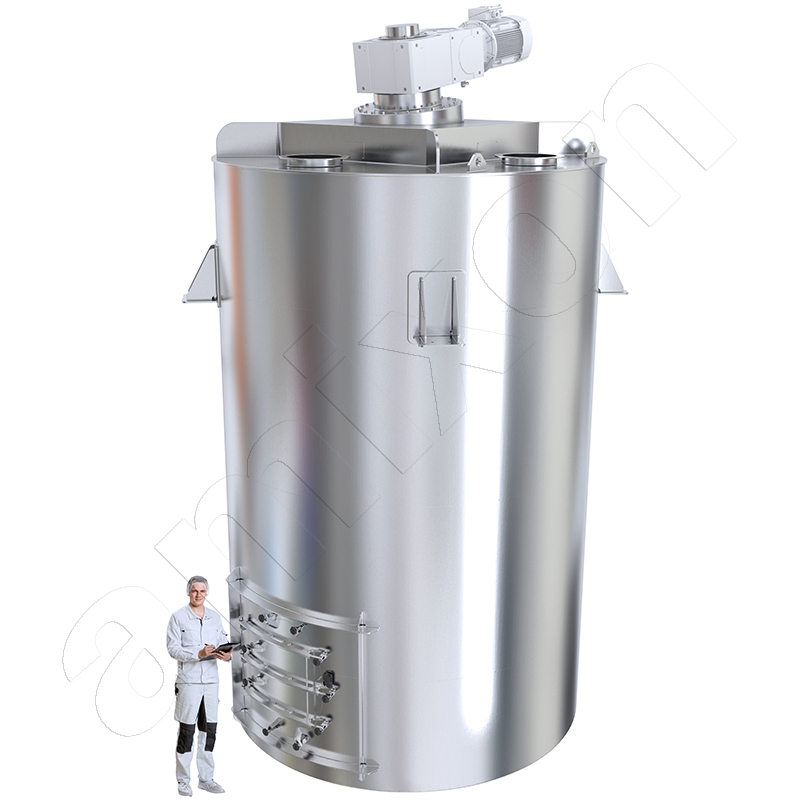
Flat-bottom silos
A flat-bottom silo is a bulk material silo which, unlike a classic hopper silo, does not have a conical bottom but a largely flat or only slightly curved bottom. This design is particularly suitable for the storage and metered discharge of poorly flowing bulk materials or pastes.
A flat-bottom bunker is mainly used
- when the flow behaviour of the bulk materials is poor
- or when several connections are to be fed with solids at the same time
- or when there are structural height restrictions.
Since bulk materials do not flow like water, an active discharge device is required. Depending on the application, this can be a mixing arm or a spiral agitator that slowly moves the bulk material towards the discharge devices. In order to make product discharge more uniform and continuous, it may be advisable in some cases to mount several arms on the shaft instead of a single clearing arm. This makes the discharge more even.
An important design feature is the type and position of the clearing arm drive.
For products that are not very abrasive and not critical in terms of hygiene, the drive can be located at the bottom. In this case, the shaft seal is exposed to the static pressure of the material and is therefore susceptible to wear. For critical bulk materials, e.g. hygroscopic, sticky or heat-sensitive products, drive from above is recommended. The shaft seal is then only exposed to dust, which ensures a significantly longer service life and operational reliability of the seal. This design is recommended, for example, if the bulk material is sugar. Sugar can caramelise due to friction.
Flat-bottomed bunkers are sometimes also designed with negative conical bottoms. The silo diameter increases towards the bottom. This geometry loosens the bulk material that slides down and improves mass flow. In a Gyraton flat-bottomed bunker, the bottom is slightly curved. The lowest point is exactly in the middle. This is helpful for wet cleaning.
amixon® manufactures two different types of flat-bottom bunkers: Type VB has a centrally mounted, rotating clearing arm. Type GM (Gyraton®) has a slightly curved bottom and a special clearing tool that moves over the bottom in a rotating and oscillating motion. This design ensures dead space-free discharge even with demanding products. Further information can be found in the glossary under ‘Wet hoppers’.
Flat-bottom hoppers can be optionally equipped with CIP cleaning systems, modular discharge devices (e.g. dosing screws, rotary valves, flaps), sensors for process monitoring and ATEX-compliant design. Flat-bottom hoppers can also be designed with double walls if the product needs to be temperature-controlled.