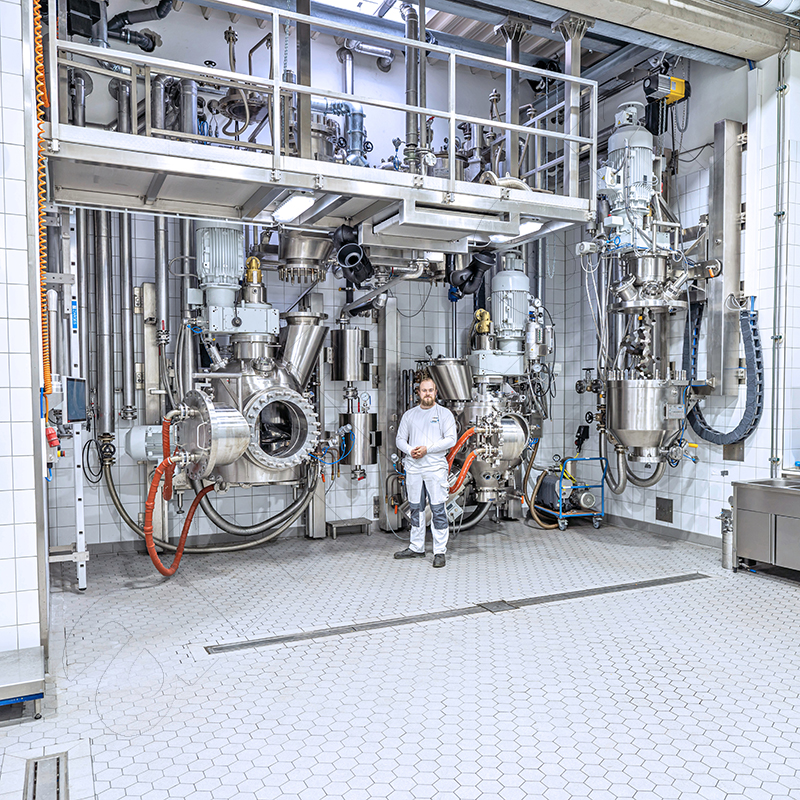
Tecnología vegetal compleja en la preparación de metilcelulosa, carboximetilcelulosa, hidroxietilcelulosa, etc.
La pulpa es la masa fibrosa producida durante el despulpado químico de las fibras vegetales. La pulpa se compone principalmente de celulosa. La palabra procede del latín y significa célula pequeña. La celulosa es la estructura estática básica de todas las células vegetales.
Derivados de la celulosa: en forma modificada químicamente -por ejemplo, como metilcelulosa- hizo posible el desarrollo de la fotografía en un principio. Es un componente importante de las fibras textiles. Ayuda a colocar baldosas, mantiene frescos los productos de panadería, da consistencia a la mayonesa y suaviza la pasta de dientes.
Procesos de reacción complejos para la carboximetilcelulosa
El éter de celulosa más importante en términos de cantidad es la carboximetilcelulosa (CMC). La celulosa purificada de madera o algodón se tritura hasta obtener un polvo fino (tamaño de partícula de 100 a 200 μm aproximadamente) y se transporta neumáticamente a una mezcladora de gran volumen de 10 a 30 m³.
A partir de ahí, la pulpa homogeneizada se transporta a un reactor de síntesis. Se rocía un 50% de sosa cáustica en el reactor. La reacción exotérmica produce celulosa sódica. A continuación, se pulveriza ácido cloroacético en el reactor. Esto produce carboxilmetilcelulosa. Opcionalmente, la síntesis de CMC puede llevarse a cabo en forma de suspensión sin disolvente o con disolvente (isopronanol o etanol).
Otros derivados de la celulosa (por ejemplo, la hidroxipropilmetilcelulosa) se producen de forma similar. La única diferencia es que aquí no suelen utilizarse disolventes y los productos químicos de reacción son gaseosos (cloruro de metilo, óxido de propileno u óxido de etileno). La conversión de sustancias requiere entonces presiones del sistema comparativamente altas (hasta 20 bares) para garantizar que los reactantes gaseosos permanezcan en el sistema a altas temperaturas.
Los reactores para la producción de derivados de la celulosa están diseñados para ser resistentes a la presión. También están equipados con una doble camisa para poder calentar o enfriar el contenido. Los reactores más grandes también tienen sistemas de refrigeración adicionales en las superestructuras y paralelos a los reactores.
amixon® ofrece tres métodos de homogeneización de gran volumen: (1), (2) y (3):
(1) el mezclador cónico amixon® mezcla de forma discontinua
En la última fase del proceso, el producto se tritura y se seca en secadores mecánicos. El secado se realiza por vía atmosférica. El material seco producido se recoge en grandes mezcladoras y se homogeneiza antes de introducirse en bolsas o BigBags.
La pasta de papel es un producto natural renovable. Como todos los productos naturales, la materia prima también está sujeta a fluctuaciones estacionales y relacionadas con el emplazamiento. Además, la sustancia se prepara por lotes. También en este caso hay ligeras diferencias de calidad de un lote a otro. Equilibrarlos es una de las principales tareas del mezclador de productos finales de gran volumen. A continuación se describen 3 métodos de mezcla final.
Dos flujos opuestos se encuentran en el mezclador cónico amixon®. En el exterior, la mezcla se transporta hacia arriba en forma helicoidal, mientras que en el centro predomina el flujo hacia abajo. En las zonas fronterizas se produce un cambio de lugar dentro del sistema de partículas. Los brazos mezcladores en forma de pala generan flujos transversales complementarios. A pesar de las bajas frecuencias de rotación, se garantizan unas cualidades de mezcla ideales que ya no pueden mejorarse en la práctica. El flujo total descrito de este modo pone constantemente a todas las partículas en movimiento relativo entre sí. Está disponible universalmente, independientemente de si el nivel de llenado es del 5% o del máximo. La forma especial de la hélice mezcladora en diseño "SinConcave®" o "SinConvex®" garantiza una descarga residual de casi el 100%. El tratamiento especialmente cuidadoso del material a mezclar es consecuencia directa de la baja potencia de accionamiento. Las partículas de la mezcla no están trituradas ni redondeadas y/o rotas.
(2) El mezclador cónico amixon® mezcla de forma continua
Lo interesante de este tipo de mezcladora es que puede funcionar de forma discontinua o continua, independientemente de su tamaño. Pero aún más interesante es que la mezcla descargada corresponde desde el principio a la calidad de mezcla ideal. No hay "pérdidas iniciales". Esto se explica a continuación:
Modo de funcionamiento al inicio de la producción:
La salida del mezclador está cerrada. Todos los dosificadores de funcionamiento gravimétrico se ponen en marcha simultáneamente con un caudal másico bajo. El control maestro de dosificación armoniza todos los flujos de producto. El nivel de llenado de la mezcladora aumenta de forma continua, comenzando el accionamiento de la mezcladora a la mitad del nivel de llenado. Este proceso de ecualización se completa cuando el mezclador está ligeramente más lleno de la mitad. Una vez alcanzado el nivel de llenado deseado (aprox. 60 a 80 % del volumen útil), el órgano de salida se abre lentamente. Este nivel de llenado se mantiene constante. El caudal de dosificación puede aumentarse bajo control constante hasta el caudal másico máximo.
Modo de funcionamiento al final de la producción:
Todos los elementos de medición desaceleran el caudal másico uno tras otro y, a continuación, se desconectan y cierran simultáneamente. La mezcladora se vacía continuamente hasta el último residuo. Los productos de flujo libre salen completamente.
Las ventajas para el usuario de un vistazo:
- Calidad de mezcla técnicamente ideal
- Puede funcionar como mezcladora discontinua para premezclas o como mezcladora continua
- La intensidad de mezcla es ajustable (homogeneización suave a desaglomeración intensiva)
- Tiempo medio de permanencia definido del material mezclado en la mezcladora en función del caudal continuo de la caldera. Esto es independiente de la velocidad de la herramienta de mezcla
- Sin pérdida de producto al inicio de la producción
- Sin pérdida de producto al final de la producción
- Descarga residual ideal
- Nivel de llenado definido y seleccionable del 10% al 100% de la capacidad útil
- Mezcla microfina del líquido sin contaminación de la mezcladora
- Procesos avanzados como la humidificación, el templado y el secado,
- Reacción posible - máximo nivel de higiene (norma GMP); limpieza fácil, en seco o en húmedo - la mezcladora sólo se monta y acciona por la parte superior.
(3) El mezclador Gyrato® mezcla de forma continua o discontinua.
Para la homogeneización de lotes especialmente grandes, amixon® ha creado una interesante novedad con el mezclador Gyraton®: La espiral mezcladora gira en el sentido de las agujas del reloj y transporta la mezcla hacia arriba. Un accionamiento adicional mueve la parte inferior del eje mezclador en una trayectoria circular. El punto de giro está situado en el centro superior del cierre del eje.
Esta mezcladora también puede utilizarse para materiales a granel secos, húmedos o en suspensión. Los tamaños se pueden elegir libremente entre 10 m³ y 100 m³. Los tamaños de hasta 70 m³ pueden transportarse completamente montados por carretera.
Los mejores resultados de mezcla se consiguen ya con un nivel de llenado del 10%. La mezcla se realiza con extrema suavidad y con un aporte de energía extremadamente bajo. La alimentación se realiza desde arriba a través de una o varias boquillas estándar. El vaciado del material mezclado se realiza con la trampilla inferior abierta a través de un vertedor estándar orientado hacia abajo.
La mezcladora Gyraton® se caracteriza por
- El proceso de mezcla tiene lugar sin espacios muertos, de forma especialmente suave y con un aporte mínimo de energía.
- Muy buen vaciado residual
- opcionalmente resistentes a la presión o al vacío
- opcionalmente, la cámara de mezcla puede regularse en función de la temperatura
- diseño compacto que ahorra espacio. La gran hormigonera puede transportarse por carretera
- la cámara de mezcla es fácilmente accesible a través de una gran puerta de inspección
- Fácil limpieza
- húmedo (automático)
- secado manual con aspiradora
- En función de la duración del tiempo de mezcla, que puede especificar el cliente, se ajustan la frecuencia de rotación de la herramienta de mezcla y el movimiento pendular superpuesto. Los motores son muy pequeños. En consecuencia, el consumo de energía es bajo.
- El sistema de mezcla también puede utilizarse para productos húmedos y poco fluidos.
Pruebas en el centro técnico amixon
Si se enfrenta a una decisión de inversión en las áreas de mezcla, homogeneización, aglomeración, síntesis, refrigeración o secado de mezclas al vacío, debería hablar con nosotros. amixon® ofrece soluciones excepcionales y altamente eficaces. Le ofrecemos amplios conocimientos de ingeniería de procesos y contamos con un departamento de construcción de máquinas y equipos excelentemente equipado. Estaremos encantados de concertar una cita con usted a corto plazo para realizar pruebas en nuestro centro técnico.
Refrigeración continua con hielo en escamas
El producto de reacción es un derivado húmedo de la celulosa que aún contiene sal común y algunos subproductos (alcoholes superiores). El producto bruto se transfiere a un baño de agua a 90 °C y se suspende. Las sales y los subproductos se disuelven en el agua caliente. Pero no el éter de celulosa: MC, HEMC y HPMC son insolubles en agua a temperaturas superiores a 50-60 °C.
A continuación, el agua de lavado caliente se separa por filtración y la torta de filtración se lava para eliminar la sal. El agua de lavado caliente puede utilizarse varias veces para la limpieza, ya que puede absorber hasta un 30% de sal común. En este sentido, se puede ahorrar energía y agua. La humedad residual del producto limpio tras la fase de filtrado y lavado sigue siendo de entre el 50% y el 60%. El éter de celulosa, que tras el lavado sigue teniendo la densidad aparente de la celulosa molida (aprox. 150 g/l), se enfría ahora selectivamente en un aglomerador mezclador de capa anular de funcionamiento continuo mediante la adición de agua fría o hielo en escamas hasta cerca de su temperatura de solubilidad en agua (aprox. 45°C).
Las grandes masas deben secarse de forma eficaz e higiénica
Los secadores rápidos utilizados en este caso suelen ser secadores de molienda de funcionamiento continuo. Son capaces de romper los aglomerados de forma eficaz. El proceso de secado es atmosférico. Grandes volúmenes de aire se limpian previamente, se secan y se calientan. El proceso de secado es muy importante. Consume mucha energía.
A continuación, el polvo seco se desempolva en un ciclón. El polvo más fino se separa en filtros de tela. A continuación, las partículas pesadas se separan y se tamizan. Un tamaño de partícula definido es importante para la aplicación final.
La pasta de papel es un producto natural renovable. Como todos los productos naturales, la pasta también está sujeta a fluctuaciones estacionales y relacionadas con el emplazamiento. La pasta también se procesa por lotes. También en este caso hay ligeras diferencias de calidad de un lote a otro. Una de las principales tareas de la mezcladora final de gran volumen es igualar estas diferencias. A continuación, la mercancía se envasa en sacos o big bags.
Los materiales de alta resistencia también deben ser permanentemente resistentes a la corrosión. La tecnología de la soldadura tiene aquí una gran importancia.
Además, hay otros criterios que deben tenerse en cuenta a la hora de diseñar el reactor. Por ejemplo, además de una gran resistencia, el material del recipiente debe tener una resistencia especial a la corrosión, ya que los cloruros de las sales que se forman son químicamente agresivos a altas temperaturas en combinación con el agua. El fenómeno del agrietamiento por corrosión bajo tensión describe una disminución de la resistencia a la corrosión de los materiales cuando se someten a un aumento de la tensión de tracción. Además, hay que tener en cuenta el fenómeno de la fatiga del material debido a los cambios de carga y temperatura.
La manipulación de reactivos y subproductos de reacción también requiere muchos conocimientos técnicos. El óxido de etileno tiene el mayor potencial de peligro (producción de HEC o éteres mixtos HE como HEMC): Es explosivo y debe almacenarse en atmósfera de nitrógeno. Durante la producción de metilcelulosas (MC, HEMC o HPMC), se forma éter dimetílico en una reacción secundaria, que es altamente inflamable, explosiva y tóxica. Debe descargarse al final de la reacción junto con el cloruro de metilo sin reaccionar. En el proceso industrial, la mezcla de gases se recoge a presión y, en el mejor de los casos, se reutiliza en el proceso.
La celulosa es un multitalento
Casi ninguna otra materia prima está tan estrechamente ligada a la historia de la humanidad como la celulosa. Sin papel, la historia de la humanidad sería diferente. Al principio, incluso se utilizaban trapos para fabricar papel. Porque están hechos de algodón. En sus fibras, la celulosa está presente en una forma particularmente pura.
El desarrollo del uso químico de la celulosa comenzó en 1846 con la producción de nitrocelulosa, también llamada trinitrato de celulosa. Se utilizó por primera vez con fines militares y también se denominó algodón para armas. Se forma cuando la celulosa se trata con ácido nitrante, una mezcla de ácido sulfúrico y ácido nítrico. En otras fases del proceso, el algodón pistola se lava, se muele y se seca.
Historia
Paralelamente al uso militar, el uso civil de la nitrocelulosa comenzó en el siglo XIX. La nitrocelulosa débilmente nitratada (dinitrato de celulosa) se mezcló con alcanfor y constituyó la base de los primeros plásticos técnicos como el celuloide.
El celuloide sirvió de soporte para películas fotográficas hasta 1951. Las pelotas de tenis de mesa también se fabricaban con celuloide hasta 2014. La primera película de plástico transparente también se basaba en la celulosa. En la década de 1920, el celofán (marca: El celofán) se fabrica con fines de envasado. Es especialmente brillante y, a diferencia de las películas de envasado modernas, puede plegarse permanentemente. Se utilizaba, por ejemplo, como envoltorio de caramelos porque se podía "retorcer" bien por ambos extremos. Entretanto, el celofán ha sido sustituido en gran medida por películas de plástico derivadas del petróleo por razones técnicas y de precio. Sin embargo, el renacimiento del celofán podría justificarse en el futuro por su excelente biodegradabilidad.
Hay una razón importante por la que el celuloide fue sustituido por otros plásticos. Se trata de la fácil inflamabilidad del celuloide.
La celulosa es biodegradable
El contenido de celulosa del algodón es de aproximadamente 84-91%. Debido a sus largas fibras, se procesa principalmente como materia prima textil. En cambio, el contenido de celulosa de la madera es de sólo un 40-45% aproximadamente y debe aislarse mediante un complejo proceso de digestión química. Principalmente, los residuos de aserradero y las maderas blandas de baja calidad se utilizan como materia prima para el reciclado industrial en papel. Sin embargo, para la fabricación de pasta química también se utilizan maderas blandas y duras de mayor calidad, procedentes en su mayoría de plantaciones.
Con ayuda del proceso de digestión con sulfito, se obtiene de la madera una celulosa especialmente pura. La celulosa química obtenida de este modo también se denomina pasta disolvente o pasta especial.
Pero primero hay que disolver la celulosa de la madera. Los troncos se cortan en astillas. El objetivo es conseguir un tamaño uniforme.
Estas astillas de madera se cuecen en reactores resistentes a la presión con productos químicos ácidos bajo calor y presión durante varias horas. Las sustancias acompañantes de la celulosa, como la lignina y las hemicelulosas, se disuelven en el ácido y se separan con el filtrado. El filtrado se denomina licor negro y contiene residuos de lignina, hidratos de carbono procedentes de la degradación de las hemicelulosas, carbonato sódico, sulfato sódico y otras sales inorgánicas. El sodio, el azufre y el calcio se recuperan en gran parte del licor negro y se reciclan. La vainillina puede extraerse de la lignina, similar a la corteza de los árboles.
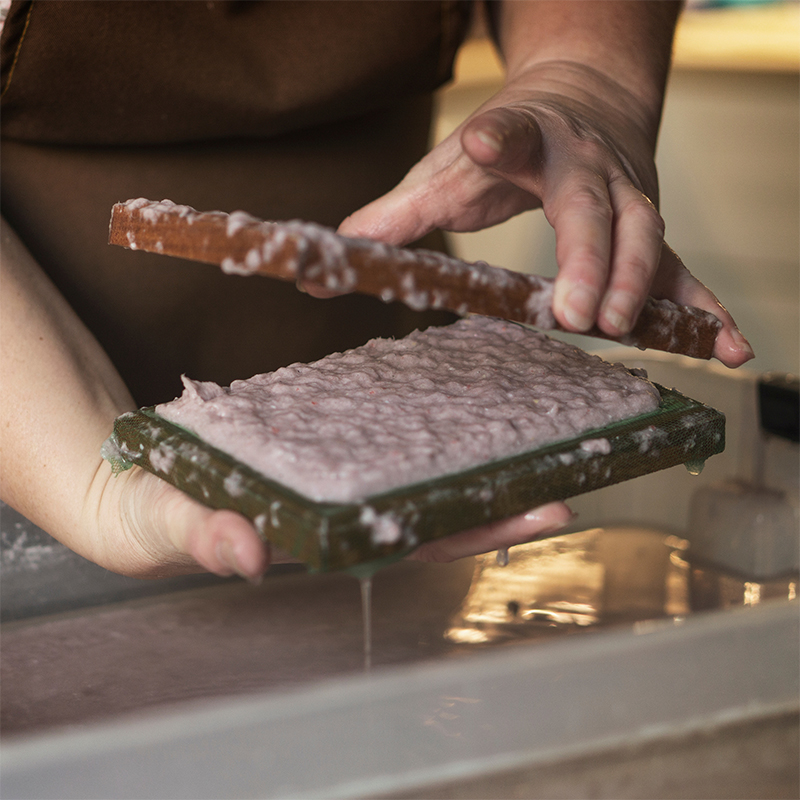
Los lodos de celulosa se deshidratan manualmente.
Derivados de la celulosa y su producción mundial en 2020
Producto | Producción mundial en 2019 | Aplicación |
Celulosa regenerada | 3.300.000 t/a | Textiles |
Acetato de celulosa | 900.000 t/a | Revestimientos y membranas |
Cellulosenitrat | 420.000 t/a | Revestimientos, membranas y explosivos |
Carboximetilcelulosa | 360.000 t/a | Alimentación, Cosmética, Farmacia, Yacimientos Petrolíferos, Papel |
Metilcelulosas | 180.000 t/a | Alimentación, farmacia y construcción |
Hidroxiletilcelulosa | 8.000 t/a | Pinturas, lacas, películas y cosméticos |
Encontramos derivados de la celulosa en casi todas partes
Los avances de la química macromolecular permitieron desarrollar diversos derivados de la celulosa con valiosas propiedades.
Celluloseester: En 1856 se fabricó el primer termoplástico a partir de alcanfor y nitrato de celulosa. El resultado fueron pelotas de tenis de mesa y material cinematográfico para fotografía e imágenes en movimiento.
Acetato de celulosa: A éste le siguió un segundo termoplástico que podía transformarse en espuma (filtros de cigarrillos) y fibras. Los desarrollos posteriores dieron lugar a cuerpos moldeados transparentes, cubos y mangos de herramientas.
Éter de celulosa: Desde principios de los años treinta, este grupo de derivados de la celulosa ha adquirido su importancia industrial, un cortejo triunfal que continúa hasta nuestros días y que tiene un abanico de aplicaciones cada vez más amplio. Los éteres de celulosa son productos no tóxicos, en su mayoría solubles en agua, que suelen comercializarse en forma de polvos o gránulos blancos. Las propiedades específicas de los éteres de celulosa individuales dependen del tipo, número y distribución de los sustituyentes introducidos por una reacción química tras la activación de la molécula de celulosa con una solución de hidróxido de sodio.
Ámbitos de aplicación
El nombre se da nombrando el sustituyente, p. ej: Metilcelulosa (MC), hidroxipropilmetilcelulosa (HPMC), carboximetilcelulosa (CMC), hidroxipropilcelulosa (HPC), etilcelulosa (EC), etc. Las aplicaciones se encuentran en la industria de la construcción como aditivos para optimizar diversas propiedades en morteros, adhesivos para baldosas o rellenos (HEMC o HPMC). La pasta de papel pintado se compone principalmente de metilcelulosa (MC) o carboximetilcelulosa (CMC).
En la conformación de metales, los derivados de la celulosa se utilizan como lubricantes, en la producción de pinturas y barnices como reguladores de la viscosidad y aglutinantes. En lavavajillas como explosivo o en agricultura para retrasar el efecto de los pesticidas.
Algunos derivados de la celulosa están autorizados como aditivos alimentarios y para su uso en fórmulas cosméticas. Entre otras cosas, se utiliza el comportamiento de los diferentes éteres de celulosa en un medio acuoso a diferentes temperaturas. A menudo son aditivos indispensables en emulsionantes, estabilizantes y conservantes. Mejoran la fluidez de las salsas y sopas instantáneas. En el helado, influyen en el comportamiento de fusión, así como en la sensación en boca, y le dan un sabor cremoso a pesar de la reducción de nata.
En las industrias alimentaria y farmacéutica, influyen en la textura, la forma, la estructura y la consistencia de los productos líquidos y semisólidos. Sus aplicaciones van desde la pasta de dientes hasta los compuestos de recubrimiento para medicamentos. En cosmética sirven como reguladores y estabilizadores de la viscosidad, determinan la reología de pomadas, cremas solares y maquillajes. Su potencial dista mucho de haberse agotado y es objeto de intensas investigaciones.
El precio de los derivados "simples" de la celulosa, como la carboximetilcelulosa (CMC), empieza en 1,50 euros/kg y sube a más de 100 euros/kg para los derivados especiales de la celulosa en aplicaciones farmacéuticas. Los éteres de celulosa son difícilmente sustituibles por productos derivados del petróleo en muchas aplicaciones. Esto aumentará su importancia en diversas industrias. En particular, en muchas aplicaciones farmacéuticas o como aditivos alimentarios, especialmente para productos precocinados.
Éteres de celulosa y sus aplicaciones en la industria
Nombre | Abreviatura | Producción | Aplicación |
Carboximetilcelulosa | CMC | Convertida en celulosa alcalina con solución de hidróxido de sodio. Alquilación con ácido cloroacético. | Industria petrolera, industria textil, aditivo de detergentes, aglutinante, espesante, agente de encolado de papel (pasta de papel pintado), coloide protector, aditivo alimentario E 466 (helados, mayonesa, gelatina, productos de panadería), pasta dentífrica, reticulado como desintegrante de comprimidos. |
Metilcelulosas | MC HEMC HPMC | Convertida en celulosa alcalina con solución de hidróxido de sodio. Alquilación con cloruro de metilo, Eterificación con Óxido de etileno o Óxido de propileno | Aditivos en diversos materiales de construcción (hormigón, mortero, adhesivos para baldosas, masillas, yesos, etc.) Pasta de papel pintado, espesante, gelificante y agente de recubrimiento, emulsionante, estabilizante en alimentos (MC: E 461, HPMC: E 464) sustitutos de la carne, helados, productos de panadería, mayonesa, productos instantáneos y productos congelados) y cosméticos. En farmacia como "lágrimas artificiales", laxante, agente de contraste negativo, retardante de principios activos, recubrimiento de comprimidos, material para cápsulas duras. |
Etilcelulosa | EC | Convertida en celulosa alcalina con solución de hidróxido de sodio. Alquilación con cloruro de etilo. | Espesante, aglutinante, adhesivo, así como formador de película y capa de barrera hidrófuga. Ingrediente principal revestimientos de éter de celulosa resistentes a la luz, materiales de envasado, termoplásticos, nieve artificial para árboles de Navidad, aislamiento de cables, pieles protectoras y juntas. Como aditivo de resinas y ceras sintéticas para barnizar huevos de Pascua coloreados y como aditivo de tintas de estampación en la industria alimentaria (E 462). En farmacia, excipiente para aumentar la viscosidad, como aglutinante para gránulos de comprimidos, como formador y desintegrante de comprimidos y, en particular, como formador de película (por ejemplo, marca comercial Surelease®) para comprimidos de laca. |
Hidroxietilcelulosa | HEC | Convertida en celulosa alcalina con solución de hidróxido de sodio. Eterificación con óxido de etileno. | En la industria de materiales de construcción, en pinturas hidrosolubles y adhesivos de dispersión, así como en yesos y masillas. En productos farmacéuticos como excipiente y en dentífricos. |
Hidroxipropilcelulosa | HPC | Convertida en celulosa alcalina con solución de hidróxido de sodio. Eterificación con óxido de propileno. | Aplicación como excipiente farmacéutico, aglutinante para masas cerámicas, para revestimientos y adhesivos, en artículos cosméticos, en tintas de impresión y en tecnología de polimerización. En alimentación como estabilizante, capa protectora y abrillantador. |
© Copyright by amixon GmbH