Precisionsmixer för smakämnen
Nuförtiden är den moderna produktionen av livsmedel knappast tänkbart utan användning av aromämnen. Ordet ”aroma” kommer från det grekiska och betyder krydda. Många smakämnen är resultatet av kemiska föreningar, som aromater, estrar, terpener, aldehyder, ketoner och andra basiska ämnen. Naturliga smakämnen finns i matråvaror eller skapas under bakning eller tilllagning. Naturidentiska arom har samma kemiska struktur som naturliga smakämnen, men produceras syntetiskt. Konstgjorda aromämnen förekommer däremot inte i naturen. Konstgjorda smakämnen kan ofta användas för att producera tilltalande smakegenskaper, som överskrider den naturliga smaken vad gäller genomslagskraft. Vissa smaker kan å andra sidan inte reproduceras tillfredsställande med konstgjorda smakämnen och måste erhållas från naturen.
En människa kan se, känna, höra, lukta och smaka med sina sensoriska organen. En aromatisk känsla är alltid kombinationen av smak och lukt. Smakintrycket uppstår, när man andas in genom gapet, medan man smakar. Aromastiska ämnen värms upp i svalget och når receptorerna i näshålan via den pharyngeal-nasala öppningen.
Tungan kan känna igen endast fem smaker – sur, söt, salt, besk och umami (buljongsmak). Umamismaken upptäcktes av den japanske forskaren Kikunae Ikeda år 1908. Den kan grovt översättas som ”hjärtlig” eller ”köttig”. Exempel på umamismak är till exempel parmesan, lasagne, pizza, sardiner, makrill och tonfisk. Bäraren av umamismaken är aminosyran glutaminsyra, som är särskilt rikligt förekommande i helt mogna tomater, kött, sojasås, ost och modersmjölk. Dess salter kallas glutamater. Receptorerna på den mänskliga nässlemhinnan uppfattar lite mer än 400 olika dofter. Tillsammans med denna luktuppfattning kan våra smaksensorer urskilja över 10.000 olika aromer och miljoner av doftämnen. Smakerna ”stark och pepprig” uppfattas å andra sidan inte i termer av smak, utan främst via smärtsensorer.
Aromtillverkare svarar på snabbt föränderliga utmaningar
Smaker skapas ständigt på nytt, som svar på konsumenternas förändrade smakpreferenser i olika kulturer och på olika kontinenter. Det gäller till exempel sockerfylld snabbmat som pulveriserade drycker, mjölk- och yoghurtdrycker, te, energidrycker, vingummi och annan godis. Flytande smakämnen och instantarom i form av pulversmaker används här.
Utmaningarna för smakprocessorn liknar mestadels de, som slutprocessorn för livsmedel har: man önskar att betjäna kunderna snabbt och uppfylla de regionala smakpreferenserna till punkt och pricka. Förutom god smak vill man också ta hänsyn till hållbarhetsaspekter av en hälsosam livsstil, som är så naturlig som möjlig. Närings- och njutningsmedel bör innehålla mindre salt, socker och fett samt bidra till en balanserad diet, helst utan smakförstärkare.
Med tanke på den snabbt växande världsbefolkningen och den växande medelklassen i tillväxtländerna, förväntas marknaden för färdigmat att öka. Här räknar man särskilt med dehydratiserad snabbmat. Baserat på kraven från marknaden, såsom innovationshastighet, närvaro, kvalitetssäkring och flexibilitet, har olika snabbprodukter och snabbmatsproducenter utvecklat sina egna, specifika ”unique selling points”.
Den koniska enaxlade blandaren AM från amixon® i tillverkning av aromer och dehydratiserade produkter
Innan den långa kedjan av snabbmatberedningen äntligen hamnar i konsumentens varukorg, måste varorna blandas, fyllas och levereras. Blandningsmetoden är särskilt avgörande för produktens kvalitet, eftersom den har ett avgörande inflytande på bulkmassans egenskaper, såsom homogenitet, naturligt utseende, flytbarhet, struktur och dammfrihet, såväl som upplöslighet och sjunkegenskaper under upplösning i olika vätskor.
Runt hela världen tillagas och färdigställs aromämnen samt livs- och njutningsmedel med hjälp av amixon®-precisionsmixer. Vi har ryktet av att vara särskilt flexibla, lätta att använda och att uppfylla kundernas grundläggande krav.
1. Idealisk blandningseffekt tack vare tredimensionellt totalflöde
Industriell blandning av pulverformiga ämnen sker mest i precisionsmixrar. I fallet med den här beskrivna mixern från amixon® blandas stapeln inuti blandningskammaren i form av ett lufttryckflöde. Blandningskammaren är en upprättstående kon med en cylinder ovanpå. Ett spiralblandningsverktyg, även känt som en skruvtransportör, roterar i mitten. Spiralen har en vinkel på ca 20°. Skruvtransportörerna är dimensionerade på ett sådant sätt, att nästan en femtedel av den totala blandningsvolymen transporteras med en rotationsrörelse av blandningsverktyget. Skruvtransportörerna samlar blandningen i periferin av blandningsreaktorn och transporterar den uppåt. När blandningen når toppen, flyter den nedåt i mitten av kammaren. Blandningseffekten sker huvudsakligen inom gränsområdena mellan de två makroflödena. Enkelt uttryckt kan processen beskrivas på följande sätt: den uppåtgående skruven i blandningarna tvingas fram av skruvtransportörerna, medan flödet nedåt sker naturligt genom tyngdkraften. I gränsområdet mellan dessa två sker förändringen av positionen inom partikelsystemet.
2. Skonsam homogenisering och intensiv behandling
a. Distribuerande blandning
Tack vare det dödutrymmesfria flödet, uppnår man redan efter ca 70 till 200 varv tekniskt idealiska blandningsegenskaper, som i praktiken inte går att förbättra. Den blandningsprocess, som sker här, kan defineras som ”distribuerande blandning” och den är särskilt skonsam och energieffektiv. Rotationshastigheten på blandverktygen (mätt inuti cylindern) är i allmänhet justerbar mellan 0,5 m/s och 2,5 m/s.
Tack vare designen kan idealiska blandningsegenskaper uppnås med en fyllnadsnivå på ca fem procent, eftersom flödeseffekten är densamma oavsett fyllningsnivå. amixon GmbH definierar typbeteckningen för sina mixer på grundval av netto- eller arbetsvolym. En mixer typ AM 3000 kan därför blanda lika bra satser på 150 liter som på 1.000 liter, i den mån det krävs en distribuerande (skonsamt fördelande) blandning.
b. Dispersiv (spridande) blandning
Ibland kräver dock användaren ytterligare bearbetningssteg, såsom avklumpning, spridning eller agglomerering. Här sker ytterligare skjuvnings- och tritureringseffekter med ökad energitillförsel. I amixon®-mixern uppnås detta å ena sidan genom att öka blandningsmekanismens rotationsfrekvens och å andra sidan genom att även använda skär- eller skjuvningsverktyg. Samma mixer tillhandahåller därför en särskilt mild homogenisator för skonsamt fördelade blandningar och en intensiv spridning vid dispersiv blandning.
3. Olika fyllningsgrader
Vid dispersiv (spridande) blandningar måste fyllningsnivån höjas, så att skjuvningsverktyget befinner sig ca 30 till 40 cm under fyllningsnivån. Beroende på storlek är minsta fyllningsnivå då ca 400 liter för AM 3000 och ca 600 liter för AM 6000.
4. Matning och utsläpp
Mixern matas med enskilda komponenter genom ett eller flera munstycken ovanför blandningskammaren, antingen i följd eller samtidigt. Mixern kan vara stillastående, om den fungerar som en doseringsvåg stående på lastceller, eller roterande, om den ena satsen efter den andra måste blandas snabbt och utan avbrott. Efter att blandningsprocessen är avslutat (efter ungefär två till sex minuter), öppnas en bottenventil utan dödutrymme och blandningen flödar nedåt genom ett munstycke i mixern. Utsläppsprocessen är fri från segregering och flödesvolymen bestäms av utsläppsventilens dimension. .
5. Blandningskammaren är utformat för att vara under- och övertryckbeständig
Det extra solida blandverktyget tillkopplas vanligtvis uppifrån och drivs endast ovanifrån. En särskilt hygienisk axeltätning garanterar en damm- och kontaminationsfri drift, även vid olika systemtryck inuti blandningskammaren. Till exempel kan det finnas ett vakuum, när blandningsmaterialet sugs in med hjälp av sugpneumatik. I speciella fall frigörs blandningskammaren från atmosfärisk syre innan den laddas med ett vakuum på ca 10 mbar absolut tryck. Blandningskammaren översvämmas sedan med kvävgas. Först därefter matas den med blandningarna. Under blandning och utsläpp upprätthålls ett lågt kväveövertryck på 50 till 100 mbar i blandningskammaren, för att hålla atmosfäriskt syre borta från materialet som ska blandas. I andra fall kan blandningskammaren matas med hjälp av pneumatiskt tryck. Även under övertrycksdrift förblir blandningskammaren gas- och dammtät. Detta gäller särskilt de komplexa konstruktionselementen, såsom axeltätning, bottentätningsbeslag och inspektionsdörrar.
6. Inspektion och rengöring
amixon® säkerställer en lätt åtkomst till blandningskammaren och fri utsikt över blandningsreaktorn genom de stora inspektionsdörrar. Detta gör att manuell torrtvätt kan utföras snabbt och säkert. Dörrarna har tillverkats enligt CleverCut®-metoden. O-ringtätningen, som är insatt i spåret, gör kammaren gas- och dammtät, eftersom den sluter till tätt intill produkten. Tätningen av dörrarna är även lämplig för automatisk våtrengöring, eftersom den tätar praktiskt taget utan dödutrymme. Fogar och kapillärer har till stor del undvikits helt. I detta avseende är den efterföljande torkningsprocessen också snabb och säker.
7. Hygien, grovhetsdimension i Ra valfritt 2 µm till 0,2 µm
Alla delar, som är i kontakt med slutprodukten, är svetsade utan fogar och kan alternativt slipas. Slipning och ytkvalitetet för de delar, som är i kontakt med slutprodukten, genomförs enligt respektive kundspecifikationer. Till och med en spegelliknande yta kan levereras, och i speciella fall är ytorna också elektrodpolerade. amixon® dokumenterar FDA-överensstämmelse för alla polymermaterial och implementerar alla nuvarande EHEDG-specifikationerna för både torr och våt drift.
8. Resttömning och automatisk våtrengöring
På grund av den koniska utformningen, tappas bulkmassan utan segregering, när blandningsverktygen roterar långsamt – konsekvent till den sista resten. I detta avseende är det lätt och smidigt för användaren att använda den allsidiga precisionsmixern. En våtrengöring kan också utföras automatiskt genom att spola alla komponenter, som kommer i kontakt med produkten med hjälp av roterande tvättlansar.
Testning och design
Varje fabriksanläggning har sin egen driftsfilosofi. I detta avseende är kraven på en processblandare alltid individuella. För att testa olika metoder har amixon® mer än 30 testmixrar på sju provanläggningen över hela världen och processingenjörerna har många års internationella marknadskunskap. Som en kontrakttillverkare implementerar amixon® kundens krav till punkt och pricka, med ett team på 130 anställda på den enda produktionsanläggningen i Paderborn, Tyskland.
Två mixrar tilldelas en påfyllningsslinje. Här blandas de kontinuerligt producerade råvarorna i spraytornet i satser och blandas, för att sedan packas oavbrutet igen. Satsstorlekarna är vanligtvis 300 till 1.200 kg. KoneSlid®-mixern har speciellt utvecklats för denna uppgift. Blandning och tömning tar högst 120 till 180 sekunder.
KoneSlid®-mixern uppnår idealisk blandningskvalitet vid låg rotationsfrekvens. Ofta behöver man inte heller förblandningar. Dessutom är blandningsmetoden extra skonsam. Praktiska erfarenheter på fältet bekräftar, att de mest känsliga agglomeraten från spraytornstorkning eller fluidiserad bäddgranulering eller vakuum-frystorkning, bevarar sin struktur nästan helt utan granulat.
Vid behov kan KoneSlid®-mixrar också göras vakuumbeständig. På det sättet kan atmosfäriskt syre avlägsnas från porösiteten i själva pulverblandningen under processen. Detta görs genom att tillföra ett vakuum. En mättnad uppnås genom att tillsätta kväve eller koldioxid. Utsläpp sker inom några få sekunder utan segregering. Fritt flytande blandmaterial flödar vanligtvis helt ut, så att korskontaminering inte är möjlig.
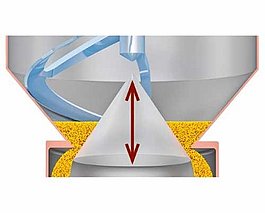
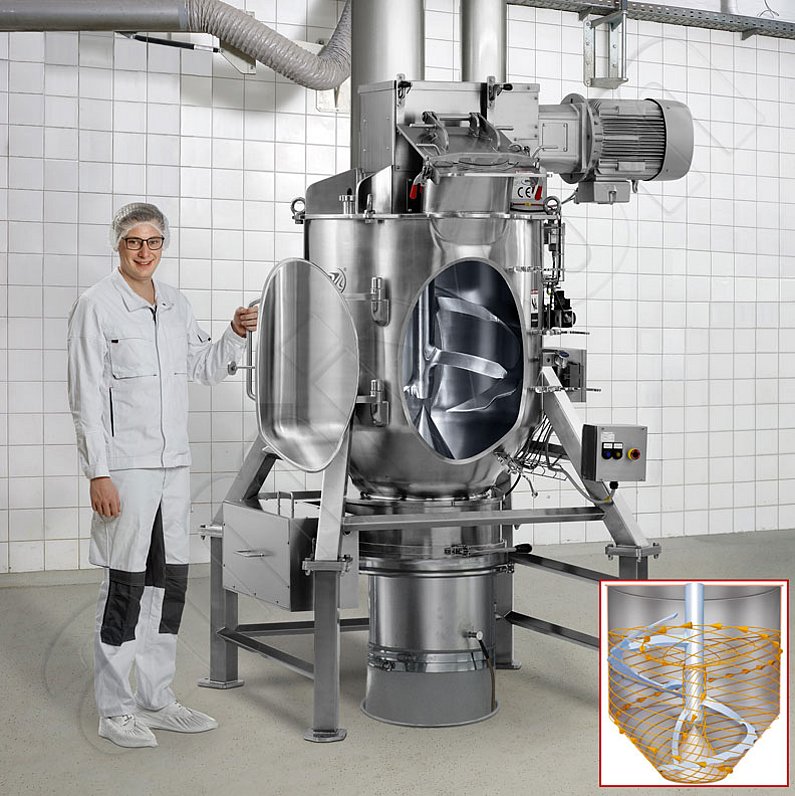
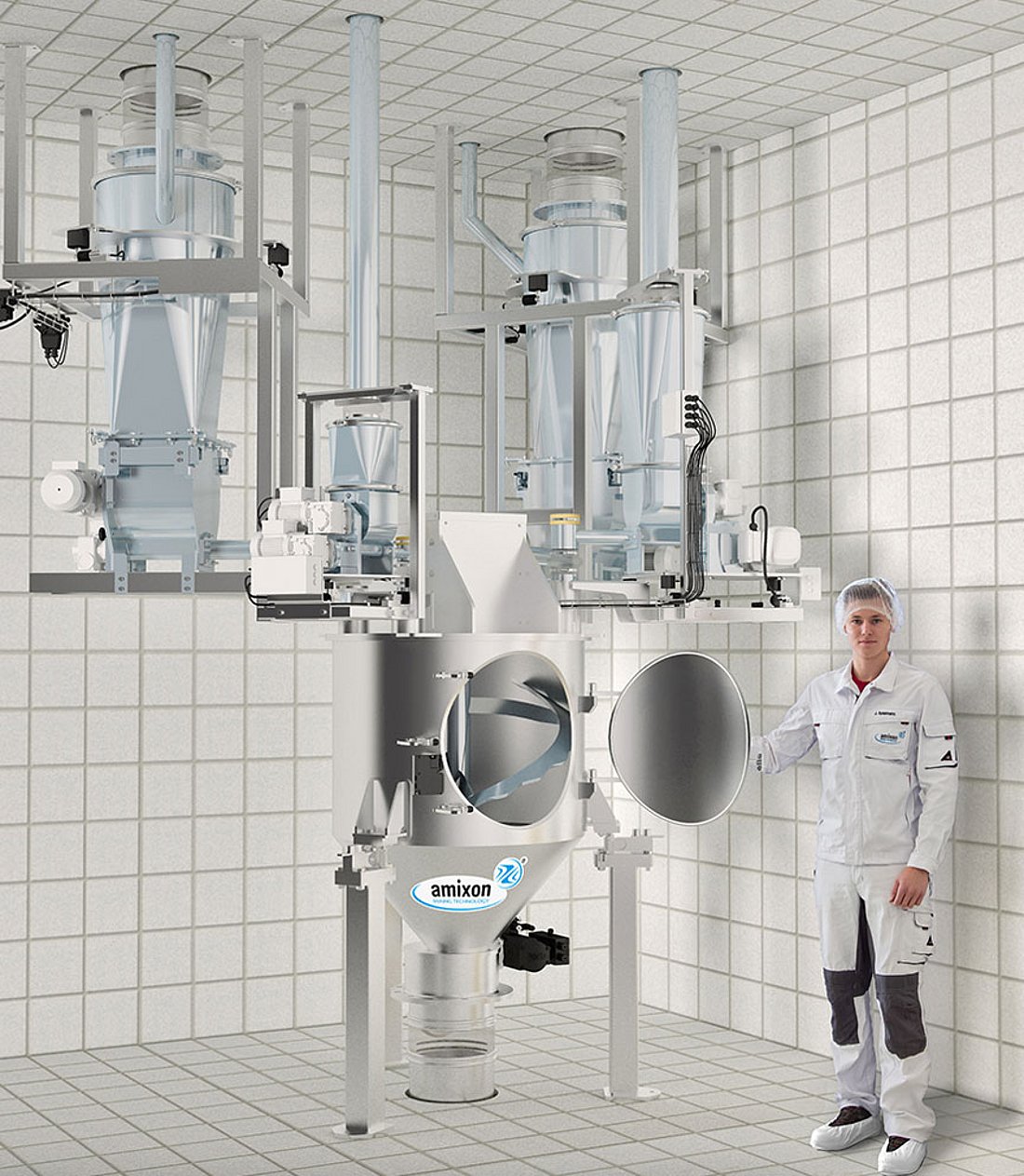
Påfyllningsnivån kan variera från ca 10 % till 100 %. Vid dammexplosivt material finns det en typundersökning Ex II 1D (för zon 20). Eventuellt kan mixern till och med göras lufttät eller hållfast mot tryckstötar.
De stora inspektionsdörrarna ger lätt åtkomst vid manuell torrtvätt. Dörrarna har tillverkats enligt CleverCut®-metoden. O-ringtätningen, som är insatt i spåret, gör kammaren gas- och dammtät, eftersom den sluter tätt intill produkten. Konstruktionen är permanent gas-, damm- och vattentät. Inspektionsdörrarna öppnas genom manuell manövrering av KwickKlamp®-slutaren. De elektromekaniska säkerhetsspärrarna tillåter inte att inspektionsdörrarna öppnas, förrän systemet har kopplats från elnätet.
amixon®-mixer i kontinuerlig produktion
En tredje typ av processmetod vid dehydratiserade näringsämnen, särskilt när halvfabrikat måste produceras i stora mängder och under långa tidsperioder, är kontinuerlig blandning. Detta ger mixern speciella fördelar.
amixon®-kontinuerlig mixer klarar denna uppgift utmärkt, genom att tillämpa principen om kontinuerligt värmepannsflöde. Alla komponenter som ingår i receptet doseras i mixern på ett gravimetriskt och kontrollerat sätt. Den färdiga blandningen tappas kontinuerligt ut. Följande omständighet är dock ett speciellt fall: när en konventionell kontinuerlig blandmaskin startas, överensstämmer produktflödet som lämnar mixern i början inte med receptet, eftersom efter att systemet har startat, måste matningshastigheten för de enskilda doseringsenheterna balanseras med varandra.
Eftersom amixon®-kontinuerlig mixer, som beskrivs här, också är en precisionsmixer, kan uppmätningsfasen för de enskilda doseringsenheterna korrigeras till 100 %. Tillvägagångssättet vid produktionsstart är enligt följande:
Mixerns utsläppsanordning är stängd. Alla gravimetriskt manövrerade doseringsenheter startas samtidigt med ett lågt massflöde och oscillerar automatiskt efter varandra. Påfyllningsnivån för mixern ökar kontinuerligt, varigenom mixern startar av sig själv vid halva påfyllningsmängden. Inkörningsprocessen är avslutad, när mixern är ungefär fylld till hälften. Utsläppsenheten öppnar långsamt efter att påfyllningsnivån är ca 80 % av den praktiskt användbara nettovolymen. Denna nivå hålls konstant. Doseringsflödena ökas under konstant avstämning – upp till det maximala massflödet. När produktionen är klar, är proceduren enligt följande: alla doseringsenheter fördröjer successivt massflödet och stängs sedan av och låses samtidigt. Mixern töms kontinuerligt, tills det inte rester. Fritt flytande varor flödar helt ut.
Varje gram av de använda komponenterna blir således en försäljningsklar produkt. Denna kontinuerliga mixer fungerar enligt principen om ”värmepannsflöde”. I detta avseende förekommer det en bred fördelning av uppehållstiden. Mixern är mycket bra på att kompensera för mindre, kortsiktiga fluktuationer i doseringen. Mixern kan också tömma fritt flytande varor nästan helt och hållet. Även här möjliggör de stora CleverCut®-inspektionsdörrar en ergonomisk inspektion och rengöring.
Ur användarens synvinkel är följande fördelar värda att nämnas:
- Blandningsprocessen är även här extra skonsam och den genomsnittliga uppehållstiden kan väljas över ett brett intervall baserat på påfyllningsnivån. Det förekommer ingen produktförlust vid produktionsstart och -slut.
- Samma mixer kan användas som en precisionsmixer från ca 15% till 100% av nettovolymen – till exempel som en mixer till förblandningar.
- Med hög tömningsgrad tack vare SinConvex®-blandverktyg
- Är särskilt smidig att använda
- Med högsta hygienstandard och flera stora CleverCut®-inspektionsdörrar
- Lämpar sig för att installeras nedströms från ett kontinuerligt transportsystem såsom ett spraytorn. Kan på begäran fås med typundersökning Ex II 1D (för zon 20).