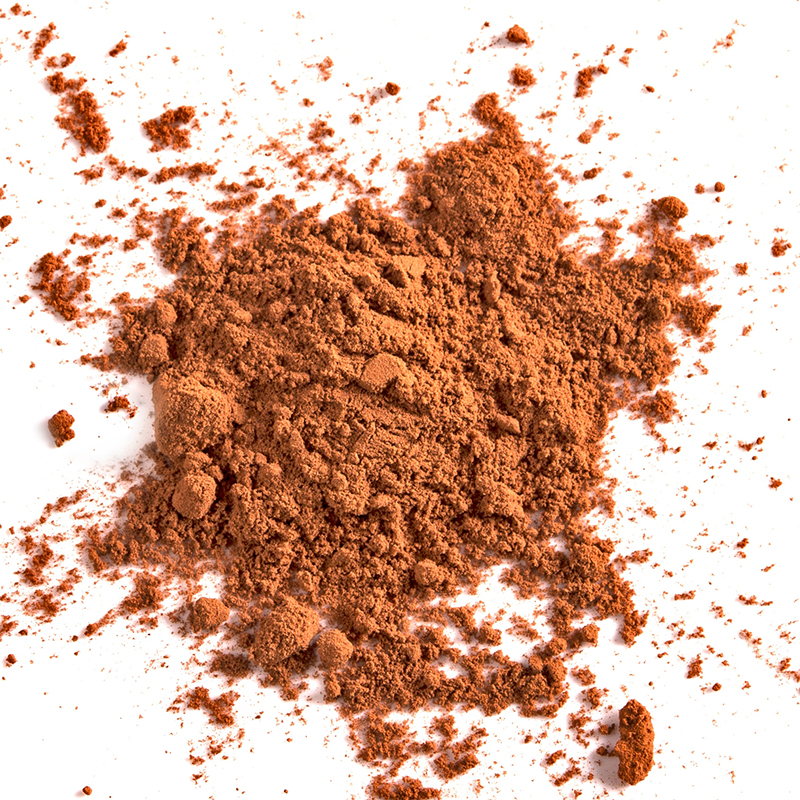
Los sólidos a granel son difíciles de describir. En la tecnología del polvo se utilizan más de 30 parámetros. La caracterización de los sólidos a granel incluye, por ejemplo, propiedades como la forma del grano, la distribución granulométrica, la humedad y la densidad aparente. Sin embargo, la polvosidad y el comportamiento de flujo también son de especial importancia.
Auxiliar de flujo y Auxiliar de filtración: Agente antiaglomerante
La calidad de un polvo o una mezcla de materiales polvos está esencialmente determinada por la pureza y el nivel de eficacia de los ingredientes utilizados. Se podría decir que, cuanto mayor sea la superficie específica de un polvo, más eficaz será. Es decir, según su nivel de pulverización. Por ejemplo, tan solo bastan pequeñas cantidades de un pigmento colorante para colorear de forma homogénea varias toneladas de pintura para paredes; tal y como también se requieren pequeñas cantidades de una mezcla de especias para lograr aquel sabor a carne en la producción de albóndigas de origen vegetal.
Sin embargo, además de la eficacia de los ingredientes en polvo o de las mezclas en polvo utilizadas, también existen otras propiedades adicionales sumamente importantes. Especialmente cuando, por ejemplo, los materiales en polvo son procesados industrialmente. Un buen ejemplo de ello son las mezclas de bebidas instantáneas, como el capuchino o el té helado, que son empacadas en bolsitas: siempre que las mezclas de té deben ser embolsadas, se requiere de un proceso de llenado a alta velocidad. Sin embargo, la mixtura de polvos debe conservar siempre excelentes propiedades de flujo y dosificación. Además, esta debe estar lo más libre de polvos nocivos posible; de lo contrario, el sellado de los sacos de té sería imposible.
Un método adecuado para despejar a los materiales en polvo de otros polvos externos no deseados es el agrandar su tamaño a fin de que estos puedan formar aglomerados estables. Algo que también mejora sus propiedades de flujo. Otra forma es el humedecer los materiales para dejarlos libres de polvo. No obstante, mientras mas húmedos, peor es su fluidez. En el proceso de humectación, es común que se distribuyan porciones de compuestos líquidos dentro de la mezcla de tal forma que cada partícula sea humedecida con una cantidad proporcional del líquido. Sin embargo, este proceso suele afectar negativamente el comportamiento de flujo de los materiales en polvo, ya que la fase líquida favorece la adhesión de las partículas; produciéndose así más aglomeraciones involuntarias.
El diseño en forma de cono del conducto de descarga da algunas pistas
Hay una gran variedad de métodos para determinar la fluidez de compuestos en polvo. Para un cálculo básico se podría utilizar, por ejemplo, un método muy sencillo: En primer lugar, se determina la altura del conducto cónico de descarga. Por su parte, los materiales en polvo pasan por un filtro hacia un cilindro metálico, formándose así una pirámide apilada de descarga. Posteriormente, esta se eleva hasta que la fuerza gravitacional es mayor que las fuerzas de cohesión. Entonces, las partículas de los materiales se deslizan unas sobre otras. En sí, el grado de inclinación del cono de descarga es una medida importante que ayuda a determinar el nivel cohesión de los polvos. Por ejemplo, un cono de vertido plano indica una buena fluidez de los materiales. Esta técnica se conoce como el método de Jenike y es una forma precisa de medir las propiedades de flujo cuando, en la industria, los materiales en polvo deben ser almacenados en grandes silos al finalizar su procesamiento.
Mecanismos de unión dentro de los colectivos de partículas
En un colectivo de partículas, la fuerza de gravedad actúa, en primer instancia, sobre cada una de las partículas individuales. Posteriormente, estas fuerzas se subsuman, en función de la altura de la pila materiales, en las capas inferiores de esta misma. Simultáneamente, las partículas producen fuerzas adhesivas entre sí; se trata de las fuerzas de Van der Waals y de las interacciones electrostáticas. Cuando las partículas son muy pequeñas, estas fuerzas interparticulares llegan a tener un impacto dominante sobre la fuerza de cizallamiento. Además, cabe señalar que la presencia de humedad también aumenta el efecto de las fuerzas interparticulares.
Tamaño de las partículas y contenido pulverulento
Cuantas más partículas estén en contacto entre sí, mayores serán las fuerzas interparticulares, ya que estas aumentan tras el contacto entre partículas. Una correlación sumamente significativa que resulta de que el grado de contacto de las partículas es inversamente proporcional al tamaño al cuadrado de las mismas.
De tal forma que, si el aire ambiente tiene una humedad relativa del 50 % o más, las partículas de polvo hidrófilo comenzarán a acumular agua. Dicha acumulación ocurre en forma de capas de adsorción mono moleculares y multi moleculares. Si las capas de adsorción de varias partículas se tocan entre sí (punto por punto), se produce entonces la conocida condensación capilar. Sin embargo, el agua forma puentes líquidos; lo que puede resultar en fuerzas de adhesión demasiado elevadas entre las partículas. Como resultado, esto puede dar comienzo a los procesos de aglomeración.
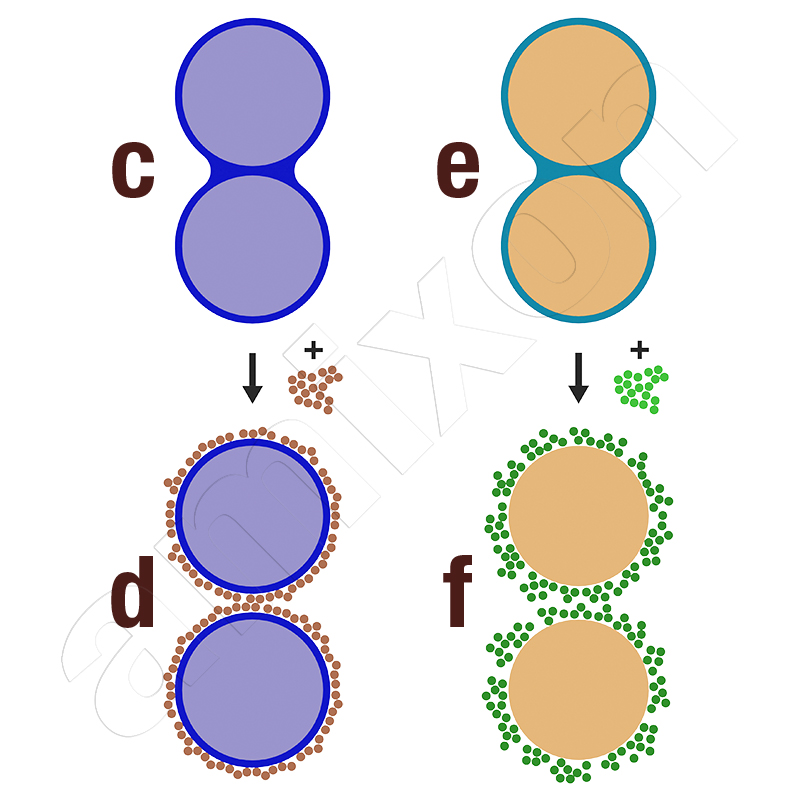
Dos anti aglomerantes de acción diferente: hidrofóbico a la izquierda, hidrofílico a la derecha.
¿Cómo pueden ayudar los auxiliares de flujo en estos casos?
- Estos mejoran el comportamiento del flujo
- Evitan el apelmazamiento y los grumos
- Hacen parecer a los materiales en polvo más secos de lo que son
Dos auxiliares de irrigación con efectos diferentes:
c. En la gráfica se puede observar cómo las partículas de color azul claro son humedecidas con un líquido azul más obscuro. Esto forma un puente líquido que une a ambas partículas.
d. Al añadir y mezclar una ligera cantidad del auxiliar de flujo en las partículas, el líquido humectante es recubierto. En sí, el auxiliar de flujo y el componente líquido difieren en cuanto a sus propiedades. Como resultado, las partículas vuelven a separarse.
e. En el caso de las partículas de color marrón, a la derecha, que son humectadas con un líquido de color turquesa, también se puede observar un puente líquido que las une.
f. Al añadir y mezclar en estas una ligera cantidad de auxiliar de flujo, el líquido humectante es absorbido, ya que el auxiliar y el componente líquido comparten propiedades semejantes. Sin embargo, al igual que con el primer método, las partículas también se separan.
En la industria, se hace uso de un auxiliar de flujo siempre y cuando los materiales en polvo tengan propiedades de fluidez poco eficientes o
- si la el proceso de logística interna es muy exigente.
- si el procesamiento automatizado de los materiales es muy complicado.
- si las máquinas de envasado de alto rendimiento se atascan frecuentemente.
- si se llega a bloquear el conducto de descarga de los silos, big bags o contenedores a granel.
- si un material a granel tiende a aglutinarse al estar en reposo (tiempo de solidificación).
Los coadyuvantes de flujo, también conocidos como auxiliares de goteo o anti aglomerantes, son polvos con una densidad muy baja dispersados muy finamente. Sin embargo, esto les suma muchas ventajas: Su superficie específica es extremadamente alta por lo que, aun en cantidades muy reducidas, pueden recubrir eficazmente los productos en polvo. Esto ocurre dado que las fuerzas interparticulares se reducen al mismo tiempo que los puentes líquidos desaparecen; así, las mercancías fluyen de manera óptima.
Sin embargo, los auxiliares de flujo como el silicato de magnesio, el silicato de calcio, el dióxido de silicio, (otros nombres son también gel de sílice, ácido silícico o gel de sílice) son extremadamente sensibles a la presión y al cizallamiento. Lo que quiere decir que, si se mezclan intensivamente con materiales a granel, estos pierden su efecto antiadherente. Como consecuencia, estos deben ser distribuidos en la masa de forma menos intensiva; es decir, con un aporte de energía mínimo. Sin embargo, aun cuando el procedimiento deba ser delicado, el auxiliar de flujo debe recubrir cada una de las partículas de los materiales a granel.
Además, los auxiliares de flujo/agentes anti aglomerantes se añaden a los materiales únicamente en proporciones de 0.001 o 0.002 por ciento en peso. En conjunto, esto hace del proceso de mezclado un verdadero reto.
La distribución uniforme de los compuestos anti aglomerantes en los materiales a granel es un verdadero desafío, pues supone enfrentarse a objetivos casi incompatibles:
- El anti aglomerante debe ser un material libre de declaración.
- Los aditivos de flujo libre se deben utilizar solamente en cantidades mínimas, por ejemplo, solo el 0.001 por ciento en peso.
- Los agentes de goteo son polvos muy ligeros. por lo que tienden a flotar en la superficie de la mezcla de polvos.
- Su eficacia se pueda garantizar únicamente si se distribuyen homogéneamente en la mezcla de polvos.
- La estructura de las partículas de los anti aglomerantes sumamente compleja y sensible por lo que solamente pueden cumplir su función si no son sometidos a algún tipo de estrés físico. Es decir, si no son condensados o cizallados.
Mezcla delicada
Gracias a nuestra amplia experiencia en la ingeniería de procesamientos industriales, en amixon® hemos desarrollado las soluciones ideales para enfrentar este tipo de desafíos: Nuestros mezcladores industriales amixon® son ideales para este tipo de procesos. En ellos, los materiales a granel adquieren excelentes propiedades de flujo aun utilizando una cantidad mínima de agentes anti aglomerantes. Algo que también se puede garantizar incluso si se procesan lotes de mezcla de gran volumen. Además, las mezcladoras industriales de amixon® no solo procesan los materiales en polvo eficiente y delicadamente, sino que también en poco tiempo.
"Líquidos Secos"
La estructura de la superficie de la partícula se caracteriza por la presencia de muchos capilares. Las partículas de los Agentes anti aglomerantes tienen superficies extremadamente grandes: hasta 500 m²/gramo. En este sentido, los agents también pueden utilizarse para absorber y aglutinar grandes cantidades de líquido (hasta tres veces su propio peso). Los mezcladores amixon® son especialmente adecuados para la producción de líquidos secos gracias a su modo de funcionar suave.
Los "líquidos secos" se producen ocasionalmente para humedecer polvos críticos y suprimir su aglomeración. Este método de humectación del polvo funciona sin sistemas de pulverización de líquidos.
Proceso de humectación. Aquí puede verse el líquido en reposo en el centro, el polvo seco en el borde y la humectación que progresa lentamente. El comportamiento de humectación de los auxiliares de flujo es totalmente diferente. En cuestión de segundos, todo el líquido será absorbido. (Absorción instantánea)
© Copyright by amixon GmbH