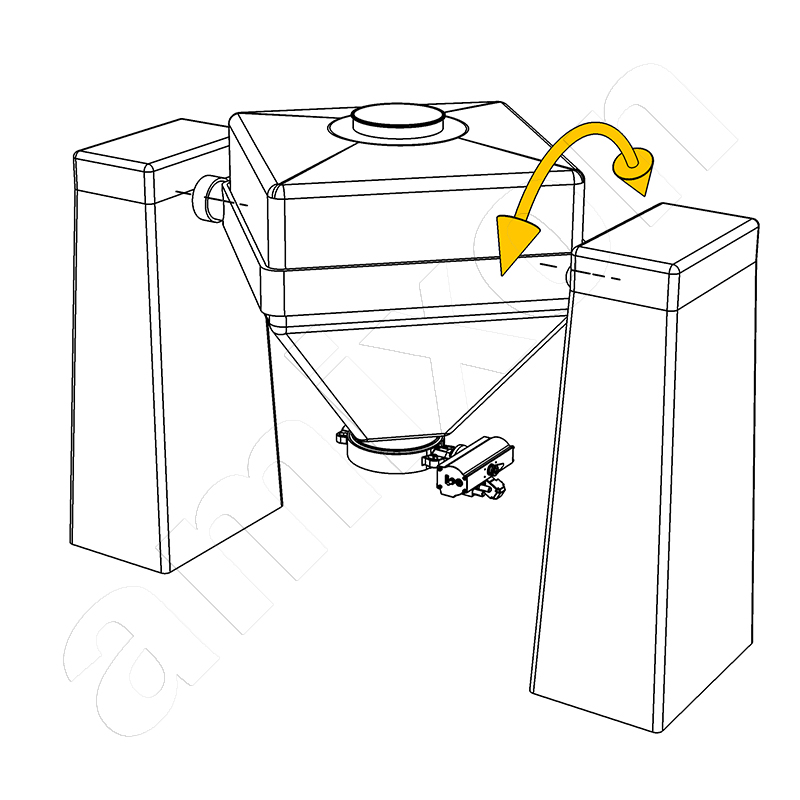
Free-fall mixer
Unlike so-called compulsory mixers, free-fall mixers do not have dynamically moving mixing tools that rotate within a mixing chamber. Instead, the completely closed mixing container is rotated around a horizontal axis. The speed is so low that centrifugal forces do not play a role. The mixture flows or falls repeatedly under the force of gravity, hence the name ‘free-fall mixing’.
There are different types of free-fall mixers. The mixing containers are often designed as IBCs, double cones, rotating cylinders or rotationally symmetrical bodies. Some designs resemble two connected trouser legs, known as V-mixers. In some variants, the cylinder is not rotated but shaken or guided in complex movement patterns. In many cases, baffles and guide plates are installed inside to change the material flow and improve mixing.
Free-fall mixers are considered particularly low-maintenance, robust and durable. Due to their simple mechanics, they are energy-efficient and inexpensive to purchase and operate. However, their use is limited to narrowly defined areas of application.
The material to be mixed must be free-flowing, dry and free of lumps. The components to be mixed should be very similar in terms of grain size, bulk density and flow behaviour. The mixing process is relatively gentle and does not result in any significant agglomeration. It is not possible to add liquids. There are also restrictions on dosing: Free-fall mixers are not suitable for recipes with extreme mixing ratios such as 1:1,000 or 1:10,000.
amixon® does not manufacture free-fall mixers. All mixers manufactured by amixon® are precision mixers. They work with vertically mounted helix mixing tools. These generate a three-dimensional flow of the mixture and ensure a homogeneous mix with no dead space. Even with very different grain sizes and component compositions of up to 1:100,000, reproducible ideal mixing qualities are achieved.