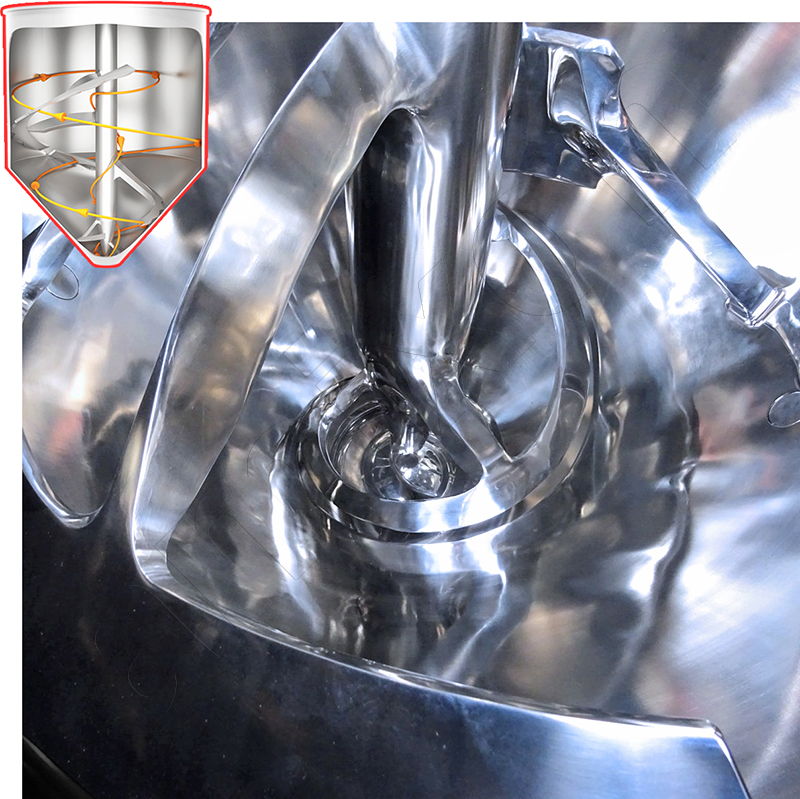
Mixing solids
Solid mixing versus liquid mixing
Mixing solids and liquids is fundamentally different. The differences relate to physical properties, measurement technology, process control, conveying technology and mixing technology.
Liquids are easier to characterise. A few parameters such as viscosity, density and rheological behaviour are often sufficient. In the shear viscometer, for example, you can see whether the flow behaviour is Newtonian, structurally viscous or dilatant. Dilatant properties usually occur with highly concentrated pastes.
This information is sufficient to simulate the mixing process and design suitable mixing tools.
Das Verströmen von Flüssigkeiten ist deutlich einfacher als das Verströmen von Feststoffen. Mit kleinen Mischwerkzeugen lassen sich große Flüssigkeitsmengen homogenisieren. Flüssigkeiten verhalten sich als Kontinuum. Druckkräfte lassen sich direkt in Bewegung umwandeln.
A rotationally symmetrical mixing vessel avoids dead zones. It is particularly effective if the axis of rotation is off-centre and inclined. This creates vortices that improve the mixing result. Depending on the viscosity, rotational frequency and mould geometry, laminar or turbulent flows can be generated.
Mixing solids is much more complex. Powders and granulates consist of many individual particles. These differ in shape, size, density, surface roughness, moisture, cohesion and other properties. Their behaviour is difficult to predict.
There is no simple description of the flow behaviour of bulk solids. Classical parameters such as viscosity do not exist. Therefore, special methods are needed to simulate bulk materials and their flowability.
Solids are mixed by setting all particles in random relative motion - for example by gravity, upward conveying, loosening or turbulence. This requires special expertise. Especially with shear-sensitive products. Or for large volumes with poorly flowing or moist powders.
To summarise: Liquid blending is often predictable, efficient and easily scalable. Liquids behave as a continuum.
Mixing solids is more complex. The characterisation of a powder often requires more than 20 measured variables. One example is the determination of flow locations using the Jenike shear tester. "The higher the powder level in the silo, the worse the flow behaviour at the outlet".
Simulations can usually depict liquid processes well. This is different for solids. The multitude of particle interactions is almost impossible to calculate. Simulations are therefore expensive and often inaccurate.
This is why amixon® operates technical centres worldwide (Germany, USA, India, China, Thailand, Korea and Japan). Mixing processes are demonstrated there. As a rule, very good results are achieved straight away. Extrapolations can then be made on site.