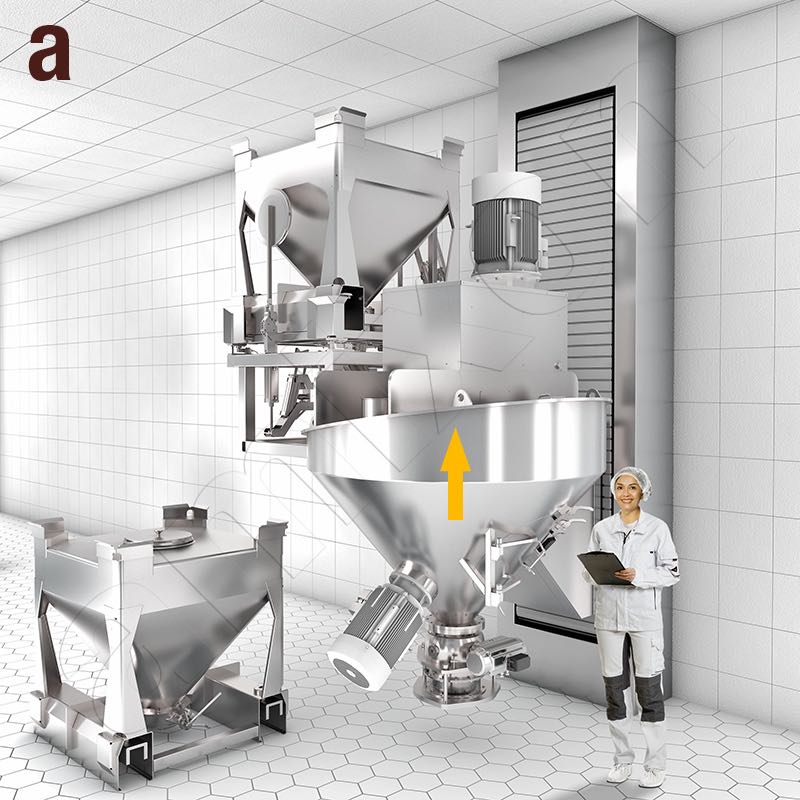
Representation of the time-efficient option for filling the amixon® cone mixer.
Excursus container mixer: amixon® conical mixer size AM 1500, filled and discharged by means of Intermediate Bulk Containers (IBC)
What are typical advantages of a container-based mixing facility?
A powder blending plant, which works with Intermediate Bulk Containers, can decouple its production steps 1 to 7 in terms of time and space:
- Composition and weighing of the raw materials in the IBC(charging).
- Mixing
- Discharging
- Filling of the container contents
- Cleaning of the mixer
- Cleaning of the container
- Cleaning of the filling machine
Depending on the order structure, the above-mentioned production steps tie up different amounts of time and personnel resources. In the mixing system shown above, charging can take place while the mixer is still being cleaned. Filling of the container contents can take place while the mixer is already processing a new mixing order. Waiting times are thus minimized and production output can be increased.
In addition to the mixing system shown here, which is filled and discharged with bulk containers, amixon® also offers classic container mixers. A critical comparison of both concepts will be discussed in another blog article.
What might a plant design look like if the available room height is too low to fill and empty an amixon® mixer by container? Alternatively, if the room height is too low to fill and empty an amixon® mixer by big bag?
If the filling and discharging of the mixer takes place with the help of standard bulk containers or by means of big bags, there are usually three levels: The filling level (top), the mixer level (middle) and the discharging level (bottom). The overall plant height results from the height of the container, which is at the bottom, plus the height of the mixing chamber, plus the height of the container, which is at the top of the mixer's feeding nozzle.
If the room height is not sufficient, amixon® can offer the solution shown here: The mixer is connected close to the wall with a lifting-lowering system. The mixer moves down for the purpose of filling. The container is placed on the mixer feeding nozzle. The container content flows into the mixing chamber. The filling valve closes, and the mixing process starts. The bulk container is removed from the mixer. Then the mixer moves upwards. An empty container is positioned under the mixer. The discharge valve opens, and the container is filled. Free-flowing mixing goods flow out of the mixer almost completely (complete discharge).
Optionally, mixers and containers are weighed. Instead of the bulk container, it is also possible to discharge into big bags, sacks or into a filling machine. This could be placed on rails under the mixer. The feeding and discharge nozzles are optionally equipped with docking devices or with big bag connection sets.
One or two large inspection doors on the mixing chamber allow convenient cleaning. The entire plant can be cleaned either wet or dry. This usually takes only a few minutes. In terms of working ergonomics, service life, hygiene (cleaning ergonomics) and flexibility, this mixing plant meets the highest demands.
There should be no shortage of bulk containers in everyday operation. Standard bulk containers are inexpensive compared to bulk containers of a container mixer, so they can also be procured in larger numbers.
© Copyright by amixon GmbH