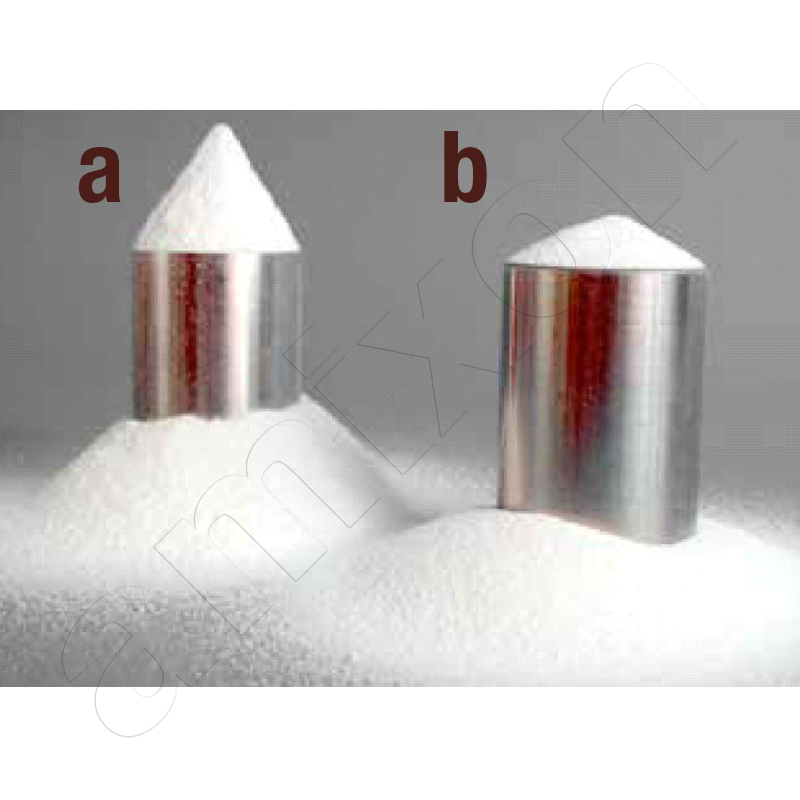
Flow properties
The flow behaviour of bulk solids is a key issue in process engineering. Unlike liquids, which only exert vertical pressure forces on the container wall when at rest, bulk solids also generate shear forces when at rest. These result from the internal friction of the bulk solid and the wall friction. Internal friction is specific to the material and depends on pressure. The behaviour can be compared to Mohr's concept of triaxial stress state.
American engineer Andrew Jenike and other scientists have systematically investigated the flow properties of bulk solids. A ‘Jenike shear device’ can be used to determine so-called flow points. These provide information on how a silo must be designed to ensure a controlled mass flow.
Important parameters for the design of a silo are
- Total height of the silo
- Diameter
- Material and its surface properties
- Wall roughness
- Cone angle
- Discharge speed
- Discharge diameter
The aim is to design silos in such a way that the bulk material flows out reliably and evenly under all operating conditions. Ideally, discharge takes place in a mass flow. All areas of bulk material move downwards simultaneously and evenly. There is no chimney effect or core flow. Segregation within the silo is also avoided.
Powder technology and the flow properties of powders are the subject of numerous scientific studies: Professor at the Friedrich-Alexander University of Erlangen-Nuremberg. He is an expert in particle and interface process engineering. Professor Bernd Kieback, long-time head of the Chair of Powder Metallurgy at the Technical University of Dresden and the Fraunhofer IFAM in Dresden. Professor Hermann Riedel, former head of the Fraunhofer Institute for Mechanics of Materials (IWM) in Freiburg. Lutz Mädler, professor at the University of Bremen and coordinator of the DFG Priority Programme 2289 on mixing dispersive systems. Bilal Gökce, Professor at the University of Wuppertal with a focus on materials for additive manufacturing.
Flow properties and particle shape are particularly important in additive manufacturing processes. The flow properties determine how well the powder can be distributed in the system. Only if the powder flows well can dense, homogeneous layers be formed. Poor flow properties lead to defects in the component.
The particle shape strongly influences the flow behaviour. Spherical particles flow better than irregularly shaped ones. Metal powders from gas atomisation usually have a good spherical shape. Powders from water atomisation are often angular and flow less well. The particle size distribution is also important. A narrow particle size distribution with as few fine particles as possible improves the flow properties. Fine particles tend to agglomerate and can impair flowability. Important parameters are the packing density and the tamping density.
The flow properties of powders play a decisive role not only in storage but also in filling and packaging. In modern filling plants, e.g. when packaging instant tea in sachets, the processes run at very high speeds. This speed is only possible if the powder has uniform flow properties. It must also be largely dust-free. Otherwise, problems may arise when sealing the packaging. Fine dust on the seal prevents a tight closure.
Internal logistics in powder-processing companies also depend on adequate flow properties. Production processes can only be automated if all powders used have defined flow behaviour.
Chemical and pharmaceutical active ingredient powders (API) sometimes have extremely poor flow properties when they consist of microfine particles. This is particularly true for active ingredients from multi-stage syntheses with nano-fine particles. These can even adhere to smooth stainless steel surfaces. Even these flow properties can be improved. One option is the targeted addition of small amounts of flow aids, such as pyrogenic silica (Aerosil). Alternatively, the particle size can be increased in a targeted manner through agglomeration.
Numerous measurement methods are available for characterising flow properties. Various devices and systems are available on the market:
- Ring shear devices from Dietmar Schulze Schüttgutmesstechnik These devices, such as the RST-XS.s and the RST Mk II, precisely measure flow properties such as internal friction, time consolidation and wall friction. They are particularly suitable for silo design and the characterisation of bulk solids such as flour, pharmaceutical powders or cement. Dietmar Schulze+2Dietmar Schulze+2Dietmar Schulze+2
- FT4 powder rheometer from Freeman Technology A versatile device for characterising powder rheology. It enables measurements under various conditions, including consolidated, aerated or fluidised states, and provides comprehensive data on powder behaviour.
- ERWEKA GT series granulate flow testers This series includes devices that offer various measurement methods for determining the flow behaviour of powders and granulates. Among other things, they enable the measurement of the angle of repose using laser technology.
- PF1 powder flow tester from SOTAX A flexible device for characterising the flow properties of powders and granulates. It combines three standardised test methods in one device and enables simple, repeatable tests.
- Powder tester from Pharma Test Apparatebau AG The PTG-S5 is an automatic powder flow tester for measuring the flow behaviour of granulates and powders according to various pharmaceutical active ingredients. It can be combined with an integrated NIR diode array spectrometer.