
Mezclador industrial al vacío
La fuerza de presión se mide en la unidad física denominada Pascal (1 Pa = 1 N/m² = 0,01 mbar).
No obstante, en ocasiones se sigue utilizando otra unidad de medida más antigua conocida como Torr (1 Torr = 1 mm Hg columna = 1,333 mbar).
La calidad de vacío se divide en las siguientes gamas
- 1 bar a 1 mbar = Vacío bruto
- 1 mbar a 10-3 mbar = Vacío fino
- 10-3 mbar a 10-7 mbar = Alto vacío
- 10-7 mbar a 10-10 mbar = Ultravacío
En este glosario utilizaremos el término "vacío" y "mezcladora al vacío" de forma general. Sin embargo, según las medidas presentadas en la tabla anterior, el nivel de vacío al que hacemos referencia correspondería únicamente al rango de "vacío bruto" y, en determinados casos, a un porcentaje del "vacío fino".
Aviso previo:
Cuando vertemos materiales a granel sobre una superficie, el resultado es un cúmulo en forma piramidal. En este estado de reposo, las partículas de dimensiones diferentes se encuentran, por así decirlo, unas encima de otras y unas junto a las otras. De esta forma, cada partícula está en equilibrio y las fuerzas que actúan sobre cada partícula son: la fuerza gravitacional, la fuerza de contacto y las fuerzas de contacto entre partículas vecinas. La suma de todas las fuerzas que actúan sobre las partículas es igual a cero. Asimismo, debido a su forma redonda, la mayoría de las partículas solo se tocan entre sí hasta cierto punto. Es decir, hay bastante espacio libre entre estas. Incluso, una sola partícula puede tener espacios vacíos en ella misma; lo que se conoce como la porosidad de un sistema disperso. Para describir o hablar de la porosidad, se suele utilizar la letra del alfabeto griego PHI. En sí, la porosidad es una magnitud adimensional que sirve para medir la cantidad de gas/aire presente en un material a granel.
Según la temperatura y la presión atmosférica, el aire ambiente contiene más o menos humedad en forma de vapor de agua. Así, el agua se acumula en capas microscópicas de condensación en las superficies sólidas, incluyendo los poros de las partículas. En este sentido, los sólidos a granel en condiciones atmosféricas son sistemas trifásicos dispersos. Es decir, se componen de sólido, líquido y gas.
Los recipientes de las máquinas para procesamientos industriales, como las mezcladoras al vacío, los agitadores, los mezcladores, los reactores, los separadores, etc., pueden llenarse con producto solamente hasta un cierto nivel. En la superficie de este material de mezcla suele haber, por lo tanto, aire del ambiente. Por lo tanto, este de gas también debe eliminarse en caso de evacuación.
Hay muchas razones por las que es necesario evacuar una sala de mezclas. Algunas de ellas son:
- Evitar la oxidación de los materiales con el oxígeno atmosférico.
- Evitar riesgos de incendio y explosión.
- Evitar la fluidificación de los materiales en polvo.
- Eliminar del exceso de presión de gas debido a la formación de gas reactivo.
- Reducir el nivel de presión del sistema a fin de acelerar un proceso de secado.
- Generar una fricción sólida intensa para acelerar el proceso de desaglomeración y de difusión dentro de las partículas sólidas.
- Aumentar temporalmente la densidad aparente.
- Intercambiar el gas contenido en el material a granel (Inertización con nitrógeno o dióxido de carbono).
- Desgasificar líquidos.
- Extraer el aire al aspirar o soplar neumáticamente polvo en un recipiente.
- Este es también el caso, por ejemplo, cuando se mezclan grandes cantidades de polvo en un líquido (tecnología de mezcla de alto cizallamiento con configuración rotor-estator).
- Cuando se sintetizan sustancias de gran pureza.
- Cuando se requieren condiciones estériles en el procesamiento y producción.
- Para controlar los procesos de fermentación.
- Cuando los sistemas dispersos deben enfriarse por reducción de entalpía.
- Durante la liofilización.
- Para impregnar líquidos muy viscosos en partículas de polvo.
- Y mucho más.
Todos los métodos anteriores pueden llevarse a cabo en un mezclador industrial al vacío de amixon® en el procesamiento industrial de materiales a granel. Es el caso, por ejemplo, de los productos farmacéuticos, cosméticos, compuestos químicos y alimentos.
Para poder crear un vacío, se necesitan dos requisitos básicos: Un recipiente hermético al gas/vacío y una bomba de vacío.
Los mezcladores indusriales al vacío de amixon® pueden utilizarse universalmente.
Al evacuar un sistema de dispersión, el gas se acelera en dirección a la bomba de vacío. Dependiendo de su velocidad, el gas que fluye puede arrastrar involuntariamente partículas de polvo de los materiales de llenado. Un resultado no deseado en la mayoría de los casos. A fin de evitarlo, se instalan filtros de polvo antes de la bomba de vacío. Al diseñar sistemas neumáticos y de vacío, deben coordinarse, entre otros, los siguientes parámetros de rendimiento:
- La velocidad de bombeo de la bomba.
- El rendimiento de la bomba.
- La robustez de esta misma.
- La velocidad efectiva de bombeo.
- La potencia de aspiración.
- La longitud de la línea.
- La velocidad del gas.
- La resistencia a la fluidez.
- Función de filtro.
- Área de filtrado.
- Carga del filtro.
- Limpieza de filtros.
- Acondicionamiento de filtros.
- Tiempo de preparación en caso de limpieza convencional o en húmedo.
- Etc.
En muchos casos, las dispersiones húmedas o mojadas también deben evacuarse o secarse al vacío en la mezcladora industrial al vacío. Cuando esto ocurre, el gas que se escapa no sólo es polvoriento, sino que también está contaminado con vapor de agua o vapor de disolvente. En la práctica, este gas se denomina vapor y solo puede purificarse en un denominado filtro de vapor. La carcasa de dicho filtro debe calentarse muy por encima de la temperatura del punto de rocío de la fase líquida. Una vez finalizado este proceso, el gas depurado puede secarse opcionalmente en un intercambiador de calor. Esta es una forma efectiva de recuperar los disolventes utilizados. El polvo relavado vuelve al mezclador industrial al vacío.
Ejemplo de aplicacióndel mezclador industrial al vacío en la producción de suplementos alimenticios
Mezcladores industriales al vacío en la producción de suplementos alimenticios a base de mezclas de proteínas en polvo:
La composición nutricional de una mezcla de proteínas en polvo consiste en fuentes proteicas como el suero, la caseína o la soja. A estas se le agregan comúnmente otros ingredientes en polvo, como aminoácidos, vitaminas, minerales y edulcorantes. En este proceso, la tecnología de vacío desempeña un papel importante al evitar la oxidación, ya que el polvo envasado en latas o bolsas debe estar prácticamente libre de oxígeno y humedad.
Una herramienta de mezclado al vacío puede ser sumamente útil en este caso pues elimina el oxígeno atmosférico de los productos mezclados antes de que sean envasados o vertidos en la mezcladora. Además, posteriormente, los lleva a la presión atmosférica con una mezcla de gas de dióxido de carbono y nitrógeno. Esta medida estabiliza las propiedades de flujo y prolonga la vida útil de los compuestos nutritivos.
Ejemplo de aplicación del mezclador industrial al vacío en la industria farmacéutica
Un mezclador al vacío para ingredientes farmacéuticos activos sólidos debe convertirse en formas de dosificación fáciles de usar, como tabletas masticables, tabletas efervescentes, tabletas orales, cápsulas o supositorios. Para ello, los principios activos deben previamente ser diluidos con la ayuda de sustancias de relleno. Esto se lleva a cabo dentro de los mezcladores industriales para materiales en polvo. En este tipo de procesos, algunas sustancias activas tienen partículas muy finas, por lo que hay que aglutinar sus polvos. Esto se hace por aglomeración en el aparato de lecho fluido o en el mezclador de vacío. Dichos procesos de aglomeración se ven favorecidos por la presencia de aglutinantes líquidos. Aunque, posteriormente, la fase líquida debe pasar por un paso de secado. Este es acelerado considerablemente al aplicar vacío. Al bajar la presión del sistema, el agua se evapora muy por debajo de los 100 °C. Las bajas temperaturas de secado también son útiles para los principios activos farmacéuticos termosensibles.
Sin embargo, el oxígeno del aire puede tener un efecto negativo en la vida útil de los medicamentos sólidos. Para hacer frente a esto, se puede llevar a cabo un proceso de inertización, -como el que ya se ha descrito anteriormente-, con la ayuda de un mezclador industrial al vacío.
- Un proceso típico de preparación galénica es la llamada trituración de ingredientes activos para dispersarlos de forma particularmente uniforme en un material de llenado o excipiente en polvo. Este tipo de desaglomeración también puede realizarse eficazmente en el mezclador al vacío. Para ello, se altera la maduración interna de la mezcla de material a granel, evitando así de forma fiable la fluidificación no deseada.
- Si se va a incrustar un principio activo líquido dentro de gránulos de relleno, es imprescindible contar con un mezclador industrial al vacío. Esto se debe a que, solamente después de que un fino vacío haya eliminado la mayor parte del aire de los poros de los materiales aglomerados, es cuando es posible pulverizar el principio activo líquido dentro de la mezcladora de vacío. Una vez finalizado este proceso, la presión del sistema aumenta lentamente hasta alcanzar la presión atmosférica. Un proceso bastante ventajoso, conocido como "impregnación", puede llevarse a cabo aplicando un gas inerte o noble.
- En el día a día, los medicamentos se administran frecuentemente en forma líquida. En este caso, puede ser que en la producción sea necesario dispersar o disolver principios activos en polvo en sustancias líquidas. Sin embargo, hay muchos problemas que surgir al introducir y distribuir polvos en líquidos. Algunos de ellas son: formación indeseable de espuma, distribución no homogénea de las fases líquida y sólida, largos tiempos de proceso, encapsulación de aglomerados de polvo. Como se mencionó al principio, la fase gaseosa siempre está presente si no se ha evacuado intencionalmente. También en este caso, los mezcladores industriales al vacío ayudan enormemente.
- En casos especiales, se debe aplicar uniformemente una sustancia activa en polvo, finamente dispersa, sobre la superficie de un material portador en polvo. Esto debe hacerse sin las desviaciones de la aglomeración de humedales. No obstante, incluso un proceso de homogeneización tan complicado como este puede llevarse a cabo cómodamente con la ayuda de este tipo de mezcladores.
- Por su parte, los procesos de fermentación y síntesis casi siempre se completan en la fase húmeda. Para ello, el contenido líquido en el producto se evapora o se deshumidifica mecánicamente como paso intermedio. Para finalizar, la etapa de secado puede llevarse a cabo también en un mezclador al vacío previamente calentado.
- También es posible sublimar la sustancia líquida. Esto significa que la sustancia activa se evapora sin pasar por la fase líquida. En un mezclador industrial al vacío de amixon®, la sublimación puede acelerarse para descargar con seguridad el gas como ingrediente activo.
Los mezcladores de vacío, que calientan la mezcla durante el mezclado, son mucho más importantes. Esto se consigue acoplando una doble camisa a la cámara de mezcla y a la herramienta de mezcla. Los medios de transferencia de calor (agua, vapor o aceite térmico) fluyen a través de la doble camisa y transfieren su energía térmica a la mezcla.
Secado de la mezcla al vacío
La humedad residual de la mezcla se vaporiza eficazmente. La mezcla se seca muy rápida y eficazmente. El vacío reduce el punto de ebullición. Esto significa que los ingredientes activos sensibles al calor pueden secarse de forma rápida y económica. Este tema se trata en las entradas del blog de este sitio web.
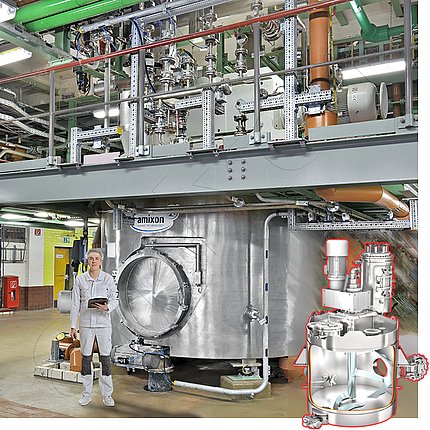
Vaporizador
En algunos casos, es necesario vaporizar líquidos. Esto también se consigue de forma eficiente y eficaz aplicando calor y vacío. Con la tecnología amixon, puede probar todos estos procesos con sus productos mezclados. Este tema también se trata en las entradas del blog de este sitio web.