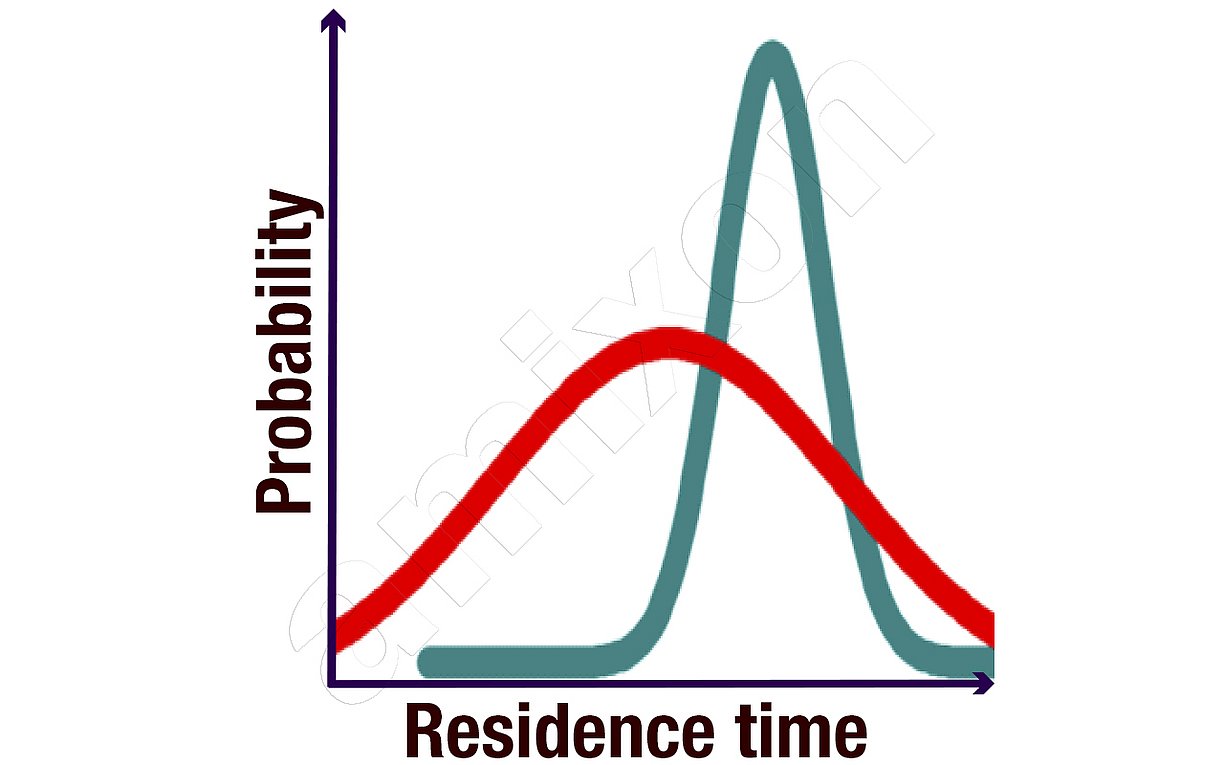
Die rote Linie beschreibt die Verweildauer der Mischgüter während einer kontinuierlichen Kesselströmung. Die grüne Linie beschreibt die Verweildauer der Mischgüter während einer Rohrströmung.
Kontinuierliches Mischen von Pulvern: Rohrströmung versus Kesselströmung
Das Mischen und Benetzen pulvriger Gütern geschieht in der Industrie entweder chargenweise oder kontinuierlich.
Das Mischen von Schüttgütern erfolgt in der Industrie chargenweise oder kontinuierlich. Mischen" steht hier als Oberbegriff für eine Vielzahl begleitender Verfahren wie Desagglomerieren, Zerkleinern, Einfärben, Entklumpen, Ummanteln, Flüssigkeitsbenetzen, Agglomerieren, Temperieren, Mischtrocknen, Synthesereaktion, Bondern, ....
Bitte lesen Sie auch unseren Blogbeitrag: „Kontinuierlich mischen versus chargenmischen“!
Bei der kontinuierlichen Schüttgutvermischung/Pulveraufbereitung unterscheidet man zwischen der Rohrströmung und der Kesselströmung. In der Praxis gibt es auch Mischformen beider Verfahren.
Rohrströmung
Erfolgt die Vermischung in Form der Rohrströmung, dann werden die kontinuierlich eingetragenen Komponenten von rechts nach links gefördert. Mischwerkzeuge fördern, mischen und verwirbeln die Mischgüter. Hier gilt das Prinzip „first-in-first-out“. Der Mischeffekt wird intensiviert, wenn einzelne Werkzeuge gegen die Fließrichtung fördern. Dort liegt dann ein erhöhter Füllgrad vor. Je mehr Rückförderung stattfindet, desto länger ist die Verweildauer. Vermehrte Rückförderung bedingt auch eine erhöhte Energieeintragung.
Kesselströmung
Im Fall der kontinuierlichen Kesselströmung wird die Hauptströmungsrichtung von der Gravitation bestimmt. Ein Helixmischwerkzeug verteilt die Mischgüter besonders effektiv indem es aufwärts fördert. Bereits nach acht Umdrehungen liegt schon eine sehr hohe Mischgüte vor. Die Rohstoffkomponenten werden von oben kontinuierlich in den Mischraum dosiert und fließen in das total homogenisierte Mischgutbett. Nach dem Zufallsprinzip werden sie im Mischraum verteilt. Im Mischraum wird ein konstanter Füllgrad eingestellt. Der kann beispielsweise zwischen 40 % und 80 % betragen.
Kesselströmung bedeutet in diesem Zusammenhang, dass im Mischraum nahezu alle Komponenten homogenisiert vorliegen. Kontinuierlich fließen Rohstoffkomponenten hinzu. Sie werden im richtigen Mengenverhältnis hinzu dosiert und ihr Volumenstrom ist vergleichsweise klein. Die Mischeffizienz ist so bemessen, dass sie nach wenigen Sekunden im Mischraum homogenisiert sind.
Frage eines Kunden: Welche Art des kontinuierlichen Mischens ist denn in der schüttgutverarbeitenden Industrie zu bevorzugen: die Rohrströmung oder die Kesselströmung?
Antwort von amixon®: Es gibt auf diese Frage keine generelle Antwort. Beide Systeme haben spezifische Vorzüge. Es kommt immer auf den jeweiligen Anwendungsfall an.
Die Rohrströmung ist der Kesselströmung immer dann vorzuziehen:
- wenn der Aufbereitungsvorgang zeitkritisch ist, wie beispielsweise schnelles Temperieren, Aufbaugranulieren, Ummanteln, oder wenn Komponenten spontan chemisch reagieren sollen…
- wenn Stoffe schwer mischbar sind, insbesondere, wenn während des Mischens intensiv desagglomeriert werden muss
- wenn Flüssigadditive hochviskos oder auch anhaftend sind
- wenn wenig vertikaler Bauraum verfügbar ist
- wenn Additive zeitlich nacheinander einzumischen sind … entlang des Mischraumes. - Das kann der Fall sein, wenn die Mischgut-Partikel mit verschiedenen Stoffen nacheinander ummantelt werden sollen
- ………
Die Kesselströmung ist der Rohrströmung dann vorzuziehen:
- wenn Anfahrverluste beim Start der Mischanlage vermieden werden sollen. Bereits die ersten Gramm des gemischten Gutes sollen spezifikationsgemäß homogen sein.
- wenn der Mischer kurzzeitig auftretende Dosierfehler bestmöglich kompensieren soll
- wenn der Mischvorgang besonders schonend stattfinden soll
- wenn ein breites Verweilzeitspektrum gewünscht ist
- wenn derselbe Mischer sowohl große, als auch sehr kleine Volumenströme homogenisieren soll
- wenn derselbe Mischer auch als Präzisions-Chargenmischer dienen soll. Beispielweise kann derselbe amixon® Konusmischer aus vielen Kleinkomponenten eine Vormischung herstellen. Diese Vormischung wird im selben Mischer später mit anderen Komponenten kontinuierlich vermischt.
- ........
Die amixon GmbH kann die oben dargestellten kontinuierlichen Mischverfahren komfortabel für Sie durchführen. Besuchen Sie uns mit Ihren Produkten in unserem Technikum in Paderborn. Wir demonstrieren Ihnen gerne die Mischverfahren!
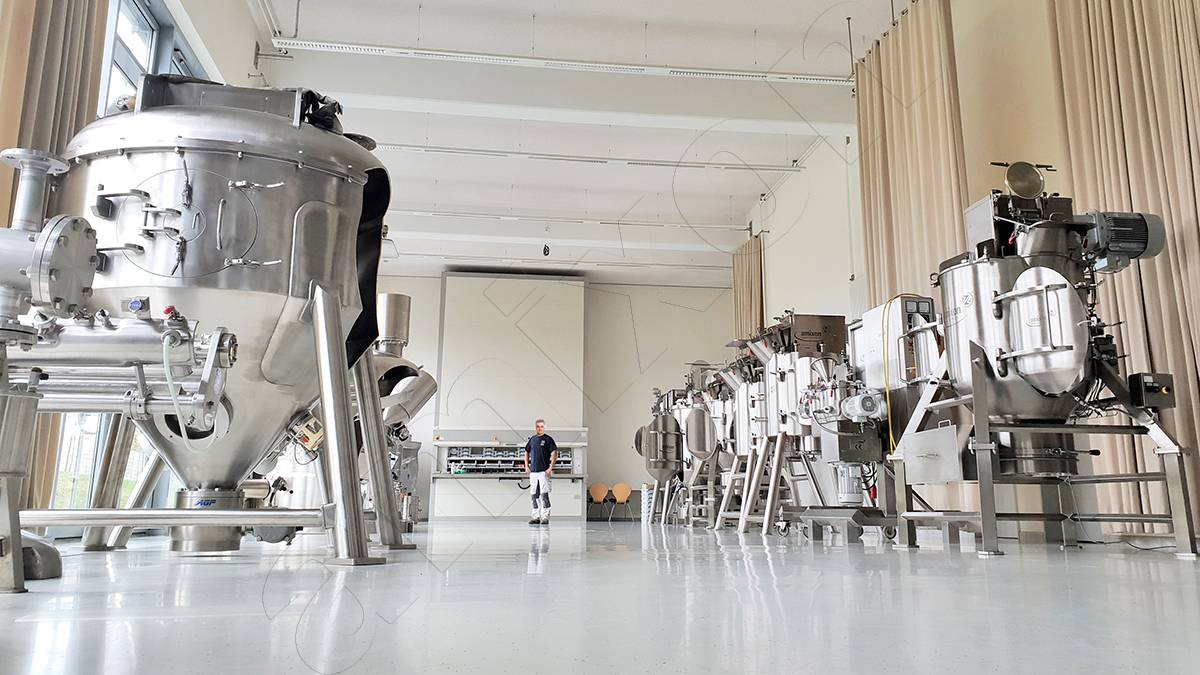
© Copyright by amixon GmbH