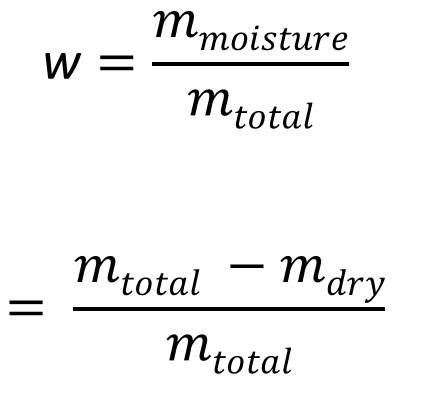
Moisture content
Moisture content of powders
The moisture content describes the proportion of liquid components in or on the solid particles of a powder. In most cases, this refers to the water content, but in principle the moisture content can also refer to other liquids or liquid mixtures such as oils, solvents or emulsions. These can either diffuse into the powder particles or adhere to their surface as a film or droplet.
Technically, the moisture content is usually defined as the mass percentage of the liquid in the total mass of the moist powder. It can be calculated by setting the difference between the total mass and the mass after complete drying in relation to the total mass. In process engineering, the moisture content is alternatively also specified in relation to the dry substance.
- w : Moisture content
mtotal : Mass of the wet powder
mdrym : Mass of the dry powder
mmoisture : Mass of the liquid
In practice, a distinction is made between adsorbed and absorbed moisture. Adsorbed moisture is located on the surface of the particles - typically in the form of physically bound water films or liquid residues. This form of moisture is comparatively easy to reverse: the moisture can be removed again by controlled drying or ventilation. In contrast, absorbed moisture has penetrated into the particle structure itself, for example through microscopically small pores. This moisture is much more difficult to remove and often requires longer or more intensive drying processes. The reversibility of moisture removal is therefore closely linked to the type of liquid binding - a crucial aspect in process design.
The moisture content of a powder influences numerous process-related and product-specific properties. The wetting behaviour of the particles plays a central role here. Hydrophilic powders such as milk powder or cellulose absorb water easily and bind it quickly to their surface. Hydrophobic powders such as talcum, paraffin or silicone-coated particles, on the other hand, have a low affinity for water. These differences are not only relevant for the behaviour during storage, but also when mixing with liquids or during the production of granulates.
Another important aspect is pourability. Even small amounts of moisture can significantly change the bulk material properties. Capillary liquid bridges create adhesion forces between the particles. This leads to agglomeration, lump formation or uncontrolled compaction - and thus to poorer flow behaviour. In industrial mixing or dosing processes, this can significantly impair process reliability.
Storage stability is also directly related to the moisture content. Dry powders generally have a longer shelf life, are less reactive and less sensitive to temperature fluctuations. Moisture, on the other hand, can promote microbial activity, accelerate chemical reactions or lead to agglomeration. Controlled storage under dry conditions is essential, especially for hygroscopic powders.
Moisture distribution plays a central role in the mixing technology used by amixon®:
- For the gentle wetting of powder mixtures.
- In vacuum mixed drying. Vacuum mix drying with amixon® is often the last process step of a synthesis stage. The aim is to obtain a dry, deagglomerated powder. This then serves as a template for the subsequent synthesis step.
- It should also be noted at this point that over-moistened powders can be made free-flowing with the help of anti-caking agents. It is important that the powdery "superabsorbents" quickly and gently coat the moist powder particles. This is where amixon mixers make an important contribution. They mix gently, quickly and with optimum precision. In this respect, extremely small quantities of anti-caking agents are sufficient.
In any case, the mixing system must be able to reliably control the changes in flow conditions that occur.