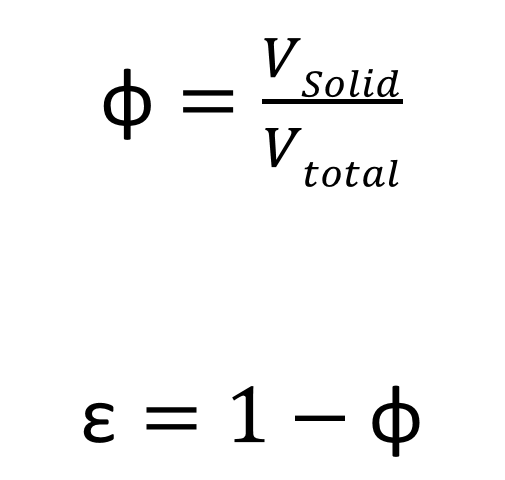
Solids (Bulk)
A solid is a state of matter in which the molecules or atoms are arranged in a fixed lattice or amorphous structure. In a technical context, however, solids are rarely homogeneous, especially when processing powders. They usually exist as multi-phase systems.
Powdered solids form so-called dispersed aggregates, i.e. collections of irregularly shaped particles of different sizes. There are inevitably voids between these particles, which are typically filled with ambient air. Such dispersions are therefore two-phase (solid + gas). If a liquid is also present, e.g. due to water adsorption or the hygroscopic properties of the particles, a three-phase system (solid + liquid + gas) exists.
The geometric arrangement and density of these aggregates is described by the so-called packing density, which can vary greatly depending on the particle shape, size and distribution. The porosity of a powder can be described mathematically and is decisive for many process engineering parameters, e.g. for flow behaviour, miscibility, drying or solubility.
ϕ : Packing density
VSolid : Volume of the solid
Vtotal : Volume of the powder mixture
ε : Porosity
Some industrial applications make targeted use of the gas phase in powdered solids:
For example, in the production of long-life baby food or probiotic powders, the ambient air is evacuated from the packaging and replaced with a protective gas mixture, usually nitrogen and carbon dioxide. This gas mixture reduces oxidation reactions and protects the packaging from temperature fluctuations. The coefficient of thermal expansion is then similar to that of the ambient air.
Powdered solid concentrates offer many advantages over liquids:
- Higher active ingredient concentration per volume
- Lower packaging volume
- Significantly improved storage stability
At the same time, the processing of solids places high demands on process engineering. Mixing powders is much more complex than mixing liquids, as the following aspects, among others, must be taken into account
- Abrasion
- Flow behaviour
- Risk of lump formation
- Separation tendencies due to density differences
- Hygiene problems due to dust formation
Note
When developing powder concentrates, the focus is on easy wetting and dissolution.
Some powder concentrates exhibit difficult wetting and dispersing behaviour. Fine gas bubbles can be introduced. This can lead to undesirable foam formation. Especially with viscous liquids or hydrophobic powder surfaces, the bubbles tend to remain stable in the system even when a vacuum is applied. To compensate for these effects, various high-shear rotor-stator systems are used in practice.
amixon® manufactures precision mixers that maintain the good solubility of powders. They mix with minimal energy and shear. They enable the ideal mixing quality of all powdery or semi-solid solids – regardless of grain size, bulk density or moisture content. The proven three-dimensional mixing principle also works with varying filling levels in the mixer.