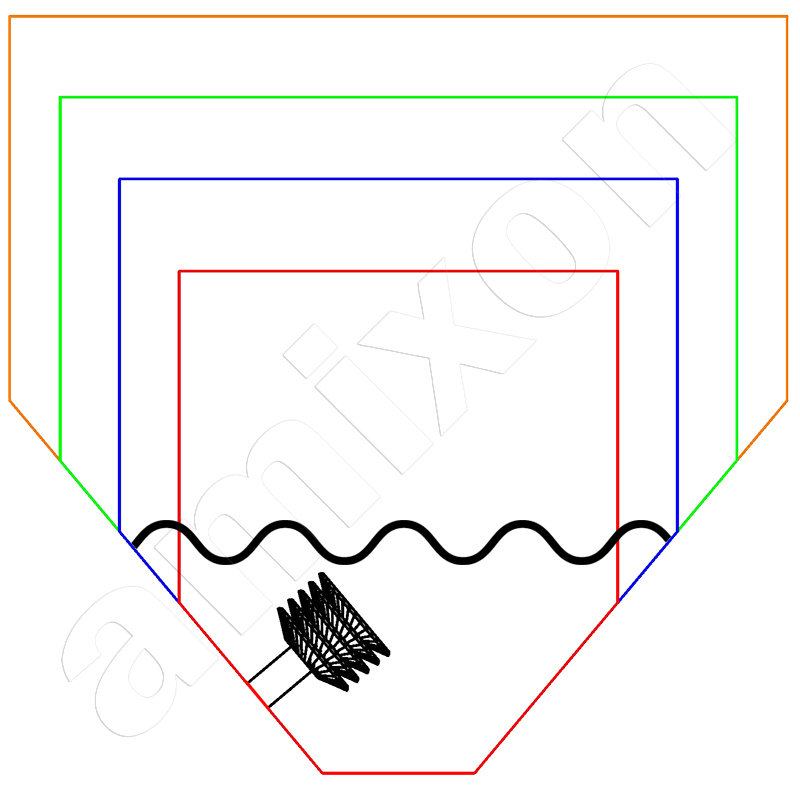
Filling degree
The filling degree describes the ratio of the filled product volume to the available process space of a process engineering machine. This applies in particular to powder mixers.
When processing powdered solids, a mixer must never be completely filled. The mixing tool would become blocked and possibly damaged. Powder mixers require free space to mix the bulk material. This free space is also referred to as gas space. It is necessary to reduce the particle density and loosen the powder. The loosening is achieved by lifting the powder against gravity. The particles are then less densely packed together. The internal friction of the powder is reduced and the mobility of the particles is improved. Powders can only be mixed homogeneously when they are loosened.
No gas space is required when mixing low-viscosity liquids. Here, the filling level can be up to 100 percent. In such cases, it is even desirable that no air is introduced into the liquid.
In contrast, solid mixers have a minimum and maximum filling level depending on their design. Within this ‘usable volume range’, the mixer works efficiently and produces optimum mixing qualities. Ideally, the filling level refers to the gross volume of the mixing chamber minus the volume of the mixing tool.
amixon cone mixers have particularly large usable volume ranges. Powdery substances can be mixed homogeneously even at a filling level of only 10 percent. The maximum filling level is approx. 75 percent. Cone mixers deliver consistently good mixing quality across the entire range. Other mixer designs are significantly limited in their flexibility.
If a mixing company wants to purchase a new powder mixer, certain data should be specified in the specifications. These include
- Maximum batch volume in litres
- Maximum batch weight in kg
- Minimum batch volume in litres
- Minimum batch volume in litres
- This requires precise knowledge of the minimum and maximum bulk density (kg/dm³) of the finished powder mixture. This cannot be calculated; it must be measured.
The type designations of powder mixers are not very meaningful in practice. Some manufacturers define the size of their mixers according to their gross volume, others according to their maximum usable volume. Only when all these specifications match is it possible to make a fair price comparison between different mixer types.
Due to the specifications in the requirements specification, there are differences in drive power and mixing times depending on the mixer type.
Deagglomeration during the mixing process:
The question of the minimum filling level is particularly important in certain cases. Effective deagglomeration is required for some mixing processes.Fast-running dispersing tools are used for this purpose. These are also known as cutting rotors, knife heads, mixing accelerators, choppers or hexlers. They only work effectively when they are installed completely below the product level. This means that the minimum filling level must be correspondingly higher when they are used.
This is not a problem for amixon cone mixers. These mixers can achieve high dispersion performance even at very low fill levels. This can be clearly seen in the adjacent illustration.
In any case, it is advisable to carry out practical tests in the technical centre before purchasing a mixer.