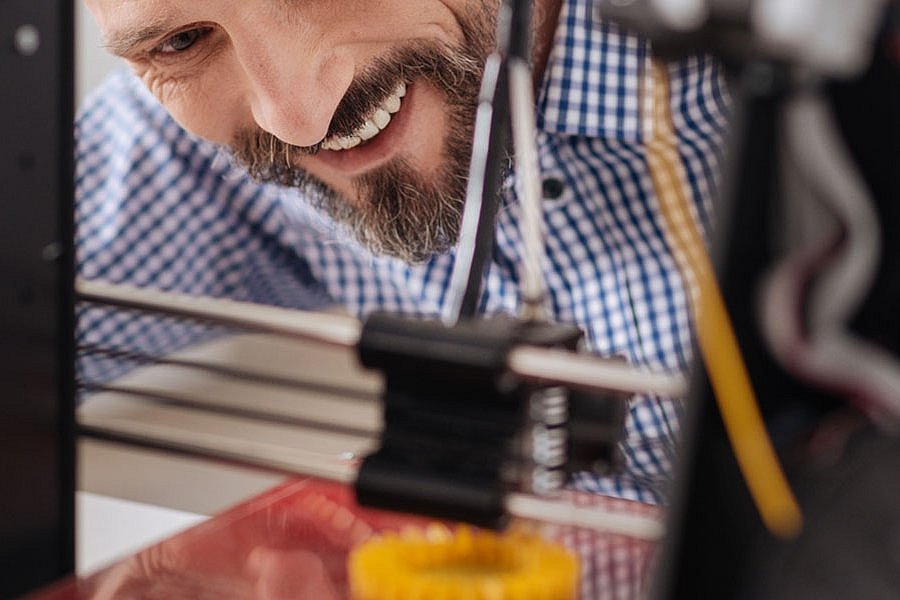
Miscelatori, essiccatori sotto vuoto e reattori di sintesi svolgono funzioni importanti nella metallurgia delle polveri e nella lavorazione dei polimeri.
Preparazione delle polveri per i processi di produzione additiva con i miscelatori industriali amixon®
I termini “stampa 3D”, “prototipazione rapida” e “fabbricazione additiva” significano essenzialmente la stessa cosa. Si riferiscono alla produzione di componenti tridimensionali mediante l'applicazione di strati successivi di materiale. Durante il processo di applicazione, gli strati vengono fusi o sinterizzati insieme. Questo processo di produzione è utilizzato con successo a livello industriale per materiali metallici, ossidi ceramici, plastiche e materiali da costruzione legati al cemento.
Processi e aree di applicazione della stampa 3D industriale
La stampa 3D è un importante processo di produzione additiva nell'Industria 4.0 e, in combinazione con altri processi additivi, rivoluzionerà i metodi di produzione come tecnologia chiave in futuro. Il processo viene sempre utilizzato quando sono presenti tre condizioni:
- Una struttura geometrica complessa,
- una piccola quantità
- un alto grado di personalizzazione.
Un esempio: la necessaria riparazione di macchine i cui pezzi di ricambio non sono più disponibili. I pezzi precedentemente progettati tridimensionalmente vengono trasformati in componenti fisici convertendo direttamente i dati. A differenza dei processi di lavorazione tradizionali, ciò significa che non sono necessari né una dima, né pezzi fusi, né un utensile specifico per il prodotto. Oltre alle proprietà meccaniche e tecnologiche del componente da produrre, è possibile creare strutture complesse che non sarebbero possibili con un processo di produzione convenzionale. Con l'aumento della complessità della geometria del componente (personalizzato) e la diminuzione del numero di unità prodotte, aumenta l'economicità del processo di stampa 3D.
Le applicazioni della stampa 3D sono presenti in molti settori industriali. Tra questi, l'ingegneria meccanica e l'industria automobilistica, la modellistica e l'architettura, nonché la medicina umana e l'odontoiatria per la produzione di protesi. Il processo è adatto anche alla rapida realizzazione di risultati intermedi ottenuti nella bionica strutturale. Ciò è particolarmente vero quando le strutture di resistenza delle fibre vegetali devono essere trasferite alle moderne strutture portanti.
L'importanza di un'adeguata preparazione della polvere per i processi di stampa 3D
All'inizio del processo di stampa 3D, viene sparso un letto di polvere con una densità di impaccamento sufficientemente buona. Se l'apporto di energia è controllato con precisione, i collettivi di particelle si fondono per formare le strutture desiderate. La polvere in eccesso viene rimossa e idealmente utilizzata per ulteriori strutture a strati. Quando si alimenta la polvere nel letto di polverizzazione, è importante che la struttura delle particelle, la loro dimensione, la densità e la reologia della polvere siano il più possibile stabili. Questo perché le fasi del processo devono essere eseguite rapidamente per garantire l'efficienza della produzione. Le fasi del processo vengono quindi eseguite con trasportatori pneumatici ad aspirazione, che sono associati a velocità di trasporto elevate e quindi a una maggiore produzione di abrasione. Un eccellente condizionamento delle polveri polimeriche utilizzate è quindi di particolare importanza.
Condizioni simili prevalgono nella sinterizzazione laser selettiva da polveri metalliche.
La polvere viene aggiunta al letto di polvere utilizzando una racla. Le proprietà di flusso della polvere hanno un'influenza importante sull'omogeneità del letto di polvere e devono quindi essere il più possibile libere di fluire. L'obiettivo è ottenere forme sferiche delle particelle e una distribuzione granulometrica ristretta. Anche gli agglomerati devono essere dispersi, altrimenti il componente presenterà difetti piatti o lineari.
Cosa serve: un'adeguata preparazione della polvere come elemento di base per una stampa 3D industriale di successo. I miscelatori di precisione o i sistemi di miscelazione che utilizzano il processo a letto fluido sono particolarmente adatti per evitare adesioni e agglomerati e migliorare la fluidità della polvere.
Miscelatori di polveri, essiccatori sotto vuoto e reattori amixon® per la preparazione di polveri per la stampa 3D industriale
I miscelatori di polveri, gli essiccatori sotto vuoto e i reattori di sintesi amixon® svolgono funzioni importanti nella metallurgia delle polveri e nella lavorazione dei polimeri. L'obiettivo: il rivestimento nanofine di ogni singola particella. Questo obiettivo può essere raggiunto solo se il materiale di rivestimento è disponibile come soluzione o sospensione debole e viene miscelato in modo microfine nella polvere. Ciò significa che la polvere deve essere inumidita in modo uniforme e poi asciugata in modo particolarmente rapido e delicato per completare con successo il processo di rivestimento uniforme di tutte le singole particelle.
Qualità di miscelazione ideale e svuotamento completo
L'essiccatore a cono e il reattore a cono amixon® consentono una qualità di miscelazione omogenea ideale e allo stesso tempo un'essiccazione sottovuoto particolarmente rapida e delicata. Il nostro innovativo SinConvex® ruota al centro e genera un flusso totale della miscela. La polvere scorre inizialmente verso l'alto in una spirale lungo la periferia del contenitore di miscelazione. Una volta giunta a destinazione, la polvere torna a scorrere verso il basso lungo l'albero di miscelazione per effetto della gravità. Il processo di flusso avviene senza spazi morti e con una bassa frequenza di rotazione. L'apporto di energia è quindi basso e protegge in modo affidabile la struttura delle particelle delle materie prime. Questo aspetto è particolarmente importante perché a volte quantità molto piccole di additivi a flusso estremamente leggero, come la silice pirogenica, vengono miscelate in modo omogeneo e delicato nelle polveri. In pratica, può accadere che l'antiagglomerante galleggi sulla polvere e quindi ostacoli in modo massiccio il processo di miscelazione. Tuttavia, sono efficaci solo se vengono distribuiti delicatamente e in modo omogeneo nella polvere, senza mai essere macinati.
Infine, le pareti del contenitore di miscelazione, l'albero di miscelazione e i bracci dell'utensile di miscelazione sono a doppio strato e sono attraversati da un fluido termico (olio termico, acqua o vapore) in un circuito chiuso. Tutto ciò favorisce inoltre l'evaporazione della fase liquida dell'impasto.
È necessario evitare la contaminazione incrociata e garantire uno svuotamento senza segregazione e senza residui, a vantaggio del controllo dei lotti e della garanzia di qualità. Grazie alla nostra innovativa
tecnologia ComDisc®, i nostri miscelatori di polveri raggiungono un tasso di scarico dei residui fino al 99,997%. Inoltre, tutti i nostri sistemi di miscelazione sono progettati senza giunti e sono sottoposti a un'accurata pulizia a umido o a bagnato. Con il nostro sistema di pulizia a umido WaterDragon®, tutte le parti che entrano in contatto con il prodotto vengono pulite senza lasciare residui - in modo autonomo, semplice e affidabile.
Sviluppo e prove di processo
Test, pilotaggio, messa in servizio. Chi sviluppa nuovi prodotti di solito deve anche sviluppare la tecnologia di processo appropriata. Nel centro tecnico amixon® sono disponibili oltre 40 macchine di prova. I lotti di prova possono variare da 1 litro a 3000 litri. Quasi ogni dispositivo che amixon produce è unico: “Appositamente personalizzato per l'applicazione del rispettivo cliente...”. Insieme ai nostri clienti, nel centro tecnico raccogliamo idee e concetti che vengono poi realizzati quando viene ordinato un apparecchio amixon.
© Copyright by amixon GmbH