Particle technology
Unlike in mechanical engineering, it is not individual workpieces - with the unit of measurement millimeter = 10-3 m - that are the object of consideration, but heterogeneous particle systems.
Suppose we had calcined 100 kg of a ceramic color body in a kiln. We would then grind this mass in a roller mill or in an air jet mill. After the crushing process, each particle of this 100 kg batch can be expected to look slightly different from all other particles. In this respect, the definition of characteristic features of the particle collective can only be done with the help of statistical methods.
In bulk solids technology, the typical length measure used to describe a particle is the micrometer: 1 µm = 10-6 m. Typical bulk material particle diameters can be e.g. 0.1 µm or several 100 µm.
However, the particles of a bulk material can also be much smaller. These are then referred to as nanoparticles. Their particle diameter is the thousandth part of a micrometer. The unit of measurement is then nanometers: 1 nm = 1/1000 micrometer = 10-9 m.
Nanoscale powders have very large surface areas. This can favour diffusion processes. You may also find this interesting. "Changing the properties of substances through diffusion".
"Bottom-up" or "top-down" method
In contrast to the particle size reduction method described above (also called the "top-down" method), nanodisperse products can also be manufactured using the "bottom-up" method.
In this process, the particles are produced in a solution by chemical precipitation. Another wet process works electrochemically when an electric current flows in a suitable solution and solid particles are separated.
Nanoparticles can be formed from the gas phase by evaporation of metals or by pyrolysis.
Some organic nanoparticles, for example, can already be excreted by microorganisms.
Characteristic properties of bulk materials
Characteristic properties of bulk materials can be: Particle diameter, particle size distribution, particle shape, sphericity of particles, packing density, bulk density, adhesion and cohesion behavior, sintering behavior, time consolidation, flow behavior, flow locations and yield points, moisture content, miscibility, segregation tendency, particle hardness, agglomeration tendency, sinking behavior and dispersibility in gaseous or liquid media, affinity to liquid or gaseous media, solubility, absorption tendency, porosity, specific surface area, air holding capacity, electrostatic charge, dust tendency and much more.
Nanoscale dusts are pose a health concern and should not be inhaled. However, their presence cannot be ruled out. They are produced during volcanic eruptions, in combustion exhaust gases or as abrasion from tires and brakes.

If a bulk material is ground or sprayed very finely, then the solid surface area increases exponentially.
If bulk materials are converted to the nano-fine state, their chemical activity is increased. In addition, chemical and physical properties can change significantly. Ceramic materials created from nanoparticles, for example, can be similarly ductile to metallic materials.
With each particle division, the surface area of the powder increases. The surface area grows exponentially. The bulk material changes its flow properties. It becomes increasingly sticky. It resembles a highly viscous paste (ceramic materials). In the nanoparticulate state, however, a powder can also exhibit increased "air holding capacity" and fluidize (industrial soot from pyrolysis). Both phenomena complicate the handling of nanoparticulate bulk materials.
However, their extremely increased specific surface area also makes them interesting, e.g. in chemistry as catalysts. They are powerful light absorbers and can be used as UV protection in sunscreens and in emulsion paints. Nanotechnology is also used in medical technology and in the manufacture of semiconductors. Nanoparticles are also formed naturally when goods burn. For example, they are deliberately generated to produce soot as a black pigment (pyrolysis). More information on build-up agglomeration, including nanoparticles, can be found here.
Handling very fine particles can trigger hazards. amixon® mixers offer a high level of safety. They are permanently gas-tight and their mixing tools rotate at relatively low rotational frequencies. Here you can find more information about Atex and type examination.
Technical terms and definitions in DIN CEN ISO/TS 80004-4
The document cited above - published in 2014 - represents an interim result of the standardization work. It differs editorially from the usual standardization documents and has therefore not yet been published as a standard. (Beuth-Verlag)
First, five manifestations of nanostructured materials are defined
1) nanostructured powder
2) Nanocomposites
3) solid nanofoams
4) nanoporous material
5) liquid nanodispersions.
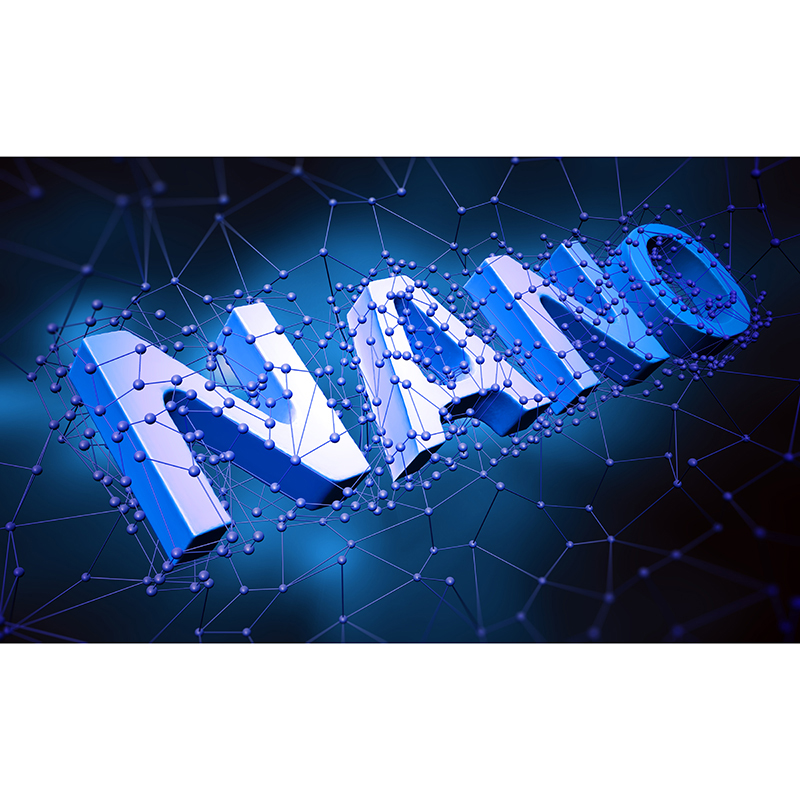
amixon® mixers and reactors are pressure and vacuum tight and can be heated up to a temperature of 350 °C.
Powder mixers play an important role whenever nanoscale powders or suspensions have to be processed. They must be technically tight according to TA-Luft. Typically, they are also designed to be pressure- and vacuum-resistant. If the parts in contact with the product (mixing tools and mixing chamber) can be heated, they can also be used as reactors.
Very fine particles tend to form agglomerates or even aggregates. The interparticle adhesive forces are then unusually high in relation to gravity. This complicates the homogenization process in the mixer. Deagglomerating nanofine particles is difficult and requires the use of high-speed tools. amixon® installs high-speed cutting rotors, HighShearBlades or rotor stators in the mixer. Hardened materials, armor plating and coatings prevent wear. They also prevent contamination of the nanopowders with the material of the dispersion tools.
© Copyright by amixon GmbH