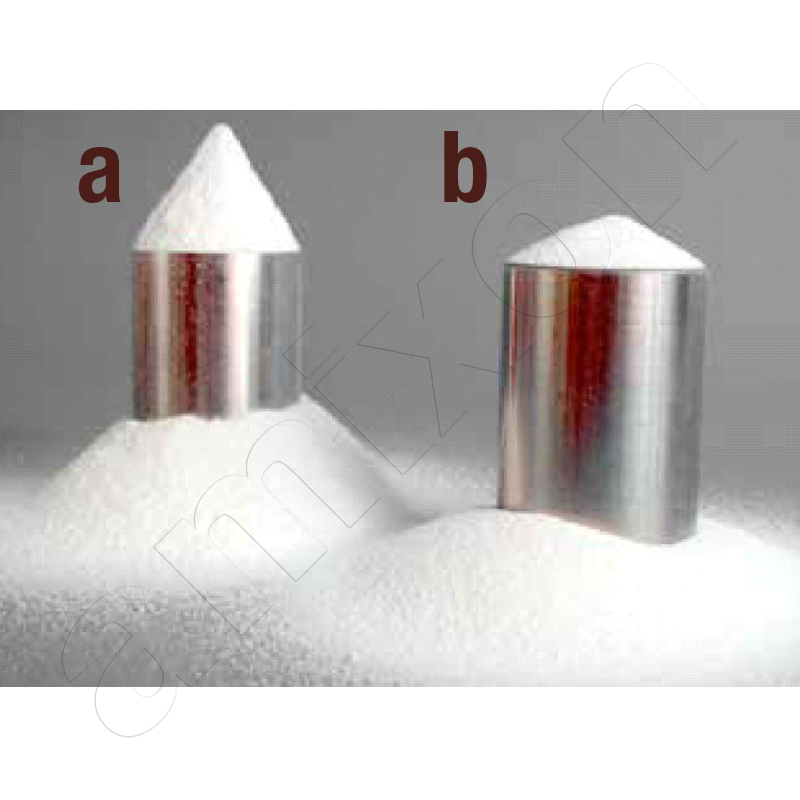
Właściwości płynięcia
Zachowanie się materiałów sypkich podczas przepływu jest kluczowym zagadnieniem w inżynierii procesowej. W przeciwieństwie do cieczy, które w stanie spoczynku wywierają na ścianki zbiornika wyłącznie siły nacisku pionowe, materiały sypkie w stanie spoczynku wytwarzają dodatkowo siły ścinające. Wynikają one z tarcia wewnętrznego materiału sypkiego oraz tarcia o ścianki zbiornika. Tarcie wewnętrzne jest specyficzne dla danego materiału i zależy od ciśnienia. Zachowanie to można porównać do koncepcji trójosiowego stanu naprężeń według Mohr.
Amerykański inżynier Andrew Jenike i inni naukowcy przeprowadzili systematyczne badania właściwości płynięcia materiałów sypkich. Za pomocą „urządzenia do ścinania Jenike” można określić tzw. miejsca płynięcia. Informują one o tym, jak należy skonstruować silos, aby zapewnić kontrolowany przepływ masy.
Ważnymi parametrami przy projektowaniu silosu są
- całkowita wysokość silosu
- średnica
- materiał i jego właściwości powierzchniowe
- chropowatość ścianek
- kąt stożka
- prędkość wydalania
- średnica wylotu
Celem jest skonstruowanie silosów w taki sposób, aby materiał sypki wypływał niezawodnie i równomiernie w każdych warunkach pracy. Idealnie jest, gdy wydalanie odbywa się w przepływie masowym. Wszystkie obszary materiału sypkiego poruszają się jednocześnie i równomiernie w dół. Nie dochodzi do tworzenia się kominów ani przepływu rdzeniowego. Unika się również rozdzielania składników w silosie.
Technologia proszkowa i właściwości przepływowe proszków są przedmiotem licznych prac naukowych: Profesor Uniwersytetu Fryderyka Aleksandra w Erlangen-Norymberdze. Jest ekspertem w dziedzinie technologii cząstek i procesów międzyfazowych. Profesor Bernd Kieback, wieloletni kierownik Katedry Metalurgii Proszkowej na Uniwersytecie Technicznym w Dreźnie oraz Fraunhofer IFAM w Dreźnie. Profesor Hermann Riedel, były kierownik Instytutu Mechaniki Materiałów Fraunhofera (IWM) we Fryburgu. Lutz Mädler, profesor Uniwersytetu w Bremie i koordynator programu DFG 2289 dotyczącego mieszania układów dyspersyjnych. Bilal Gökce, profesor Uniwersytetu Bergischen w Wuppertalu, specjalizujący się w materiałach do produkcji addytywnej.
W procesach produkcji addytywnej szczególne znaczenie mają właściwości płynięcia i kształt cząstek. Właściwości płynięcia decydują o tym, jak dobrze proszek rozprowadza się w systemie. Tylko wtedy, gdy proszek dobrze płynie, powstają gęste, jednorodne warstwy. Złe właściwości płynięcia prowadzą do powstawania wad w elemencie konstrukcyjnym.
Kształt cząstek ma duży wpływ na właściwości płynięcia. Cząstki kuliste płyną lepiej niż cząstki o nieregularnym kształcie. Proszki metalowe uzyskane w procesie rozpylania gazowego mają zazwyczaj dobry kształt kulisty. Proszki z rozpylania wodnego są często kanciaste i gorzej płyną. Ważny jest również rozkład wielkości ziaren. Wąski rozkład wielkości ziaren z jak najmniejszą zawartością drobnych cząstek poprawia właściwości płynięcia. Drobne cząstki mają tendencję do aglomeracji i mogą pogarszać płynność. Ważnymi parametrami są gęstość upakowania i gęstość ubijania.
Właściwości przepływowe proszków odgrywają decydującą rolę nie tylko podczas przechowywania, ale także podczas napełniania i pakowania. W nowoczesnych zakładach napełniania, np. podczas pakowania herbaty instant w saszetki, procesy przebiegają z bardzo dużą prędkością. Taka prędkość jest możliwa tylko wtedy, gdy proszek ma równomierne właściwości przepływowe. Ponadto musi być w znacznym stopniu wolny od pyłu. W przeciwnym razie mogą wystąpić problemy z uszczelnieniem opakowania. Drobny pył na zgrzewie uniemożliwia szczelne zamknięcie.
Również logistyka wewnętrzna w zakładach przetwórstwa proszków wymaga odpowiednich właściwości płynięcia. Tylko wtedy, gdy wszystkie stosowane proszki wykazują określone właściwości płynięcia, można zautomatyzować procesy produkcyjne.
Proszki substancji czynnych chemicznych i farmaceutycznych (API) mają czasami bardzo złe właściwości płynięcia, jeśli składają się z mikrocząstek. Dotyczy to w szczególności substancji czynnych pochodzących z wielostopniowych syntez z nanocząsteczkami. Mogą one nawet przylegać do gładkich powierzchni ze stali nierdzewnej. Również takie właściwości przepływowe można poprawić. Jedną z możliwości jest celowe dodanie niewielkich ilości środków przeciwzbrylających, takich jak pirogeniczny kwas krzemowy (Aerosil). Alternatywnie można celowo zwiększyć wielkość cząstek poprzez aglomerację.
Do charakteryzowania właściwości przepływowych dostępnych jest wiele metod pomiarowych. Na rynku dostępne są różne urządzenia i systemy:
- Urządzenia pierścieniowe firmy Dietmar Schulze Schüttgutmesstechnik Urządzenia te, takie jak RST-XS.s i RST Mk II, precyzyjnie mierzą właściwości płynięcia, takie jak tarcie wewnętrzne, utwardzanie w czasie i tarcie ścienne. Nadają się one szczególnie do projektowania silosów i charakteryzowania materiałów sypkich, takich jak mąka, proszki farmaceutyczne lub cement. Dietmar Schulze+2Dietmar Schulze+2Dietmar Schulze+2
- Reometr proszkowy FT4 firmy Freeman Technology Wszechstronne urządzenie do charakteryzowania reologii proszków. Umożliwia pomiary w różnych warunkach, w tym w stanie zestalonym, napowietrzonym lub fluidyzowanym, i dostarcza kompleksowych danych dotyczących zachowania proszków.
- ERWEKA Urządzenia do badania płynności granulatu serii GT Seria ta obejmuje urządzenia oferujące różne metody pomiarowe do określania właściwości płynięcia proszków i granulatów. Umożliwiają one między innymi pomiar kąta sypania za pomocą technologii laserowej.
- PF1 Urządzenie do badania płynności proszków firmy SOTAX Elastyczne urządzenie do charakteryzowania właściwości płynięcia proszków i granulatów. Łączy trzy standardowe metody testowe w jednym urządzeniu i umożliwia proste, powtarzalne testy.
- Tester proszków firmy Pharma Test Apparatebau AG PTG-S5 to automatyczny tester przepływu proszków do pomiaru właściwości przepływowych granulatów i proszków według różnych substancji czynnych farmaceutycznych. Możliwe jest połączenie z wbudowanym spektrometrem diodowym NIR.