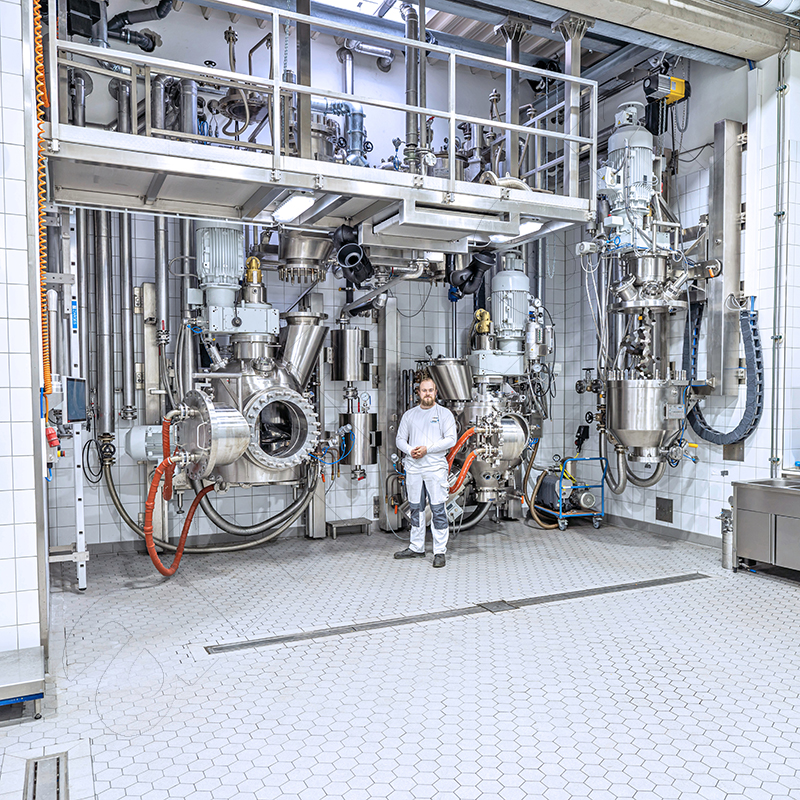
Technique d'installation complexe lors du traitement de la méthylcellulose, de la carboxyméthylcellulose, de l'hydroxyéthylcellulose, etc.
La pâte à papier est la masse fibreuse qui résulte de la décomposition chimique des fibres végétales. La pâte à papier est principalement composée de cellulose. Le mot vient du latin et signifie petite cellule. La cellulose est la structure statique de base de toutes les cellules végétales.
Dérivés de la cellulose : sous une forme chimiquement modifiée - par exemple sous forme de méthylcellulose -, elle a rendu possible le développement de la photographie. Elle est un composant important des fibres textiles. Elle aide à la pose de carreaux, conserve la fraîcheur des produits de boulangerie, donne sa consistance à la mayonnaise et rend le dentifrice souple.
Processus de réaction complexes pour la carboylméthylcellulose
L'éther de cellulose le plus important en termes de quantité est la carboylméthylcellulose (CMC). La cellulose purifiée provenant du bois ou du coton est broyée en une poudre fine (taille des particules : environ 100 à 200 μm) et transportée pneumatiquement dans un mélangeur de grande capacité de 10 à 30 m³.
De là, la pâte homogénéisée est transportée vers un réacteur de synthèse. De la soude caustique à 50 % est injectée dans le réacteur. La réaction exothermique produit de la cellulose de sodium. De l'acide chloracétique est ensuite pulvérisé dans le réacteur. Il en résulte de la carboxyméthylcellulose. Au choix, la synthèse de CMC sous forme de slurry peut être réalisée sans, ou avec solvant (isopronanol ou éthanol).
D'autres dérivés de la cellulose (par exemple, l'hydroxypropylméthylcellulose) sont produits de manière similaire. Sauf qu'ici, on n'utilise généralement pas de solvants et que les produits chimiques de réaction sont gazeux (chlorure de méthyle, oxyde de propylène ou oxyde d'éthylène). La transformation de la matière nécessite alors des pressions relativement élevées dans le système (jusqu'à 20 bars) afin de garantir que les éduits gazeux restent dans le système à des températures élevées.
Les réacteurs destinés à la production de dérivés de cellulose sont conçus pour résister à la pression. Ils sont également dotés d'une double enveloppe afin de pouvoir chauffer ou refroidir leur contenu. Les plus grands réacteurs disposent en outre d'autres systèmes de refroidissement dans les superstructures ainsi que parallèlement aux réacteurs.
(1) amixon ® mélangeur à cône mélange de manière discontinue
Lors de la dernière étape du processus, le produit est broyé et séché dans des séchoirs électriques. Le séchage se fait de manière atmosphérique. Les matières sèches produites sont collectées et homogénéisées dans de grands mélangeurs avant d'être conditionnées en sacs ou en big-bags.
La matière première qu'est la cellulose est un produit naturel renouvelable. Comme tous les produits naturels, la matière première est soumise à des variations saisonnières et locales. De plus, la préparation de la substance se fait par lots. Ici aussi, il y a de légères différences de qualité d'un lot à l'autre. L'une des tâches principales du mélangeur de produits finis à grand volume est de les compenser. Trois méthodes de mélange final sont décrites ci-dessous.
Dans le mélangeur conique amixon®, deux flux opposés se rencontrent. À l'extérieur, l'enrobé est transporté en hélice vers le haut, tandis qu'au centre, c'est le flux descendant qui prédomine. Dans les zones limites, un changement de place a lieu au sein du système de particules. Les bras du mélangeur, en forme de pale, génèrent des flux transversaux complémentaires. Malgré des fréquences de rotation lentes, des qualités de mélange idéales sont garanties, qui ne peuvent plus être améliorées dans la pratique. L'écoulement total ainsi décrit met constamment toutes les particules en mouvement relatif les unes par rapport aux autres. Elle est présente de manière universelle, que le taux de remplissage soit de 5% ou maximal. La forme particulière de l'hélice de mélange de type "SinConcave®" ou "SinConvex®" garantit une vidange résiduelle de presque 100%. Le traitement particulièrement délicat du matériau à mélanger résulte directement de la faible puissance d'entraînement. Les particules d'enrobé ne sont ni broyées, ni arrondies et/ou cassées.
(2) amixon® mélangeur à cône mélange en continu (3) Le mélangeur Gyrato® mélange au choix en c
L'intérêt de ce type de mélangeur est qu'il peut fonctionner au choix en discontinu ou en continu, quelle que soit sa taille. Mais ce qui est encore plus intéressant, c'est que l'enrobé évacué correspond dès le départ à la qualité de mélange idéale. Il n'y a pas de "pertes au démarrage". C'est ce que nous expliquons ci-dessous :
Méthode de travail au début de la production :
La sortie du mélangeur est fermée. Tous les organes de dosage fonctionnant par gravimétrie sont démarrés simultanément avec un faible débit massique. La commande de dosage maître harmonise tous les flux de produits. Le taux de remplissage du mélangeur augmente continuellement, l'entraînement du mélangeur démarrant à la moitié du taux de remplissage. Ce processus d'équilibrage est terminé lorsque le mélangeur est rempli un peu plus de la moitié. Une fois le degré de remplissage souhaité atteint (environ 60 à 80 % du contenu utile), l'organe d'écoulement s'ouvre lentement. Ce niveau de remplissage est maintenu constant. Le débit de dosage peut être augmenté jusqu'au débit massique maximal sous une régulation permanente.
Mode de fonctionnement en fin de production :
Tous les organes de dosage retardent successivement le débit massique, puis s'arrêtent et se ferment simultanément. Le mélangeur se vide en continu jusqu'au dernier résidu. Les produits coulants s'écoulent complètement.
Les avantages pour l'utilisateur en un coup d'œil :
- qualité de mélange techniquement idéale
- peut être utilisé au choix comme malaxeur discontinu pour les prémélanges ou comme malaxeur continu
- l'intensité du mélange est réglable (de l'homogénéisation douce à la désagglomération intensive)
- Temps de séjour moyen défini du produit mélangé dans le malaxeur sur la base du flux continu de la chaudière. Ceci est indépendant de la vitesse de rotation de l'outil de mélange
- pas de perte de produit au début de la production
- pas de perte de produit en fin de production
- vidage idéal des résidus
- degré de remplissage défini sélectionnable de 10% à 100% du contenu utile
- mélange microfin du liquide sans encrassement du mélangeur
- des processus étendus tels que l'humidification, le tempérage, le séchage,
- Passage de réaction possible - standard d'hygiène le plus élevé (standard GMP) ; nettoyage facile, à sec ou humide - le mélangeur est uniquement logé et entraîné par le haut.
(3) Le mélangeur Gyrato® mélange au choix en continu ou en discontinu.
Pour l'homogénéisation de charges particulièrement importantes, amixon® a créé un nouveau développement intéressant avec le mélangeur Gyraton® : L'hélice de mélange tourne dans le sens des aiguilles d'une montre et transporte l'enrobé vers le haut. Un entraînement supplémentaire déplace la partie inférieure de l'arbre du mélangeur sur une trajectoire circulaire. Le point de pivot se trouve en haut, au milieu du joint d'arbre.
Ce mélangeur peut également être utilisé pour des produits en vrac secs, humides ou même en suspension. Les tailles peuvent être choisies librement de 10 m³ à 100 m³. Des tailles allant jusqu'à 70 m³ peuvent être transportées par la route, entièrement montées.
Les meilleurs résultats de mélange sont déjà obtenus avec un taux de remplissage de 10%. Le mélange se fait de manière extrêmement délicate avec un apport d'énergie extrêmement faible. Le chargement se fait par le haut via une ou plusieurs tubulures normalisées. La vidange du produit mélangé s'effectue vers le bas par une tubulure normalisée lorsque le clapet de fond est ouvert.
Le mélangeur Gyraton® se caractérise par
- Le processus de mélange s'effectue sans espace mort, avec un soin particulier et un apport d'énergie minimal.
- très bonne évacuation des résidus
- en option, résistant à la pression ou au vide
- la chambre de mélange peut être tempérée en option
- construction compacte et peu encombrante. Le grand malaxeur peut être transporté par la route
- la chambre de mélange est facilement accessible grâce à une grande porte d'inspection
- Nettoyage facile
- humide (automatique)
- à sec manuellement avec un aspirateur
- En fonction de la longueur du temps de mélange, qui peut être définie par le client, la fréquence de rotation de l'outil de mélange et le mouvement pendulaire superposé sont adaptés. Les moteurs sont très petits. La consommation d'énergie est donc faible.
- Le système de mélange peut également être utilisé pour les produits humides qui s'écoulent mal.
Essais dans le centre technique amixon
Si vous êtes sur le point de prendre une décision d'investissement dans les domaines du mélange, de l'homogénéisation, de l'agglomération, de la synthèse, du refroidissement ou du mélange-séchage sous vide, vous devriez nous contacter. amixon® propose des solutions exceptionnelles et hautement efficaces. Nous vous offrons un large savoir-faire en matière de procédés et disposons d'un service de construction de machines/appareils remarquablement équipé. Nous nous ferons un plaisir de convenir avec vous d'un rendez-vous à court terme pour des essais dans notre centre technique.
Réfrigération continue avec de la glace écailles
Le produit de la réaction est un dérivé humide de la cellulose, qui contient encore du sel de cuisine et quelques sous-produits (alcools supérieurs). Le produit brut est transféré dans un bain d'eau à 90 °C et mis en suspension. Les sels et les sous-produits se dissolvent dans l'eau chaude. Ce n'est pas le cas de l'éther de cellulose : MC, HEMC et HPMC sont insolubles dans l'eau à des températures supérieures à 50-60 °C.
L'eau de lavage chaude est ensuite séparée par filtration et le gâteau de filtre est lavé sans sel. L'eau de lavage chaude peut être utilisée plusieurs fois pour le nettoyage, car elle peut absorber jusqu'à 30 % de sel de cuisine. Il est donc possible d'économiser de l'énergie et de l'eau. Après l'étape de filtrage et de lavage, l'humidité résiduelle du produit nettoyé est encore d'environ 50 à 60 pour cent. L'éther de cellulose qui, après le lavage, présente encore la densité apparente de la cellulose broyée (env. 150 g/l), est maintenant refroidi de manière ciblée dans un mélangeur-agglomérateur à couche annulaire fonctionnant en continu, par ajout d'eau froide ou de glace écailleuse, jusqu'à une température proche de sa température de solubilité dans l'eau (env. 45°C).
Les grandes masses doivent être séchées de manière efficace et hygiénique.
Les sécheurs à courant utilisés ici sont généralement des broyeurs-sécheurs fonctionnant en continu. Ils sont capables de briser efficacement les agglomérats. Le séchage s'effectue de manière atmosphérique. De grandes quantités d'air sont pré-épurées, séchées et réchauffées. Il faut accorder une grande importance au processus de séchage. Il consomme beaucoup d'énergie.
La poudre séchée est ensuite dépoussiérée dans un cyclone. Les poussières les plus fines sont séparées dans des filtres en tissu. Les particules lourdes sont ensuite triées et tamisées. Une granulométrie définie est importante pour l'application finale.
La cellulose est un produit naturel renouvelable. Comme tous les produits naturels, la pâte à papier est soumise à des variations saisonnières et locales. De plus, la pâte à papier est préparée par lots. Ici aussi, il existe de légères différences de qualité d'un lot à l'autre. L'une des tâches principales du mélangeur final à grand volume est de les compenser. La marchandise est ensuite emballée dans des sacs ou des big-bags.
Les matériaux à haute résistance doivent également être durablement résistants à la corrosion. La technique de soudage revêt ici une grande importance.
En outre, il existe d'autres critères à prendre en compte lors de la conception du réacteur. Ainsi, en plus d'une grande solidité, le matériau du réservoir doit présenter une résistance particulière à la corrosion, car les chlorures des sels qui se forment sont chimiquement agressifs à haute température en combinaison avec l'eau. Le phénomène de corrosion fissurante sous contrainte décrit une diminution de la résistance à la corrosion des matériaux lorsqu'ils sont soumis à une contrainte de traction accrue. En outre, il faut tenir compte du phénomène de fatigue des matériaux dû aux variations de charge et de température.
La manipulation des réactifs et des sous-produits de réaction requiert également un grand savoir-faire. L'oxyde d'éthylène (production d'HEC ou d'éthers mixtes HE comme l'HEMC) présente le potentiel de risque le plus élevé : Il est explosif et doit être stocké sous atmosphère d'azote. Lors de la production de méthylcelluloses (MC, HEMC ou HPMC), une réaction secondaire produit de l'éther diméthylique, qui est facilement inflammable, explosif et toxique. Il doit être évacué à la fin de la réaction en même temps que le chlorure de méthyle qui n'a pas réagi. Dans le processus industriel, le mélange de gaz est récupéré sous pression et, dans le meilleur des cas, réutilisé dans le processus.
La cellulose a de multiples talents
Il n'y a guère d'autre matière première avec laquelle l'histoire de l'humanité soit aussi étroitement liée qu'avec la cellulose. Sans le papier, l'histoire de l'humanité serait différente. Au début, même les chiffons étaient utilisés pour fabriquer du papier. Car ils sont en coton. Dans leurs fibres, la cellulose se trouve sous une forme particulièrement pure.
Le développement de l'utilisation chimique de la cellulose a commencé en 1846 avec la production de nitrocellulose, également appelée trinitrate de cellulose. Il a d'abord été utilisé à des fins militaires et a également été appelé coton de tir. Elle se forme lorsque la cellulose est traitée avec de l'acide nitrique, un mélange d'acide sulfurique et d'acide nitrique. Au cours des étapes suivantes du processus, le coton de trame est lavé, moulu et séché.
Historique
Parallèlement à l'utilisation militaire, l'utilisation civile de la nitrocellulose a commencé au 19e siècle. La nitrocellulose faiblement nitrurée (dinitrate de cellulose) était mélangée à du camphre et constituait, sous forme de celluloïd, la base des premières matières plastiques techniques.
Le celluloïd a servi de support aux films photographiques jusqu'en 1951. Les balles de tennis de table étaient également fabriquées en celluloïd jusqu'en 2014. Le premier film plastique transparent était également à base de cellulose. Dans les années 1920, le cellophane (nom de marque : cellophane) à des fins d'emballage. Il est particulièrement brillant et, contrairement aux films d'emballage modernes, il peut être plié de manière durable. Il était par exemple utilisé comme emballage de bonbons, car il pouvait facilement être "twisté" aux deux extrémités. Entre-temps, la cellophane a été largement remplacée par des films plastiques à base d'huile pour des raisons de prix et de technique. Une renaissance du cellophane pourrait toutefois être justifiée à l'avenir par son excellente biodégradabilité.
Il y a une raison importante pour laquelle le celluloïd a été remplacé par d'autres matières plastiques. C'est la facilité d'inflammation du celluloïd.
La cellulose est biodégradable
La teneur en cellulose du coton est d'environ 84-91%. En raison de la longueur de ses fibres, il est principalement utilisé comme matière première textile. En revanche, la teneur en cellulose du bois n'est que d'environ 40-45% et doit être isolée par une décomposition chimique complexe. Ce sont surtout les résidus de scierie et les résineux de moindre qualité qui sont utilisés comme matière première pour la valorisation industrielle en papier. Mais des qualités supérieures de résineux et de feuillus, généralement issus de plantations, sont également utilisées pour la pâte chimique.
Le procédé de digestion au sulfite permet d'obtenir une cellulose particulièrement pure à partir du bois. La cellulose chimique ainsi obtenue est également appelée pulpe de dissolution ou pâte spéciale.
Mais il faut d'abord extraire la cellulose du bois. Les troncs sont réduits en copeaux. L'objectif est de parvenir à une taille uniforme.
Ces copeaux de bois sont cuits dans des réacteurs résistants à la pression avec des produits chimiques acides sous l'effet de la chaleur et de la pression pendant plusieurs heures. Les substances accompagnant la cellulose, comme la lignine et les hémicelluloses, se dissolvent dans l'acide et sont séparées avec le filtrat. Le filtrat est appelé liqueur noire et contient des résidus de lignine, des hydrates de carbone issus de la dégradation des hémicelluloses, du carbonate de sodium, du sulfate de sodium et d'autres sels inorganiques. Le sodium, le soufre et le calcium sont en grande partie récupérés et recyclés à partir de la liqueur noire. La vanilline peut être extraite de la lignine, comme de l'écorce d'arbre.
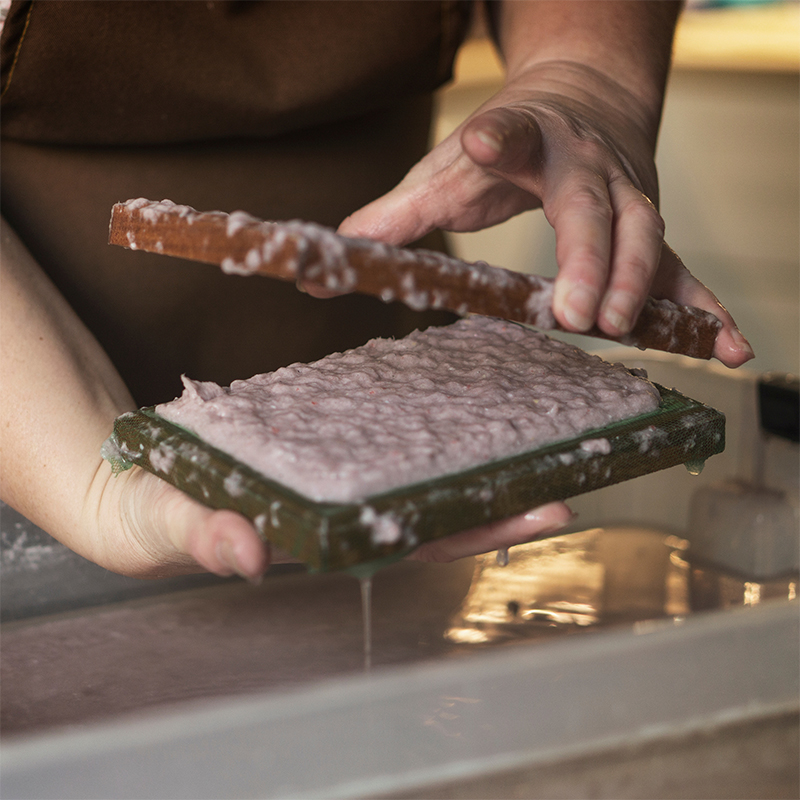
Les boues de cellulose sont déshydratées manuellement.
Dérivés de la cellulose et leur production mondiale en 2020
Produit | Production mondiale en 2019 | Application |
Cellulose régénérée | 3.300.000 t/a | Textiles |
Acétate de cellulose | 900.000 t/a | Revêtements et membranes |
Nitrate de cellulose | 420.000 t/a | Revêtements, membranes et explosifs |
Carboxyméthyl-cellulose | 360.000 t/a | Alimentation, cosmétique, pharmaceutique, champ pétrolifère, papier |
Méthylcelluloses | 180.000 t/a | Alimentation, pharmacie et construction |
Hydroxyléthylcellulose | 8.000 t/a | Peintures, vernis, films et cosmétiques |
Éthylcellulose | 80 t/a | Pharmaceutique, électronique |
Les dérivés de la cellulose se retrouvent presque partout
Les progrès de la chimie macromoléculaire ont permis de développer une multitude de dérivés de la cellulose aux propriétés précieuses.
Esters de cellulose: En 1856, le premier plastique thermoplastique a été fabriqué à partir de camphre et de nitrate de cellulose. Il en a résulté des balles de ping-pong et du matériel cinématographique pour la photographie et les images animées.
Acétate de cellulose: Il a été suivi d'un deuxième thermoplastique qui pouvait être transformé en mousse (filtres de cigarettes) et en fibres. Des développements ultérieurs ont conduit à des corps moulés transparents, des cubes et des poignées d'outils.
Éther de cellulose: Depuis le début des années 30, ce groupe de dérivés de la cellulose a pris son importance industrielle, un triomphe qui se poursuit encore aujourd'hui et qui présente un spectre d'applications toujours plus large. Les éthers de cellulose sont des produits non toxiques, généralement solubles dans l'eau, qui sont généralement commercialisés sous forme de poudre ou de granulés blancs. Les propriétés spécifiques de chaque éther de cellulose dépendent du type, du nombre et de la répartition des substituants introduits par une réaction chimique après activation de la molécule de cellulose avec de la soude caustique.
Domaines d'application
Le nom est donné en mentionnant le substituant, par ex : Méthylcellulose (MC), hydroxypropylméthylcellulose (HPMC), carboxyméthylcellulose (CMC), hydroxypropylcellulose (HPC), éthylcellulose (EC), etc. Les domaines d'application se trouvent dans l'industrie du bâtiment en tant qu'additifs pour optimiser différentes propriétés dans les mortiers, les colles à carrelage ou les enduits (HEMC ou HPMC). La colle à papier peint est principalement composée de méthylcellulose (MC) ou de carboxyméthylcellulose (CMC).
Les dérivés de la cellulose sont utilisés comme lubrifiants dans le formage des métaux et comme régulateurs de viscosité et liants dans la fabrication de peintures et de vernis. Dans les tablettes de lave-vaisselle comme explosif ou dans l'agriculture pour retarder l'action des produits phytosanitaires.
Certains dérivés de la cellulose sont autorisés comme additifs alimentaires et pour une utilisation dans des formulations cosmétiques. On utilise entre autres le comportement des différents éthers de cellulose dans un environnement aqueux à différentes températures. Ils sont souvent des additifs indispensables dans les émulsifiants, les stabilisants et les conservateurs. Ils améliorent la fluidité des sauces et des soupes instantanées. Dans les glaces, ils influencent le comportement de la fonte ainsi que la sensation en bouche et confèrent à la glace un goût crémeux et crémeux malgré la réduction de la crème.
Dans l'industrie alimentaire et pharmaceutique, ils influencent la texture, la forme, la structure et la consistance des produits liquides et semi-solides. Leur domaine d'application va du dentifrice aux masses d'enrobage pour les médicaments. Dans les cosmétiques, ils servent de régulateurs de viscosité et de stabilisateurs, ils déterminent la rhéologie des pommades, des crèmes solaires et du maquillage. Leur potentiel est loin d'être épuisé et fait l'objet de recherches intensives.
Le prix des dérivés de cellulose "simples" comme la carboxyméthylcellulose (CMC) commence à 1,50 €/kg et augmente jusqu'à plus de 100 €/kg pour les dérivés de cellulose spéciaux utilisés dans les applications pharmaceutiques. Dans de nombreuses applications, les éthers de cellulose sont difficilement substituables par des produits à base de pétrole. Cela augmentera leur importance dans différentes industries. Notamment dans de nombreuses applications pharmaceutiques ou comme additifs alimentaires, surtout pour les produits de commodité.
Les éthers de cellulose et leurs applications dans l'industrie
Nom | Abréviation | Production | Application |
Carboxyméthylcellulose | CMC | Transformé en cellulose alcaline avec de la soude caustique. Alkylation avec l'acide chloroacétique. | Industrie pétrolière, industrie textile, additif pour lessive, liant, épaississant, agent de collage du papier (colle à papier peint), colloïde de protection, additif alimentaire E 466 (glace, mayo, gelée, pâtisserie), dentifrice, réticulé comme agent de dispersion des comprimés |
Méthylcelluloses | MC HEMC HPMC | Transformé en cellulose alcaline avec de la soude caustique. Alkylation par le chlorure de méthyle, Ethérification avec oxyde d'éthylène ou Oxyde de propylène | Additifs dans différents matériaux de construction (béton, mortier, colle à carreaux, enduits, crépis, etc.) Colle à papier peint, épaississant, gélifiant et agent d'enrobage, émulsifiant, stabilisateur dans les aliments (MC : E 461, HPMC : E 464) substituts de viande, glaces, pâtisseries, mayonnaise, produits instantanés et surgelés) et les cosmétiques. En pharmacie comme "liquide lacrymal artificiel", laxatif, agent de contraste négatif, retardement de substances actives, enrobage de comprimés, matériau pour capsules dures. |
Éthylcellulose | EC | Transformé en cellulose alcaline avec de la soude caustique. Alkylation par le chlorure d'éthyle. | Agent épaississant, liant, adhésif, ainsi que filmogène et couche barrière hydrofuge. Composant principal des vernis d'éthers cellulosiques résistants à la lumière, des matériaux d'emballage, des thermoplastiques, de la neige artificielle pour les sapins de Noël, des isolations de câbles, des peaux de protection et des joints. Comme additif de résines synthétiques et de cires pour le vernissage d'œufs de Pâques colorés et comme additif pour les encres à tampon dans l'industrie alimentaire (E 462). En pharmacie, excipient pour augmenter la viscosité, comme liant pour les granulés de comprimés, comme adjuvant et agent de désintégration pour les comprimés ainsi que, en particulier, comme agent filmogène (p. ex. protégé par le droit des marques sous le nom de Surelease®) pour les comprimés vernis. |
Hydroxyéthylcellulose | HEC | Transformé en cellulose alcaline avec de la soude caustique. éthérification à l'oxyde d'éthylène. | Dans l'industrie des matériaux de construction, dans les peintures et les colles à dispersion solubles dans l'eau ainsi que dans les enduits et les mastics. Dans les produits pharmaceutiques comme excipient et dans les dentifrices. |
Hydroxypropylcellulose | HPC | Transformé en cellulose alcaline avec de la soude caustique. éthérification avec de l'oxyde de propylène. | Utilisation comme excipient pharmaceutique, liant pour les masses céramiques, pour les revêtements et les colles, dans les produits cosmétiques, dans les encres d'impression et dans la technique de polymérisation. Dans les aliments, comme stabilisateur, couche protectrice et revêtement brillant. |
© Copyright by amixon GmbH