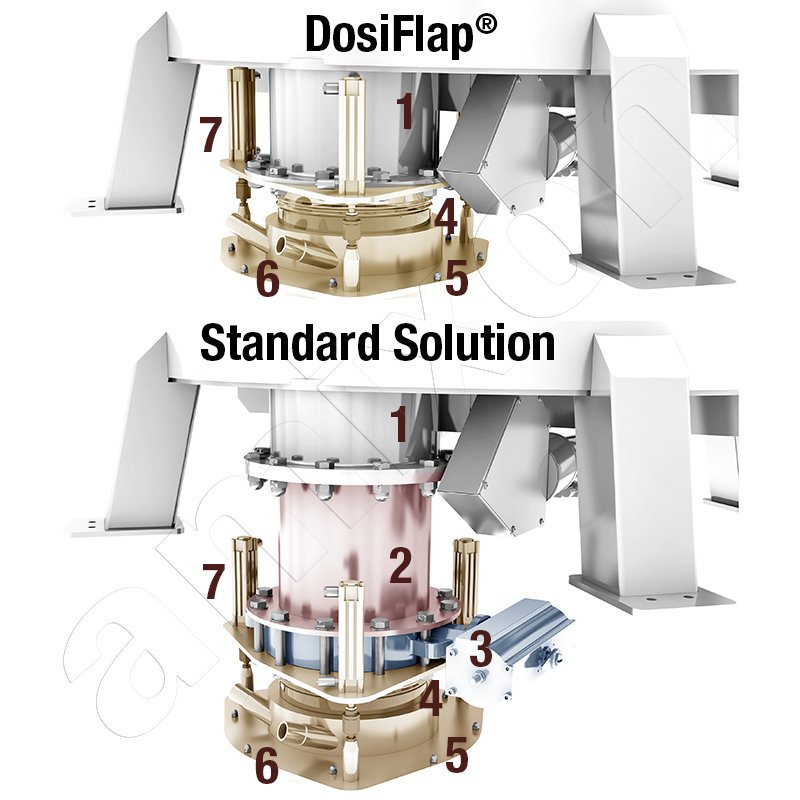
Above you can see the DosiFlap® solution. It requires little vertical space. It closes the mixing chamber free of dead space and regulates the mix discharge. Below is the default solution. A rotary flap is installed below the mixer's discharge flap, which regulates the discharge of the mix.
FAQ: The powder mixer fills standard bulk containers and Bigbags
Powder mixers can also discharge large amounts of mixture in portions; in big bags or bulk containers (IBS)
- Mixer discharge nozzle with integrated discharge flap
- Extension piece (so that the discharge flap and the rotary flap do not collide)
- Rotary flap
- Bellows
- Support plate rests on the container nozzle and then lifts up a few mm
- Air vent
- Lifting and lowering device for support plate
Standard solution
Another fitting suitable for powder is installed below the dead space-free flap of the mixer. This is usually a rotary valve. This can close and open slowly or quickly against the outflowing mix. It is well suited to control the filling level of a container or big bag. However, the function of a rotary valve is not comparable with the performance of a filling machine. A targeted filling weight in the container can only be achieved approximately. This classic solution works well in industrial practice as long as the powders flow reasonably well. If the powder accumulates between the two fittings, another solution must be found.
Closing of the amixon® mixer with DosiFlap®
This is a new kind of closing and sealing technology that allows the flap to be closed and opened at any time against the downflowing mix. The powder flow becomes more and more constricted and is reliably stopped when the flap closes the mixing chamber in the end position. One and the same fitting can seal the mixing chamber free of dead space and close against the mixed material flowing down.
Powder discharge from the large mixer into bulk containers and big bags
Question: Is it possible to fill mixed products directly from the mixer in portions into big bags or containers? The difficulty is to avoid underfilling or overfilling the container or big bag.
Reply from amixon: In fact, it happens frequently that mixed products have to be filled directly from the mixer into containers or other packages. The task can be realized quite easily if the entire mixed batch fits exactly into a container/big bag. The matter becomes more complicated when the mixed batch is several times larger than the capacity of the container. In this case, the outflowing mixing goods must be throttled and cut off at the right time, in accordance with the increasing degree of filling in the container. The discharge valve of a precision powder mixer - regardless of the manufacturer - is designed as a butterfly valve that operates without dead space. Normally, it must only be closed when no powder trickles out, i.e. when the mixer is emptied. This restriction is due to the design of the discharge flap. During mixing, it must seal the mixing chamber in a coplanar, dead-space-free and gas-tight manner. It can only do so if it follows the contour of the mixing chamber in the closed state. If an attempt were made to close the standard butterfly valve against the down flowing product stream, then particles of mixed material would become trapped in the seal of the valve. The seal would be destroyed over time and the flap would leak. The problem described above can be solved in two ways: Standard solution or DosiFlap®.
Question: What advantages does DosiFlap® offer for the user?
Reply from amixon®: Ultimately, there are three advantages:
- Mixtures that flow poorly can also be poured directly from the mixer into containers or big bags without overfilling the containers. The danger of accumulation below the flap is low, because the powder, being in free fall, trickles downwards without any build-up.
- The elimination of the rotating flap means that there is more space available under the mixer. The lack of vertical installation space under a mixer is synonymous with a loss of ergonomics and performance.
- The absence of a second fitting means it never needs to be cleaned.
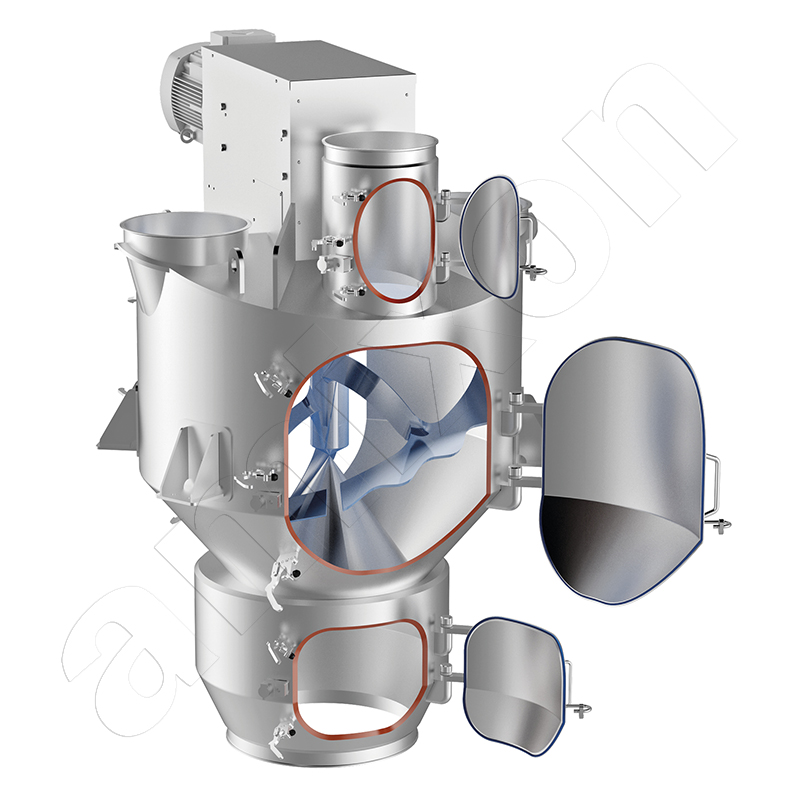
Discharge nozzle has an OmgaSeal type inspection flap
Dead space-free discharge fitting that can be cleaned very easily
Please note: Butterfly valves are located inside pipelines. They are difficult to access. If thorough cleaning is desired, it would have to be disassembled. Some operators nevertheless clean the butterfly valve in the assembled state by spraying the valve inside the pipeline with washing water from above and from below. This usually works well if the system is dried thoroughly afterwards. Depending on the design, rotary flaps can have capillaries that make drying difficult.
At this point, a very nice hygienic solution from amixon® should be mentioned. The nozzles above and below the mixer are fitted with inspection doors. In this respect, the operator can conveniently check the cleaning status or carry it out manually. Even replacing a worn seal is easy with this inspection flap. It is designed according to the Clever-Cut® principle and has an O-ring seal that seals particularly close to the mixing goods. The design is almost free of dead space. This particularly hygienic sealing groove bears the name OmgaSeal®.
© Copyright by amixon GmbH