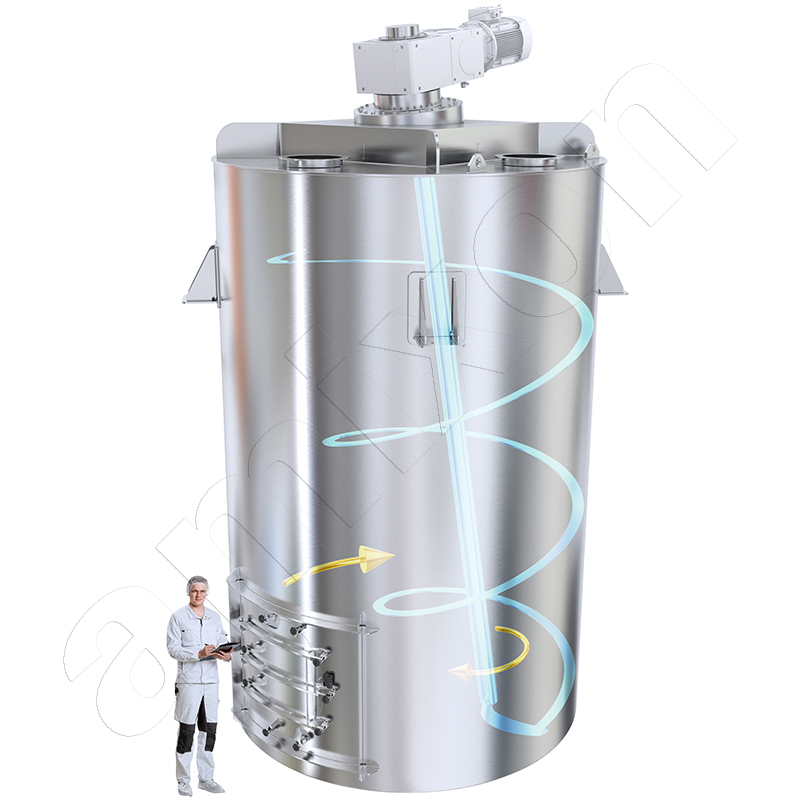
Silo de mélange Gyraton® pour les lots de 50 m³.
Le silo de mélange permet d'obtenir des qualités de mélange optimales
La fabrication amixon® ne s'occupe que de ses propres brevets et développements sur le thème "MÉLANGER". En font partie
- Mélangeur de précision
- Sécheur par contact sous vide
- Réacteurs de synthèse
- Appareils pour l'agglomération de la construction
et
- Silo de mélange Gyraton®.
On parle de mélange de précision de produits dispersés lorsque la variance de la qualité du mélange d'une composition de poudre de 1:100 000 est reproductible à moins de 5 %.
Les produits pulvérulents à mélanger peuvent être secs, humides ou en suspension. amixon® est synonyme de mélangeurs de précision à action verticale.
Un silomixeur Gyraton® atteint des qualités de mélange similaires à celles d'un mélangeur de précision classique
Un silo-mélangeur Gyraton® peut homogénéiser jusqu'à 100 m³ d'enrobé. Il s'agit donc d'un silo de mélange. Ce qui est particulier : Ce silo-mélangeur peut homogénéiser avec précision de grandes quantités de produits en vrac avec des puissances d'entraînement extrêmement faibles. Il en résulte des qualités de mélange qui correspondent à un mélange aléatoire idéal.
On parle de mélange aléatoire idéal lorsque la répartition de la poudre est si homogène qu'une optimisation par des moyens techniques n'est plus possible.
À droite de l'image, on peut voir un mélangeur vertical à hélice. Il s'agit d'un mélangeur de précision classique. Ce type de construction est rarement fabriqué pour des volumes supérieurs à 15 m³. Les grands mélangeurs de précision nécessitent des moteurs d'entraînement de taille correspondante et sont donc relativement chers. Les mélangeurs de précision ne peuvent pas fonctionner aussi lentement que l'on veut.
Si la fréquence de rotation critique n'est pas atteinte, le produit en vrac est simplement entraîné en rotation. Comme l'écoulement tridimensionnel nécessaire à un mélange homogène fait défaut, il n'est pas possible d'obtenir un mélange aléatoire idéal.
La fréquence de rotation minimale d'un mélangeur vertical à arbre unique est généralement d'environ 8 à 12 rpm, mais elle peut être supérieure. Elle dépend en grande partie de la taille du mélangeur ainsi que des propriétés rhéologiques des poudres, notamment de leur densité apparente, de leur répartition granulométrique et de leur fluidité.
L'outil de mélange hélicoïdal du mélangeur Gyraton® est monté sur cardan dans sa partie supérieure. Le fond de la chambre de mélange est conçu comme une coque sphérique. Son rayon correspond à la longueur de l'arbre de mélange. La superposition de la précession et de la rotation crée un mouvement cycloïdal. Selon le rapport entre la fréquence de précession et la fréquence de rotation, on obtient différents profils de circulation. Ceux-ci sont adaptés à la tâche de mélange respective. Comme le centre de rotation se déplace en continu, toutes les zones de la chambre de mélange sont mélangées efficacement.
On peut partir du principe qu'un outil de malaxage Gyraton® peut être utilisé à des fréquences de rotation très basses tout en produisant des qualités de malaxage idéales. Cela doit être démontré.
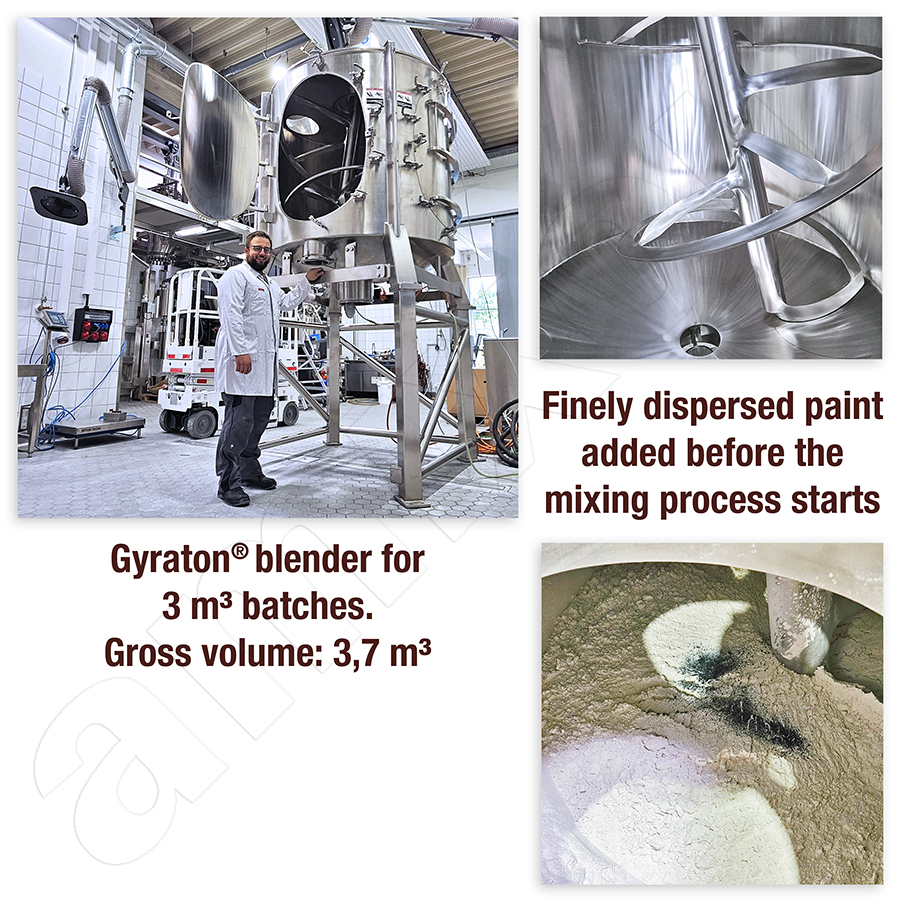
L'efficacité de mélange du mélangeur Gyraton® doit être démontrée
amixon® a construit un silo de mélange Gyraton® avec une taille de lot de 3 m³ pour le tester. Ce silo de mélange permet de mélanger différents lots de poudre.
- Des substances inorganiques très fines, comme le kaolin et les pigments de couleur, y sont mélangées.
- La poussière de carbonate de calcium est humidifiée et mélangée à des pigments de couleur.
- Les mélanges de poudres humides hétérogènes sont colorés.
- Le taux de remplissage est alors maximal à chaque essai. La taille des lots est toujours de 3 m³.
- Les petits additifs pigmentaires sont toujours ajoutés en dernier au centre de la chambre de mélange. Il s'agit de la zone où le mouvement de précession de l'hélice du mélangeur est le moins prononcé.
- Ainsi, au début du processus de mélange, la ségrégation est maximale !
La vitesse périphérique de l'hélice conique du mélangeur augmente de bas en haut. En même temps, l'effet du mouvement de précession diminue de bas en haut.
Preuve de l'excellente qualité du mélange
Tous les résultats obtenus sont excellents. Nous effectuons ensuite d'autres tests de qualité des mélanges sous contrôle scientifique. Nous utilisons pour cela un certificat de qualité officiellement certifié pour les aliments pour animaux (de rente). Il permet de prouver l'homogénéité des compositions de composants jusqu'à un rapport de 1:100 000.
Nous remplissons exactement 1.500 kg d'aliments pour animaux de rente finement broyés pour les porcs et les bovins. La substance utilisée comme traceur est le bleu patenté. Le bleu patenté est extrêmement coloré, soluble dans l'eau, finement dispersé et se présente sous forme désagglomérée et sèche. On en verse exactement 15 grammes par le haut au centre de la chambre de mélange. On obtient une composition de substances avec un rapport pondéral de 1:100 000.
Ensuite, nous fermons la salle de mélange et démarrons l'outil de mélange.
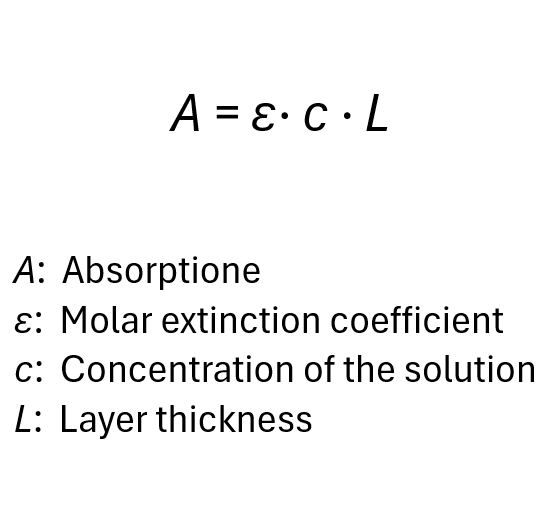
Formule de Lambert.
Loi de Lambert
Après un nombre de rotations bien défini, l'outil de mélange s'arrête. Des échantillons de 30 grammes sont prélevés à dix endroits différents de la chambre de mélange et sont emballés hermétiquement dans de petits sachets. Au laboratoire, on en prélève exactement 15.000 mg que l'on verse dans une cuvette normalisée, puis on ajoute une quantité d'eau ultrapure définie avec précision.
Une fois le temps de dissolution standardisé écoulé, on obtient une solution de couleur homogène. Une source lumineuse monochromatique traverse la cuvette. La mesure est basée sur la loi de Lambert-Beer, qui décrit la relation entre l'absorption de la lumière et la concentration de la substance dissoute. Un photodétecteur enregistre l'intensité de la lumière transmise. Une cuvette remplie de 15 grammes de mélange sans colorant sert de référence. L'absorption de lumière mesurée est proportionnelle à la concentration en colorant dans l'échantillon.
Les résultats sont impressionnants. Le mélangeur Gyraton® produit toujours des qualités de mélange constantes. Ceci est valable indépendamment de la vitesse de rotation de l'outil de mélange Helix. Seul le nombre de rotations est déterminant.
Il est évident que nous disposons ici d'un système de mélange qui peut être mis à l'échelle pour de grands lots. De très petits moteurs d'entraînement permettent d'obtenir des qualités de mélange idéales.
Qualité de mélange réalisable – une analyse à l'aide du coefficient de variation
La qualité du mélange est généralement décrite par le coefficient de variation. Il est particulièrement intéressant d'observer comment cette valeur caractéristique évolue au cours d'un processus de mélange défini et à partir de quel moment elle atteint une valeur stable et optimale. Dans la pratique, la valeur finale stable correspond à un mélange aléatoire maximal pouvant être atteint. Celui-ci n'est pas parfait, mais présente une dispersion résiduelle « V∞ ». Celle-ci décrit l'écart restant par rapport à une répartition idéale en moyenne statistique.
L'évolution temporelle du coefficient de variation peut être représentée de manière idéalisée à l'aide d'une fonction exponentielle.
Vx(t) = V0 · e−k·t + V∞
x1,x2,...,xn : teneurs en concentration
n : nombre d'échantillons
s : écart type
xq : valeur moyenne de la concentration
V0 : coefficient de variation de la dispersion initiale
Vx : coefficient de variation
k : intensité de mélange
t : temps de mélange
V∞ : coefficient de variation de la dispersion résiduelle à l'équilibre
Remarque :
pour obtenir une homogénéité encore meilleure que celle obtenue par hasard, il faudrait théoriquement placer chaque particule de tous les composants à l'endroit exact dans une matrice tridimensionnelle. Cela est concevable, mais irréalisable dans la pratique.
Courbe d'évolution de la qualité du mélange
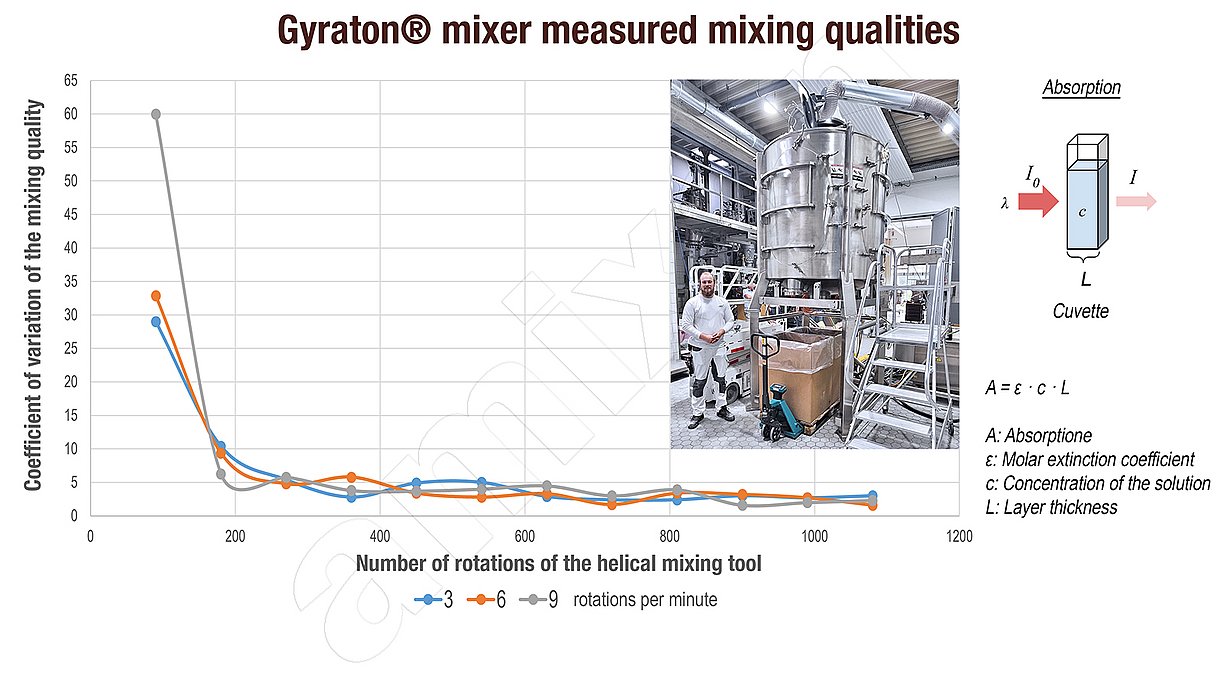
Grande flexibilité et diversité d'utilisation
Pour pouvoir mieux classer les résultats de qualité de mélange, nous les comparons à ceux de nos mélangeurs de précision établis. Nous disposons à cet effet de nombreux résultats de référence. Nous pouvons démontrer que le mélangeur Gyraton produit des qualités de mélange idéales dans les conditions de fonctionnement que nous avons choisies.
Il semble valable dans de larges domaines que la fréquence de rotation de l'outil de mélange Gyraton, multipliée par son temps de mélange, donne une constante :
Fréquence de rotation - temps de mélange = constante C1
Il est connu, sur la base d'une longue pratique d'exploitation, que le couple d'entraînement des mélangeurs à spirale verticaux reste largement constant tant qu'il y a un "mélange par poussée". Par conséquent, le produit de la puissance d'entraînement et du temps de mélange est également constant.
Puissance d'entraînement - temps de mélange = constante C2
Le graphique de gauche illustre la flexibilité. Lorsqu'il n'y a pas d'urgence, le mélangeur Gyraton® peut par exemple être alimenté par l'énergie solaire momentanément disponible sur le toit. Au final, une grande charge de poudre est idéalement homogène.
En règle générale, le temps de mélange d'un mélangeur de silo n'est de toute façon pas soumis à des exigences élevées. Le temps de stockage est disponible pour l'homogénéisation. Par conséquent, s'il n'y a pas urgence, le mélangeur Gyraton® peut par exemple être alimenté par l'énergie solaire actuellement disponible sur le toit. Au final, une grande charge de poudre est homogénéisée avec une précision idéale.
Homogénéisation de produits en vrac
Un conteneur maritime de 40 pieds a une capacité d'environ 70 m³. Des marchandises en vrac comme le thé, les épices, le tabac, le café, les matières premières chimiques et les minerais de terres rares sont livrées quotidiennement dans les ports maritimes. Il est cependant toujours difficile d'estimer la quantité de matériaux de valeur que contient le conteneur. Cela n'est possible que si de très nombreux échantillons sont prélevés et analysés.
Un mélangeur Gyraton® permet d'obtenir une meilleure solution. Il homogénéise l'ensemble du lot de manière économique et précise. La structure des grains est préservée. L'apport de puissance et le dégagement de chaleur sont minimes. Le temps de mélange est réglable et peut varier entre 4 et 24 heures. Ensuite, un seul prélèvement d'échantillon suffit. L'analyse indique la teneur exacte en terres rares. La valeur économique peut être déterminée avec certitude.
De plus, tous les processus de traitement en aval peuvent être contrôlés avec plus de précision.
Plus la marchandise est homogène, plus la préparation de la matière première est efficace.
Partout où le traitement des matières premières a lieu - en particulier lors de l'extraction de métaux alcalins, dont fait partie l'extraction du lithium - de grandes quantités de matières premières sont produites.
Dans les bons gisements, la teneur en lithium est tout au plus de 0,006 %. Pour obtenir 1 kg de lithium pur, il faut traiter 16,7 tonnes de masse brute. Les chaînes de processus sont donc longues et comprennent
- Broyage,
- Classement,
- Séparation des densités,
- Mise en suspension dans des acides de digestion,
- l'extraction chimique,
- Abattage,
- floculation,
- Sédimentation,
- Filtración,
- Séchage,
- Calcination,
- ....
L'homogénéisation suit toujours. Elle marque le début de l'étape suivante du processus. Plus les matières premières sont homogènes, plus le processus suivant peut être géré efficacement et plus les rendements sont élevés. Cela vaut également pour le recyclage et la chimie de synthèse, qui permettent de créer de nouvelles substances actives et de base.
De grands lots doivent être homogénéisés lors de la fabrication de substances actives pharmaceutiques (API). De même, les excipients et les additifs fonctionnels pour les produits pharmaceutiques, les extraits de nutriments, les dérivés d'amidon, la méthylcellulose, la pectine, la gélatine, ...... doivent être homogénéisés en grand volume.
© Copyright by amixon GmbH