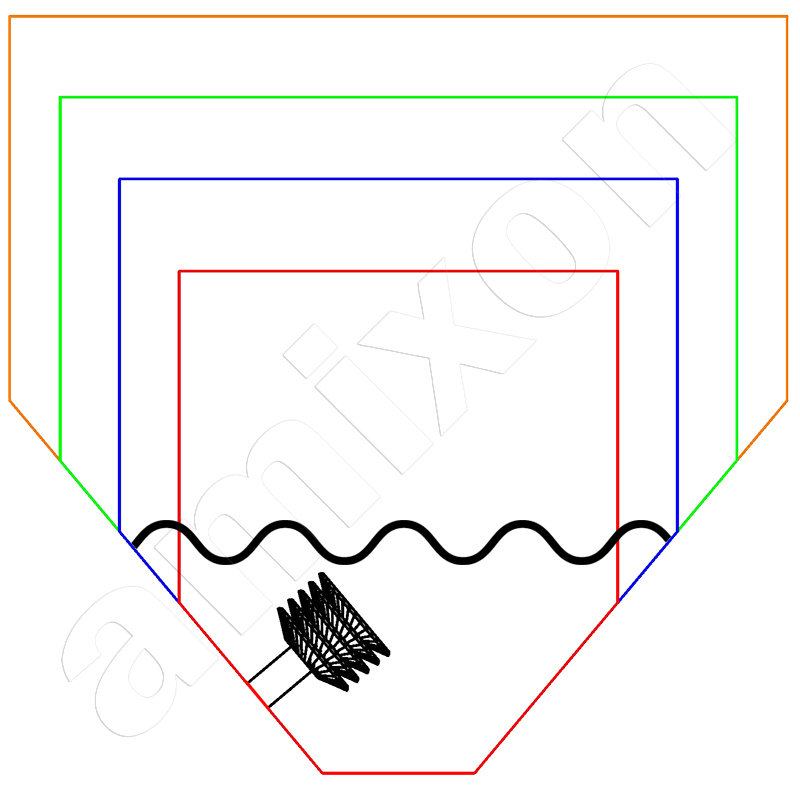
Degré de remplissage
Le degré de remplissage décrit le rapport entre le volume de produit rempli et l'espace disponible dans une machine de traitement. Cela concerne en particulier les mélangeurs de poudres.
Lors du traitement de solides pulvérulents, un mélangeur ne doit en aucun cas être rempli complètement. L'outil de mélange se bloquerait et pourrait être endommagé. Les mélangeurs de poudre ont besoin d'un espace libre pour pouvoir mélanger le produit en vrac. Cet espace libre est également appelé espace gazeux. Il est nécessaire pour réduire la densité des particules et aérer la poudre. L'aération s'effectue en soulevant la poudre à l'encontre de la force de gravité. Les particules sont alors moins compactes. Le frottement interne de la poudre est réduit et la mobilité des particules améliorée. Ce n'est que dans un état aéré que les poudres peuvent être mélangées de manière homogène.
Lors du mélange de liquides à faible viscosité, aucun espace gazeux n'est nécessaire. Le degré de remplissage peut alors atteindre 100 %. Dans de tels cas, il est même souhaitable qu'aucun air ne pénètre dans le liquide.
Dans les mélangeurs de matières solides, en revanche, il existe un degré de remplissage minimal et maximal selon le type de construction. C'est dans cette « plage de volume utile » que le mélangeur fonctionne efficacement et produit des qualités de mélange optimales. Le degré de remplissage se rapporte idéalement au volume brut de la chambre de mélange moins le volume de l'outil de mélange.
Les mélangeurs coniques d'amixon disposent de plages de volume utile particulièrement importantes. Même avec un taux de remplissage de seulement 10 %, les substances pulvérulentes peuvent être mélangées de manière homogène. Le taux de remplissage maximal est d'environ 75 %. Les mélangeurs coniques offrent une qualité de mélange constante sur toute la plage. D'autres types de mélangeurs sont nettement plus limités en termes de flexibilité.
Si une entreprise de mélange souhaite acquérir un nouveau mélangeur de poudres, certaines données doivent être précisées dans le cahier des charges. Il s'agit notamment
- du volume maximal des charges en litres
- de la masse maximale des charges en kg
- du volume minimal des charges en litres
- du volume minimal des charges en litres
- Cela nécessite une connaissance précise de la densité apparente minimale et maximale (kg/dm³) des poudres mélangées. Celle-ci ne peut pas être calculée. Elle doit être mesurée.
Les désignations des types de mélangeurs de poudres ne sont pas très significatives dans la pratique. Certains fabricants définissent la taille de leurs mélangeurs en fonction du volume brut, d'autres en fonction du volume maximal utilisable. Ce n'est que lorsque toutes ces informations concordent qu'il est possible de comparer équitablement les prix des différents types de mélangeurs.
En raison des spécifications du cahier des charges, il existe des différences de puissance d'entraînement et de temps de mélange selon le type de mélangeur.
Désagglomération pendant le processus de mélange :
La question du degré de remplissage minimum est particulièrement importante dans certains cas. Certains processus de mélange nécessitent une désagglomération efficace.Pour cela, on utilise des outils de dispersion à rotation rapide. Ceux-ci sont également appelés rotor de coupe, tête de coupe, accélérateur de mélange, broyeur ou hachoir. Ils ne fonctionnent efficacement que s'ils sont installés complètement en dessous du niveau du produit. Cela signifie que leur utilisation nécessite un niveau de remplissage minimum plus élevé.
Ce n'est pas un problème pour les mélangeurs coniques d'amixon. Ces mélangeurs peuvent développer une puissance de dispersion élevée même à des niveaux de remplissage très faibles. Cela est clairement visible sur l'illustration ci-contre.
Dans tous les cas, il est recommandé de réaliser des essais pratiques en laboratoire avant d'acheter un mélangeur.