Mélangeur optimal d’aliments pour bovins, volaille, porcins & Cie
Les aliments pour animaux de rente doivent répondre à des critères de qualité élevés : ils doivent notamment être purs. Ils doivent être déclarés et traçables. Les aliments doivent contenir exactement les nutriments dont l'animal à l'engrais a besoin dans la phase de croissance correspondante.
La forme de présentation est également importante : les aliments doivent être fluides et exempts de poussière. Ce n'est qu'à cette condition qu'ils peuvent être utilisés dans des systèmes d'alimentation automatiques.
- Les aliments concentrés pour vaches laitières doivent par exemple contenir une forte proportion de fibres brutes afin de garantir une bonne digestibilité et une faible formation de méthane.
- Les aliments concentrés pour porcs doivent contenir peu de phosphore, mais les bons acides aminés.
- Les aliments concentrés pour volailles doivent contenir certaines enzymes et des protéines bien digestibles.
Les mélangeurs amixon® garantissent une qualité de mélange optimale et une vidange complète
La multitude de composants et les recettes en constante évolution exigent des performances logistiques maximales de la part des fabricants d'aliments pour animaux. Les composants de matières premières dont le prix journalier semble inapproprié ou qui ne sont pas disponibles sur le marché doivent souvent être remplacés par d'autres ayant une teneur en nutriments comparable.
L'exigence imposée au mélangeur en tant qu'installation à valeur ajoutée dans la chaîne de production est donc la suivante : obtenir des qualités de mélange idéales, impossibles à améliorer dans la pratique. Et tout cela
- en peu de temps et
- avec des taux de remplissage variables
- avec un apport énergétique minimal et
- une résistance à l'usure optimale
- vidange rapide et complète en quelques secondes
- longue durée de vie
- bonne accessibilité et nettoyage facile de la chambre de malaxage
- accessibilité ergonomique de la chambre de malaxage
- réparation facile des composants usés - de préférence par des serruriers internes spécialement formés à cet effet.
«Dans la pratique, la qualité du mélange est synonyme d'homogénéité. Elle décrit la capacité d'une installation de mélange à «mélanger de manière homogène différentes quantités de composants individuels dans un temps défini».
Déterminer la qualité du mélange d'un produit en vrac hétérogène est un défi complexe en matière de technologie des procédés. Il existe plus de 20 formules différentes pour définir la qualité du mélange. Pour vérifier la qualité du mélange dans les aliments pour animaux, des méthodes pratiques ont été mises au point. Des colorants alimentaires organiques ou des microtraceurs sont ajoutés à l'aliment dans un rapport de 1:100 000, ce qui correspond à 100 grammes de substance active par tonne. Après un temps de mélange défini, un nombre suffisant d'échantillons (en général au moins dix) d'un volume suffisant (souvent 20 g) sont prélevés à différents endroits de la salle de mélange à l'aide d'un échantillonneur et analysés. La qualité de l'analyse de la qualité du mélange dépend de nombreux paramètres, mais surtout du nombre d'échantillons et du volume d'échantillon choisi. Il est particulièrement important de diviser ou de répartir les échantillons de manière à éviter toute ségrégation.
Évaluation de la route de processus pour les nouveaux types de produits
Des situations difficiles surviennent parfois lorsqu'un type de produit ou un processus entièrement nouveau doit être établi ou lorsqu'un nouveau mélangeur est mis en service. L'entreprise de production d'aliments composés souhaite alors savoir comment l'homogénéité se développe pendant le temps de mélange et combien de temps elle doit mélanger pour obtenir une qualité de mélange suffisamment élevée. Pour le savoir, on peut procéder comme suit : l'échantillonnage est répété après de courtes périodes de mélange supplémentaires, comme décrit ci-dessus. Par exemple, les dix premiers échantillons sont prélevés après environ 180 secondes, les dix seconds après 30 secondes de mélange supplémentaires, etc.
Dans le cas d'un mélangeur ayant fait l'objet de tests approfondis, son efficacité de mélange universelle est considérée comme validée. Il suffit donc de prélever les échantillons pendant la rotation de l'outil de mélange à l'aide d'un échantillonneur sans espace mort. Cela s'applique également aux échantillons de réserve.
La distribution granulométrique joue également un rôle dans l'obtention d'une qualité de mélange élevée. L'expérience a montré que l'homogénéisation des petits composants dans le matériau de base est plus efficace lorsque la taille des particules est comprise entre 200 et 500 micromètres. Si les particules sont beaucoup plus petites, elles sont plus difficiles à doser et à contrôler, peuvent pénétrer accidentellement dans les filtres de dépoussiérage ou se fixer par hasard sur des particules plus grosses et rendre ainsi difficile une répartition uniforme.
Les poudres de lait de remplacement pour veaux sont enrichies en matières grasses et en nutriments
Lorsque les veaux sont séparés de leur mère à un âge avancé, la mamelle de la vache n'est plus disponible pour l'alimentation. Des dérivés spéciaux du lait en poudre sont enrichis en matières grasses, oligo-éléments et vitamines. Le mélange prêt à l'emploi est conditionné dans de petits récipients. Selon les besoins, la marchandise est ensuite mise en suspension ou dissoute dans l'eau et est particulièrement nutritive pour le jeune animal.
Dans le mélangeur à double arbre amixon®, 3 m³ d'aliment d'allaitement pour veaux sont enrichis de grandes quantités de graisse. Néanmoins, le mélange fini s'écoule librement. Le robinet de vidange est particulièrement grand pour une vidange rapide et complète.
Prévention des contaminations croisées lors du mélange des lots
La pureté des lots est une exigence extrêmement importante pour les mélanges de précision dans l'alimentation animale. Par exemple, les micro-ingrédients actifs qui sont bons pour les vaches peuvent être nocifs pour la volaille. Il est donc essentiel de prouver que les contaminations croisées sont suffisamment évitées. Le contrôle est effectué de la même manière que le contrôle de la qualité du mélange. Après un lot de mélange régulier, un autre lot est mélangé sans substance active. Aucune substance active ne doit être trouvée lors de l'examen de ce lot « 0 ». L'examen peut être effectué spécifiquement pour le mélangeur ou pour l'ensemble de l'installation : balance de dosage, organes de transport, silo de collecte, broyeur, etc.
L'exigence d'une production sans contamination ne peut être satisfaite que si le mélangeur mélange rapidement et précisément. Il doit également se vider rapidement et complètement. amixon® a développé un mélangeur de précision appelé KoneSlid®. Il mélange en quelques secondes et se vide tout aussi rapidement. Les mélangeurs KoneSlid® sont économiques et résistants à l'usure.
amixon® fabrique des mélangeurs de précision, des réacteurs, des mélangeurs-sécheurs sous vide et des fermenteurs
Un outil de mélange hélicoïdal tourne à l'intérieur d'un récipient de mélange cylindro-conique. L'outil de mélange SinConcave® est entraîné et logé au centre, en haut. L'alimentation en produit à mélanger se fait par le haut, le vidage de l'appareil amixon® se fait en dessous de la chambre de mélange. Un organe d'arrêt sans espace mort s'ouvre dans le cône de la chambre de mélange. Toutes les pièces en contact avec le produit sont soigneusement soudées et polies, de même que l'outil de mélange. Des bras en forme de pales portent la spirale de mélange (modèle SinConcave®).
En option, l'outil de mélange peut être entièrement chauffé, l'arbre de mélange, les bras et la spirale de mélange sont alors à double paroi. Le fluide thermique tempère l'ensemble de l'outil de mélange. La vapeur, l'eau ou l'huile thermique peuvent être utilisées comme fluide caloporteur.
L'outil de mélange génère un flux total sans zone morte. Il est parfois nécessaire de désagglomérer ou de répartir efficacement des additifs liquides dans la poudre. On utilise alors des outils de broyage ou des lames HighShear qui libèrent partiellement une densité de puissance élevée dans la poudre. Peu importe que les produits soient granuleux, poussiéreux, fibreux, secs, humides, pâteux, liquides, fluides ou non. L'outil de mélange est conçu de telle sorte qu'il fait circuler une fois tout le contenu après environ quatre à cinq tours. Ce principe de circulation est également appelé circulation en cuve. En règle générale, après quelques tours, tous les composants sont répartis de manière homogène dans l'ensemble de la chambre de mélange et on parle d'une qualité de mélange idéale qui ne peut plus être améliorée dans la pratique.
La vanne de décharge sans zone morte peut également être remplacée par un organe de transport horizontal. Les convoyeurs horizontaux sont toujours utiles lorsque le déchargement du produit doit être dosé.
Les fermenteurs/réacteurs amixon® peuvent être utilisés
- lorsqu'un produit organique doit être stérilisé à la vapeur saturée
- lors de la fabrication de pénicillines ou
- lorsqu'une fermentation enzymatique doit avoir lieu
- lorsqu'un séchage sous vide particulièrement doux doit avoir lieu
- lorsque des produits en vrac poreux (granulés extrudés) doivent être imprégnés en profondeur de liquides à haute viscosité. (L'application du vide permet de débarrasser les pores de tout gaz. L'augmentation de pression qui s'ensuit stabilise l'imprégnation).
Les aliments concentrés représentent jusqu'à 14 % de l'alimentation des animaux de rente
L'époque où les agriculteurs nourrissaient leurs bovins et leurs porcs exclusivement avec de l'herbe, du foin, des céréales, des betteraves et de l'ensilage produits par leurs propres soins est révolue depuis longtemps. Aujourd'hui, les aliments pour animaux produits par les exploitations agricoles ne servent plus que de « fourrage de base ». En outre, les « aliments concentrés » sont indispensables. Ce terme désigne tous les aliments pour animaux à forte concentration en nutriments et autres additifs. On distingue ici les aliments simples et les aliments composés. Les aliments simples à forte concentration en nutriments sont par exemple les graisses, le tourteau de soja et la mélasse, un sous-produit de la transformation de la betterave sucrière.
Un aliment composé est un mélange de deux aliments simples. Mais les aliments composés modernes sont en réalité des composés très complexes, qui se composent de plusieurs aliments simples et d'additifs sélectionnés, et qui couvrent ainsi individuellement les besoins nutritionnels spécifiques et actuels des différents animaux. Un aliment composé typique se compose aujourd'hui en moyenne de huit à douze aliments simples et jusqu'à 15 additifs. Les principales matières premières sont les différentes céréales telles que le blé, l'orge et le maïs, suivies du colza et du soja. Les additifs alimentaires sont des minéraux, des vitamines, des acides aminés, des oligo-éléments et des enzymes.
Selon les chiffres actuels de l'Association des agriculteurs allemands, les mélanges d'aliments représentent environ 14 % de l'alimentation des animaux de rente en Allemagne. 54 % sont des aliments de base et 32 % des aliments simples. En 2020, selon l'Association allemande des aliments pour animaux, l'industrie des aliments pour animaux a produit 24,1 millions de tonnes d'aliments composés, dont 9,8 millions de tonnes pour les porcs, 6,9 millions de tonnes pour les bovins et 6,4 millions de tonnes pour la volaille.
L'industrie allemande des aliments pour animaux est caractérisée par des entreprises de taille moyenne. Fin 2020, on comptait 287 fabricants d'aliments composés pour animaux, qui ont réalisé un chiffre d'affaires de 6,8 milliards d'euros. L'industrie est concentrée dans le nord de l'Allemagne. Dans le sud, la demande d'aliments composés pour animaux est plus faible, car le cheptel y est moins important.
La tendance aux mélanges fourragers individuels
Même si le secteur est marqué par des moyennes entreprises, le développement des recettes d’aliments composés témoigne d’un grand engagement scientifique. À cet égard, on ne distingue pas uniquement les espèces animales, mais également l’affectation, le stade de développement et le rendement des animaux. Il convient également de tenir compte des différents besoins alimentaires, systèmes digestifs et métabolismes. Les aliments doivent également plaire aux animaux et ils doivent être transférés depuis la citerne du camion au silo journalier avant d’être distribués sans ségrégation à chaque animal. Il n’est ainsi pas rare qu’un seul producteur propose plusieurs centaines de recettes et formulations d’aliments composés différentes.
Dans l’élevage bovin, on trouve des mélanges sur mesure spécifiques pour les veaux, les génisses, les vaches laitières, les taureaux d’engraissement et les vaches taries (phase entre deux vêlages). Les exigences pour les taureaux d’engraissement par ex. sont comme suit : prise de poids journalière élevée, beaucoup de viande maigre et peu de graisse, un estomac bovin sain et peu de refus dus à la maladie. La ration de base se caractérise toutefois par une faible teneur en protéines pour un développement musculaire rapide. De même, les minéraux, les vitamines et les oligoéléments sont trop peu présents dans la ration de base. Un aliment composé sur mesure pour les taureaux d’engraissement permet de compenser ces manques.
Les agriculteurs modernes font tout d’abord analyser la ration de base qu’ils produisent eux-mêmes. Cette analyse permet de déterminer précisément la teneur en nutriments (glucides, graisses et protéines), en minéraux (calcium, sodium, magnésium, etc.) et en oligoéléments (zinc, cuivre, iode, etc.). La composition de l’aliment composé est ensuite minutieusement adaptée à la ration de base.
Cette analyse de la ration de base représente certes un certain coût initial, mais celui-ci est souvent rapidement compensé par l’alimentation spécifique qui contribue à la rentabilité de l’élevage bovin. En effet, tous les minéraux et oligoéléments - ne devant plus être compris dans l’aliment composé - constituent un véritable facteur de coût.
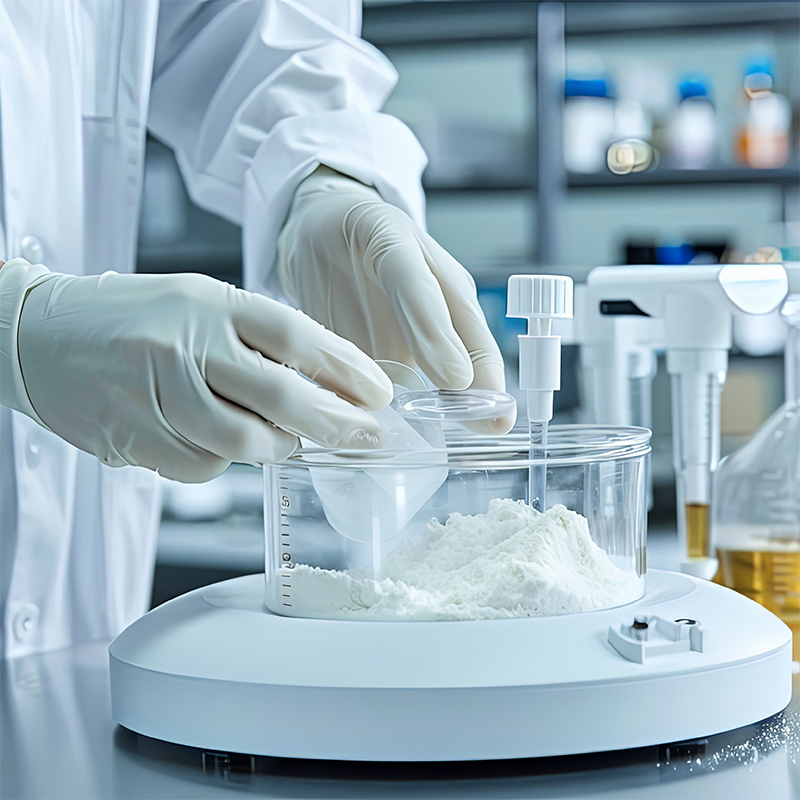
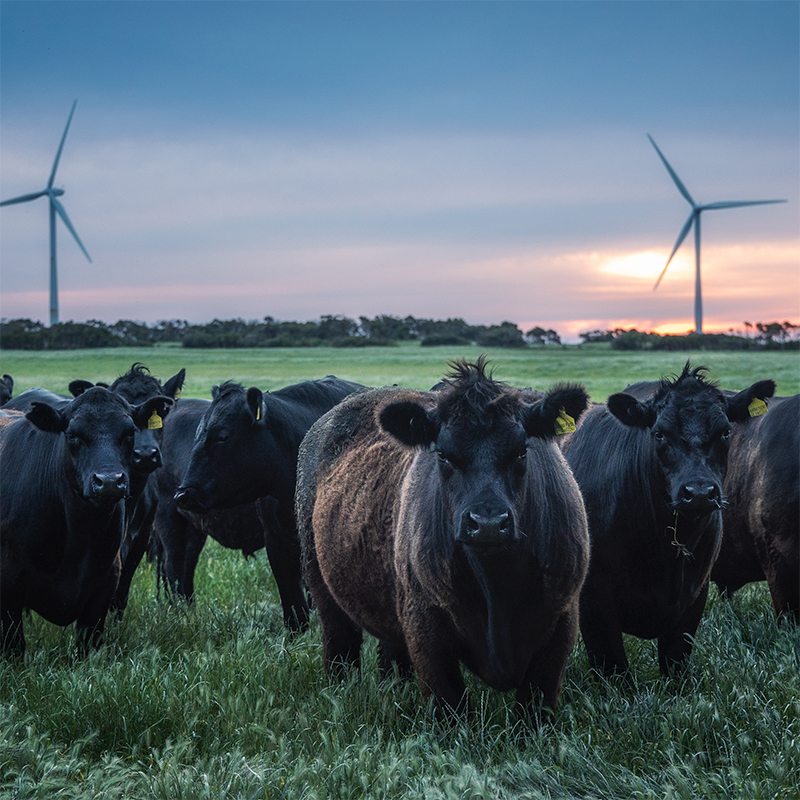
Une alimentation parfaitement adaptée pour le bien-être des animaux et la protection de l'environnement
Une production d'aliments pour animaux flexible et adaptée permet également de s'adapter à des conditions météorologiques extrêmes. Par exemple, les vaches laitières peuvent souffrir de stress thermique pendant les journées d'été. Dès que la température extérieure atteint 24 °C, le bien-être des animaux diminue, ils mangent moins et finissent par produire moins de lait. Lors d'une vague de chaleur estivale, l'ajout de carbonate de sodium à l'alimentation des vaches est utile.
Un mélange de fourrage finement ajusté peut même contribuer à la protection de l'environnement. Pour obtenir des rendements élevés, il est impératif de fertiliser régulièrement les terres agricoles. Le lisier, s'il est épandu correctement et avec modération, est en principe un bon engrais. Mais il ne faut pas en abuser. Parfois, les apports de phosphate et d'azote qu'il contient contaminent notre eau potable. Les vaches laitières ont besoin d'un apport suffisant en phosphore. Une carence en phosphore entraîne une diminution de la consommation de fourrage, de la production laitière et de la fertilité. En cas d'apport excessif en phosphore, la vache laitière réagit par une augmentation de l'excrétion de phosphate. Des compositions de composants judicieusement équilibrées déterminent donc également la qualité du lisier en tant qu'engrais et contribuent à protéger à la fois les terres arables et les eaux souterraines. Le fabricant d'aliments pour animaux Agravis propose par exemple un outil de calcul de rations appelé «Phokus», qui permet de réduire de manière ciblée la teneur en phosphore des aliments pour animaux.
Lisez ici quelques déclarations de différents propriétaires de moyennes entreprises d'aliments pour animaux.
Développement de recettes et de processus
Lors du mélange des aliments pour animaux, il est essentiel que les différents composants soient répartis de manière homogène. En effet, chaque animal ne reçoit qu'une fraction minime d'un lot. Et dans l'idéal, cette fraction devrait avoir exactement la même composition pour chaque animal d'une exploitation. Cela vaut également pour chaque ration alimentaire, même si certains oligo-éléments n'ont été ajoutés qu'en très petite quantité. Les mélangeurs d'aliments pour animaux doivent être capables de répartir uniformément de très petites quantités dans les céréales moulues. Dans le secteur, l'exigence de composition quantitative est formulée de 1 pour 10 000 à 1 pour 100 000. Il s'agit d'une exigence, en aucun cas d'une mesure de qualité de mélange.
Les aliments pour animaux sont des produits de masse, et les fabricants d'aliments pour animaux les produisent avec des marges bénéficiaires très faibles. À cet égard, une exigence supplémentaire est que le temps de séjour des produits mélangés dans le mélangeur - et même dans l'usine - doit être aussi court que possible. Il n'est pas rare que la durée d'un lot de mélange ne dure que quatre à six minutes. Pendant ce temps, le mélangeur est alimenté avec tous les composants nécessaires à la recette, le mélange est effectué, le mélangeur est vidé et le dispositif de vidange est fermé. Un cycle de mélange aussi court pour un mélangeur de 12 m³ nécessite des caractéristiques spécifiques.
L'interaction entre le développement de la recette, la mise à disposition des composants, le pesage des composants, l'homogénéisation du mélangeur et la capacité d'absorption des unités suivantes nécessite un grand savoir-faire de la part de l'exploitant. Enfin, le bilan énergétique doit également être correct. Chaque unité de la logistique interne des produits en vrac et de la préparation des produits doit être alimentée en énergie électrique. Elle est soumise à l'usure et augmente le prix des aliments composés.
Le choix d'un mélangeur adapté
L'homogénéité d'un mélange est souvent décrite par le coefficient de variation (CV) :
CV = (σ / μ) × 100 %.
- σ = écart-type de la concentration d'un composant
- μ = valeur moyenne de la concentration d'une fraction de composant
Dans la pratique, une qualité de mélange idéale peut être définie comme suit : on utilise un mélangeur de précision qui convient le mieux possible. Ce mélangeur atteint un coefficient de variation CV aussi faible que possible.
L'homogénéité obtenue avec ce mélangeur de précision ne peut plus être améliorée dans la pratique. Pour de nombreux mélanges de poudres, une valeur cible CV < 5 % peut être atteinte.
Plus la composition des poudres est hétérogène, plus la qualité du mélange obtenu est mauvaise. L'échantillon de mélange à analyser doit représenter une fraction de la portion utilisée par l'utilisateur final.
Les mélangeurs de précision – avec outils de mélange tournant à l’horizontale ou à la verticale – satisfont pleinement aux critères de qualité du mélange pour les aliments pour animaux. Les différences majeures résident toutefois dans
- la durée de mélange,
- la flexibilité du niveau de remplissage,
- le degré de vidange,
- la facilité de nettoyage / d’accès,
- la vitesse de vidange ainsi que
- la puissance absorbée de l’entraînement.
Pour choisir un système de mélange adéquat, il faut concilier l’encombrement du mélangeur avec la place disponible in situ. amixon® peut adapter individuellement ses mélangeurs ; une configuration plus basse avec le modèle plat ou une configuration mince lorsque la surface de montage est plus petite. En outre, amixon® peut fabriquer toutes les tailles souhaitées par pas de 100 litres. Pour le reste, les critères susnommés « Exigences posées aux mélangeurs » sont d’application. Les volumes de charge usuels au sein de l’industrie des aliments pour animaux vont de deux à six tonnes (env. 4 à 12 m³) et de une à trois tonnes (env. 1 à 3 m³) pour les mélanges minéraux.
Facteurs pour une humidification de poudre fonctionnelle dans le processus de mélange
Dosage précis et répartition homogène des liquides
Les mélanges d'aliments pour animaux contiennent également différents additifs liquides tels que des graisses, de l'eau, des acides aminés, de la mélasse ou des vitamines, en quantité suffisante pour répondre aux besoins des animaux de rente. En outre, ils ont pour but de lier les particules de poussière et d'améliorer le goût.
En règle générale, les aliments en poudre ne sont enrichis que de petites quantités de liquides. Si des adjonctions de liquides sont nécessaires, il est important que le mélangeur humidifie toutes les particules de manière homogène.
Il est intéressant de noter que la porosité du matériau augmente légèrement lorsque la quantité de liquide ajoutée est faible. Le matériau devient plus meuble et plus fluide, le volume du mélange augmente légèrement, la teneur en poussière diminue et la fluidité s'améliore légèrement. Mais il n'est pas facile de mouiller rapidement et uniformément un tas de matériaux avec une large répartition granulométrique.
Un post-traitement sous le mélangeur peut réduire la durée du processus
Si les temps de cycle sélectionnés sont très courts, les additifs liquides doivent être refoulés tout aussi rapidement dans le mélangeur. Suite à une brève durée de mélange, le mélangeur double rotor amixon® fournit un produit homogène. Ce dernier peut toutefois encore contenir ici et là des agglomérats (diamètre de 2 à 5 mm). Ces agglomérats humides sont certes distribués uniformément dans toute la chambre de mélange, mais pas entièrement dispersés dans l’aliment composé. Il faudrait encore prolonger le processus de mélange pour garantir leur distribution intégrale avec les rotors de coupe à grande vitesse, bien que la qualité du mélange soit atteinte. La méthode du post-traitement permet ici d’économiser l’énergie.
Pour broyer complètement les agglomérats, il est utile d’installer un « finisher » sous le mélangeur. Le produit mélangé traverse continuellement le finisher à haute vitesse. L’apport d’énergie spécifique est minime. Il est alors possible de démontrer que tous les liquides sont distribués dans la composition correcte jusque dans le plus petit volume.
amixon® est synonyme de mélangeurs de précision avec des arbres de mélange montés verticalement
Un outil de mélange hélicoïdal tourne à l'intérieur d'un récipient de mélange cylindrique. Il est entraîné et logé au centre, exclusivement en haut. L'alimentation des produits à mélanger se fait par le haut, le vidage du mélangeur se fait par le bas, par l'ouverture d'un clapet qui se ferme de manière coplanaire avec le plan du fond de la chambre de mélange. Il s'agit d'un clapet de fermeture sans espace mort, qui est ouvert et fermé par voie électropneumatique à l'intérieur d'un raccord. Tous les composants en contact avec le produit sont soigneusement soudés et polis, tout comme l'outil de mélange. Des bras en forme de pelle portent l'hélice de mélange, qui est ici fabriquée en « forme concave ».
L'outil de mélange peut être entièrement chauffé, auquel cas l'arbre de mélange, les bras et la spirale de mélange sont tous deux à double paroi. Le fluide thermique tempère l'ensemble de l'outil de mélange. La vapeur, l'eau ou l'huile thermique peuvent être utilisées comme fluides thermiques. L'outil de mélange crée un flux total qui domine l'espace sans laisser de zones mortes. Il est parfois nécessaire de désagglomérer ou de répartir efficacement des additifs liquides dans la poudre. C'est là qu'interviennent les outils de broyage ou les lames HighShear, qui libèrent une forte densité de puissance dans la poudre. Peu importe que les produits soient granuleux, poussiéreux, fibreux, secs, humides, pâteux, liquides, fluides ou non. L'outil de mélange est conçu de telle sorte qu'il a mélangé l'ensemble du contenu une fois après environ quatre à cinq tours. Ce principe d'écoulement est également appelé écoulement en cuve. Après quelques tours, on observe régulièrement une répartition homogène et égale de tous les composants dans toute la chambre de mélange. On parle alors d'une qualité de mélange idéale, qui ne peut plus être améliorée dans la pratique.
Mélanges de minéraux avec oligo-éléments et vitamines
Les préparations minérales constituent une forme particulière de complément alimentaire. Elles sont ajoutées en petites quantités aux aliments composés destinés aux animaux de rente. Les recettes sont spécialement adaptées aux besoins des bovins, des porcs, des chevaux et de la volaille. Il s'agit de mélanges de chaux et de substances actives qui contiennent au choix du fer, de la vitamine C, du calcium, du zinc, de l'iode, du cuivre, du sélénium, du chrome, du fluor, du potassium, du sodium, du magnésium ou du phosphore. Comme ils agissent en tant que composants actifs mineurs dans les aliments composés, ils doivent être particulièrement homogènes et bien répartis. Pour les rendre peu poussiéreux, ils sont en partie encapsulés ou agglomérés. Pour ces produits également, l'objectif est d'obtenir un produit sans grumeaux ni poussière avec une qualité de mélange optimale.
Quel que soit le mélangeur amixon® utilisé (mélangeur à arbre unique ou mélangeur à double arbre), la qualité de mélange obtenue est toujours idéale. Les deux types de mélangeurs ne diffèrent que par le temps de mélange nécessaire et l'apport énergétique qui en résulte.
Si l'apport d'énergie doit être réduit au minimum, il n'y a pas d'alternative au mélangeur à deux arbres (à l'exception du mélangeur KoneSlid®). Celui-ci
- atteint une qualité de mélange idéale en très peu de temps
- disperse les produits en douceur avec un apport d'énergie minimal
- présente une conception basse et particulièrement compacte
- maîtrise différents niveaux de remplissage
- est particulièrement accessible et sa fabrication est idéale sur le plan de l'hygiène
- convient à tous les types de produits secs, humides et en suspension
- permet une vidange particulièrement efficace
- dispose au choix de plusieurs tubulures de sortie
- comme tous les mélangeurs amixon®, il est équipé d'un arbre de mélange qui n'est monté et entraîné que par le haut.
Mélangeur conique amixon®
Comme le mélangeur conique garantit un mélange rapide et une vidange rapide et quasi totale, il est souvent et aisément mis en œuvre comme mélangeur de FIN DE LIGNE. Le mélangeur conique procède alors à la vidange directement dans le camion-citerne ou la machine de remplissage. Il se distingue par sa capacité à garantir l’exclusion pure et simple de contamination dans la production de mélanges médicaux. Les restes de la charge précédente ne peuvent en aucun cas être transmis aux mélanges fourragers suivants. C’est pourquoi le mélangeur conique est souvent aménagé en fin de chaîne de production. Les ingrédients médicaux sont directement ajoutés dans le mélangeur, uniformément répartis dans l’aliment composé puis entièrement vidés dans le récipient de l’utilisateur final.
Les exigences sont ici comme suit :
- qualité de mélange idéale,
- brève durée de mélange,
- excellente vidange totale,
- vidange rapide,
- grandes portes de visite - bonne accessibilité et
- exécution particulièrement hygiénique.
Le mélangeur se distingue encore par une autre spécialité : il peut être exploité par charges ou en continu.
Mélangeur en tant que mélangeur discontinu ou mélangeur continu
Mélangeur amixon® Gyraton® pour les lots particulièrement importants
Les exigences posées à un mélangeur d'aliments pour animaux peuvent varier fortement selon le type d’entreprise de production d’aliments composés. Par conséquent, il convient d’évaluer soigneusement les conditions d’exploitation et de production avant d’acheter un mélangeur.
La liste de contrôle ci-dessous peut aider à déterminer si le procédé de mélange par charges ou en continu est à privilégier pour un besoin spécifique.
Les critères d’exigence peuvent par ex. être les suivants :
- niveaux de remplissage fortement variables présents / pas présents
- mélange ménageant les particules requis / pas requis
- distribution de liquides à faible niveau de remplissage requise / ….
- distribution de liquides tout en douceur requise / ….
- distribution de liquides fortement désagglomérante et particulièrement rapide requise / ….
- vidange totale très rapide requise / ….
- vidange lente ou par cycles souhaitée / ….
- vidange totale et optimale / ….
- vidange séparée ou simultanée dans plusieurs machines de remplissage requise / ….
- puissance connectée aussi faible que possible exigée / ….
- protection spéciale contre l’usure / ….
- mélangeur devant également être utilisé pour le développement des produits et procédés et donc mise en œuvre variable / ….
- monoproduction dans une large mesure / ….
- différents ordres de mélange qui se suivent rapidement / ….
- accessibilité ergonomique requise pour un nettoyage à sec rapide / ….
- nettoyage humide et séchage rapides et fréquents / ….
- pastilles devant être imprégnées de liquides / ....
- étanchéité à la pression ou au vide de la chambre de mélange requise / ….
- Mélanges prêts à l’emploi avec densité apparente variable de .... kg/dm³ à .... kg/dm³
- produits mélangés dont la température doit être régulée dans le mélangeur / ….
- apport de gaz dans le mélangeur exigé / ....
© Copyright by amixon GmbH