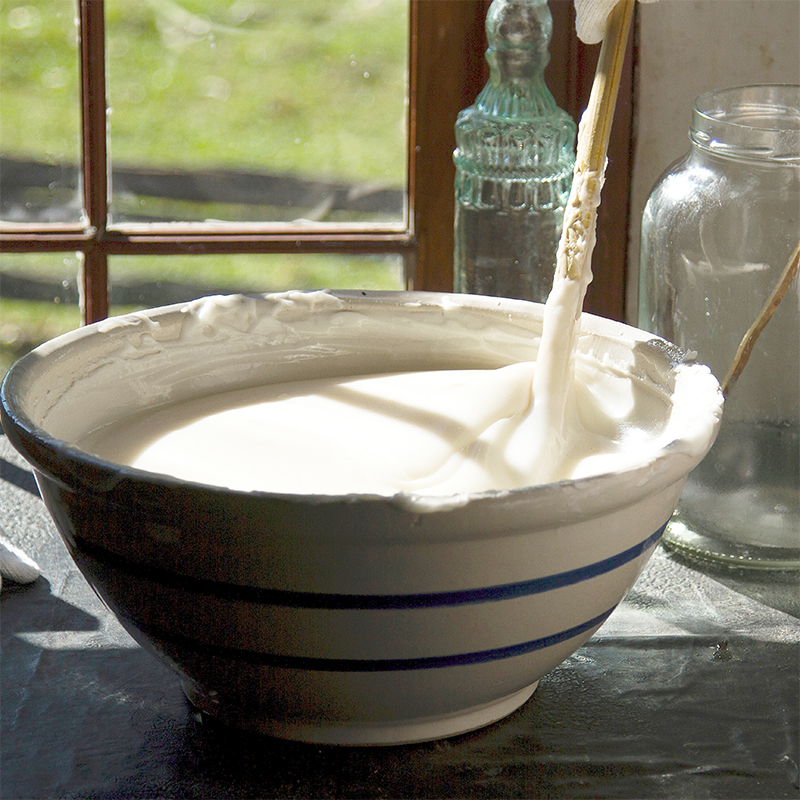
Soaps are inexpensive anionic surfactants. Hard soaps are based on sodium salts. Soft soaps are based on potassium salt.
amixon® mixers and reactors in oleochemistry for the production of detergents and metal soaps
Oleochemistry influences the quality of products as diverse as cosmetics, plastics, rubber, food, surface protection, paper, pharmaceuticals, lubricants, ....
In the production of detergents and metal soaps, many specific requirements are placed on the mixers/synthesis reactors. amixon equipment fulfills these special tasks in an exemplary manner.
Soaps are potassium salts and sodium salts of fatty acids. Soap is one of the oldest chemical products. Even primitive peoples knew about the lubricating and separating effect of soap. They used the ash from burnt wood and mixed it in water to make a diluted lye. They strained the ash residue from the liquid phase and vaporized it. Thus, they concentrated the weak lye and mixed it with oil and fat - preferably in a heated state. The onset of turbidity is an indication of the formation of soap suds, which has fat- and water-solving properties. Ideally, the more solid components of the soapsuds were separated from the more liquid ones. This made them easier to store and transport. This method was used by the Sumerians as early as 3000 BC, using the soap substance for healing purposes.
amixon® mixers, vacuum dryers and synthesis reactors for the production of magnesium stearate, calcium stearate and sodium stearate
Soaps are not only used for cleaning. In the metalworking industry, they play an important role as lubricants, for example in the deep drawing of car bodies or steel bathtubs. They also provide the necessary lubricating layer in cold deep drawing and in the so-called pilgrimage of pipes.
These are the metal soaps magnesium stearate, calcium stearate and sodium stearate. They are abbreviated as stearates. They are produced by esterifying stearic acid with metal oxides or hydroxides. This produces a finely dispersed, waxy powder with the separation of glycerine.
Unlike classic potassium or sodium soaps, metal soaps are not water-soluble. They usually appear as a white powder. Even small amounts of this powder can improve the flowability of poorly flowing bulk materials. However, they must be distributed evenly throughout the bulk material. This property makes them valuable additives – not only in the pharmaceutical and cosmetics industries, but also in feed and food processing. There, they prevent the formation of bridges in silos. They facilitate the conveying processes.
European patent specification EP 0330097 describes a process for producing basic metal soaps based on stearic acid. Precise temperature control and the selection of a suitable mixing system are crucial in this process. This makes it possible to produce a light-coloured, fine-grained and free-flowing product. The transition from the liquid to the solid phase occurs spontaneously. The product is then dried under vacuum. Other processes, such as those described in German patent application DE 4019167 A1, rely on a two-stage process. The aim is to produce a flaky, low-dust powder with stable flowability.
amixon® conical processing units are also designed and manufactured according to the customer's specific requirements.
The production chain for metal soaps is highly complex and very individually shaped by company-specific process philosophies. The process step "powder mixing" is important at several points: first for the collection and preparation of the raw materials and then for carrying out the syntheses. The hydroxides of the metals mentioned are introduced in powder form, along with suitable oils and fats. The mass is heated and homogenized to a low-viscosity suspension, which becomes a viscous paste after adding small amounts of a catalyst or heating the mass. The reaction then continues with the reactor vessel closed, with strong heat generation, and the system pressure increases to values that are many times higher than the ambient pressure. After the reaction is complete, the synthesis reactor is evacuated to dry and cool the mass. The end result is a white, finely dispersed powder.
Cleansing effect of soap
It was not until Roman times that the cleansing effect of soap was cultivated. Roman writings mention the Germanic soap, which consisted of tallow, ash and plant juices. It was used to dye the skin and hair red before the fight. The art of soap boiling is said to have been passed on from the Arabs to the Spaniards, and Charlemagne encouraged the settlement of soap boilers in the Franconian Empire during his reign from 768 to 814. Old German terms such as Seifa, Seipha or Säpa for soft soap have been handed down. The production of hard white soap was considered special and was favored by the use of marine plants and olive oil as raw materials. Infused with medicinal herbs, antioxidants, deodorants and fragrance oils, soap was a coveted luxury item.
Around 900, Marseille was a stronghold of soap production. Five centuries later, it was the Italian cities of Savona, Venice and Genoa. King Louis XVI (reigned 1775 to January 21, 1793) issued a quality guideline for soap in France: The oil content had to be at least 72 percent by weight.
amixon® Continuous mixer for powder detergents
In this plant, heavy-duty detergents, color detergents and mild detergents are filled. High-performance filling lines must operate as uninterruptedly as possible. The material supply must be continuous. A continuous mixer from amixon® reliably fulfills this task. In this case, the mixing principle of continuous boiler flow applies. This continuous mixer can mix up to five solid streams. The various components are metered from the top according to the recipe, mixed in the mixer and discharged to the bottom. This continuous mixer can feed 1, 2 or 3 filling machines simultaneously.
The use of an amixon® mixer ensures particularly gentle homogenization. The particles of the mixture retain their structure and size. At the end of a production campaign, the mixer can discharge completely automatically if the mixing tool is equipped with ComDisc® tools.
Early industrial production
Around 1900, industrial processes replaced potash with artificial soda ash as well as the strong alkalis sodium hydroxide and potassium hydroxide. The basic chemicals perborate and silicate gave rise to Henkel's Persil brand product in 1907. In 1929, Benckiser developed a dishwashing detergent for the hotel and restaurant industry in Ludwigshafen. Curd soap became a mass product. To this day, great efforts have been made to make detergents more environmentally friendly. For example, the enzymes and surfactants used in modern detergents are biodegradable, microplastics, phosphates and bleaching agents are not used.
In addition to the foaming and washing capacity, the phenomenon of "soap skin" should be mentioned. In this process, the property of soap forming a surface film is utilized. If a spatially irregularly curved wire loop is dipped into a soap solution and lifted, a soap skin is formed. The area stretched in this way represents the minimum surface area. The irregularly shaped roofs of the Olympic tents in Munich were optimized using this method.
This amixon® twin-shaft mixer mixes batchwise
Another specialty concerns the final mixing of dishwasher detergent tabs / compacts. These consist of different formulations, which are often colored differently. They indicate advanced functions and stand for "grease remover", "rinse aid", "extra-dry effect", "cleaning booster", "water softener" or even "drugstore tab". High-performance tablet presses are capable of forming tabs from different colored tablet parts.
This requires that the various washing powders are mixed in such a way that their particle shape is maintained. The specific flow and cohesion properties must also be maintained. In order to maintain the function of so-called exploders, mixing must be extremely gentle. Such batch mixers must work largely self-cleaning and self-discharging.
Special application: Continuous agglomeration with increased energy input
Powder detergents are sometimes post-treated to densify them. This saves transport costs and packaging material. Continuously operating mixing granulators produce round agglomerates from a powdery washing-active substance by build-up granulation. In most cases, small amounts of a liquid binder are added. The amount of liquid should be as small as possible to avoid subsequent thermal drying. The previously powdery-dusty bulk material is then granular and low in dust. Agglomerated bulk materials are generally easy to dose and fill.
Ideal mixing quality with minimum energy input
The commercial importance of soap extends to its washing-active property as a detergent for personal care, clothing, dishes and household cleaning in liquid and solid form as powder, granules, ball or tablet. A completely different field of application extends to the industrial applications of stearates.
A look at the product range of major stearate manufacturers shows how broad the application spectrum of metal soaps is: Calcium stearates and zinc stearates are effective stabilizers in plastic production and allow the use of PVC for drinking water pipes. The PVC plastic is stabilized against washout. Calcium stearate is also used as a lubricant additive in rolling bearings.
The stearates of the metals zinc, sodium, barium, lithium and aluminum have very different efficacies in different compositions: For example, as a chemical acid scavenger, as an impregnating agent, as a vulcanization aid for rubber, as a lubricant in metal processing, as a hydrophobizing agent in the manufacture of building materials, as a release agent or adhesion promoter, as an abrasive when lapping surfaces or as a matting agent for paint lacquers, as a thickener/emulsifier in creams, shampoos and foods, for hydrophobizing absorbent materials.
With a particle size of 3 to 15 µm, magnesium stearate has a very large surface area and, in the smallest concentrations, serves as an effective flow aid for bulk materials of all kinds. However, it is important that the mixing process is gentle and precise. High shear mixing reduces the flowability. Without magnesium stearate, the production output of today's tablet presses would be unthinkable.
Summary
amixon® mixers
- amixon® machines are able to achieve a technically ideal mixing quality in a short time with minimum energy input, which cannot be further improved in practice.
- Since the metallic soaps consist of very fine powder, the risk of dust explosion is increased. amixon® mixers are certified according to Atex type testing.
- In the amixon® mixer, ideal mixing quality is achieved even at peripheral speeds of the mixing tool of less than 1 m/s.
- The powder derivatives of oleo chemistry usually have poor flow properties. amixon® mixers are capable of mixing even poorly flowing powders homogeneously and discharging them completely.
- amixon® mixers can be used flexibly. They mix equally well even at low filling levels.
- amixon® mixers have large inspection doors. They are easily accessible when manual cleaning is required.
- amixon® mixers are permanently gas-tight. This is especially important when the mixing chamber is inerted with nitrogen.
amixon® vacuum dryers/ synthesis reactors
- Thermal processes work more effectively the more heat exchange surface is available. amixon® processing equipment can be heated and cooled over its entire surface: Mixing shaft, static mixing tools, mixing arm and mixing helix, and the entire mixing chamber.
- The consistency of the mixing goods can vary depending on the reaction process: liquid, semi-solid, highly viscous or powdery. amixon® devices mix ideally and effectively in every phase.
- Frequent load changes lead to material fatigue. This is especially true when process temperatures change frequently and rapidly. amixon® has decades of experience and is able to design and manufacture apparatus in such a way that they still have a long service life.
Use the amixon® test machines for your process optimization!
amixon has gained extensive experience in various fields of synthesis reaction control since 1983 and offers users a comprehensive range of process machines with vertically mounted helical mixing tools.
In the amixon test center, 20 different vertical mixing systems and 4 different synthesis reactors are available for trials. Tests in the pilot plant usually deliver first-class results.
© Copyright by amixon GmbH