Complex plant technology in the preparation of methyl cellulose, carboxymethyl cellulose, hydroxyethyl cellulose, etc.
Pulp is the fibrous mass produced during the chemical pulping of plant fibres. Pulp consists mainly of cellulose. The word comes from Latin and means small cell. Cellulose is the basic static structure of all plant cells.
Cellulose is a multi-talent: In chemically modified form - as a cellulose derivative - it made the development of photography possible in the first place. It is an important component of textile fibres, helps lay tiles, keeps baked goods fresh, gives mayonnaise its consistency and makes toothpaste smooth. But the production of the various cellulose derivatives only works with high-quality processing plants.
Cellulose is a multi-talent
Hardly any other raw material is as closely linked to the history of mankind as cellulose. Without paper, the history of mankind would be different. Even rags were used to make paper in the beginning. Because they are made of cotton. In their fibres, the cellulose is present in a particularly pure form.
The development of the chemical use of cellulose began in 1846 with the production of nitrocellulose, also called cellulose trinitrate. It was first used for military purposes and was also called gun cotton. It is formed when cellulose is treated with nitrating acid, a mixture of sulphuric and nitric acid. In further process steps, the gun cotton is washed, ground and dried.
Parallel to military use, civilian use of nitrocellulose began in the 19th century. Weakly nitrated nitrocellulose (cellulose dinitrate) was mixed with camphor and formed the basis for the first technical plastics as celluloid.
Celluloid served as a carrier for photographic films until 1951. Table tennis balls were also made of celluloid until 2014. The first transparent plastic film was also based on cellulose. In the 1920s, cellophane (brand name: Cellophane) is produced for packaging purposes. It is particularly glossy and, unlike modern packaging films, can be permanently folded. It was used, for example, as a candy wrapper because it could be "twisted" well at both ends. In the meantime, cellophane has been largely replaced by oil-based plastic films for price and technical reasons. However, a renaissance of cellophane could be justified in the future by its excellent biodegradability.
There is an important reason why celluloid was replaced by other plastics. This is the easy flammability of celluloid.
Cellulose is biodegradable
The cellulose content of cotton is about 84-91%. Due to its long fibres, it is mainly processed as a textile raw material. The cellulose content of wood, on the other hand, is only approx. 40-45% and must be isolated through a complex chemical digestion process. Mainly sawmill residues and low-grade softwoods are used as raw material for industrial recycling into paper. However, higher-quality softwood and hardwood grades, mostly from plantations, are also used for chemical pulp.
With the help of the sulphite digestion process, a particularly pure cellulose is obtained from wood. The chemical cellulose obtained in this way is also called dissolving pulp or special pulp.
But first the cellulose must be dissolved out of the wood. The logs are chopped into wood chips. The aim is to achieve a uniform size.
These wood chips are cooked in pressure-resistant reactors with acid chemicals under heat and pressure for several hours. Accompanying substances of the cellulose such as lignin and hemicelluloses dissolve in the acid and are separated with the filtrate. The filtrate is called black liquor and contains lignin residues, carbohydrates from the degradation of hemicelluloses, sodium carbonate, sodium sulphate and other inorganic salts. Sodium, sulphur and calcium are largely recovered from the black liquor and recycled. Vanillin can be extracted from the lignin, similar to tree bark.
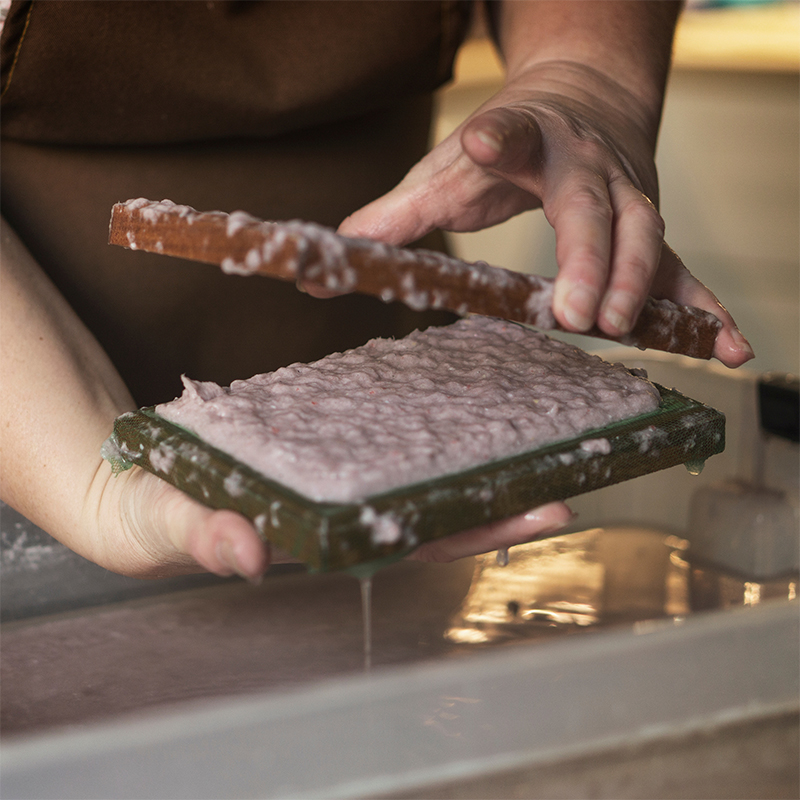
Cellulose sludge is dewatered manually.
Cellulose derivatives and their world production in 2020
Product | World production in 2019 | Application |
Cellulose regenerated | 3.300.000 t/a | Textiles |
Cellulose acetate | 900,000 t/a | Coatings and membranes |
Cellulose nitrate | 420.000 t/a | Coatings, membranes and explosives |
Carboxymethyl-cellulose | 360.000 t/a | Food, Cosmetics, Pharma, Oilfield, Paper |
Methylcelluloses | 180,000 t/a | Food, pharma and construction |
Hydroxylethyl-cellulose | 8,000 t/a | Paints, lacquers, films and cosmetics |
Several washing processes follow. The bleaching of the cellulose takes place in several stages depending on the desired product quality. The cellulose is then mechanically and thermally dried. Depending on the fibre quality of the wood and the desired purity of the cellulose, up to 400 kg of cellulose can be obtained from one tonne of wood. The pulp is usually marketed in rolls (approx. 500 kg) or in bales (approx. 200 kg).
Of the approximately 150 million tonnes of pulp produced worldwide each year, 96 per cent goes into paper production. Only 3.5 percent are refined in the chemical industry.
We encounter derivatives of cellulose almost everywhere
Advances in macromolecular chemistry led to the development of a variety of cellulose derivatives with valuable properties.
Cellulose ester: In 1856, the first thermoplastic was produced from camphor and cellulose nitrate. This resulted in table tennis balls and film material for photography and moving images.
Cellulose acetate: This was followed by a second thermoplastic that could be processed into foam (cigarette filters) and fibres. Further developments led to transparent moulded bodies, cubes and tool handles.
Cellulose ether: Since the beginning of the 1930s, this group of cellulose derivatives has gained its industrial importance, a triumphal procession that continues to this day and has an ever-widening range of applications. Cellulose ethers are non-toxic, mostly water-soluble products that are usually traded as white powders or granules. The specific properties of the individual cellulose ethers depend on the type, number and distribution of substituents introduced by a chemical reaction after activation of the cellulose molecule with sodium hydroxide solution.
The name is given by naming the substituent, e.g.: Methyl cellulose (MC), hydroxypropyl methyl cell ulose (HPMC), carboxymethyl cell ulose (CMC), hydroxypropyl cell ulose (HPC), ethyl cell ulose (EC), etc. Applications are found in the construction industry as additives to optimise various properties in mortars, tile adhesives or fillers (HEMC or HPMC). Wallpaper paste consists mainly of methyl cellulose (MC) or carboxymethyl cellulose (CMC).
In metal forming, cellulose derivatives are used as lubricants, in the production of paints and varnishes as viscosity regulators and binders. In dishwasher tabs as an explosive or in agriculture to delay the effect of pesticides.
Some cellulose derivatives are approved as food additives and for use in cosmetic formulations. Among other things, the behaviour of the different cellulose ethers in an aqueous environment at different temperatures is used. They are often indispensable additives in emulsifiers, stabilisers and preservatives. They improve the flowability of instant sauces and soups. In ice cream, they influence the melting behaviour as well as the mouthfeel and give it a creamy taste despite cream reduction.
In the food and pharmaceutical industries, they influence the texture, shape, structure and consistency of liquid and semi-solid products. Their applications range from toothpaste to coating compounds for medicines. In cosmetics they serve as viscosity regulators and stabilisers, they determine the rheology of ointments, sun creams and make-up. Their potential is far from exhausted and is the subject of intensive research.
The price for "simple" cellulose derivatives such as carboxymethyl cellulose (CMC) starts at 1.50 €/kg and rises to over 100 €/kg for special cellulose derivatives in pharmaceutical applications. Cellulose ethers are hardly substitutable by petroleum-based products in many applications. This will increase their importance in various industries. In particular, in many pharmaceutical applications or as food additives, especially for convenience products.
Cellulose ethers and their applications in industry
Name | Abbreviation | Production | Application |
Carboxymethyl cellulose | CMC | Converted to alkali cellulose with sodium hydroxide solution. Alkylation with chloroacetic acid. | Petroleum industry, textile industry, detergent additive, binder, thickener, paper sizing agent (wallpaper paste), protective colloid, food additive E 466 (ice cream, mayo, jelly, baked goods), toothpaste, cross-linked as tablet disintegrant. |
Methylcelluloses | MC | Converted to alkali cellulose with sodium hydroxide solution. Alkylation with methyl chloride, | Additives in various building materials (concrete, mortar, tile adhesives, fillers, plasters, etc.) Wallpaper paste, thickener, gelling and coating agent, emulsifier, stabiliser in food (MC: E 461, HPMC: E 464) meat substitutes, ice cream, bakery products, mayo, instant products and frozen products) and cosmetics. In pharmacy as "artificial tears", laxative, negative contrast agent, retardation of active ingredients, tablet coating, material for hard capsules. |
Ethyl cellulose | EC | Converted to alkali cellulose with sodium hydroxide solution. Alkylation with ethyl chloride. | Thickener, binder, adhesive, as well as film former and water-repellent barrier layer. Main ingredient lightfast cellulose ether coatings, packaging materials, thermoplastics, artificial snow for Christmas trees, cable insulation, protective skins and seals. As an additive of synthetic resins and waxes for varnishing coloured Easter eggs and as an additive for stamping inks in the food industry (E 462). In pharmacy, excipient for increasing viscosity, as a binder for tablet granules, as a builder and disintegrant for tablets, and in particular also as a film former (e.g. trademarked under Surelease®) for lacquer tablets. |
Hydroxyethylcellulose | HEC | Converted to alkali cellulose with sodium hydroxide solution. Etherification with ethylene oxide. | In the building materials industry in water-soluble paints and dispersion adhesives as well as plasters and fillers. In pharmaceuticals as an excipient and in toothpaste. |
Hydroxypropylcellulose | HPC | Converted to alkali cellulose with sodium hydroxide solution. Etherification with propylene oxide. | Application as pharmaceutical excipient, binder for ceramic masses, for coatings and adhesives, in cosmetic articles, in printing inks and in polymerisation technology. In food as a stabiliser, protective layer and gloss coating. |
Complex reaction processes for carboylmethylcellulose
The most important cellulose ether in terms of quantity is carboylmethylcellulose (CMC). The purified cellulose from wood or cotton is ground into a fine powder (particle size approx. 100 to 200 μm) and pneumatically conveyed into a large-volume mixer with 10 to 30 m³.
From there, the homogenised pulp is conveyed into a synthesis reactor. Fifty percent caustic soda is sprayed into the reactor. The exothermic reaction produces sodium cellulose. Then chloroacetic acid is sprayed into the reactor. This produces carboxylmethylcellulose. Optionally, the CMC synthesis can be carried out in slurry form without, or with solvent (isopronanol or ethanol).
Other cellulose derivatives (e.g. hydroxypropylmethylcellulose) are produced in a similar way. The only difference is that no solvents are usually used here and the reaction chemicals are gaseous (methyl chloride, propylene oxide or ethylene oxide). The conversion of substances then requires comparatively high system pressures (up to 20 bar) to ensure that the gaseous reactants remain in the system at high temperatures.
Reactors for the production of cellulose derivatives are designed to be pressure-resistant. They are also equipped with a double jacket to be able to heat or cool the contents. Larger reactors also have additional cooling systems in the superstructures and parallel to the reactors.
High-strength materials must also be permanently corrosion-resistant. Welding technology is of great importance here.
In addition, there are other criteria that must be taken into account when designing the reactor. For example, in addition to high strength, the container material must have special corrosion resistance, as the chlorides of the salts that are formed are chemically aggressive at high temperatures in combination with water. The phenomenon of stress corrosion cracking describes a decrease in the corrosion resistance of materials when they are subjected to increased tensile stress. In addition, the phenomenon of material fatigue due to changing load and temperature must be taken into account.
Handling reagents and reaction by-products also requires a lot of know-how. Ethylene oxide has the highest hazard potential (production of HEC or HE mixed ethers such as HEMC): It is explosive and must be stored in a nitrogen atmosphere. During the production of methyl celluloses (MC, HEMC or HPMC), dimethyl ether is formed in a side reaction, which is highly flammable, explosive and toxic. It must be discharged at the end of the reaction together with unreacted methyl chloride. In the industrial process, the gas mixture is collected under pressure and at best reused in the process.
The reaction product is a moist cellulose derivative that still contains common salt and some by-products (higher alcohols). The raw product is transferred to a 90 °C water bath and suspended. Salts and by-products dissolve in the hot water. But not the cellulose ether: MC, HEMC and HPMC are insoluble in water at temperatures above 50-60 °C.
The hot wash water is then separated by filtration and the filter cake is washed free of salt. The hot wash water can be used several times for cleaning, as it can absorb up to 30 percent common salt. In this respect, energy and water can be saved. The residual moisture of the cleaned product after the filter and washing stage is still about 50 to 60 percent. The cellulose ether, which after washing still has the bulk density of the ground cellulose (approx. 150 g/l), is now selectively cooled in a continuously operating ring-layer mixer agglomerator by adding cold water or flake ice until it is close to its solubility temperature in water (approx. 45°C).
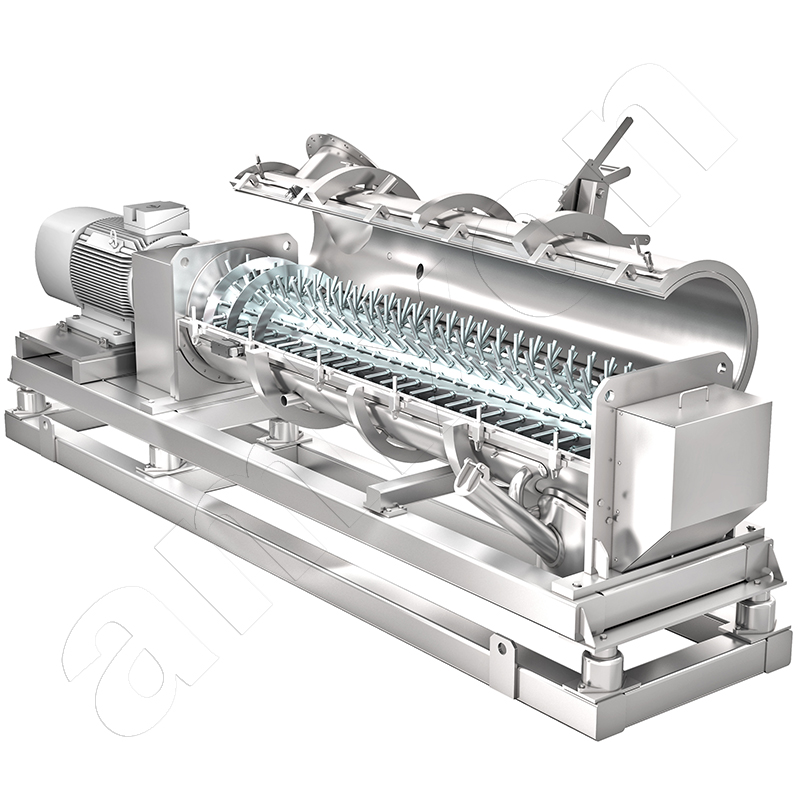
Ring layer mixing granulator: The methyl cellulose and the flake ice are continuously fed into the ring-layer mixing granulator and accelerated into a swirling motion. A ring layer forms on the wall. This is intensively mixed, deagglomerated, compacted and conveyed by the pin tools. The discharge nozzle is located on the right below the mixing chamber.
Final homogenisation
In the final process step, the product is ground and dried in power dryers. The drying takes place atmospherically. The dry material produced is collected in large mixers and homogenised before being filled into bags or BigBags.
The raw material pulp is a renewable natural product. Like all natural products, the raw material is also subject to seasonal and site-related fluctuations. In addition, the substance is prepared in batches. Here, too, there are slight differences in quality from batch to batch. Balancing these out is one of the main tasks of the large-volume end product mixer. In the following, 3 methods of final mixing are described.
Two opposing flows meet in the amixon® conical mixer. On the outside, the mix is conveyed upwards in a helical pattern, while the downward flow predominates in the middle. In the border areas, a change of place takes place within the particle system. The blade-shaped mixer arms create complementary cross-flows. Despite slow rotation frequencies, ideal mixing qualities are ensured that can no longer be improved in practice. The total flow described in this way constantly sets all particles in relative motion to each other. It is universally available, regardless of whether the filling level is 5% or maximum filling. The special shape of the mixing helix in "SinConcave®" or "SinConvex®" design guarantees almost 100% residual discharge. The particularly gentle treatment of the material to be mixed results directly from the low drive power. The mix particles are neither crushed nor rounded and/or broken.
Continuous mixing of the end products
The interesting thing about this type of mixer is that it can be operated either discontinuously or continuously, regardless of its size. Even more interesting, however, is that the discharged mix corresponds to the ideal mix quality right from the start. There are no "start-up losses". This is explained below:
Mode of operation at the start of production:
The mixer outlet is closed. All gravimetrically operating metering units are started simultaneously with a low mass flow. The master dosing control harmonises all product flows. The mixer filling level increases continuously, with the mixer drive starting at half the filling level. This equalisation process is completed when the mixer is slightly more than half full. After reaching the desired fill level (approx. 60 to 80 % of the usable volume), the outlet organ opens slowly. This filling level is kept constant. The dosing flow can be increased under constant control up to the maximum mass flow.
Operating mode at end of production:
All metering elements decelerate the mass flow one after the other and then switch off and close simultaneously. The mixer empties continuously to the last residue. Free-flowing products flow out completely.
The advantages for the user at a glance:
- technically ideal mixing quality
- Can be operated either as a batch mixer for premixes or as a continuous mixer
- the mixing intensity is adjustable (gentle homogenisation to intensive deagglomeration)
- Defined average residence time of the mixed material in the mixer based on the continuous boiler flow. This is independent of the speed of the mixing tool
- No product loss at the beginning of production
- No product loss at the end of production
- ideal residual discharge
- Defined filling level selectable from 10% to 100% of the usable capacity
- Microfine mixing of the liquid without contamination of the mixer
- advanced processes such as humidifying, tempering, drying,
- Reaction possible - highest hygiene standard (GMP standard); easy cleaning, dry or wet - the mixer is only top-mounted and driven.
The Gyraton® mixers represent a new alternative when it comes to homogenising large volumes.
For the homogenisation of particularly large batches, amixon® has created an interesting new development with the Gyraton® mixer: The mixing spiral rotates clockwise and conveys the mix upwards. An additional drive moves the lower part of the mixer shaft on a circular path. The pivot point is located at the top centre of the shaft seal.
This mixer can also be used for dry, moist or suspended bulk materials. The sizes are freely selectable from 10 m³ to 100 m³. Sizes up to 70 m³ can be transported fully assembled by road.
Best mixing results are already achieved at a filling level of 10%. The mixing is done extremely gently with extremely low energy input. Feeding takes place from above via one or more standard nozzles. The emptying of the mixed material takes place with the bottom flap open via a standard spout pointing downwards.
The Gyraton® mixer is characterised by
- The mixing process takes place without dead space, particularly gently and with minimal energy input.
- Very good residual emptying
- optionally pressure or vacuum resistant
- the mixing chamber is optionally temperature-controllable
- space-saving, compact design. The large mixer can be transported on the road
- the mixing chamber is easily accessible through a large inspection door
- Easy cleaning
- wet (automatic)
- dry manual with hoover
- Depending on the length of the mixing time, which can be specified by the customer, the rotation frequency of the mixing tool and the superimposed pendulum movement are adjusted. The engines are very small. The energy consumption is correspondingly low.
- The mixing system can also be used for moist, poorly flowing products.
Trials in the amixon® technical centre
If you are faced with an investment decision in the areas of mixing, homogenising, agglomerating, synthesis, cooling or vacuum mix drying, you should talk to us. amixon® offers exceptional and highly efficient solutions. We offer you broad process engineering know-how and have an excellently equipped machine/equipment construction department. We would be happy to arrange an appointment with you at short notice for tests in our technical centre.
© Copyright by amixon GmbH