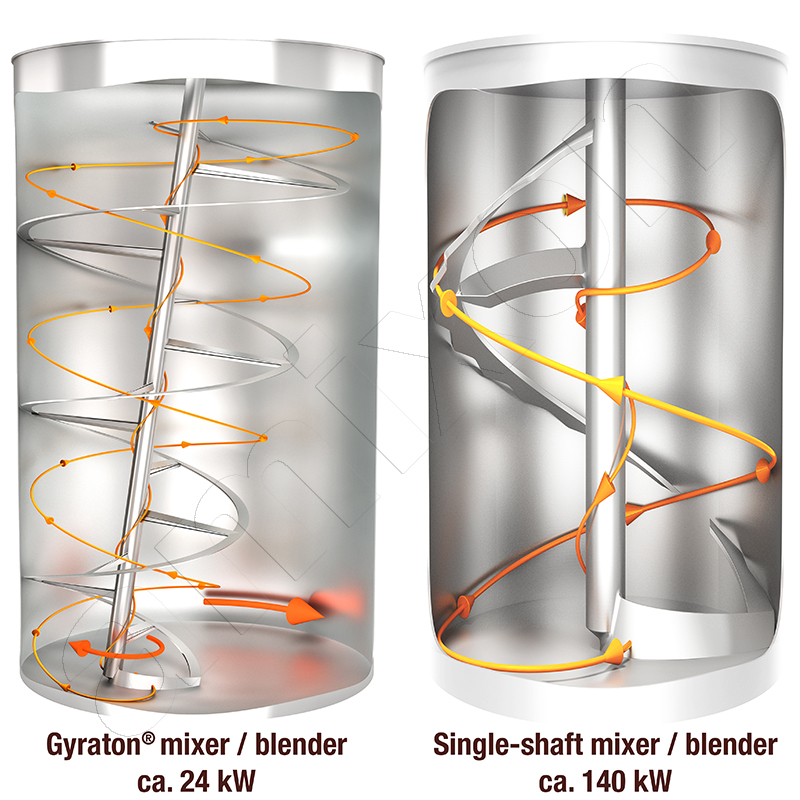
Slurry bunkers
Moisture silos are specialised silos or containers for storing and discharging moist masses such as pastes, slurries, suspensions or heavily moistened powders. Unlike dry, free-flowing bulk materials, these materials are characterised by severely restricted flow properties. Conventional silo systems reach their limits here, as moist bulk materials tend to block and cannot flow out on their own.
Moist materials arise as intermediate or end products in process engineering, for example after mechanical dehumidification by chamber filter presses, peeling centrifuges, belt presses or pressure nutches. Before thermal drying, these moist masses must be safely stored and dosed as required – a central task that moisture bunkers perform reliably.
Various drying processes are used in the processing industry. Tray dryers work on the principle of a tunnel oven. Here, the moist product is spread like dough on sheets or trays and passed through a heated channel. Vacuum drying uses negative pressure to dry at low temperatures in a particularly gentle manner. The vacuum mixing dryer is a particularly elegant solution that mixes, dries and homogenises at the same time. Devices such as the VMT or AMT from amixon combine these functions in a single system. In other cases, such as pumpable suspensions, spray dryers are used.
Regardless of the process used, it is essential that the moist materials are discharged safely from the storage container. As the moisture content increases, bulk materials lose their ability to flow. The internal adhesive and cohesive forces increase, which often leads to bridging, channel flow or complete material blockages. Some moist materials exhibit thixotropic properties: they solidify when at rest and only liquefy when agitated. To keep these materials storable and dosable, permanent, gentle agitation is necessary – for example, by means of agitators, screw conveyors or special mixing tools.
amixon® offers three different system solutions for the safe storage and reliable discharge of moist masses. The (1) VM vertical single-shaft mixer is equipped with a SinConcave mixing spiral and is particularly suitable for the gentle loosening and discharge of pasty products up to 40 m³. The (2) AM cone mixer has the same tool principle. It can even discharge tough, plastic masses safely. For particularly large batches of up to 100 cubic metres: The (3) Gyraton® mixing bunker is a particularly versatile solution. The Gyraton® can homogenise large batches with minimal drive power. In all cases, the mixing tool not only supports homogenisation but also ensures controlled discharge. In addition, amixon offers special designs of wet material bunkers that can function as fermenters or reactors, for example. These variants are often heatable, temperature-controllable and equipped with sensors and are mainly used in the chemical and biotechnological industries.
In many cases, the material is discharged directly from the wet material bunker into an amixon® vacuum mixing dryer.
In addition to the vertical mixing silos realised by amixon®, other types of moisture silos are used in process engineering. Agitator silos have integrated anchor agitators to prevent sedimentation. Belt silos enable continuous discharge via moving belts or push conveyor elements. Paddle silos work with rotating lump-breaking paddle arms. Vibration silos use targeted mechanical impulses to prevent bridging.
Moisture silos are indispensable when it comes to the safe handling, temporary storage and demand-oriented dosing of moist, non-free-flowing products. Their design contributes significantly to process stability. amixon develops tailor-made solutions for this purpose, which are precisely tailored to the product properties and operational requirements – whether as a simple buffer container or as an integral part of a complex process step such as mixing or drying.