
Miscelatore sottovuoto
La pressione viene misurata nell'unità fisica Pascal. 1 Pa = 1 N/m² = 0,01 mbar.
A volte si incontra anche la vecchia unità di misura Torr = 1 mm Hg di colonna = 1,333 mbar.
La qualità del vuoto è suddivisa nei seguenti intervalli
- Da 1 bar a 1 mbar Vuoto basso
- Da 1 mbar a 10-3 mbar Vuoto medio
- Da 10-3 mbar a 10-7 mbar Vuoto alto
- Da 10-7 mbar a 10-10 mbar Vuoto ultra alto
In questo glossario, utilizziamo il termine vuoto/miscelatore sottovuoto in modo semplificato. Tuttavia, secondo la tabella sopra riportata, ciò si riferisce solo alla gamma del "vuoto basso" e, in singoli casi, a una "parte del vuoto medio".
Preavviso:
Quando versiamo materiali sfusi su un piano, il risultato è una pila a forma di cono. Nello stato di riposo, le particelle di forma diversa si trovano, per così dire, sopra e accanto l'una all'altra. Ogni particella è in equilibrio. Le forze che agiscono su una singola particella sono: la forza gravitazionale, la forza di contatto e le forze di contatto delle particelle vicine. La somma di tutte le forze che agiscono sulle particelle è pari a zero. A causa della loro forma rotonda, la maggior parte delle particelle si toccano solo selettivamente. Ci sono molti vuoti tra le particelle. Anche una singola particella può presentare dei vuoti. Questa caratteristica viene definita porosità di un sistema disperso. Nelle formule fisiche, per la porosità si usa di solito la lettera del greco antico PHI. La porosità è una grandezza adimensionale. È una misura della quantità di gas/aria presente in un materiale sfuso.
A seconda della temperatura e della pressione atmosferica, l'aria ambiente contiene più o meno umidità sotto forma di vapore acqueo. L'acqua si accumula in strati microscopici di condensa sulle superfici solide e nei pori delle particelle. In questo senso, i solidi sfusi in condizioni atmosferiche sono sistemi dispersi a tre fasi. Sono costituiti da solidi, liquidi e gas.
I serbatoi delle macchine per l'ingegneria di processo, come i miscelatori sottovuoto, gli agitatori, i miscelatori, i reattori, i separatori, ecc. possono essere riempiti di prodotto solo fino a un livello massimo di riempimento consentito. Al di sopra dello strato di materiale misto si trova solitamente l'aria ambiente. Questo volume di gas deve essere rimosso anche in caso di evacuazione.
Le ragioni per cui può essere necessario evacuare un locale di miscelazione sono molteplici. Alcune di esse sono:
- Evitare l'ossidazione con l'ossigeno atmosferico,
- Evitare i rischi di incendio e di esplosione,
- Evitare la fluidificazione delle polveri,
- Eliminare la pressione in eccesso dovuta alla formazione di gas reattivi,
- Ridurre la pressione del sistema per accelerare un processo di essiccazione,
- Generare un intenso attrito solido per accelerare la disagglomerazione e la diffusione all'interno delle particelle solide,
- Aumentare temporaneamente la densità apparente,
- Sostituire il gas contenuto nel materiale sfuso (inertizzazione con azoto o anidride carbonica)
- Degassificare i liquidi,
- Rimuovere l'aria quando la polvere viene aspirata o soffiata pneumaticamente in un contenitore,
- Questo avviene anche, ad esempio, quando grandi quantità di polvere vengono miscelate in un liquido (tecnologia di miscelazione ad alto sforzo di taglio con configurazione rotore-statore).
- quando si sintetizzano sostanze di elevata purezza,
- quando sono necessarie condizioni di sterilità,
- nel controllo dei processi di fermentazione,
- quando i sistemi dispersi devono essere raffreddati per riduzione entalpica,
- durante la liofilizzazione,
- quando i liquidi altamente viscosi devono essere impregnati in particelle di polvere
- ......
I metodi sopra descritti possono essere applicati al finissaggio industriale dei tessuti nel miscelatore sottovuoto. È il caso, ad esempio, dei prodotti farmaceutici, dei cosmetici, degli agenti chimici e degli alimenti.
Per poter creare il vuoto, sono necessari due requisiti fondamentali: Un contenitore a tenuta di gas/vuoto e una pompa per il vuoto.
I miscelatori sottovuoto possono essere utilizzati universalmente.
Durante l'evacuazione di un sistema di dispersione, il gas viene accelerato in direzione della pompa del vuoto. A seconda della velocità del gas, il flusso di gas può involontariamente intrappolare le particelle di polvere dal letto. Nella maggior parte dei casi ciò non è auspicabile. Pertanto, i filtri antipolvere sono installati a monte della pompa del vuoto. Quando si progettano sistemi pneumatici e a vuoto, è necessario coordinare, tra gli altri, i seguenti parametri di prestazione:
- la velocità di pompaggio della pompa
- l'efficienza della pompa
- la robustezza della pompa
- la velocità di pompaggio effettiva
- la potenza di aspirazione
- la lunghezza della linea
- la velocità del gas
- Resistenza al flusso
- Funzione filtro
- Area filtro
- Carico del filtro
- Pulizia del filtro
- Condizionamento del filtro
- Tempo di allestimento in caso di pulizia/lavaggio a umido
- ...
In molti casi, le dispersioni umide o bagnate devono essere evacuate/essiccate sottovuoto nel miscelatore sottovuoto. In questo caso, il gas che fuoriesce non è solo polveroso, ma anche contaminato da vapore acqueo o solvente. Nella pratica, questo tipo di gas è chiamato "vapore". Può essere pulito solo in un cosiddetto filtro a vapore. L'alloggiamento del filtro deve essere riscaldato ben al di sopra della temperatura del punto di rugiada della fase liquida. Il gas purificato può essere deumidificato in uno scambiatore di calore. I solventi possono essere recuperati in questo modo. La polvere ritorna al miscelatore del vuoto.
Esempio di applicazione del miscelatore sottovuoto nella produzione di integratori alimentari
Miscelatori sottovuoto nella produzione di integratori alimentari a base di miscele di proteine in polvere:
La composizione nutrizionale di una miscela di proteine in polvere è costituita da fonti proteiche come il siero del latte, la caseina o la soia. Questi vengono mescolati con altri ingredienti in polvere, come aminoacidi, vitamine, minerali ed edulcoranti. La tecnologia del vuoto svolge un ruolo importante in questo processo per prevenire l'ossidazione. La polvere, che viene riempita in barattoli o sacchetti, deve essere in gran parte priva di ossigeno e umidità.
In questo caso un miscelatore sottovuoto può essere utile, rimuovendo l'ossigeno atmosferico dai materiali miscelati prima del confezionamento/riempimento nel miscelatore e portandoli poi a pressione atmosferica con una miscela di anidride carbonica e azoto. Questa misura stabilizza le proprietà di scorrimento e prolunga la durata di conservazione della composizione nutritiva.
Esempio di applicazione del miscelatore sottovuoto nell'industria farmaceutica
Miscelatore sottovuoto per ingredienti farmaceutici attivi solidi
devono essere convertiti in forme di dosaggio facili da usare, come compresse masticabili, compresse effervescenti, compresse orali, capsule o supposte, ...... Prima di tutto, i principi attivi devono essere diluiti con l'aiuto di riempitivi. Questo avviene nei miscelatori di polveri. Alcuni principi attivi sono estremamente fini, quindi le loro polveri devono essere legate. Ciò avviene per agglomerazione nell'apparecchio a letto fluido o nel miscelatore sottovuoto. I processi di agglomerazione sono favoriti dalla presenza di leganti liquidi. La fase liquida deve poi essere essiccata. Il processo di essiccazione viene accelerato in modo massiccio dall'applicazione del vuoto. Abbassando la pressione del sistema, l'acqua evapora ben al di sotto dei 100°C. Le basse temperature di essiccazione sono utili anche per gli ingredienti farmaceutici attivi termosensibili.
L'ossigeno atmosferico può influire negativamente sulla durata di conservazione dei farmaci solidi. Il processo di inertizzazione può essere eseguito come descritto nel capitolo precedente, con l'aiuto di un miscelatore sottovuoto.
- Un tipico processo di preparazione galenica è la cosiddetta triturazione dei principi attivi per disperderli in modo particolarmente uniforme in un riempitivo o eccipiente in polvere. Questo tipo di disagglomerazione può essere efficacemente supportato nel miscelatore sottovuoto. La maturazione interna della miscela sfusa viene aumentata e si evita in modo affidabile una fluidificazione indesiderata.
- Se un principio attivo liquido deve essere incorporato all'interno di pellet di riempimento, è utile un miscelatore sottovuoto. Solo dopo che un vuoto medio ha rimosso la maggior parte dell'aria dai pori degli agglomerati di riempimento, l'ingrediente attivo liquido viene spruzzato nel miscelatore sottovuoto. La pressione del sistema viene quindi aumentata lentamente fino alla pressione atmosferica. La cosiddetta impregnazione può essere effettuata vantaggiosamente utilizzando un gas inerte o nobile.
- A volte i farmaci vengono somministrati in forma liquida. In questo caso, può essere necessario disperdere o sciogliere nel liquido i principi attivi in polvere. L'introduzione e la distribuzione di polveri nei liquidi può causare molti problemi. Alcuni di questi sono: schiumosità indesiderata, distribuzione disomogenea delle fasi liquide e solide, lunghi tempi di lavorazione, incapsulamento di agglomerati di polvere. Come detto all'inizio, la fase gassosa è sempre presente se non è stata evacuata in precedenza. Anche in questo caso, i miscelatori sottovuoto forniscono servizi preziosi.
- In casi particolari, un principio attivo polveroso e finemente disperso deve essere applicato uniformemente sulla superficie di un materiale di supporto in polvere. Questo dovrebbe essere fatto senza la deviazione dell'agglomerato di zone umide. Anche un processo di omogeneizzazione così complicato può essere eseguito comodamente con l'aiuto di miscelatori sottovuoto.
- I processi di fermentazione e sintesi sono quasi sempre completati nella fase umida. Il prodotto viene poi evaporato o deumidificato meccanicamente come fase intermedia. La fase finale di essiccazione può essere eseguita comodamente in un miscelatore sottovuoto riscaldato.
- Il principio attivo in polvere può sublimare. Ciò significa che l'ingrediente attivo evapora saltando la fase liquida. In un miscelatore sottovuoto, la sublimazione può essere accelerata per scaricare in modo sicuro il gas come ingrediente attivo.
I miscelatori a vuoto, che riscaldano la miscela durante la miscelazione, sono molto più importanti. Ciò si ottiene collegando una doppia camicia alla camera di miscelazione e all'utensile di miscelazione. I mezzi di trasferimento del calore (acqua, vapore o olio termico) passano attraverso la doppia camicia e trasferiscono la loro energia termica alla miscela.
Essiccazione dell'impasto sottovuoto
L'umidità residua dell'impasto viene vaporizzata in modo efficace. L'impasto si asciuga in modo rapido ed efficace. Il vuoto abbassa il punto di ebollizione. Ciò significa che gli ingredienti attivi sensibili al calore possono essere essiccati in modo rapido ed economico. Questo argomento è trattato nei post del blog di questo sito.
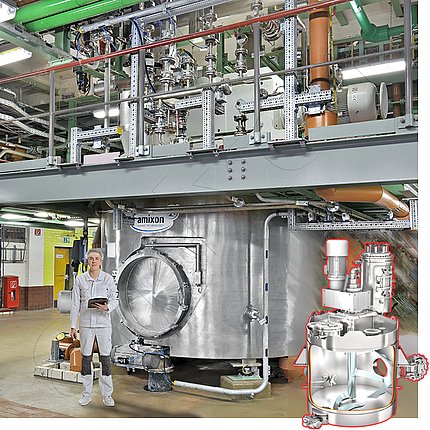
Vaporizzatore
In alcuni casi, i liquidi devono essere vaporizzati. Anche questo si ottiene in modo efficiente ed efficace applicando calore e vuoto. Con la tecnologia amixon, potete testare tutti questi processi con i vostri prodotti misti. Anche questo argomento è trattato nei post del blog di questo sito.