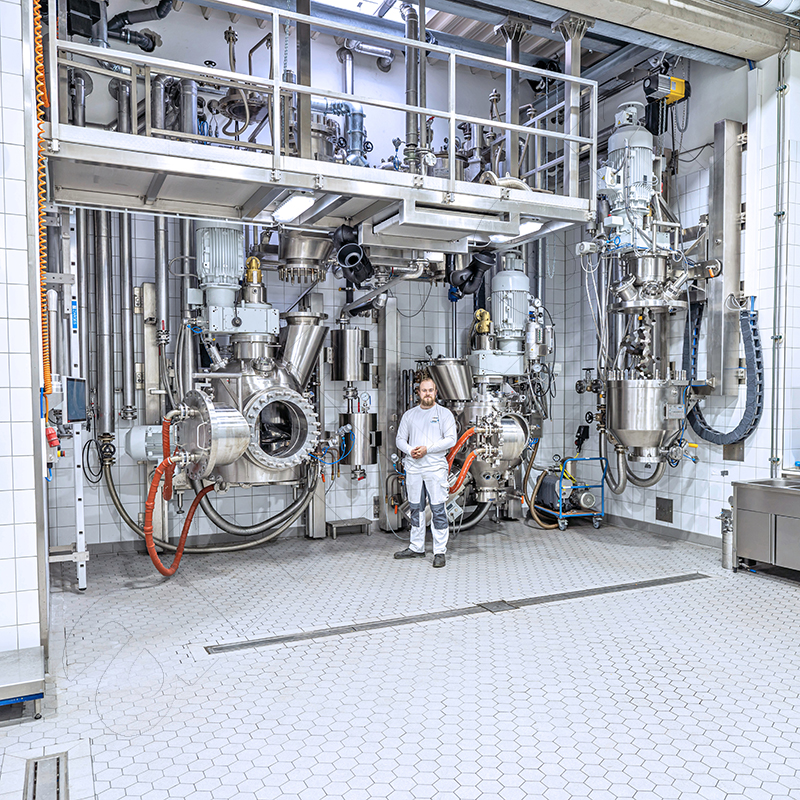
Komplexe Anlagentechnik bei der Aufbereitung von Methylcellulose, Carboxymethylcellulose, Hydroxyethylcellulose usw.
Zellstoff ist eine faserige Masse, die durch chemischen Aufschluss von Pflanzenfasern gewonnen wird. Zellstoff besteht aus Cellulose. Das Wort stammt aus dem Lateinischen und bedeutet kleine Zelle. Cellulose ist das statische Grundgerüst aller Pflanzenzellen.
Cellulosederivate: In chemisch veränderter Form - zum Beispiel als Methylcellulose - machte sie die Entwicklung der Fotografie erst möglich. Sie ist ein wichtiger Bestandteil von Textilfasern. Sie hilft beim Fliesenlegen, hält Backwaren frisch, gibt Mayonnaise ihre Konsistenz und macht Zahnpasta geschmeidig.
Der mengenmäßig bedeutendste Celluloseether ist Carboylmethylcellulose (CMC)
Der gereinigte Zellstoff aus Holz oder Baumwolle wird zu einem feinen Pulver (Partikelgröße ca. 100 bis 200 μm) gemahlen und pneumatisch in einen Großraummischer mit einem Volumen von 10 bis 30 m³ gefördert.
Von dort wird der homogenisierte Zellstoff in einen Synthesereaktor gefördert. In den Reaktor wird fünfzigprozentige Natronlauge eingesprüht. Durch die exotherme Reaktion entsteht Natriumzellulose. Anschließend wird Chloressigsäure in den Reaktor eingesprüht. Es entsteht Carboxylmethylcellulose. Wahlweise kann die CMC-Synthese als Slurry ohne oder mit Lösungsmittel (Isopronanol oder Ethanol) durchgeführt werden.
Andere Cellulosederivate (z. B. Hydroxypropylmethylcellulose) werden auf ähnliche Weise hergestellt. Allerdings werden hier in der Regel keine Lösungsmittel eingesetzt und die Reaktionschemikalien sind gasförmig (Methylchlorid, Propylenoxid oder Ethylenoxid). Der Stoffumsatz erfordert dann vergleichsweise hohe Systemdrücke (bis zu 20 bar), damit die gasförmigen Edukte bei hohen Temperaturen im System verbleiben.
Reaktoren zur Herstellung von Cellulosederivaten sind druckfest ausgelegt. Sie sind außerdem mit einem Doppelmantel ausgestattet, um den Inhalt heizen oder kühlen zu können. Größere Reaktoren verfügen zusätzlich über leistungsstarke Kondensatoren.
amixon® bietet drei Methoden der großvolumigen Homogenisierung: (1), (2) und (3):
(1) amixon® Konusmischer mischt diskontinuierlich
Im amixon® Konusmischer treffen zwei gegenläufige Strömungen aufeinander. Außen wird das Mischgut schraubenförmig nach oben gefördert, in der Mitte überwiegt die Abwärtsströmung. In den Grenzbereichen findet ein Platzwechsel innerhalb des Partikelsystems statt. Die schaufelartig geformten Mischwerksarme erzeugen komplementäre Querströmungen. Trotz langsamer Umdrehungsfrequenzen werden ideale Mischqualitäten gewährleistet, die in der Praxis nicht mehr zu verbessern sind. Die so beschriebene Totalströmung versetzt alle Partikel ständig in Relativbewegung zueinander. Sie ist universell vorhanden, egal ob der Füllgrad 5% oder Maximalfüllung beträgt. Die besondere Formgebung der Mischwendel in „SinConcave®“- oder „SinConvex®“-Bauweise garantiert eine nahezu 100%ige Restentleerung. Die besonders schonende Behandlung des Mischgutes ergibt sich unmittelbar aus der geringen Antriebsleistung. Die Mischgutpartikel werden weder zerkleinert noch verrundet und/oder zerbrochen.
(2) amixon® Konusmischer mischt kontinuierlich
Das Interessante an diesem Mischertyp ist, dass er unabhängig von seiner Größe wahlweise diskontinuierlich oder kontinuierlich betrieben werden kann. Noch interessanter ist aber, dass das ausgetragene Mischgut von Anfang an der idealen Mischqualität entspricht. Es gibt keine „Anfahrverluste“. Dies wird im Folgenden erläutert:
Arbeitsweise bei Produktionsbeginn:
Der Mischerauslauf ist geschlossen. Alle gravimetrisch arbeitenden Dosierorgane werden gleichzeitig mit geringem Massenstrom gestartet. Die Master-Dosiersteuerung harmonisiert alle Produktströme. Der Füllgrad des Mischers steigt kontinuierlich an, wobei der Mischerantrieb bei halber Füllmenge startet. Dieser Ausgleichsvorgang ist abgeschlossen, wenn der Mischer etwas mehr als zur Hälfte gefüllt ist. Nach Erreichen des gewünschten Füllgrades (ca. 60 bis 80 % des Nutzinhaltes) öffnet sich das Auslauforgan langsam. Dieser Füllgrad wird konstant gehalten. Der Dosierstrom kann unter ständiger Regelung bis zum maximalen Massenstrom gesteigert werden.
Betriebsart bei Produktionsende:
Alle Dosierorgane verzögern nacheinander den Massenstrom und schalten dann gleichzeitig ab und schließen. Der Mischer entleert sich kontinuierlich bis zum letzten Rest. Rieselfähige Produkte fließen vollständig aus.
Die Vorteile für den Anwender auf einen Blick:
- technisch ideale Mischqualität
- wahlweise als Chargenmischer für Vormischungen oder als kontinuierlicher Mischer betreibbar
- die Mischintensität ist einstellbar (schonend homogenisieren bis intensiv desagglomerieren)
- Definierte, mittlere Verweilzeit des Mischguts im Mischer auf Basis der kontinuierlichen Kesselströmung. Das ist unabhängig von der Drehzahl des Mischwerkzeugs
- kein Produktverlust am Anfang der Produktion
- kein Produktverlust am Ende der Produktion
- ideale Restentleerung
- definierter Füllgrad wählbar von 10% bis 100% des Nutzinhaltes
- mikrofeine Einmischung der Flüssigkeit ohne Verschmutzung des Mischers
- erweiterte Prozesse wie Befeuchten, Temperieren, Trocknen,
- Reaktionsdurchführung möglich - höchster Hygienestandard (GMP-Standard); einfache Reinigung, trocken oder nass - der Mischer ist nur oben gelagert und angetrieben.
(3) Gyraton® Mischer mischt wahlweise kontinuierlich oder diskontinuierlich
Für die Homogenisierung besonders großer Chargen bis 100 m³ hat amixon® mit dem Gyraton®-Mischer eine interessante Neuentwicklung geschaffen: Die Mischwendel dreht sich im Uhrzeigersinn und fördert das Mischgut nach oben. Ein zusätzlicher Antrieb bewegt den unteren Teil der Mischwerkswelle auf einer Kreisbahn. Der Pivotpunkt befindet sich oben in der Mitte der Wellendichtung. Auch dieser Mischer kann für trockene, feuchte oder auch suspendierte Schüttgüter eingesetzt werden. Die Baugrößen sind von 10 m³ bis 100 m³ frei wählbar. Baugrößen bis 70 m³ können komplett montiert auf der Straße transportiert werden.
Beste Mischergebnisse werden bereits bei einem Füllgrad von 10% erreicht. Die Mischung erfolgt äußerst schonend bei extrem geringem Energieeintrag. Die Beschickung erfolgt von oben über einen oder mehrere Normstutzen. Die Entleerung des Mischgutes erfolgt bei geöffneter Bodenklappe über einen Normstutzen nach unten.
Der Gyraton®-Mischer zeichnet sich aus durch
- Der Mischvorgang erfolgt totraumfrei, besonders schonend und mit minimalem Energieeintrag.
- sehr gute Restentleerung
- optional druck- oder vakuumfest
- der Mischraum ist optional temperierbar
- platzsparende, kompakte Bauweise. Der Großmischer ist auf der Straße transportierbar
- der Mischraum ist durch eine große Inspektionstür leicht zugänglich
- Einfache Reinigung
- nass (automatisch)
- trocken manuell mit Staubsauger
- Je nach Länge der Mischzeit, die vom Kunden vorgegeben werden kann, wird die Drehfrequenz des Mischwerkzeugs und die überlagerte Pendelbewegung angepasst. Die Motoren sind sehr klein. Der Energieverbrauch ist entsprechend gering.
- Das Mischsystem kann auch für feuchte, schlecht fließende Produkte eingesetzt werden.
Versuche im amixon®-Technikum
Wenn Sie vor einer Investitionsentscheidung in den Bereichen Mischen, Homogenisieren, Agglomerieren, Synthese, Kühlen oder Vakuummischtrocknen stehen, sollten Sie mit uns sprechen. amixon® bietet außergewöhnliche und hocheffiziente Lösungen. Wir bieten Ihnen ein breites verfahrenstechnisches Know-how und verfügen über einen hervorragend ausgestatteten Maschinen-/Apparatebau. Gerne vereinbaren wir mit Ihnen kurzfristig einen Termin für Versuche in unserem Technikum.
Kontinuierliche Kühlung mit Scherbeneis
Das Reaktionsprodukt ist ein feuchtes Cellulosederivat, das noch Kochsalz und einige Nebenprodukte (höhere Alkohole) enthält. Das Rohprodukt wird in ein 90 °C heißes Wasserbad überführt und suspendiert. Salze und Nebenprodukte lösen sich im heißen Wasser. Nicht jedoch die Celluloseether: MC, HEMC und HPMC sind bei Temperaturen über 50-60 °C wasserunlöslich.
Anschließend wird das heiße Waschwasser durch Filtration abgetrennt und der Filterkuchen salzfrei gewaschen. Das heiße Waschwasser kann mehrfach zur Reinigung verwendet werden, da es bis zu 30 Prozent Kochsalz aufnehmen kann. Dadurch können Energie und Wasser eingespart werden. Die Restfeuchte des gereinigten Produktes beträgt nach der Filter- und Waschstufe noch etwa 50 bis 60 Prozent. Der Celluloseether hat nach der Wäsche noch eine Schüttdichte von ca. 150 g/l. Zur Kühlung werden kontinuierlich arbeitende Horizontalmischer eingesetzt. Die Kühlung erfolgt in der Regel mit Scherbeneis. Bei Temperaturen unter 45 °C ist das Produkt nicht mehr wasserlöslich.
Große Massen müssen effizient und hygienisch getrocknet werden.
Die hier eingesetzten Stromtrockner sind meist kontinuierlich arbeitende Mahltrockner. Sie sind in der Lage, Agglomerate effektiv aufzubrechen. Die Trocknung erfolgt atmosphärisch. Große Luftmengen werden vorgereinigt, getrocknet und erwärmt. Dem Trocknungsprozess ist große Bedeutung beizumessen. Er verbraucht viel Energie.
Das getrocknete Pulver wird anschließend in einem Zyklon entstaubt. Feinste Stäube werden in Gewebefiltern abgeschieden. Anschließend werden die Schwerteile aussortiert und gesiebt. Für die Endanwendung ist eine definierte Korngröße wichtig.
Zellstoff ist ein nachwachsendes Naturprodukt. Wie alle Naturprodukte unterliegt auch Zellstoff jahreszeitlichen und standortbedingten Schwankungen. Zudem wird Zellstoff chargenweise aufbereitet. Auch hier gibt es von Charge zu Charge leichte Qualitätsunterschiede. Diese auszugleichen ist eine der Hauptaufgaben des großvolumigen Finalmischers. Anschließend wird die Ware in Säcke oder Bigbags verpackt.
Hochfeste Werkstoffe müssen auch dauerhaft korrosionsbeständig sein. Hier kommt der Schweißtechnik eine große Bedeutung zu.
Darüber hinaus gibt es weitere Kriterien, die bei der Auslegung des Reaktors zu berücksichtigen sind. So muss der Behälterwerkstoff neben einer hohen Festigkeit eine besondere Korrosionsbeständigkeit aufweisen, da die entstehenden Chloride der Salze bei hohen Temperaturen in Verbindung mit Wasser chemisch aggressiv sind. Das Phänomen der Spannungsrisskorrosion beschreibt eine Abnahme der Korrosionsbeständigkeit von Werkstoffen, wenn diese einer erhöhten Zugspannung ausgesetzt werden. Darüber hinaus ist das Phänomen der Materialermüdung durch wechselnde Belastung und Temperatur zu berücksichtigen.
Auch der Umgang mit Reagenzien und Reaktionsnebenprodukten erfordert viel Know-how. Das höchste Gefährdungspotential hat Ethylenoxid (Herstellung von HEC oder HE-Mischethern wie HEMC): Es ist explosiv und muss unter Stickstoffatmosphäre gelagert werden. Bei der Herstellung von Methylcellulosen (MC, HEMC oder HPMC) entsteht in einer Nebenreaktion Dimethylether, der leicht entzündlich, explosiv und giftig ist. Er muss am Ende der Reaktion zusammen mit nicht umgesetztem Methylchlorid abgeführt werden. Im industriellen Verfahren wird das Gasgemisch unter Druck aufgefangen und bestenfalls im Prozess wiederverwendet.
Cellulose ist ein Multitalent
Mit kaum einem anderen Rohstoff ist die Geschichte der Menschheit so eng verbunden wie mit der Cellulose. Ohne Papier wäre die Geschichte der Menschheit eine andere. Sogar Lumpen wurden anfangs zur Papierherstellung verwendet. Denn sie bestehen aus Baumwolle. In deren Fasern liegt die Cellulose in besonders reiner Form vor.
Die Entwicklung der chemischen Nutzung der Cellulose begann 1846 mit der Herstellung von Nitrocellulose, auch Cellulosetrinitrat genannt. Sie wurde zunächst für militärische Zwecke verwendet und auch als Schießbaumwolle bezeichnet. Sie entsteht, wenn Cellulose mit Nitriersäure, einer Mischung aus Schwefel- und Salpetersäure, behandelt wird. In weiteren Verfahrensschritten wird die Schießbaumwolle gewaschen, gemahlen und getrocknet.
Historie
Parallel zur militärischen Nutzung begann im 19. Jahrhundert die zivile Nutzung der Nitrocellulose. Schwach nitrierte Nitrocellulose (Cellulosedinitrat) wurde mit Kampher vermischt und bildete als Zelluloid die Grundlage für die ersten technischen Kunststoffe.
Als Träger für fotografische Filme diente Zelluloid bis 1951. Auch Tischtennisbälle wurden bis 2014 aus Zelluloid hergestellt. Die erste durchsichtige Kunststofffolie basierte ebenfalls auf Zellulose. In den 1920er Jahren wurde Zellglas (Markenname: Cellophan) für Verpackungszwecke hergestellt. Es ist besonders glänzend und lässt sich im Gegensatz zu modernen Verpackungsfolien dauerhaft knicken. Es wurde z. B. als Bonbonverpackung verwendet, da es sich an beiden Enden gut „twisten“ ließ. Inzwischen wurde Cellophan aus preislichen und technischen Gründen weitgehend durch Kunststofffolien auf Ölbasis ersetzt. Eine Renaissance des Cellophans könnte jedoch in Zukunft durch seine hervorragende biologische Abbaubarkeit begründet sein.
Es gibt einen wichtigen Grund, warum Zelluloid durch andere Kunststoffe ersetzt wurde. Das ist die leichte Entflammbarkeit von Zelluloid.
Cellulose ist biologisch abbaubar
Der Zellulosegehalt der Baumwolle beträgt etwa 84-91%. Aufgrund ihrer langen Fasern wird sie hauptsächlich als Textilrohstoff verarbeitet. Der Cellulosegehalt von Holz beträgt dagegen nur ca. 40-45% und muss durch einen aufwändigen chemischen Aufschluss isoliert werden. Vor allem Sägerestholz und minderwertige Nadelhölzer werden als Rohstoff für die industrielle Verwertung zu Papier eingesetzt. Aber auch höherwertige Nadel- und Laubholzqualitäten, meist aus Plantagen, werden für die Verwendung als Chemiezellstoff eingesetzt.
Mit Hilfe des Sulfitaufschlussverfahrens wird aus Holz eine besonders reine Cellulose gewonnen. Die so gewonnene Chemiezellulose wird auch Dissolving Pulp oder Spezialzellstoff genannt.
Doch zunächst muss die Cellulose aus dem Holz herausgelöst werden. Die Stämme werden zu Hackschnitzeln zerkleinert. Dabei wird eine einheitliche Größe angestrebt.
Diese Holzhackschnitzel werden in druckfesten Reaktoren mit sauren Chemikalien unter Hitze und Druck über mehrere Stunden gekocht. Begleitstoffe der Cellulose wie Lignin und Hemicellulosen lösen sich in der Säure und werden mit dem Filtrat abgetrennt. Das Filtrat wird Schwarzlauge genannt und enthält Ligninreste, Kohlenhydrate aus dem Abbau der Hemicellulosen, Natriumcarbonat, Natriumsulfat und andere anorganische Salze. Aus der Schwarzlauge werden Natrium, Schwefel und Calcium weitgehend zurückgewonnen und wiederverwertet. Aus dem Lignin kann, ähnlich wie aus Baumrinde, Vanillin gewonnen werden.
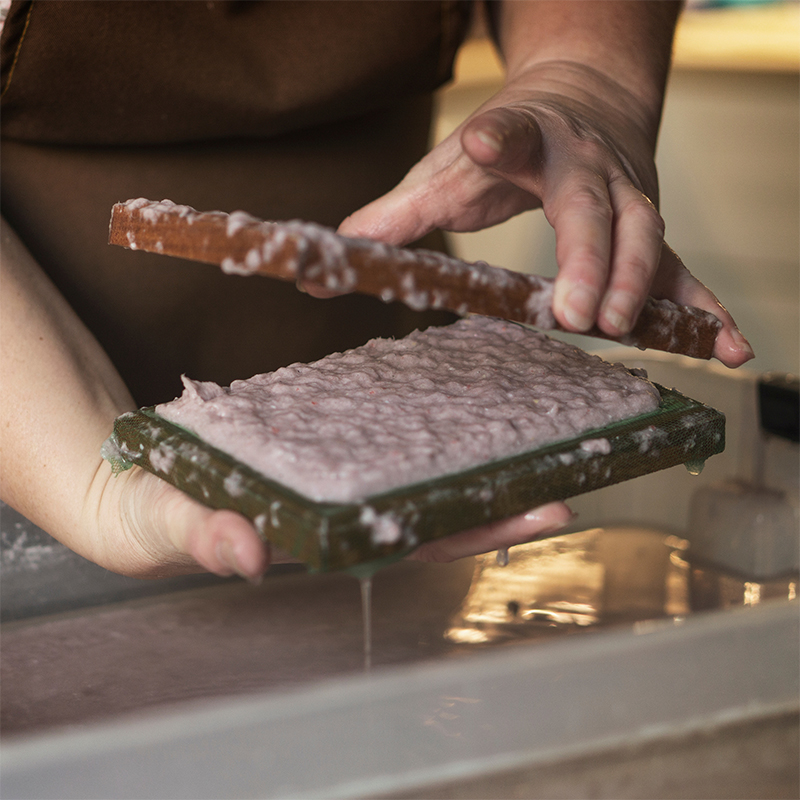
Zelluloseschlamm wird manuell entwässert.
Cellulosederivate und ihre Weltproduktion im Jahr 2020
Produkt | Weltproduktion im Jahr 2019 | Anwendung |
Cellulose regeneriert | 3.300.000 t/a | Textilien |
Celluloseacetat | 900.000 t/a | Beschichtungen und Membranen |
Cellulosenitrat | 420.000 t/a | Beschichtungen, Membranen und Sprengstoffe |
Carboxymethyl-cellulose | 360.000 t/a | Lebensmittel, Kosmetik, Pharma, Ölfeld, Papier |
Methylcellulosen | 180.000 t/a | Lebensmittel, Pharma und Bau |
Hydroxylethyl-cellulose | 8.000 t/a | Farben, Lacke, Filme und Kosmetika |
Ethylcellulose | 80 t/a | Pharma, Elektronik |
Derivate der Cellulose begegnen uns fast überall
Die Fortschritte in der makromolekularen Chemie führten zur Entwicklung einer Vielzahl von Cellulosederivaten mit wertvollen Eigenschaften.
Celluloseester: 1856 wurde aus Kampher und Cellulosenitrat der erste thermoplastische Kunststoff hergestellt. Daraus entstanden Tischtennisbälle und Filmmaterial für Fotografie und bewegte Bilder.
Celluloseacetat: Es folgte ein zweiter thermoplastischer Kunststoff, der zu Schaumstoff (Zigarettenfilter) und Fasern verarbeitet werden konnte. Weiterentwicklungen führten zu transparenten Formkörpern, Würfeln und Werkzeuggriffen.
Celluloseether: Seit Anfang der 30er Jahre hat diese Gruppe der Cellulosederivate ihre industrielle Bedeutung erlangt, ein Siegeszug, der bis heute anhält und ein immer breiteres Anwendungsspektrum aufweist. Celluloseether sind ungiftige, meist wasserlösliche Produkte, die meist als weiße Pulver oder Granulate gehandelt werden. Die spezifischen Eigenschaften der einzelnen Celluloseether hängen von der Art, Anzahl und Verteilung der Substituenten ab, die durch eine chemische Reaktion nach Aktivierung des Cellulosemoleküls mit Natronlauge eingeführt werden.
Einsatzbereiche
Die Namensgebung erfolgt unter Nennung des Substituenten, z.B.: Methylcellulose (MC), Hydroxypropylmethylcellulose (HPMC), Carboxymethylcellulose (CMC), Hydroxypropylcellulose (HPC), Ethylcellulose (EC), etc. Einsatzgebiete finden sich in der Bauindustrie als Zusatzstoffe zur Optimierung verschiedener Eigenschaften in Mörteln, Fliesenklebern oder Spachtelmassen (HEMC oder HPMC). Tapetenkleister besteht hauptsächlich aus Methylcellulose (MC) oder Carboxymethylcellulose (CMC).
In der Metallumformung werden Cellulosederivate als Gleitmittel eingesetzt, bei der Herstellung von Farben und Lacken als Viskositätsregler und Bindemittel. In Geschirrspülmaschinentabs als Sprengmittel oder in der Landwirtschaft, um die Wirkung von Pflanzenschutzmitteln zu verzögern.
Einige Cellulosederivate sind als Lebensmittelzusatzstoffe und für den Einsatz in kosmetischen Formulierungen zugelassen. Dabei macht man sich unter anderem das Verhalten der verschiedenen Celluloseether in wässriger Umgebung bei unterschiedlichen Temperaturen zunutze. Sie sind oft unverzichtbare Zusätze in Emulgatoren, Stabilisatoren und Konservierungsmitteln. Sie verbessern die Fließfähigkeit von Instantsoßen und -suppen. In Speiseeis beeinflussen sie das Schmelzverhalten sowie das Mundgefühl und verleihen ihm trotz Rahmreduktion einen cremig-sahnigen Geschmack.
In der Lebensmittel- und Pharmaindustrie beeinflussen sie Textur, Form, Struktur und Konsistenz von flüssigen und halbfesten Produkten. Ihr Anwendungsbereich reicht von Zahnpasta bis zu Überzugsmassen für Arzneimittel. In der Kosmetik dienen sie als Viskositätsregler und Stabilisatoren, sie bestimmen die Rheologie von Salben, Sonnencremes und Make-up. Ihr Potenzial ist noch lange nicht ausgeschöpft und Gegenstand intensiver Forschung.
Der Preis für „einfache“ Cellulosederivate wie Carboxymethylcellulose (CMC) beginnt bei 1,50 €/kg und steigt bis auf über 100 €/kg für spezielle Cellulosederivate in pharmazeutischen Anwendungen. Celluloseether sind in vielen Anwendungen kaum durch erdölbasierte Produkte substituierbar. Dies wird ihre Bedeutung in verschiedenen Industrien erhöhen. Insbesondere in vielen pharmazeutischen Anwendungen oder als Lebensmittelzusatzstoffe, vor allem für Convenience-Produkte.
Celluloseether und ihre Einsatzgebiete in der Industrie
Name | Ab-kürzung | Herstellung | Anwendung |
Carboxy-methyl-cellulose | CMC | Mit Natronlauge in Alkalicellulose überführt. Alkylierung mit Chloressigsäure. | Erdölindustrie, Textilindustrie, Waschmittelzusatz, Bindemittel, Verdicker, Papierleimungsmittel (Tapetenkleister), Schutzkolloid, Lebensmittelzusatzstoff E 466 (Eis, Mayo, Gelee, Backwaren), Zahncreme, vernetzt als Tablettensprengmittel |
Methyl- cellulosen | MC HEMC HPMC | Mit Natronlauge in Alkalicellulose überführt. Alkylierung mit Methylchlorid, Veretherung mit Ethylenoxid oder Propylenoxid | Additive in verschiedenen Baustoffen (Beton, Mörtel, Fliesenkleber, Spachtelmassen, Putze, etc.) Tapetenkleister, Verdickungs-, Gelier- und Überzugsmittel, Emulgator, Stabilisator in Lebensmittel (MC: E 461, HPMC: E 464) Fleischersatzprodukte, Eis, Backwaren, Mayo, Instantprodukte und Tiefkühlwaren) und Kosmetika. In der Pharmazie als „künstliche Tränenflüssigkeit“, Abführmittel, negatives Kontrastmittel, Retardierung von Wirkstoffen, Tabletten-Coating, Material für Hartkapseln. |
Ethyl-cellulose | EC | Mit Natronlauge in Alkalicellulose überführt. Alkylierung mit Ethylchlorid. | Verdickungs-, Binde-, Klebemittel, sowie als Filmbildner und wasserabweisende Barriereschicht. Hauptbestandteil lichtechter Celluloseetherlacke, Packmittel, thermoplastischen Kunststoffen, künstlichem Schnee für Weihnachtsbäume, Kabelisolierungen, Schutzhäuten und Dichtungen. Als Zusatz von Kunstharzen und Wachsen zum Lackieren von gefärbten Ostereiern und als Zusatz für Stempelfarben in der Lebensmittelindustrie (E 462). In der Pharmazie Hilfsstoff zur Viskositätserhöhung, als Bindemittel für Tablettengranulate, als Gerüststoff und Sprengmittel für Tabletten sowie insbesondere auch als Filmbildner (z. B. unter Surelease® markenrechtlich geschützt) für Lacktabletten |
Hydroxy-ethyl-cellulose | HEC | Mit Natronlauge in Alkalicellulose überführt. Veretherung mit Ethylenoxid. | In der Baustoffindustrie in wasserlöslichen Farben und Dispersionsklebern sowie Putz- und Spachtelmassen. In Pharmazeutika als Hilfsstoff und in Zahncreme. |
Hydroxy-propyl-cellulose | HPC | Mit Natronlauge in Alkalicellulose überführt. Veretherung mit Propylenoxid. | Anwendung als pharmazeutischer Hilfsstoff, Bindemittel für keramische Massen, für Überzüge und Klebstoffe, in Kosmetikartikeln, in Drucktinten und in der Polymerisationstechnik. In Lebensmitteln als Stabilisator, Schutzschicht und Glanzüberzug. |
© Copyright by amixon GmbH