Container mixer for bulk materials
If your company mixes bulk materials and your production logistics are based on intermediate bulk containers (IBCs), it makes sense to align your mixing technology with this. In this blog post, the focus is on container blenders as precision blenders.
Precision mixers are able to homogenise powdery component compositions with a mass ratio of 1 to 100,000 with technically ideal precision. This may also include liquid or moist substances. Or components with different bulk densities and particle sizes. In this context, precision mixing is only possible if the container mixer has a dynamically moving, space-controlling mixing tool.
Picture left: amixon® container mixer type COM. Here the bulk container serves as a mixing container. The mixing tool is introduced from above into the material to be mixed and the container is closed with the lid. The mixing tool carries out the mixing work in the sealed, gas-tight container. The drive then switches to reverse operation. The mixing tool slowly ‘unscrews’ itself from the mixture. The mixture in the container is now optimally mixed. The container is removed.
Container blending system with standard IBCs
This amixon® container mixing system works differently than described above. These are standard bulk material containers with relatively small filling and discharge spouts.
The bulk material containers used can be round or square and also have different sizes. The containers can feed the entire batch of mixed material into the mixer. However, several containers can also be involved in filling the mixer.
The amixon® mixer moves downwards. The bulk goods container is placed on top and docked dust-tight. The closing flap of the container opens. An optional vibrator supports the emptying of the container. The docking station is optionally equipped with a scale. After filling, the mixer moves upwards during the mixing process. The previously used container can be used to pick up the finished product.
This amixon® container mixing system is wet-cleaned several times a day. Drying takes place just as quickly. The API active ingredients are mixed into carrier compounds.
Explanations on the subject of free-fall mixers
Free-fall mixing takes place when a powder mixture is repeatedly transferred from one container to another. The flow movement of the powders can also take place within the same container. Industrial "free-fall mixing" takes place automatically when a suitable container is filled with powder and rotated around a horizontal axis. High mixing qualities can be achieved with free-fall mixers. However, many requirements must be met:
- the smallest component should not make up less than 5% of the total mass
- All components must be dry
- All components must flow freely
- All components must have similar flow properties
- all components must have similar grain sizes
- all components must have a similar bulk density
- It must be ensured that all particles are separated (deagglomerated)
- It must be ensured that no lumps form/ or agglomerates roll up during free-fall mixing
- Free-fall mixers can only mix well if the filling level is precisely adjusted
If the aforementioned factors are fulfilled, a free-fall mixer can be tested and validated if the results are favourable.
- Free-fall mixers have the advantage that they usually mix very gently
- fragile particles are retained during mixing
- Free-fall mixers are often used as batch mixers. Often as "free-fall drum mixers" or "free-fall container mixers"
- There are also industrial applications in which free-fall mixers are used as continuous tube mixing systems. They are used in high-temperature processes, for example. The bulk materials are heated directly with a gas flame during mixing, e.g. during calcination or chemical reduction.
If the above conditions are not met, the opposite of mixing may occur. Previously mixed components can separate and segregate.
Wear minimisation plays an important role in the processing of abrasive mixes. Free-fall mixers operate at comparatively low peripheral speeds and therefore have specific advantages over compulsory mixers. This applies, for example, to the processing of heavy metal cast iron, blast furnace slag, metal powder, sintered metals, ceramic bodies, in the non-metallic minerals industry, ....
Free-fall mixers are not part of the amixon® production programme.
The amixon® container mixer type COM is well suited for dust-free mixes
In both cases, the mixing processes are the same and take place in conical containers. Nevertheless, the two amixon® container mixing systems differ. The COM container mixer is recommended if the material to be processed is not dusty or odourless.
Question from a customer: To what extent is a classic COM container mixer less suitable for dusty mixes?
Answer from amixon®: With the COM type, the bulk material container also serves as a mixing chamber. The spiral-shaped mixing tool must enter the container from above. This is only possible if the entire cross-section is open. A large lid is therefore required.
With dusty mixes, a certain amount of dust emission is unavoidable when the mixing tool is immersed in the mix and retracted again after the mixing process. Due to the large open area of this type of container, it is difficult to completely extract the dust.
An amixon® container mixer type COM should only be considered if both the raw materials and the finished mixtures are safe. By this we mean powders or granulates with the following properties:
- dust-free
- Non-toxic
- not corrosive
- not jeopardising
- neutral odour
There are many different types of bulk containers
A standard container can be round or square in shape. It is characterised by the fact that it has a filler neck at the top and an outlet neck at the bottom. Both spouts usually have the same dimensions. The lower nozzle contains a shut-off valve. This can be designed as a slide valve or a rotary valve. The upper connection piece can optionally also be fitted with a shut-off valve. For reasons of easy cleaning, only one cover is usually fitted. Depending on the type of bulk material and the container size, the nozzle dimensions vary from DN 200 to DN 350.
The situation is different if the container is part of an amixon® container mixer type COM. In this case, the lower closure fitting must have a rotationally symmetrical or flat shape. To achieve a high mixing quality, the mixing tool must cover the entire surface of the container. This also applies to the shut-off valve.
Docking stations are required to match the containers. With their help, it is possible to fill and empty bulk containers dust-free or with low dust levels. On the left, a mounting device for the 4 container feet. In the centre is a pressure sleeve for the spout.
- Docking stations can optionally also function as scales.
- They can also be equipped with a vibrator. This can improve the emptying behaviour of the container.
Further developed containment docking stations can even work completely dust-free and fulfil clean room conditions.
Bulk goods containers for dusty, hazardous bulk goods
If your goods are dusty or hazardous, we recommend the use of closed standard bulk containers. Such standard containers (IBC = Intermediate Bulk Container) are produced in large quantities. They are lighter and considerably more cost-effective than bulk containers, which serve as a mixing chamber for dynamic mixing tools.
Cylindrical bulk containers generally have better emptying behaviour than containers with a square cross-section. On the other hand, square containers offer better space utilisation.
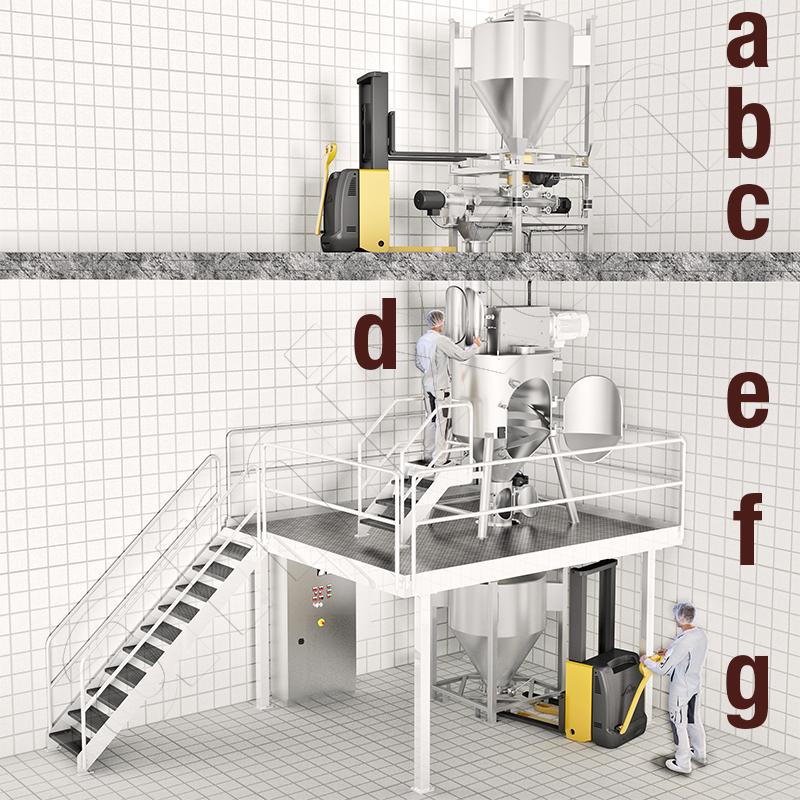
"Stand-alone mixing unit" for newly established departments or operations: A standard container (a) is docked to an eddy current screening machine (c) with a hand lift truck (b). The connecting tube to the amixon® conical mixer has an inspection door (d). Further inspection doors are located at the mixing chamber (e) and at the outlet spigot (f). The same bulk container can receive the mix from the mixer.
What needs to be considered if the intention is to set up a mixed container operation
Industrial powder mixing companies generally have a larger selection of raw materials from which a wide variety of mixtures have to be produced. In this respect, the raw materials can be divided into
a) complicated; difficult, b) moderately difficult or c) simple.
A similar classification should be made for the end products. Then classify the size and added value of the mixed orders. A further consideration concerns the future strategic orientation and market development.
The above considerations result in representative recipes. These will be used to carry out mixing tests with manufacturers who offer container mixers.
The next step is to evaluate the design and size of the large container (IBC): The individual components and also the mixed products must flow out safely, completely and without segregation. The following considerations are linked to this:
- Container shape round or square, stackable?
- Net volume versus gross volume: What gross volume must the container have, taking into account the angle of repose of the mixed material?
- Is the cone inclination steep enough to ensure that the powder discharge is segregation-free?
- Type of closure fitting?
- Discharge fitting to be operated automatically if necessary?
- Diameter sufficient for safe powder discharge?
- Is the closure fitting permanently dust-tight even when the container is being transported?
- Is the closure fitting suitable for dosing powder discharge?
- The container may be coupled with a vibration device for the purpose of powder discharge
- Filling spout of the bulk goods container closed by fitting or lid
- Sometimes bulk containers have a filter connection for aeration and deaeration => nature of the filter?
- Stability; impact protection?
- Surface quality?
- Wet or dry cleanable?
- Suitable for a "wash-in-place" (wip) cleaning station?
- .... more details?
Trials in the amixon technical centre are always a gain in know-how
In order to assess the above questions, practical emptying tests with various standard bulk containers cannot be dispensed with. This is the only way to find out whether and how your powders flow out of the container.
The amixon® team will be happy to advise you and carry out the tests for you. Each test section is documented with a results protocol.
© Copyright by amixon GmbH