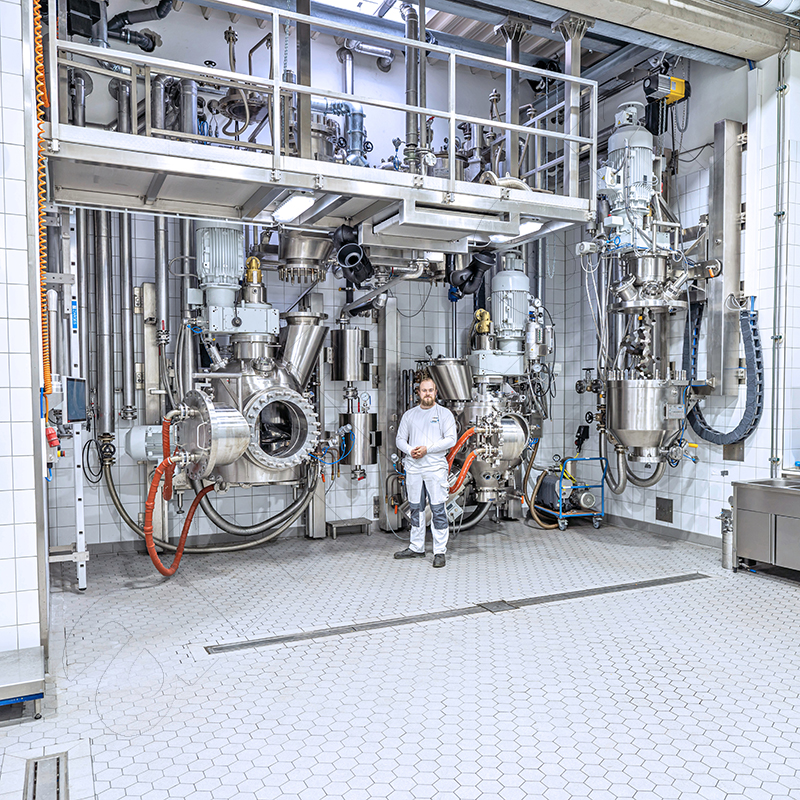
Tecnologia vegetale complessa per la preparazione di metilcellulosa, carbossimetilcellulosa, idrossietilcellulosa, ecc.
La polpa è la massa fibrosa prodotta durante la spappolatura chimica delle fibre vegetali. La polpa è costituita principalmente da cellulosa. Il termine deriva dal latino e significa piccola cella. La cellulosa è la struttura statica di base di tutte le cellule vegetali.
Dérivés de la cellulose : sous une forme chimiquement modifiée - par exemple sous forme de méthylcellulose -, elle a rendu possible le développement de la photographie. Elle est un composant important des fibres textiles. Elle aide à la pose de carreaux, conserve la fraîcheur des produits de boulangerie, donne sa consistance à la mayonnaise et rend le dentifrice souple.
Processi di reazione complessi per la carbocellulosa
L'etere di cellulosa più importante in termini di quantità è la carbocellulosa (CMC). La cellulosa purificata proveniente dal legno o dal cotone viene macinata in una polvere fine (dimensioni delle particelle da 100 a 200 μm circa) e trasportata pneumaticamente in un miscelatore di grande volume da 10 a 30 m³.
Da qui, la pasta omogeneizzata viene convogliata in un reattore di sintesi. Il 50% di soda caustica viene spruzzato nel reattore. La reazione esotermica produce cellulosa di sodio. Quindi l'acido cloroacetico viene spruzzato nel reattore. Si ottiene così carbossimetilcellulosa. Opzionalmente, la sintesi della CMC può essere effettuata in forma di slurry senza o con solvente (isopronanolo o etanolo).
Altri derivati della cellulosa (ad esempio l'idrossipropilmetilcellulosa) sono prodotti in modo simile. L'unica differenza è che in questo caso non vengono utilizzati solventi e le sostanze chimiche di reazione sono gassose (cloruro di metile, ossido di propilene o ossido di etilene). La conversione delle sostanze richiede quindi pressioni di sistema relativamente elevate (fino a 20 bar) per garantire che i reagenti gassosi rimangano nel sistema a temperature elevate.
I reattori per la produzione di derivati della cellulosa sono progettati per essere resistenti alla pressione. Sono inoltre dotati di una doppia camicia per poter riscaldare o raffreddare il contenuto. I reattori più grandi hanno anche sistemi di raffreddamento aggiuntivi nelle sovrastrutture e parallelamente ai reattori.
amixon ® offre tre metodi di omogeneizzazione di grandi volumi: (1), (2) e (3):
(1) il miscelatore conico amixon® mescola in modo discontinuo
Nella fase finale del processo, il prodotto viene macinato ed essiccato in essiccatori elettrici. L'essiccazione avviene in atmosfera. Il materiale secco prodotto viene raccolto in grandi miscelatori e omogeneizzato prima di essere riempito in sacchi o BigBag.
La materia prima cellulosa è un prodotto naturale rinnovabile. Come tutti i prodotti naturali, anche la materia prima è soggetta a fluttuazioni stagionali e legate al sito. Inoltre, la sostanza viene preparata in lotti. Anche in questo caso si riscontrano lievi differenze di qualità da un lotto all'altro. Il bilanciamento di questi elementi è uno dei compiti principali del miscelatore di prodotti finali di grande volume. Di seguito vengono descritti 3 metodi di miscelazione finale.
Nel miscelatore conico amixon® si incontrano due flussi opposti. All'esterno, l'impasto viene convogliato verso l'alto con un andamento elicoidale, mentre al centro prevale il flusso verso il basso. Nelle zone di confine si verifica un cambiamento di luogo all'interno del sistema particellare. I bracci del miscelatore a forma di lama generano flussi incrociati complementari. Nonostante le basse frequenze di rotazione, vengono garantite qualità di miscelazione ideali che non possono più essere migliorate nella pratica. Il flusso totale così descritto pone costantemente tutte le particelle in moto relativo tra loro. È disponibile universalmente, indipendentemente dal fatto che il livello di riempimento sia del 5% o del massimo. La speciale forma dell'elica di miscelazione nel design "SinConcave®" o "SinConvex®" garantisce uno scarico residuo quasi al 100%. Il trattamento particolarmente delicato del materiale da miscelare deriva direttamente dalla bassa potenza di azionamento. Le particelle della miscela non sono né frantumate né arrotondate e/o rotte.
(2) il miscelatore conico amixon® mescola in modo continuo
L'aspetto interessante di questo tipo di miscelatore è che può funzionare in modo discontinuo o continuo, indipendentemente dalle sue dimensioni. Ancora più interessante, tuttavia, è che il mix scaricato corrisponde alla qualità ideale del mix fin dall'inizio. Non ci sono "perdite di avviamento". Questo viene spiegato di seguito:
Modalità di funzionamento all'inizio della produzione:
L'uscita del miscelatore è chiusa. Tutte le unità di misurazione a funzionamento gravimetrico vengono avviate simultaneamente con un flusso di massa ridotto. Il controllo del dosaggio master armonizza tutti i flussi di prodotto. Il livello di riempimento del miscelatore aumenta continuamente, con l'azionamento del miscelatore che inizia a metà del livello di riempimento. Questo processo di equalizzazione è completato quando il miscelatore è leggermente più pieno della metà. Dopo aver raggiunto il livello di riempimento desiderato (circa il 60-80% del volume utile), l'organo di scarico si apre lentamente. Questo livello di riempimento viene mantenuto costante. Il flusso di dosaggio può essere aumentato sotto controllo costante fino alla portata massica massima.
Modalità di funzionamento a fine produzione:
Tutti gli elementi di misurazione decelerano il flusso di massa uno dopo l'altro e poi si spengono e chiudono simultaneamente. Il miscelatore si svuota continuamente fino all'ultimo residuo. I prodotti a flusso libero fuoriescono completamente.
I vantaggi per l'utente in sintesi:
- qualità di miscelazione tecnicamente ideale
- Può essere utilizzato come miscelatore discontinuo per le premiscele o come miscelatore continuo.
- l'intensità di miscelazione è regolabile (da omogeneizzazione delicata a deagglomerazione intensiva)
- Tempo di permanenza medio definito del materiale miscelato nel miscelatore in base al flusso continuo della caldaia. Ciò è indipendente dalla velocità dell'utensile di miscelazione.
- Nessuna perdita di prodotto all'inizio della produzione
- Nessuna perdita di prodotto a fine produzione
- scarico residuo ideale
- Livello di riempimento definito selezionabile dal 10% al 100% della capacità utile
- Miscelazione microfine del liquido senza contaminazione del miscelatore
- processi avanzati come l'umidificazione, la tempra e l'essiccazione,
- Reazione possibile - massimo standard igienico (standard GMP); facile pulizia, a secco o a umido - il miscelatore è montato e azionato solo dall'alto.
(3) Il miscelatore Gyrato® mescola in modo continuo o discontinuo.
Per l'omogeneizzazione di lotti particolarmente grandi, amixon® ha creato un nuovo interessante sviluppo con il miscelatore Gyraton®: La spirale di miscelazione ruota in senso orario e trasporta la miscela verso l'alto. Un azionamento supplementare muove la parte inferiore dell'albero del miscelatore su un percorso circolare. Il punto di rotazione si trova al centro della guarnizione dell'albero.
Questo miscelatore può essere utilizzato anche per materiali sfusi secchi, umidi o in sospensione. Le dimensioni sono liberamente selezionabili da 10 m³ a 100 m³. Le dimensioni fino a 70 m³ possono essere trasportate completamente assemblate su strada.
I migliori risultati di miscelazione si ottengono già con un livello di riempimento del 10%. La miscelazione avviene in modo estremamente delicato e con un apporto energetico estremamente ridotto. L'alimentazione avviene dall'alto tramite uno o più ugelli standard. Il materiale miscelato viene svuotato verso il basso tramite un beccuccio standard quando lo sportello inferiore è aperto.
Il miscelatore Gyraton® è caratterizzato da
- Il processo di miscelazione avviene senza spazi morti, in modo particolarmente delicato e con un apporto energetico minimo.
- Ottimo svuotamento residuo
- opzionalmente resistente alla pressione o al vuoto
- la camera di miscelazione è opzionalmente regolabile in temperatura
- design compatto e salvaspazio. Il miscelatore di grandi dimensioni può essere trasportato su strada
- la camera di miscelazione è facilmente accessibile attraverso un ampio sportello di ispezione
- Facile da pulire
- bagnato (automatico)
- manuale a secco con hoover
- In base alla durata del tempo di miscelazione, che può essere specificata dal cliente, vengono regolati la frequenza di rotazione dell'utensile di miscelazione e il movimento a pendolo sovrapposto. I motori sono molto piccoli. Il consumo energetico è di conseguenza ridotto.
- Il sistema di miscelazione può essere utilizzato anche per prodotti umidi e poco scorrevoli.
Prove nel centro tecnico amixon®
Se dovete prendere una decisione di investimento nei settori della miscelazione, dell'omogeneizzazione, dell'agglomerazione, della sintesi, del raffreddamento o dell'essiccazione di miscele sottovuoto, rivolgetevi a noi. amixon® offre soluzioni eccezionali e altamente efficienti. Vi offriamo un ampio know-how in materia di ingegneria di processo e disponiamo di un reparto di costruzione di macchine/attrezzature ottimamente attrezzato. Saremo lieti di concordare con voi un appuntamento a breve termine per le prove nel nostro centro tecnico.
Raffreddamento continuo con ghiaccio in scaglie
Il prodotto della reazione è un derivato umido della cellulosa che contiene ancora sali comuni e alcuni sottoprodotti (alcoli superiori). Il prodotto grezzo viene trasferito in un bagno d'acqua a 90 °C e sospeso. I sali e i sottoprodotti si dissolvono nell'acqua calda. Ma non l'etere di cellulosa: MC, HEMC e HPMC sono insolubili in acqua a temperature superiori ai 50-60 °C.
L'acqua di lavaggio calda viene poi separata per filtrazione e il panetto filtrante viene lavato senza sale. L'acqua di lavaggio calda può essere utilizzata più volte per la pulizia, in quanto può assorbire fino al 30% di sale comune. In questo modo è possibile risparmiare energia e acqua. L'umidità residua del prodotto pulito dopo la fase di filtraggio e lavaggio è ancora pari a circa il 50-60%. L'etere di cellulosa, che dopo il lavaggio ha ancora la densità apparente della cellulosa macinata (circa 150 g/l), viene ora raffreddato selettivamente in un agglomeratore con miscelatore ad anello a funzionamento continuo mediante l'aggiunta di acqua fredda o ghiaccio in scaglie, fino a raggiungere la temperatura di solubilità in acqua (circa 45°C).
Le grandi masse devono essere essiccate in modo efficiente e igienico.
Gli essiccatori flash utilizzati in questo caso sono solitamente essiccatori a macinazione a funzionamento continuo. Sono in grado di rompere efficacemente gli agglomerati. Il processo di essiccazione avviene in atmosfera. Grandi volumi d'aria vengono pre-puliti, essiccati e riscaldati. Il processo di essiccazione è molto importante. Consuma molta energia.
La polvere essiccata viene poi depolverata in un ciclone. La polvere più fine viene separata in filtri di tessuto. Le particelle pesanti vengono poi selezionate e setacciate. Una dimensione definita delle particelle è importante per l'applicazione finale.
La pasta è un prodotto naturale rinnovabile. Come tutti i prodotti naturali, anche la pasta è soggetta a fluttuazioni stagionali e legate al sito. La pasta viene inoltre lavorata in lotti. Anche in questo caso, la qualità varia leggermente da lotto a lotto. Uno dei compiti principali del miscelatore finale di grandi volumi è quello di livellare queste differenze. La merce viene poi confezionata in sacchi o big bag.
I materiali ad alta resistenza devono anche essere permanentemente resistenti alla corrosione. La tecnologia di saldatura è di grande importanza.
Inoltre, ci sono altri criteri che devono essere presi in considerazione nella progettazione del reattore. Ad esempio, oltre all'elevata resistenza, il materiale del contenitore deve avere una particolare resistenza alla corrosione, poiché i cloruri dei sali che si formano sono chimicamente aggressivi alle alte temperature in combinazione con l'acqua. Il fenomeno della cricca da tensocorrosione descrive una diminuzione della resistenza alla corrosione dei materiali quando questi sono sottoposti a una maggiore tensione di trazione. Inoltre, si deve tenere conto del fenomeno della fatica del materiale dovuta alla variazione del carico e della temperatura.
Anche la gestione dei reagenti e dei sottoprodotti di reazione richiede un notevole know-how. L'ossido di etilene presenta il potenziale di pericolo più elevato (produzione di HEC o di eteri misti HE come l'HEMC): È esplosivo e deve essere conservato in atmosfera di azoto. Durante la produzione di metilcellulosa (MC, HEMC o HPMC), in una reazione secondaria si forma dimetil etere, altamente infiammabile, esplosivo e tossico. Deve essere scaricato alla fine della reazione insieme al cloruro di metile non reagito. Nel processo industriale, la miscela di gas viene raccolta sotto pressione e, nella migliore delle ipotesi, riutilizzata nel processo.
La cellulosa è una sostanza multitalento
Quasi nessun'altra materia prima è così strettamente legata alla storia dell'umanità come la cellulosa. Senza la carta, la storia dell'umanità sarebbe diversa. All'inizio si usavano persino gli stracci per fare la carta. Perché sono in cotone. Nelle loro fibre, la cellulosa è presente in forma particolarmente pura.
Lo sviluppo dell'uso chimico della cellulosa iniziò nel 1846 con la produzione di nitrocellulosa, chiamata anche trinitrato di cellulosa. Fu utilizzato per la prima volta per scopi militari e fu chiamato anche cotone per armi da fuoco. Si forma quando la cellulosa viene trattata con l'acido nitrico, una miscela di acido solforico e nitrico. In ulteriori fasi del processo, il cotone per armi viene lavato, macinato ed essiccato.
Storia
Parallelamente all'uso militare, l'uso civile della nitrocellulosa è iniziato nel XIX secolo. La nitrocellulosa debolmente nitrata (dinitrato di cellulosa) fu mescolata con la canfora e costituì la base delle prime materie plastiche tecniche come la celluloide.
La celluloide è stata utilizzata come supporto per le pellicole fotografiche fino al 1951. Anche le palline da tennis da tavolo sono state realizzate in celluloide fino al 2014. Anche il primo film plastico trasparente era a base di cellulosa. Negli anni '20, il cellophane (marchio: Il cellophane) viene prodotto a scopo di imballaggio. È particolarmente lucido e, a differenza dei moderni film da imballaggio, può essere piegato in modo permanente. Veniva utilizzato, ad esempio, come involucro per le caramelle perché poteva essere "attorcigliato" bene a entrambe le estremità. Nel frattempo, il cellophane è stato ampiamente sostituito da pellicole plastiche a base di petrolio per ragioni tecniche e di prezzo. Tuttavia, una rinascita del cellophane potrebbe essere giustificata in futuro dalla sua eccellente biodegradabilità.
C'è un motivo importante per cui la celluloide è stata sostituita da altre materie plastiche. Si tratta della facile infiammabilità della celluloide.
La cellulosa è biodegradabile
Il contenuto di cellulosa del cotone è di circa 84-91%. Grazie alle sue fibre lunghe, viene lavorata principalmente come materia prima tessile. Il contenuto di cellulosa del legno, invece, è solo del 40-45% circa e deve essere isolato attraverso un complesso processo di digestione chimica. Principalmente i residui di segheria e le conifere di bassa qualità vengono utilizzati come materia prima per il riciclaggio industriale in carta. Tuttavia, per la pasta chimica vengono utilizzati anche legni di conifere e latifoglie di qualità superiore, per lo più provenienti da piantagioni.
Con l'aiuto del processo di digestione al solfito, dal legno si ottiene una cellulosa particolarmente pura. La cellulosa chimica così ottenuta è chiamata anche pasta di dissoluzione o pasta speciale.
Ma prima è necessario sciogliere la cellulosa dal legno. I tronchi vengono tritati e trasformati in trucioli di legno. L'obiettivo è ottenere una dimensione uniforme.
Questi trucioli di legno vengono cotti in reattori resistenti alla pressione con sostanze chimiche acide sotto calore e pressione per diverse ore. Le sostanze che accompagnano la cellulosa, come la lignina e le emicellulose, si dissolvono nell'acido e vengono separate con il filtrato. Il filtrato è chiamato black liquor e contiene residui di lignina, carboidrati derivanti dalla degradazione delle emicellulose, carbonato di sodio, solfato di sodio e altri sali inorganici. Il sodio, lo zolfo e il calcio vengono in gran parte recuperati dal bagno nero e riciclati. La vanillina può essere estratta dalla lignina, simile alla corteccia degli alberi.
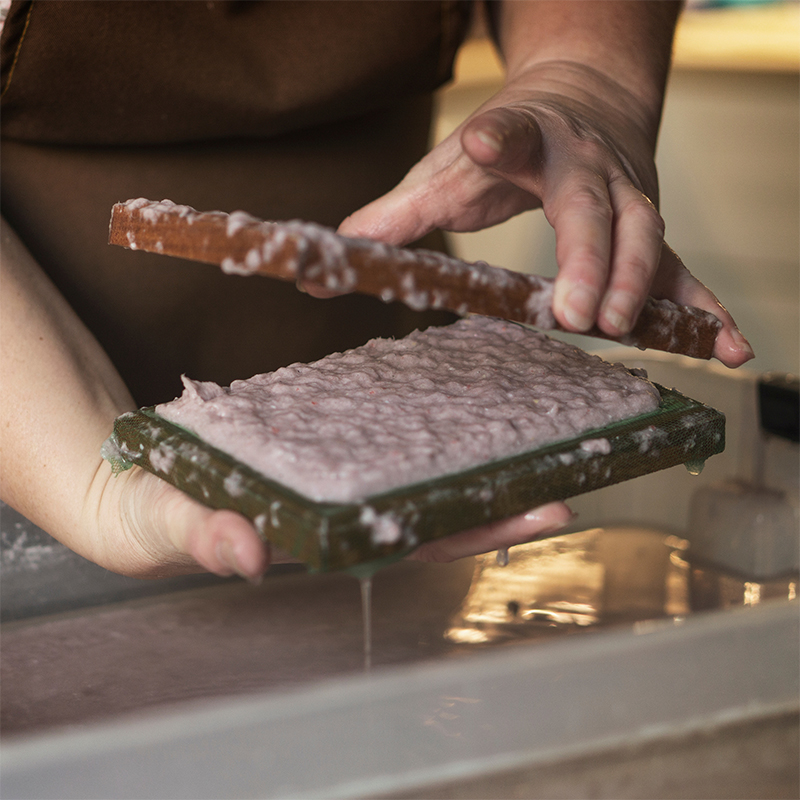
I fanghi di cellulosa vengono disidratati manualmente.
Derivati della cellulosa e loro produzione mondiale nel 2020
Prodotto | Produzione mondiale nel 2019 | Applicazione |
Cellulosa rigenerata | 3.300.000 t/a | Tessile |
Acetato di cellulosa | 900.000 t/a | Rivestimenti e membrane |
Nitrato di cellulosa | 420.000 t/a | Rivestimenti, membrane ed esplosivi |
Carbossimetilcellulosa | 360.000 t/a | Alimentare, cosmetico, farmaceutico, petrolifero, cartaceo |
Metilcellulose | 180.000 t/a | Alimentare, farmaceutico e costruzioni |
Idrossietilcellulosa | 8.000 t/a | Pitture, lacche, pellicole e cosmetici |
Cellulosa etilica | 80 t/a | Farmaceutica, Elettronica |
I derivati della cellulosa si incontrano quasi ovunque
I progressi della chimica macromolecolare hanno portato allo sviluppo di una varietà di derivati della cellulosa con proprietà preziose.
Estere di cellulosa: Nel 1856 è stata prodotta la prima termoplastica a partire da canfora e nitrato di cellulosa. Ne sono scaturite palline da ping pong e materiale cinematografico per la fotografia e le immagini in movimento.
Acetato di cellulosa: A questa è seguita una seconda termoplastica che poteva essere trasformata in schiuma (filtri di sigarette) e in fibre. Ulteriori sviluppi hanno portato a corpi stampati trasparenti, cubi e manici di utensili.
Etere di cellulosa: Dall'inizio degli anni '30, questo gruppo di derivati della cellulosa ha acquisito la sua importanza industriale, un corteo trionfale che continua ancora oggi con una gamma di applicazioni sempre più ampia. Gli eteri di cellulosa sono prodotti non tossici, per lo più solubili in acqua, solitamente commercializzati come polveri o granuli bianchi. Le proprietà specifiche dei singoli eteri di cellulosa dipendono dal tipo, dal numero e dalla distribuzione dei sostituenti introdotti da una reazione chimica dopo l'attivazione della molecola di cellulosa con una soluzione di idrossido di sodio.
Raffreddamento continuo con ghiaccio in scaglie
Il nome è dato dal nome del sostituente, ad es: Metilcellulosa (MC), idrossipropilmetilcellulosa (HPMC), carbossimetilcellulosa (CMC), idrossipropilcellulosa (HPC), etilcellulosa (EC), ecc. Le applicazioni si trovano nell'industria delle costruzioni come additivi per ottimizzare varie proprietà nelle malte, negli adesivi per piastrelle o nei riempitivi (HEMC o HPMC). La pasta per carta da parati è composta principalmente da metilcellulosa (MC) o carbossimetilcellulosa (CMC).
Nella formatura dei metalli, i derivati della cellulosa sono utilizzati come lubrificanti, nella produzione di pitture e vernici come regolatori di viscosità e leganti. Nelle lavastoviglie come esplosivo o in agricoltura per ritardare l'effetto dei pesticidi.
Alcuni derivati della cellulosa sono approvati come additivi alimentari e per l'uso in formulazioni cosmetiche. Tra le altre cose, viene utilizzato il comportamento dei diversi eteri di cellulosa in ambiente acquoso a diverse temperature. Sono spesso additivi indispensabili negli emulsionanti, negli stabilizzatori e nei conservanti. Migliorano la fluidità di salse e zuppe istantanee. Nel gelato, influenzano il comportamento di fusione e la sensazione in bocca e conferiscono un gusto cremoso nonostante la riduzione della crema.
Nell'industria alimentare e farmaceutica, influenzano la consistenza, la forma, la struttura e l'omogeneità dei prodotti liquidi e semisolidi. Le loro applicazioni spaziano dai dentifrici ai composti di rivestimento per i farmaci. In cosmetica servono come regolatori di viscosità e stabilizzatori, determinano la reologia di unguenti, creme solari e make-up. Il loro potenziale è lungi dall'essere esaurito ed è oggetto di intense ricerche.
Il prezzo dei derivati della cellulosa "semplici", come la carbossimetilcellulosa (CMC), parte da 1,50 €/kg e sale a oltre 100 €/kg per i derivati speciali della cellulosa nelle applicazioni farmaceutiche. In molte applicazioni gli eteri di cellulosa sono difficilmente sostituibili con prodotti a base di petrolio. Ciò aumenterà la loro importanza in vari settori industriali. In particolare, in molte applicazioni farmaceutiche o come additivi alimentari, soprattutto per i prodotti convenience.
Eteri di cellulosa e loro applicazioni nell'industria
Nome | Abbreviazione | Produzione | Applicazione |
Carbossimetilcellulosa | CMC | Convertita in cellulosa alcalina con soluzione di idrossido di sodio. Alchilazione con acido cloroacetico. | Industria petrolifera, industria tessile, additivo per detergenti, legante, addensante, appretto per carta (pasta per carta da parati), colloide protettivo, additivo alimentare E 466 (gelati, mayo, gelatina, prodotti da forno), dentifricio, reticolato come disintegrante per compresse. |
Metilcellulose | MC HEMC HPMC | Convertita in cellulosa alcalina con soluzione di idrossido di sodio. Alchilazione con cloruro di metile, Eterificazione con Ossido di etilene o Ossido di propilene | Additivi in vari materiali da costruzione (calcestruzzo, malta, adesivi per piastrelle, riempitivi, intonaci, ecc.) Pasta per carta da parati, addensante, agente gelificante e di rivestimento, emulsionante, stabilizzante negli alimenti (MC: E 461, HPMC: E 464) sostituti della carne, gelati, prodotti da forno, mayo, prodotti istantanei e prodotti surgelati) e cosmetici. In farmacia come "lacrime artificiali", lassativo, agente di contrasto negativo, ritardante di principi attivi, rivestimento di compresse, materiale per capsule rigide. |
Cellulosa etilica | EC | Convertita in cellulosa alcalina con soluzione di idrossido di sodio. Alchilazione con cloruro di etile. | Addensante, legante, adesivo, nonché film former e strato barriera idrorepellente. Ingrediente principale rivestimenti in etere di cellulosa resistenti alla luce, materiali da imballaggio, termoplastici, neve artificiale per alberi di Natale, isolamento di cavi, pelli protettive e guarnizioni. Come additivo di resine sintetiche e cere per la verniciatura di uova di Pasqua colorate e come additivo per gli inchiostri da stampa nell'industria alimentare (E 462). In farmacia, eccipiente per aumentare la viscosità, come legante per i granuli di compresse, come costruttore e disintegratore per le compresse e, in particolare, come film former (ad esempio con il marchio Surelease®) per le compresse laccate. |
Idrossietilcellulosa | HEC | Convertita in cellulosa alcalina con soluzione di idrossido di sodio. Eterificazione con ossido di etilene. | Nell'industria dei materiali da costruzione, nelle vernici idrosolubili e negli adesivi in dispersione, nonché negli intonaci e negli stucchi. Nei prodotti farmaceutici come eccipiente e nei dentifrici. |
Idrossipropilcellulosa | HPC | Convertita in cellulosa alcalina con soluzione di idrossido di sodio. Eterificazione con ossido di propilene. | Applicazione come eccipiente farmaceutico, legante per masse ceramiche, per rivestimenti e adesivi, in articoli cosmetici, in inchiostri da stampa e nella tecnologia di polimerizzazione. Negli alimenti come stabilizzante, strato protettivo e rivestimento lucido. |
© Copyright by amixon GmbH